OMG Induction Heater
Experimentonomen, Wed Dec 26 2007, 04:07PM
I found this one a few days ago and i am truly amazed of what this kid have accomplished. I have a hard time believing its true.

Re:
OMG Induction Heater
CompWiz, Thu Dec 27 2007, 06:44AM
Holy Crap
I want one!!!!

Re: OMG Induction Heater
Steve Conner, Fri Dec 28 2007, 12:47PM
Well, I noticed hfsstc-freak's comment on the Youtube vid, and I agree with his analysis of the situation. The guy probably has a couple of conduction-cooled capacitors, specially designed for induction heating, between those heatsinks. The capacitor is the most difficult part of an induction heater, and if you can get a real induction heating type, your chances of success go right up!
The crucible probably makes a big difference too. It'll keep the heat in, and the steel will get a lot hotter than if it was just dangling in the work coil.
I managed to get one of those Celem conduction-cooled mica caps off Ebay for $39, but so far I've not been able to drive it at more than a tiny fraction of its 100kVA rated power. I've just got it hooked up to a Mazzilli oscillator running at 400kHz, and if I try and increase the power above a few hundred watts, the MOSFETs go into parasitic oscillations and blow themselves up.
It really needs a proper driver and a water cooling system to do it justice. Also, at 0.4uF, 500V RMS, 200A RMS rating, it wants a fairly large work coil of about 2.5uH and an operating frequency of 160kHz to give its full rated kVA. I used it with a smaller coil, hence why I ended up at 400kHz.
Re:
OMG Induction Heater
Marko, Fri Dec 28 2007, 01:21PM
Yes, the biggest thing is actually the thermal insulation around the workpiece (meltpiece) which isn't always possible though.
I managed to get one of those Celem conduction-cooled mica caps off Ebay for $39, but so far I've not been able to drive it at more than a tiny fraction of its 100kVA rated power. I've just got it hooked up to a Mazzilli oscillator running at 400kHz, and if I try and increase the power above a few hundred watts, the MOSFETs go into parasitic oscillations and blow themselves up.
Any more information, pics of your setup steve?

I became a sort of a fan of royer oscillator and am becoming more and more aware of it's problems. I can't think of what would ''parasitic oscillations'' be... are you using a ferrite core?
The diodes tend to be a big trouble. Running at 1Mhz no load (air coil) I cooked the 200ns trr diodes, and as they were heating up, I found that peak gate voltage was rising constantly
and threatened to blow the mosfets! :O
Putting a gate protection diode cured that, but even at like 50V supply voltage diodes were grossly hot. Even 25ns trr diodes were getting too hot at higher voltages, and a forward drop seriously close to mosfet threshold voltage

Think if you needed diodes that would stand 1000V at that frequency. This, together with too hot resistors and slow turn on times, made me to start developing a proper gate driver.
Although shot through itself is not dangerous in ZVS, this appears to break the oscillation down in some cases.
To cut the story, I'd love to see your work steve!
BTW, doesn't this thread look like it doesn't belong to project board, after all?
Re: OMG Induction Heater
Experimentonomen, Fri Dec 28 2007, 02:38PM
Maybe i should have posted this in general chitchat.
Re:
OMG Induction Heater
Steve Ward, Fri Dec 28 2007, 09:35PM
I can't think of what would ''parasitic oscillations'' be... are you using a ferrite core?
Resonance between the resonant cap and its inductance to the mosfets. I had huge problems with this when attempting a higher power ZVS oscillator when using high speed gate drivers instead of the crappy low speed "gate drive resistors". I believe that using gate drivers makes the parasitic oscillations WORSE because its easier to excite that resonant mode with the faster drive. In fact it was so bad i gave up on it rather quickly and determined that if i was gonna do a ZVS circuit, i would do it properly instead of the "mozilli" driver :P.
Now that i can get my hands on some giant powdered iron toroids, a ZVS inverter looks attractive again for induction heating. Still need to find one of those badass ceramic caps, though.
Re: OMG Induction Heater
Experimentonomen, Fri Dec 28 2007, 10:41PM
Steve, badass ceramic caps ?
Re:
OMG Induction Heater
Steve Ward, Sat Dec 29 2007, 02:04AM
Yeah, like those water-cooled heat-sinkable ones. I was fairly sure they were ceramic dielectric, though i suppose i might be thinking of the mica types. Probably less likely to be PP for temperature reasons.
Right now i do have a pair of .01uF 10kV caps that are rated 18ARMS, but that doesnt work too well for a solid state induction heater. Really, just give me something around 1uF that can do a few hundred amps RF and i will make something cool

. I was also thinking about just using a DRSSTC (with a miniaturized primary) and heating some stuff with that. It wouldnt be terribly efficient, but im sure it could process a lot of power

.
Re:
OMG Induction Heater
Experimentonomen, Sat Dec 29 2007, 11:15AM
I have one of these:

Re:
OMG Induction Heater
Steve Conner, Sat Dec 29 2007, 08:20PM
Here's mine:
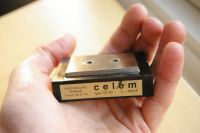
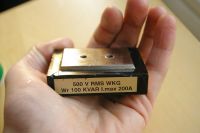
The dielectric is mica. To get the full rated power, it needs to be sandwiched between water cooled busbars. Using the driver I've currently got, it barely gets warm even with no cooling.
Re:
OMG Induction Heater
Marko, Sun Dec 30 2007, 01:07PM
yay steve - nice toy over there.
I wonder how would it fare against a bigger stack of good old CDE942's?
Shortening their legs and soldering them tightly onto water cooled busbars might help them get rid of heat.
If you are already water-cooling the coil water flowing through same pipes could simply be passed around the cap.
Resonance between the resonant cap and its inductance to the mosfets. I had huge problems with this when attempting a higher power ZVS oscillator when using high speed gate drivers instead of the crappy low speed "gate drive resistors". I believe that using gate drivers makes the parasitic oscillations WORSE because its easier to excite that resonant mode with the faster drive. In fact it was so bad i gave up on it rather quickly and determined that if i was gonna do a ZVS circuit, i would do it properly instead of the "mozilli" driver :P.
Interesting points steve... when did you really run into problem? (power level, voltage..?)
I had most of trouble with diodes; I couldn't even put in an UCC directly, because voltage drop of most diodes is too high to turn them off safely.
My newest ideas are completely different from this though, I can tell more about them if you guys are interested.
I always intuitively kept drain inductance as low as possible, cutting the mosfet legs down and soldering the cap right onto them.
That wasn't a problem for power levels I was running, but if you have a large water cooled cap like that it becomes a bigger problem.
I wondered if you could simply keep the cap close to it's work coil, and make low current connection with the inverter over two fat coax cables.
Or, if you have enough water cooling, you could simply put the mosfets directly onto the cap and cool everything at once. I don't know.
My best shot of doing a ZVS inverter ''right'' would be to use PLL and a current fed fullbridge.
Hardest part is definitely designing the gate drive, which needs to be make-before-break (now I need to generate shoot-through instead of deadtime) and this makes use of an GDT difficult.
It may be solved through some crazy logic, but I don't really have any original ideas.
Feedback could simply be taken as voltage feedback from the bridge output.
I imagine circuit could suffer from same problem as royer but PLL could limit the frequency range.
I'm glad I got you 'big guys' interested, you are making an interesting discussion.
BTW, huben made some good work at project board - it may not be all that problematic as you guys made it appear. Just needs to get scaled up with some 1200V devices...


Re: OMG Induction Heater
Experimentonomen, Sun Dec 30 2007, 10:15PM
Nice results!! What topology are you using ?
Re:
OMG Induction Heater
Marko, Sun Dec 30 2007, 11:49PM
Those humps on the waveform do scare me though. I noticed the same thing on my class E SSTC, but never on royer yet even in Mhz range.
How did the failure happen though? Mosfets just badly overheated? (right one sort of doesn't look like it's heatsunk properly

)
Thinking again, could the oscillations be happening because there is some deadtime between transitions? I mean, the feedback system of the royer isn't too perfect on itself.
Having lots of mosfets around I was tempted to try a royer IH, but my main problems are lack of a power supply (like 100..150V with lots of amps) and adequately sized heatsinks. I have only some small CPU heatsinks left around, so I think I'll have to find something on ebay or etc.

Oh, and too much simultaneous projects...
For, HFsstc freak, royer oscillator (Mazzilli driver, ZVS flyback driver) is used, adn this is basic schematic

Instead of a flyback a work coil in the air is simply used.
Marko
Re: OMG Induction Heater
Steve Conner, Mon Dec 31 2007, 12:18PM
Hi all,
Yes, like Marko said, it is a ZVS/Mazzilli/Royer/whatever oscillator. The only unusual thing is that there is no centre tap on the work coil. I used a bifilar wound ferrite transformer connected in parallel with the work coil to "add" a centre tap. Maybe the stray inductances of this transformer are what's causing the problem. I don't know, I just wanted to try this to see if it would work.
I was running it off a variac, transformer and bridge rectifier, and what happened was that it stopped heating, started to hum, and blew a fuse. I just assumed one of the MOSFETs had popped. But when I got the thing out again, both MOSFETs were actually good! I think it just dropped out of oscillation which makes both MOSFETs turn on, shorting the power supply.
I don't know what those humps are either! :( But I do know that as I increase the voltage, the ringing you see on them takes longer and longer to decay, until it bursts into continuous oscillation of huge amplitude and everything RF sensitive in the neighbourhood freaks out... Again I'm not sure how this happens, but these parasitic oscillations are what limit how far I can turn it up.
In any case, this is about as much power as I'd care to use without water cooling. The work coil gets hot enough to char the wooden table, and the tank capacitor gets hot enough that it's painful to touch. I've stopped using it in case I damage the capacitor.
The MOSFETs run quite cool in spite of the terrible heatsinking, and all the magnetics run cool too. The DC bus choke is a stack of four iron powder cores that I got off Ebay. They are Micrometals type 52 material IIRC.
Re:
OMG Induction Heater
Marko, Mon Dec 31 2007, 02:33PM
Yes, I noticed you have no center tap on the coil!
I'm not sure if transformer is any good though, the ringing could be due to it's leakage inductance resonating. Center tap to the work coil always seemed to work well - could be done by a small conductor since it carries relatively small current.
I myself try to get rid of ferrite anywhere I don't really need it!
I was running it off a variac, transformer and bridge rectifier, and what happened was that it stopped heating, started to hum, and blew a fuse. I just assumed one of the MOSFETs had popped. But when I got the thing out again, both MOSFETs were actually good! I think it just dropped out of oscillation which makes both MOSFETs turn on, shorting the power supply.
I managed to replicate exactly the same thing. With mosfets like IRFZ44, low power circuit always happily worked from 12V and I was lighting bulbs by magnetic coupling to the coil safely.
Then I tried the same thing with 2+2 (wanted ot add much more later) small 1.5 amp 500V mosfets, with high ON resistance (7 ohms or so). I used a much bigger work coil and a smaller cap;
As I powered the circuit up with just 12V, it shorted the supply the same way with no load at all!
It worked only if I applied the gate voltage first (then it starts to oscillate through gate drive resistors) and then apply the drain voltage.
Still circuit would sometimes drop out of oscillation if overloaded.
In an IRFP450 based circuit, I also blew a mosfet this way, by applying the drain voltage before gate power.
Now may be getting some insight why is this happening, since I made an actively-pulluped circuit which never dropped out of oscillation (yet).
Hmmmmmmmmmmmm....
Re:
OMG Induction Heater
Experimentonomen, Mon Dec 31 2007, 05:17PM
The OMG IH dude is back:

!!!!!!!
Re:
OMG Induction Heater
Steve Ward, Mon Dec 31 2007, 09:25PM
I don't know what those humps are either! :( But I do know that as I increase the voltage, the ringing you see on them takes longer and longer to decay, until it bursts into continuous oscillation of huge amplitude and everything RF sensitive in the neighbourhood freaks out... Again I'm not sure how this happens, but these parasitic oscillations are what limit how far I can turn it up.
Thats exactly what happened with my setup too. Seemed to limit me to about 30VDC which was a far cry from the 170VDC i was hoping to eventually use :P. Next time i will just generate the drive signals with an oscillator and forget the feedback/drive stuff. Shouldnt be too big of a problem with an induction heater.
Re: OMG Induction Heater
Experimentonomen, Mon Dec 31 2007, 09:56PM
Get some of these gate drivers with built in oscillator ;) IR2153
Re: OMG Induction Heater
kim_ladha, Mon Jan 07 2008, 12:02PM
Hi, that was my video that melted the steel....
Steve Conner- absolutley right mate, those are celem conduction cooled caps in the tank circuit. They are the most critical component used here and also the most expensive.
I have experimented with the full bridge and half bridge topologies. The Fairchild application note is right, a half bridge is better for reliability. I used a hgtg20n60a4d half bridge in my latest and best version. Much simpler and reliable. It draws 3.1kW continuously and melts steel without insulation now. My other youtube video shows the setup more clearly. I think anyone who can build a drsstc will have no problem building one of these.
As for water cooling... ESSENTIAL. The copper work coil softens and colapses in less than 2 seconds with no water at 3kw. Also, if the water pump stops, the water in the coil boils in a few seconds and fires the silicone pipes off.
Alot of people have been asking for schematics and i will try and find some time to draw some up.
Regards
Karim
Re:
OMG Induction Heater
Steve Conner, Mon Jan 07 2008, 05:11PM
Hi kim_ladha, welcome to the forum! Your induction heater is great, it seems to have inspired everyone, including me

BTW, are you also water cooling the capacitors, or are those heatsinks the only cooling they have?
Re:
OMG Induction Heater
Experimentonomen, Mon Jan 07 2008, 05:36PM
Here comes the schematic, kim sent it to me via email and granted me access to publish it here.

Re: OMG Induction Heater
kim_ladha, Tue Jan 08 2008, 01:52PM
Hi Steve,
I use a 0.75 k/w aircooled heatsink (cut in half) for the capacitors. The max dissipation of the capacitors is higher than the heatsinks can handle but it takes 10 minutes or so to reach their max opperating temp of 85C. The water cooling is really just for the work coil- if run with no work piece, the water comes out almost boiling! The heater draws 13 amps at 240v at this condition- thats more than a normal kettle. I guess about 90% of this power is being dissipated in the coil alone, the rest being dissipated in the igbts and capacitor.
Karim
Re: OMG Induction Heater
Marko, Tue Jan 08 2008, 02:43PM
Awesome to see you here sir! Welcome to forum.
That is one of first heaters I could call *useful*, keep this work up!
One thing I don't understand here is, how are you taking current feedback just like that from the parallel LC tank?
Steve Ward had a hard time assuring me that that is impossible, as matching inductor would be hard switched with rather poor power factor and result in gross overheating of IGBT's.
Also, thinking abut water cooling, does the conductivity of water ever represent a problem?
You are running it through quite high potential gradients. Distilled water can acquire rubbish through time which makes it more and more conductive.
Radiators and pumps, you keep them just grounded?
Any plans on upgrading the water cooling to cool the caps and maybe switches?
Marko
Re: OMG Induction Heater
kim_ladha, Wed Jan 09 2008, 11:54PM
Wow, lots of questions....
The feedback is definitly only possible from the actual tank circuit and only for inductor fed resonant tanks. I have 800 amps going through mine so it is hard to just use conventional techniques. To drop the current i put a loop of coax braid (any copper wire will do) soldered on one of the straight sections of the work coil. The connections are 1" appart and this 'resistivly' drops the current to 50 amps or so- this is simply due to the resistance of the copper pipe! Then i tried several closed ferrites but they all over heated. Finally I used a c core, the air gap stops saturation and it kept cool. This went into a 1:500 current xfmr (cheapo plasic type) to get a few milli amps which i use for my pll signal. (using the term pll loosly). I came up with the concept using pspice- the theory is sound and reliable.
As for the other things. 1). Use long plasic water pipes- water conductivity is not really a problem however
2). You can short out the work coil in my design, the current becomes square wave and switching losses are high- it doesn't break however. Same happens if you loose current feedback.
3). Grounding only represents a problem if the circuit fails and your touching the coil/water. I use an isolation transformer for testing so i don't die- no earth. The coil is live but safe to touch probably due to the high frequency. In a normal failure it will also be safe to touch. There is always a chance that the devices will short so that it is connected to live- although unlikely, I try and avoid touching it. For normal heating work you can just connect it straight to the mains- every device failure I have had in any equipment like this ALWAYS blows a fuse and isolates it. Of course- the time it doesn't could be your last so be careful!
4). No plans to upgrade circuit anymore. I am at the limit of what I can draw from a mains plug socket already! If I wanted to make a 5-6 kw version, the fgh50n6s2d looks like a safe bet.
Karim
Re: OMG Induction Heater
HV Enthusiast, Thu Jan 10 2008, 01:19PM
Actually, there is a VERY NICE High Energy water-cooled induction capacitor on EBAY now. And a good price too.
EBAY ITEM: 280185795601
Re: OMG Induction Heater
Experimentonomen, Thu Jan 10 2008, 04:04PM
This capacitor is meant for vacuum tube ih, not solid state. It´s 2nF @ several kilovolts.
Re:
OMG Induction Heater
HV Enthusiast, Thu Jan 10 2008, 06:21PM
HFsstc-freak wrote ...
This capacitor is meant for vacuum tube ih, not solid state. It´s 2nF @ several kilovolts.
you have something against tubes???
Re: OMG Induction Heater
Experimentonomen, Thu Jan 10 2008, 08:26PM
Absolutely not, i just thought this thread was for ssih.
Re:
OMG Induction Heater
HV Enthusiast, Fri Jan 11 2008, 01:26AM
HFsstc-freak wrote ...
Absolutely not, i just thought this thread was for ssih.
No, the subject title that you started is "OMG Induction Heater."
If you wanted to keep it solid state, you should have made that clear in either your first post or through the title.
Re:
OMG Induction Heater
Marko, Fri Jan 11 2008, 01:56AM
kim_ladha wrote ...
Wow, lots of questions....
The feedback is definitly only possible from the actual tank circuit and only for inductor fed resonant tanks. I have 800 amps going through mine so it is hard to just use conventional techniques. To drop the current i put a loop of coax braid (any copper wire will do) soldered on one of the straight sections of the work coil. The connections are 1" appart and this 'resistivly' drops the current to 50 amps or so- this is simply due to the resistance of the copper pipe! Then i tried several closed ferrites but they all over heated. Finally I used a c core, the air gap stops saturation and it kept cool. This went into a 1:500 current xfmr (cheapo plasic type) to get a few milli amps which i use for my pll signal. (using the term pll loosly). I came up with the concept using pspice- the theory is sound and reliable.
As for the other things. 1). Use long plasic water pipes- water conductivity is not really a problem however
2). You can short out the work coil in my design, the current becomes square wave and switching losses are high- it doesn't break however. Same happens if you loose current feedback.
3). Grounding only represents a problem if the circuit fails and your touching the coil/water. I use an isolation transformer for testing so i don't die- no earth. The coil is live but safe to touch probably due to the high frequency. In a normal failure it will also be safe to touch. There is always a chance that the devices will short so that it is connected to live- although unlikely, I try and avoid touching it. For normal heating work you can just connect it straight to the mains- every device failure I have had in any equipment like this ALWAYS blows a fuse and isolates it. Of course- the time it doesn't could be your last so be careful!
4). No plans to upgrade circuit anymore. I am at the limit of what I can draw from a mains plug socket already! If I wanted to make a 5-6 kw version, the fgh50n6s2d looks like a safe bet.
Karim
Sir I'm very interested in how you made the thing work!
In some older discussions, steve ward was pointing out why is it not possible to have feedback on LCLR heater;
My understanding was that resonant frequency of entire system will be lower than tank frequency, and that you will be hard switching reactive power which is very unpleasant for IGBT's at that power level.
I was never into anything more than a hand-tuned IRFP450 driven LCLR heating a bolt red, but his theory made sense to me.
I don't know how are you making this thing pump that much power. :)
Sort of unusual to see a ferrite transformer cooking from a single turn winding...
I wonder if it would heat less if your burden was smaller (more opposing amp-turns)...
Or just a rogowski coil would probably work well for such currents..? :P
Oh, and how does your bridge output current waveform look?
Marko
Re:
OMG Induction Heater
Experimentonomen, Sun Jan 13 2008, 04:20PM
I cooked up a board today for my build and version of this induction heater:

Re: OMG Induction Heater
kim_ladha, Mon Jan 21 2008, 10:52PM
Hi Marko,
The simulation of the heater opposes your theory of feedback being a problem. When you tune to resonance with a light load and low matching inductor, the bridge current is 'almost' sinusoidal- my switching transistions are arround 12amps and my switching loss is low. As the load is increased (say by putting a bolt in the coil) the current bcomes hard switched and triangular. The switches exhibit higher losses and less power is drawn from the mains- 1kw. The steel quickly goes above curie temperature and becomes a lighter non-magnetic load. The frequency increases and the current goes somewhere between a sinusoid and a triangular shape- 2kw. Then the steel melts and becomes highly resistive (light load) and the current goes sinusoidal - 3kw.
If you simulate an LLC (inductor fed LC tank) heater you will see that the switching waveform at max power is in phase with the tank current- i.e. It is possible to use it to ocntrol the switches. You can check this in practice too but.... now the bit about ferrite getting hot.... remember that ferrite anywhere near the work coil causes alot of the generated field to pass through it and cause heating. The current transformer must be remote from the coil. Secondly, most current transformers can handle the current and overheat from losses or resisive heating. Finally, homemade current transformers have low coupling and give bad phase shifts as a result- 0.99 is quite low for this type application since the ferrite has to be physically large to fit round the work coil and hence has a large Al value- say you pick a nice big f44 ring with 6000nH al and 99% coupling with 100 turns (sound reasonable enough)- you end up with 6uH of stray inductance! The work coil is typically 1-3uH.... Basically, don't try and use a conventional current transformer.
I use a c core ferrite with only 50 turns passing through a normal current transfomer- I get a phase lag but I can still get almost exactly at resonance with this set up.
Let me know if you have any problems building one. If you replace the igbts with irfp450a's you can get 1kw without any problems. You might want to bypass their slow internal diodes if you want more power.
Regards
Karim
p.s. I meant to say triangle wave in my last post- the current is never square wave!
Re: OMG Induction Heater
GeordieBoy, Tue Jan 22 2008, 11:35AM
Sensing a continuous RF current in the work-coil that is in the hundreds or thousands of amperes is going to be troublesome. You can get around this in the LCLR arrangement by instead sensing the voltage across the tank circuit. You can do this with a small ferrite voltage transformer that can be conveniently located outside the alternating field of the tank circuit. Use twisted pairs leading to and from the VT to avoid pickup from the IH field. Although this voltage is 90 degrees out of phase with the current, you can compensate for this phase-shift in the control circuit.
Other options include using a Rogowski coil (to eliminate the lossy ferrite). This also gives a phase-shift but can be trimmed out in the controller. ...or alternatively a method that Steve Conner suggested to me recently, which is to parallel the tank capacitor with a PP cap of much lower value and then use a CT or sense-resistor to sense the much reduced portion of the tank current passing through this "sense capacitor."
Karim, when the Induction Heater is lightly loaded and draws 3kW from the wallplug have you thought where that power is going?
Re:
OMG Induction Heater
Tonskulus, Tue Jan 22 2008, 01:29PM
GeordieBoy wrote ...
Sensing a continuous RF current in the work-coil that is in the hundreds or thousands of amperes is going to be troublesome. You can get around this in the LCLR arrangement by instead sensing the voltage across the tank circuit. You can do this with a small ferrite voltage transformer that can be conveniently located outside the alternating field of the tank circuit. Use twisted pairs leading to and from the VT to avoid pickup from the IH field. Although this voltage is 90 degrees out of phase with the current, you can compensate for this phase-shift in the control circuit.
I have been using this method in some of my IH projects. Just o ferrite toroid that has some tens of turns primary winding, paralleled with workcoil. I made several single-ended self excited inductionheater oscillators using this method. Some commerical ind.heaters are using that kind of feedback too.
Re:
OMG Induction Heater
Steve Ward, Tue Jan 22 2008, 07:14PM
In some older discussions, steve ward was pointing out why is it not possible to have feedback on LCLR heater;
Perhaps "impossible" is a poor word. I was merely saying that its difficult to get ZCS by simply using a CT on the work coil and switching the bridge with a zero-cross detector (like my DRSSTCs do). As Karim already mentioned about his own setup, it is hard switched under many conditions. What conditions do give him ZCS, i will have to review for myself since it inherently seems strange to me for all of the currents to be in phase. I sort of think about it as an induction motor: if the winding current is phased such that its synchronous with the armature currents, then no torque is produced. Only when the stator and armature currents are "non-synch" does the induction motor do work (and hence they always operate at less than synchronous speed when loaded).
In any case, it should be obvious now that i really dont have the LCLR model fully understood in my head, and when i mentioned the difficulty of a simple feedback scheme, i was mainly commenting from my own experiences that failed to operate how i "wanted" them to.
Re: OMG Induction Heater
Experimentonomen, Tue Jan 22 2008, 08:17PM
I think that all it takes to get soft switching is shift the phase somewhere in the loop. Maybe this could be tested with one of those phase adjusters like those on subwoofers but modified for high freq rather than low.
Re:
OMG Induction Heater
Marko, Tue Jan 22 2008, 09:40PM
Big cheers Richie, welcome to forum!

This is one of threads you guys can be really proud with.
The simulation of the heater opposes your theory of feedback being a problem. When you tune to resonance with a light load and low matching inductor, the bridge current is 'almost' sinusoidal- my switching transistions are arround 12amps and my switching loss is low. As the load is increased (say by putting a bolt in the coil) the current bcomes hard switched and triangular. The switches exhibit higher losses and less power is drawn from the mains- 1kw. The steel quickly goes above curie temperature and becomes a lighter non-magnetic load. The frequency increases and the current goes somewhere between a sinusoid and a triangular shape- 2kw. Then the steel melts and becomes highly resistive (light load) and the current goes sinusoidal - 3kw.
Hard switching is not really such a big problem as long as magnetizing current isn't really too high, and everything just appears to be in limits here.
You must not be circulating lots of reactive power through the halfbridge as it pushes IGBT's and diodes hard. That is what I most feared of, but apparently I was wrong.
Richie wrote ...
...or alternatively a method that Steve Conner suggested to me recently, which is to parallel the tank capacitor with a PP cap of much lower value and then use a CT or sense-resistor to sense the much reduced portion of the tank current passing through this "sense capacitor."
And who could have a brilliant idea like that but Steve? makes me think ''how didn't I thought of that''?
That would allow a small CT, like 1:10 or maybe even 1:1, leakage inductance really killed down!
Makes me wonder why wouldn't we through all the time thought to use this in DRSSTC.
Tonskulus wrote ...
I have been using this method in some of my IH projects. Just o ferrite toroid that has some tens of turns primary winding, paralleled with workcoil. I made several single-ended self excited inductionheater oscillators using this method. Some commerical ind.heaters are using that kind of feedback too.
Tonskulus, how did you account for the phase shift? Fast integrator?
Very interesting thread, too bad I have poliprojectitis.
The biggest trouble are not the transistors but the water cooled capacitor, I could hardly get this far with MMC's.
Have fun guys and lots of molten steel,
Marko
Re:
OMG Induction Heater
Tonskulus, Tue Jan 22 2008, 11:00PM
Ok, my circuit is now up and running. Im using 74HC14 schmitt trigger and discrete component gate driver and GDT. I had some phasing problems earlier (either igbts or freewheeling diodes got really hot!) but solved this by changing some component values in feedback circuit. Tank capacitor, so far, is just MMC of 14 x 220nF/1000V plessey KP-series polypropylene foil caps. It stays cool enough at this powerlevel, about 800watts. Work coil gets so hot that watercooling is required for higher power levels. I took some pictures of the system:
http://www.elisanet.fi/tonskulus/ih/hothot.jpg http://www.elisanet.fi/tonskulus/ih/ssih_5.jpg And for the question about voltage feedback, it was commerically used in self-excited class-c oscillator induction heaters. Schematics can be found from google patent search:
http://www.google.com/patents?id=vNUgAAAAEBAJ&dq=self+excited+class-c Maybe this helps for designing voltage feedback but I think its not worth that. Current feedback seems to be just fine as we can see from kim ladhas induction heater.. :)
Re:
OMG Induction Heater
Steve Conner, Wed Jan 23 2008, 10:37AM
Hi guys,
First of all, in order to have real power flow through an inductor, the voltages at its two ends must differ in phase. The phase angle determines the real power flow, and when it's 90 degrees, you have as much real power flow as you're going to get.
Since we want the maximum real power flow, then, we want a feedback system that drives the inverter 90 degrees out of phase to the tank capacitor voltage.
Since the tank capacitor current leads the voltage by 90 degrees (this is always true for a capacitor) it's therefore suitable for a feedback signal. With the inverter locked to this, its output voltage will lead the tank voltage by 90', which is what's needed.
The work coil current is not quite the same as the tank capacitor current (it differs by the current injected from the inverter) but it seems to be close enough, since that's how Karim's circuit worked. Sensing the tank voltage and adding a 90' phase lead will work too.
Richie updated his induction heating page with a much more complete explanation than this.

Re:
OMG Induction Heater
Tonskulus, Wed Jan 23 2008, 11:31AM
Same happened again as always for me. It seemed to work just fine at 110V supplyvoltage. IGBT's and freewheeling diodes didnt get hot, just slightly warm.
Inverter voltage vs. current:
http://www.elisanet.fi/tonskulus/inverter_out.jpg And then, i decided to try this at full 220V supply voltage. I also added more inductance for zmatch to keep supply current at reasonable level, still 5..7Amps. It didnt last even one minute before igbt failure happened. Both were shorted. Is it possible that some shoottrough happened there for some reason? I had always the same problem with halfbridges driven at >100Volt supply. they wont suffer.
Re: OMG Induction Heater
GeordieBoy, Wed Jan 23 2008, 01:51PM
Although the devices died cold, shoot-through seems unlikely as there would be a lot of noise on the voltage waveform. Diode reverse recovery problems also seem unlikely as ringing on the current waveform suggests switching takes place before the current zero-crossing.
The voltage waveform looks strange though: Rounded leading edges and almost a 60% voltage overshoot! This may be exceeding the rating of your switches at the peaks of the supply voltage. That cosine shaped wiggle on top of the inverter voltage waveform (which should be flat) is usually indicative of excessive inductance in the DC bus wiring to the inverter. Try adding more capacitance across the DC bus right where the IGBT's are located.
Have you checked what your gate drive waveforms look like at the IGBTs during operation? It's also worth checking that your x10 (or x100) scope probes are correctly compensated before making these high-frequency measurements.
Re:
OMG Induction Heater
Tonskulus, Wed Jan 23 2008, 07:27PM
I just noticed that there is overshooting problem. Without load at all (inverter output open), there is still current going through igbts. 200mA or so. I did try adding 10µF capacitor to the DC supply rail and it helped smoothing invertrer voltage.:
http://www.elisanet.fi/tonskulus/ih/volts.jpg
Re: OMG Induction Heater
GeordieBoy, Wed Jan 23 2008, 08:53PM
That output waveform looks a lot better now.
With no load on the output of a half-bridge (or full bridge) you always get some current drawn from the supply, particularly when running at high frequency and high voltage. This 200mA current does not necessarily indicate shoot-through due to conduction overlap in the IGBTs. It may just represent the power required to charge and discharge the output capacitances of your switching devices.
(The power dissipated to charge/discharge device capacitances alone can get high for large die devices at high frequencies and high supply voltages. Eliminating this loss is the main motivation behind ZVS schemes like Class E, etc in power electronics.)
Re: OMG Induction Heater
Tonskulus, Wed Jan 23 2008, 09:58PM
Ok, i have been running this inverter today for a while with new igbts. Everything seems to be ok at 110Volts. I pushed this to the limits, 15Amps input current and no problems. But im sure it blows up if i switch to 220V. Thats what it always does. Yesterday I was running off 110Volts / 10Amps and decided to switch 220V. IGBT failure happened at only 4Amp supply current.
Re: OMG Induction Heater
kim_ladha, Wed Jan 23 2008, 10:12PM
Hi Tonskulus, Well done. Looks ok. The waveforms are either shoot-through or too much inductance on the low side drain- otherwise it should be working by now. Scrap that 10u cap though- the waveforms are fine. Geordie Boy hasn't realised the reason for the dodgy looking waveform- its is tracking the mains voltage. ....UPDATE- Yes he did! He has added a thread just after I posted this....This keeps your power factor high. I get 0.99 PF which is as good as a comercial unit!
Shame about the IGBT failures though- just looked at your other waveforms. The 10u won't solve shoot through it will just damp the ringing frequency. You need a dead time- I use 500ns ant 120khz- its high but seems to work reliably. You have some high frequency ringing on the collectors that looks suspicious- look for stray inductance. Finally make sure your oscillator is far from the work coil and shielded and the current feedback to the oscillator is minimal- current transformer saturation led to early unexplained failures for me.
Hi Steve, Awsome idea about the little cap to drop the current- Better than my solution. As for ZCS, it only occurs at high currents with low work coil loading. The work coild current is supperimposed onto bridge output by the ratio on the coil inductance to the inductor. If i have a small inductor i can get good zcs but high device currents. If I have a large inductor my current is almost triangular all the time. My ratio is 10-20 to 1 deppending what power i want.
Geordie Boy, the 3 kW low load power goes like this... all approx- 70w into switches, 100w into inductor (resisitive), 135w into my caps and the rest into water heating through resistive work coil losses (no work piece)- water goes in at 15 degrees and comes out at 70!
Regards to all
Karim
Re:
OMG Induction Heater
GeordieBoy, Wed Jan 23 2008, 10:16PM
Tonskulus: For debugging unexplained failures it helps if you can run it from a regulated adjustable DC supply to remove the 100Hz envelope blurring. Wind the voltage up slowly towards 340VDC whilst watching all the waveforms on a scope. The clues are there!
At the risk of getting my backside kicked for turning this thread into a lesson on inverter testing I'll leave it there.

-Richie,
Re: OMG Induction Heater
Tonskulus, Wed Jan 23 2008, 10:38PM
Without 10µF DC filtering cap there are huge amounts of ringing at inverter output! Anyway, im using 50Amp IGBT brick instead of HGTG30N60xx's. It drives ok at 100kHz. I have to get rid of some stray inductances and make a shield for oscillator/driverboard if it helps, just like Kim told me to do.
I'll keep working :)
Re:
OMG Induction Heater
Experimentonomen, Thu Jan 24 2008, 05:40PM
Hey kim! What is your comments on my board design ?

Re:
OMG Induction Heater
Tonskulus, Fri Jan 25 2008, 03:32PM
Finally Im able to melt some steel parts with this thing. Still 110Volt supply is used as it seems to work reliable now, I have no reason for higher input voltages to be used. Not for this one..maybe I can make another system for higher powerlevels later but its another story then. Ok, I made a short video about bolt being melted. Input voltage 110Volts and current 10..15Amps, 20A is maximum (limited by isolation trafo).
http://www.elisanet.fi/tonskulus/ih/ssih13.avi My workcoil didnt suffer, it collapsed and destroyed (full of holes) because there is no water cooling:
http://www.elisanet.fi/tonskulus/ih/bustedcoil.jpg
Re: OMG Induction Heater
kim_ladha, Sun Jan 27 2008, 08:04PM
Hi Tonskulus,
Nice work. I think you have pushed air cooled work coils as far as they can go!!
Hi HFsstc-freak,
Nice looking board. You should have no problems putting the 50 amp peak curents through your board. I would expect similar (probably better) performance to my pcb. The ultimate limitations is how you get rid of the excess heat. I was running mt setup at 3kw continuously and at just 40 degrees heat sink temperature I got an igbt failure- It takes 20 minutes to reach this temperature. I think the culprit is thermal runaway on the igbts. You might want to try a lower conduction loss version for a larger safety margin on newer designs like yours. The 20n60s are meant to be used for upto 3kw in this topology- I recon you need some kind of forced cooling of the devices to reach 3kw continuously though.
Regards
Karim
Re:
OMG Induction Heater
Marko, Sun Jan 27 2008, 08:54PM
Hello guys, Kim
oh do I hate mysterious IGBT deaths.
40 degrees C is really nothing I'd worry about, your cooling actually looks very good.
If I was really paranoid I'd just use water cooling on IGBT's too.
I don't know what you mean by thermal runaway... IGBT voltage drop actually decreases with increase of temperature. Paralleled devices can run away but even that is fixed well with mutual thermal coupling (bricks),
I don't really know why are your IGBT's dying sir.
Could it be that power dissipation just exceeds the limit (too high thermal resistance die->heatsink?) If that's it maybe it's time for you guys to move on bricks.
Have you tried to measure the output current of your inverter at various loads?
Still I don't think 70amp IGBT's should die so easily.
Richie wrote ...
At the risk of getting my backside kicked for turning this thread into a lesson on inverter testing I'll leave it there.
Hey, nobody will surly get you 'backside kicked', inverter design is like at least half of IH design so any of your help will be appreciated a lot!
Marko
Re: OMG Induction Heater
Dr. Dark Current, Sun Jan 27 2008, 09:40PM
Sorry no experience with induction heating, but my 40A IGBTs died too with just little warm heatsinks and ca. 10-15A peak current. I dont know exactly why it happened but:
1) IGBTs usually survive worse than similarly rated FETs
2) Too fast gate drive (with too sharp fall edges) decreases the device's turn off current capability.
Re: OMG Induction Heater
Experimentonomen, Sun Jan 27 2008, 10:47PM
Kim, did you ever check your gate waveforms ?
I drove 20n60 igbts with IR2110 and the IR2110 got very hot very fast due to the high current needed to drive the igbt gates, do your IR2184 get hot too ?
Maybe you have insufficent gate drive.
Re: OMG Induction Heater
Marko, Sun Jan 27 2008, 11:22PM
I'd really love to hear what Richie has to say on this 'too fast gate drive' thing...
I didn't ask, kim, you are saying that 40 degrees is heatsink temperature, have you actually attempted to measure it on IGBT's themselves? Maybe with some of those sticky probe thermometers.
Oh, and have you scoped your gates, how do they look like?
Marko
Re:
OMG Induction Heater
GeordieBoy, Mon Jan 28 2008, 12:59AM
> I'd really love to hear what Richie has to say on this 'too fast gate drive' thing...
Do you mean for Induction Heaters or MOSFETs or IGBTs in general?
Textbooks usually say "as fast as possible", but in real life this isn't usually the case, and the designer messes about with (read "optimises"!) the switching speeds in order to get a decent compromise between efficiency, reliability and EMI. It's a big subject and depends on the switching topology, devices chosen and the application spec.
I can elaborate more if you want but I'm not sure the discussion belongs here.
-Richie,
Re:
OMG Induction Heater
Steve Conner, Mon Jan 28 2008, 11:21AM
I think a discussion of gate drive would be great, but it's applicable to so much more than induction heaters, that it probably belongs in another thread, like this one
BTW, I've made a set of water-cooled copper busbars to hold my Celem capacitor, a ferrite-cored series drive transformer that also fits into the busbar assembly, and a new work coil. Will post pics when I get my internet working at home again...
Re:
OMG Induction Heater
Experimentonomen, Mon Jan 28 2008, 04:03PM
I bought some parts:

Re:
OMG Induction Heater
Marko, Mon Jan 28 2008, 05:28PM
yeah guys, moving that to another thread is a good idea.
Steve: cool, is the bus bar a single copper plate turn incorporated onto the transformer?

looking forward for your project.
Hfsstc freak, what is that water-cooled-transformer-like thing in the first pic?
Marko
Re: OMG Induction Heater
Experimentonomen, Mon Jan 28 2008, 07:19PM
Those parts are stuff from an Ajax Tocco Meltmaster induction heater cabinet, same one as the celem caps came from.
The transformer is the matching trafo. The boards are the mosfet gate drivers.
Re:
OMG Induction Heater
Kizmo, Wed Jan 30 2008, 09:35PM
I just took one half of my SGTC 75nF @ 24kV MMC (72x CDE 942C20P15K) and i will make heavy duty copper busbars to connect them in parallel. It would have been great idea NOT to solder them together when i made it

Those caps have proven to be almost indestructible in heavy spark-gap and drsstc duty. But will they cope with some induction heating..
Bank i planned would be like this:
- 36 capacitors
- 5.4uF @ 2000V
- 486A RMS @ 100kHz @ +70C (13.5A each)
- 15552A Peak current (432A each)
Now i think that would do some serious damage to poor bolts and nuts

Re:
OMG Induction Heater
Experimentonomen, Sat Feb 02 2008, 11:49PM
I fired up my version today and it worked on more or less first try.
Pics of test setup:

R.I.P matching inductor, i was running 50V input and around 7-10A current draw, all of a sudden all waveforms went screwed, power draw went beyond 10A, room lights dimmed and igbt's died, then i noticed L-Match had melted. However ther work piece got to a orange/yellow color.
Re: OMG Induction Heater
kim_ladha, Sun Feb 03 2008, 12:00AM
Hi All,
Sorry been away for a few days and questions have mounted up.
My gate drive waveforms are fine, The ir2184s get hot to touch but you can touch them. The igbt failure mode is unusual. The bottom of the igbts show melting in a patch on the device rear. This suggests this bit got hotter than the rest. I think that the thermal runaway I was speaking about occurs when part of the silicon die is hotter than the rest. This exhibits a lower on voltage and tries to take more of the current. The end result is that this bit fuses. The heasink is relatively cold when failure occurs (40 C). My igbt half bridge current is 40 amps rms at 120 khz (on last failure)- the datasheet says 20 amps at 100khz max- I think they are on the edge and hence die at relatively low temperatures.
Looks like people are getting things working though. I will post any improvements I make to improve reliability.
HFsstc-freak- Same thing happened to my matching inductor! Luckily I smelled the melted plastic fast enough! ou need to make the inductor large and flat to get rid of the heat better. Watch out for its magnetic field, it can induction heat things too!
Good luck to all... still waiting for someone to do a 10kw version :)
Karim
Re: OMG Induction Heater
Experimentonomen, Sun Feb 03 2008, 12:18AM
I also have an advice: Keep the feedback coil away from the work coil!!
I ended up putting my C-core on the inverter side of the tank cap to get clean waveforms and ability to run high current in igbt's without failures.
My igbt's died becase of too dirty stuff going through them, not by overheating.
Re:
OMG Induction Heater
kim_ladha, Sun Feb 03 2008, 05:34PM
Hi, as you know I had an unexpected 'cold' igbt failure under normal opperation. I fixed this and repeated the conditions under a more clinical environment with lots of probes.... I have found the cause!
When the high side transistor switches off, the current free wheels down through the low side igbt diode. The diode is fast but has a poor transfer characteristic. It allows the output to drop below the 0v line by a staggering 4v. This gets worse when the current is triangular. The current through my boot strap diode and the high side zenner is the only thing clamping it during this transistion. They get hot and fail- this causes everything else to break.
THE FIX- put a 47 ohm resistor in series with the bootstap diode. This lets the free wheel diode do its jub and stops all the problems... for now.
Next I tried Steve Wards current divider idea using a small poly propylene cap. The feed back of the current has a high BW and so there is a little more hash on the oscillator input but IT WORKS. This greatly simplifies the design and I would recommend it for new builds.
I reatached my schematic with the changes
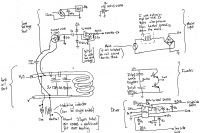
Re:
OMG Induction Heater
Kizmo, Sun Feb 03 2008, 05:50PM
Looks great! I just ordered some parts and i will try out that schematic (that would be my first proper IH, i have done only few ZVS versions) ...so prepare for stupid questions
As tank capacitor there will be bunch of these mounted on tightest possible arrangement to get low inductance:

Re:
OMG Induction Heater
Experimentonomen, Sun Feb 03 2008, 06:57PM
And here is my latest results:

Re:
OMG Induction Heater
kim_ladha, Sun Feb 03 2008, 07:26PM
HFsstc-freak-
The magnetic field provides a constriction force pushing on the outside of the washer. If you heat it up slowly you can get really cool effects as the melted parts of the washer flow inwards.
Like this one:
How much power are you using?
Regards
Karim
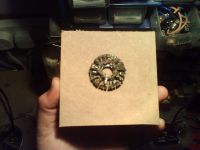
Re: OMG Induction Heater
Experimentonomen, Sun Feb 03 2008, 07:32PM
I had to cancel the heating proces becuase the washer started to give off too much smoke. Also i'm alittle scared to actually go up to melting since i don't have any good stuff to protect wooden table from hot metal.
In the vid, around 600-750W.
Re: OMG Induction Heater
teravolt, Mon Feb 04 2008, 03:03AM
HFsstc-freak what type of capacitor are you useing and do you have any recomondations. I want to do what kizmo is doing in his last thread because I cannot find any ceramic induction capacitors. any recomendations from any body my buget is about 100$
Re: OMG Induction Heater
Tonskulus, Mon Feb 04 2008, 02:32PM
Teravolt: Ceramic capacitors are used mainly in vacuumtube type induction heaters. Most solidstate types are using polypropylene- or similar cap or caps. Im not sure about construction details of celem caps but i think those are not ceramic. Just take a look for good quality polypropylene film-foil capacitors from Wima, Rifa etc. dv/dt is critical value so try to find caps that has high dv/dt value. It should be several kilovolts / µs. Im using 12 x 220nF plessey KP capacitors in parallel configuration (polypropylene foil) and they are just fine for 1..2kW.
Re:
OMG Induction Heater
Experimentonomen, Mon Feb 04 2008, 04:10PM
These are the caps i use:


Re:
OMG Induction Heater
Experimentonomen, Mon Feb 04 2008, 06:36PM
Update!!!

Re: OMG Induction Heater
teravolt, Tue Feb 05 2008, 04:37AM
thanks tonskulus I'll give it a shot. HFsstc-freek want to part with your celem
Re:
OMG Induction Heater
Experimentonomen, Tue Feb 05 2008, 03:58PM

<-- get your own!
Re: OMG Induction Heater
Experimentonomen, Sat Feb 09 2008, 10:50PM
My version of kim's ih reached 2kW today, 230V up to 9A.
Re:
OMG Induction Heater
Tonskulus, Thu Feb 14 2008, 12:59AM
I just rebuilt my system for PC case:
http://www.elisanet.fi/tonskulus/ssih/ssih_7.jpg It has still same driver board as previously but new halfbridge PCB is from MIG-welder. IGBT module is Semikron SKM150GB (150Amps) and it is faster than my previous one(Risetime 80ns/falltime 70ns, on/off times 160 and 40ns).
Tank res. frequency is about 60kHz.
And here, inverter current waveform:
http://www.elisanet.fi/tonskulus/ssih/v2_current.jpg Inverter voltage (measured from lowside igbt's D-S):
http://www.elisanet.fi/tonskulus/ssih/v2_voltage.jpg It is working good, so far 230V and 15Amps input has been tested. But im still worried about self-oscillating schmitt trigger. The resistor beetween i/o of trigger requires lots of care and finetuning. Mistuned resistor may lead excessive current drawn and may cause igbt failure. No matter if it's adjusted too high or too low, bad things may occur. i think that trigger is trying to mix these two signals and it messes everything up, it just cant be stable for reliable operation. So maybe it is time to go back to 4046 VCO..?
Re:
OMG Induction Heater
Experimentonomen, Mon Mar 10 2008, 08:40AM
I did a Tonskulus and got me some 50A igbt bricks, heres the result:

Re:
OMG Induction Heater
GeordieBoy, Thu Mar 13 2008, 12:16PM
Looks good Steve! ...but what did that poor bolt ever do to you!?!?
The switching waveforms look very clean on the scope - No doubt due to the actions of the board on the left?
Thanks for all the pics. Do you have a close-up of the ferrite power transformer used to couple power into the series-resonant tank?
-Richie,
Re:
OMG Induction Heater
Marko, Thu Mar 13 2008, 07:56PM
Steve that is awesome, welcome back

Oh, any transformer closeup pics for me too?
Are you using anything to control the current (hysteresis on-off control?) to regulate power and prevent the system from blowing up without a workpiece?
Hope to see that thing boxed up and put to use now

Just a noob question for the end, seeing Steve is using a series resonant system driving a practically resistive load at quite high frequencies with larger IGBT's, would there be merit to use a commutating inductor at the output of your bridge? Or maybe just put some small air gap onto the transformer core?
Keep this work up, all of you guys,
- cheers,
Re:
OMG Induction Heater
GeordieBoy, Thu Mar 13 2008, 08:24PM
seeing Steve is using a series resonant system driving a practically resistive load at quite high frequencies with larger IGBT's, would there be merit to use a commutating inductor at the output of your bridge?
I'd guess that if he wanted a slightly inductive load from the series resonant system he could just tune the driver slightly on the high-side of the tank circuit's resonant frequency, and the inverter would see a lagging current.
Or maybe just put some small air gap onto the transformer core?
...or like you said the magnetising inductance of the ferrite transformer will also act like a commutating inductor and contribute a small lagging component to the inverter load current.
-Richie,
Re:
OMG Induction Heater
Steve Conner, Mon Mar 17 2008, 10:20AM
Hi guys
Just an update on this...
For those who asked, I'll write this up as a proper project and give schematics and pictures of the transformer after Easter. I'm really busy just now.
I actually blew up the IGBTs trying to do levitation melting! I made a coil like the one Ameritherm show on their website, and it would just nearly levitate a small piece of aluminium. So I turned the current limiter off, turned my variac up to 260V, and I had the lump of aluminium floating and glowing a dull red for a few seconds, and then guess what happened.

The driver board is one of my Mk2 DRSSTC drivers, unmodified apart from the interrupter signal being jumpered permanently on. I found that it can't lock by itself when DC bus voltage is first applied. It needs the tuning pot to be twiddled until it locks. (this is best done at reduced DC bus voltage!) Once it's locked though, it seems to stay locked reliably as workpieces are moved in and out of the coil.
The DRSSTC current limiter seemed to work fine, untill I turned it off! When the workpiece was removed it would kick in. It made some audible noise, but didn't seem grossly unstable.
The transformer has 20 primary turns (IIRC?!) and one secondary turn of water cooled copper plate. The core is one of a selection that I bought off EastVoltResearch years ago, and I have no idea what grade of ferrite it is.
The IGBTs were some Fairchild FGH50N6S2D that I had left over from my SSTC experiments. I'm surprised they lasted so long, especially since they would have been running over 300kHz with the second work coil. I'll try again with a full bridge of IRFP460s. (These will probably be happier with a lagging current and some extra deadtime to give ZVS, as Marko and Richie suggested.)
More info after Easter! :P
Re: OMG Induction Heater
GeordieBoy, Mon Mar 17 2008, 02:05PM
Thanks for the info. I look forward to seeing more details when you have time.
The IGBT failures may just have been down to poor heatsink contact and thermal resistance in the Silpads. With better heatsinking and positive pressure over the die you could probably have run them harder.
-Richie,
Re: OMG Induction Heater
Steve Conner, Mon Mar 17 2008, 02:21PM
Yes, I forgot to mention that, the heatsinking was so bad I'm ashamed of it! The heatsink was pretty hot after it failed, and the devices were probably a lot hotter still due to poor thermal contact. Whatever devices I use next time, I'll be sure to try harder with the thermal management...
Re:
OMG Induction Heater
Marko, Mon Mar 17 2008, 02:50PM
Hi guys, thanks steve a lot for the post!
Are you using all of your celem caps, Steve? (don't see well behind that cup?) Your resonant frequency seems fairly high, I don't think you need closely that much unless you are for some special sort of surface annealing.
Are you limited with your capacitance vs. sane dimensions of the coil?
Under 50kHz seems to work pretty well, and people seem to do very well with common bricks like CM150's (I'm sure you have some around?), tons of power and thermal contact area.
Yes, I forgot to mention that, the heatsinking was so bad I'm ashamed of it! The heatsink was pretty hot after it failed, and the devices were probably a lot hotter still due to poor thermal contact. Whatever devices I use next time, I'll be sure to try harder with the thermal management...
Oh, didn't want to moan, I see you used a To3 sil pad under one IGBT? :O
Richie always recommended to actually use no sil-pads if possible and use separate heatsinks for each device.
ISOTOP and brick packages are OK; but due to their internal thermal insulator they may even have higher thermal resistance than direct contact of uninsulated TO247.
I even considered to solder the TO247 to copper but Richie didn't like that idea too much over simply screwing down the devices directly.
Re: OMG Induction Heater
Experimentonomen, Mon Mar 17 2008, 03:16PM
I hate mosfets! They blow instantly in my circuit, only igbt´s work reliably.
Re:
OMG Induction Heater
Steve Conner, Mon Mar 17 2008, 03:17PM
Hi Marko
I've only got one Celem capacitor, HFSSTC-Freak got to the Ebay auction before me
With a rating of 0.4uF, 500V RMS, 200A RMS, it would deliver its maximum 100kVA at 160kHz, but to get the frequency that low, I'd need either a very big work coil or some very small copper tube. I didn't want to make the work coil too big in case it failed to concentrate the magnetic field enough to melt or levitate anything. And I'm already using 4mm tube which is pretty thin.
Re: OMG Induction Heater
Experimentonomen, Mon Mar 17 2008, 06:05PM
Hey conner! How much ringing did you have on the transformer input ?
I am trying series feed and have this far blasted 200VAC in to the thing but i get loads of turn on rings on the transformer input, but this could be explained by the 0.5+ meter long leads between it and the inverter.
Re: OMG Induction Heater
Raka, Tue Feb 10 2009, 08:03PM
Is it really necessary to have the Schmitt trigger in the circuit? Isn’t it possible to use only an inverting mosfet driver like the TC4421 (with clipping diodes on the input), its got build in hysteresis as well.
Re:
OMG Induction Heater
Tonskulus, Thu Feb 19 2009, 11:39AM
Raka wrote ...
Is it really necessary to have the Schmitt trigger in the circuit? Isn’t it possible to use only an inverting mosfet driver like the TC4421 (with clipping diodes on the input), its got build in hysteresis as well.
Yes, because trigger also acts as "starting oscillator". Its self oscillating frequency is adjusted close to tank circuit resonant frequency by tuning feedback resistor.
My induction heater is still fine. Its been used for many times and many hours continously at 2..3kVA power.
So is seems to be reliable enough. No need to change blown mosfets or igbts every 5minutes.
I also made small curcible to melt some metals:
Only things that gets hot is cooling water and, ofcourse, workpiece itself. IGBT stays always under 40celsius, just slightly warm after 30mins at full power run.
Re: OMG Induction Heater
Raka, Thu Feb 19 2009, 08:14PM
Can’t you give the TC4421 some positive feedback, to make it self resonant?
Edit: I meant self oscillating
Re: OMG Induction Heater
Paragon, Sat Jul 17 2010, 02:44PM
Hello All,
I have been playing around with a similiar setup to Kim Lahda and would like to ask for some advice.
The snubber capacitors values for the half bridge that Kim states on his schematic are 7 x 1uf for each side.
Could someone please explain how this value was arrived at and also how critical this value is?
The reason I ask is that I am currently employing IRFP460's as switches due having aprox 70 of them that I picked up cheap and was wondering if I would require different value snubbers!
Thanks
SRG
Re:
OMG Induction Heater
IamSmooth, Sat Jul 17 2010, 05:49PM
SRG,
Refer to the middle of this page that shows the capacitors:

They filter out the DC component. I tried various combinations with my levitation coil that has near 50A on the primary side.

If the value is too high there is still some DC current that gets through. I found that when I got under 0.5uf I did not have a significant difference in the DC current. I just wound up with more expensive capacitors. My final cap values are 0.44uf. Each 0.44uf "capacitor" is made from two 0.22uf capacitors. Each capacitor can handle 750vac and 12A. This gives each leg 750vac/24A. So, I can handle 48A (full current cycle), with 50A pushing the limit.
So, in answer to your question, I choose my capacitors so they could handle the current and voltage, and filter out the DC current.
Here are the caps:

Re:
OMG Induction Heater
Paragon, Sun Jul 18 2010, 06:00PM
Firstly, thanks very much for the information you supplied IamSmooth,
Could you (or anone else) kindly help with L-match?
My inverter appears to be drawing way to much current, reading from the dc bus at 10v it is drawing around 2A!
Am I correct with my understand that the L-match inductor is to match impedance of the inverter to the load and by doing so also limits the current draw through the inverter?
According to the diagram below taken from RB's site the L-match inductor 45uh would you know how this value is arrived at?
Kind Regards,
SRG
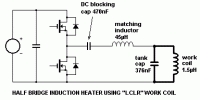
Re: OMG Induction Heater
GeordieBoy, Sun Jul 18 2010, 07:35PM
The matching inductor forms a conventional L-match circuit with a portion of the tank capacitance. It transforms the parallel load resistance of the tank circuit from what would be quite a high number of ohms down to a something in the region of 10 ohms load to be presented to the inverter. This lower impedance is much more suited to being driven by switch-mode power MOSFETs running directly off the mains line.
The L-match arrangement is just a combination of an inductor and capacitor connected in series that transforms one AC impedance into another AC impedance. It is commonly used in RF engineering to achieve impedance matching between things like power amplifiers and antennas in transmitter setups.
I don't have the equations in front of me now, but you should be able to do a google search for L-match equations/calculations whatever. Or i'm sure most of the usual amateur radio text books will cover this calculation in the early chapters.
I hope this helps,
-Richie,
Re: OMG Induction Heater
803, Mon Jul 19 2010, 02:57PM
WOW, A 3 YEAR LONG THREAD!! Go melting molten steel!
Re:
OMG Induction Heater
Paragon, Wed Jul 21 2010, 02:11PM
Thanks for your informative reply Richie.
Yep a three year thread that just won't die

I was wondering if these capacitors would suffice for tank capacitors.
MEA Capacitor 224k 0.22uF 2000V +/-10% Metallized Polyester as opposed to polypropylene?
The reason I ask is that I can get my hands on aprox 50 quite cheaply!
I don't think I can stretch to the Celem caps at this time, although saying that I have no idea what two csp150/200 would cost!?
Kind Regards,
SRG
Re: OMG Induction Heater
Inducktion, Sat Oct 01 2011, 03:41PM
I apologize for bringing this thread back alive, AGAIN, but I was wondering if it would be possible to try the schmitt trigger feedback system with a series resonant system...
Re: OMG Induction Heater
Gabriel35, Mon Feb 27 2012, 05:15PM
That's a Good Question...
I wanted to know that too
Re: OMG Induction Heater
Tetris, Tue Feb 28 2012, 05:09PM
When I first saw the title, I had to laugh. Of course there are only 17 576 permutations of 3 letter combinations. Induction heaters would be nice. Set it to low power, wear some sort of jacket with metal filings, and there, only the people who want to be warm in a house can be warm.
Re: OMG Induction Heater
Mark-H, Wed Feb 29 2012, 10:32AM
Surely, if you were wearing a jacket indoors, you wouldn't need an induction heater to keep you warm.
Just a thought.
Cheers.
Re: OMG Induction Heater
Gabriel35, Wed Feb 29 2012, 12:46PM
And what about the series ressonant topology using the same Kim's circuit...
Is it possible?
Searching some Induction Heater theories, everybody discovered that series ressonant topology is way better than parallel.
Re: OMG Induction Heater
Gabriel35, Tue Mar 20 2012, 06:12PM
Anyone?
Re: OMG Induction Heater
Steve Conner, Tue Mar 20 2012, 11:09PM
Don't know, I don't support Kim's circuit. But my own one works fine with series resonant.
The LCLR circuit has a parallel resonant tank, but the matching inductor performs an impedance inversion, so it probably looks similar to a series resonant circuit as far as the driver is concerned.
Re: OMG Induction Heater
Gabriel35, Thu Mar 22 2012, 02:12AM
Interesting... Can't wait to try it up and see what happens...
What variant are you using Steve?
Do you have any schematics of it?
Re: OMG Induction Heater
Dr. Dark Current, Thu Mar 22 2012, 12:54PM
A series resonant induction heater without current limiting has a little problem, and that's that it explodes with no load.
Re:
OMG Induction Heater
IamSmooth, Thu Mar 22 2012, 01:18PM
Dr. Dark Current wrote ...
A series resonant induction heater without current limiting has a little problem, and that's that it explodes with no load.
I noticed that the current would go through the roof when I removed the load. That is why I had the uP limit the current by going off resonance if this happened.
Re: OMG Induction Heater
Steve Conner, Thu Mar 22 2012, 01:26PM
The LCLR has the same problem too, due to the impedance inversion.
Current-fed inverters driving parallel resonant tanks (eg: Royer, vacuum tube oscillator) do the opposite: the current draw decreases to a safe level when the workpiece is removed.
But the downside is that the power throughput also decreases when a ferromagnetic workpiece goes above its Curie temperature, and that's just when you need the power to stay high, if you want to melt it. Using more power to start with will fix it.
The circuit I used was just my Mk2 DRSSTC driver with the interrupter wired permanently on. It has a current limiting circuit that took care of the no-workpiece problem.
Re:
OMG Induction Heater
Kizmo, Thu Mar 22 2012, 07:16PM
Steve Conner wrote ...
The circuit I used was just my Mk2 DRSSTC driver with the interrupter wired permanently on. It has a current limiting circuit that took care of the no-workpiece problem.
Thats almost same what im using. Normal drsstc driver, feedback from tank circuit current and OCD current transformer is measuring inverter output current.
Im also planning to use slightly modified interrupter for power control.
Re: OMG Induction Heater
Gabriel35, Fri Mar 23 2012, 02:32AM
But what about the L-match Inductor?
Isn't there to avoid high current surges when Load is removed from the workcoil?
Re:
OMG Induction Heater
Steve Conner, Fri Mar 23 2012, 06:39AM
No, it's not.

It's an impedance transformer that allows the work coil current to be higher than the inverter output current.
Re: OMG Induction Heater
Gabriel35, Sat Mar 24 2012, 02:11PM
Well, but when using a series tank topology, reducing the number os turns on the primary of the toroid, means more current draw on the inverter.
Right?
Re: OMG Induction Heater
GeordieBoy, Sat Mar 24 2012, 11:55PM
Steve Conner is right. An LCLR induction heater is just as capable of blowing up with no load as one using a simple series resonant tank if it's not controlled appropriately.
With no load in the series resonant tank the Xl and Xc reactances of the work coil and tank cap are equal and opposite at resonance. They cancel-out leaving very little series resistance in a low-loss work coil arrangement with no workpiece. There's no "loss" in the system to limit the current rise due to high Q-factor. So if you don't back off the drive the inverter current will quickly go sky high, along with the tank current and tank component voltages and something has to give.
With the LCLR arrangement it's not as easy to see what happens with no workpiece present. Again there is very little loss in an efficiently designed tank system and the Q factor goes high. At a particular frequency the Xl and Xc of the work coil and tank cap don't quite cancel out, and leave just enough net capacitive reactance to perfectly cancel out the inductive reactance of the matching inductor. The end result is a very very small resistive load and large current rise again if you linger at this spot frequency for too long without backing off the drive.
Of course in practice, you would detect either the inverter output current rising, or the tank voltage/current getting too high and detune the drive frequency, reduce the inverter output voltage, or take some other measure to limit the ring-up of energy in the tank circuit before something blows up.
So in reality the series resonant tank and the LCLR arrangement don't behave that different. The LCLR just has a lot of practical implementation advantages like keeping the main induction heating current out of the inverter and confined to a small loop local to the heat station. It is also fault tolerant to a s/c of the work-coil or tank capacitor, both resulting in the inveter being presented with a light inductive load.
One good way to get your head round the LCLR tank arrangment is to split the physical tank capacitance into two halves C1 & C2. Then think of the LCLR arrangment as a series-resonant tank circuit (consisting of the matching inductor and C1) feeding a parallel-resonant tank circuit (C2 and the work coil) connected across the C1 of the first series resonant circuit. The first series-resonant LC circuit provides the impedance matching between the inverter and the load, and the second parallel-resonant tank circuit effectively provides power-factor-correction for the work-coil by parallel resonating it's inductance with a local "PFC" capacitance, therefore containing the large circulating current in the work-coil.
-Richie,
Re: OMG Induction Heater
IamSmooth, Sun Mar 25 2012, 02:51AM
Kizmo, how are you cooling your igbts?
Re:
OMG Induction Heater
Conundrum, Sun Mar 25 2012, 06:24AM
Someone please do an "induction soldering iron" build

Hand held, runs off internal Li+ batteries and allows you to heat a bolt, screw etc to red heat from 2" away.
see

-A
Re:
OMG Induction Heater
Kizmo, Sun Mar 25 2012, 07:23AM
IamSmooth wrote ...
Kizmo, how are you cooling your igbts?
130x120x300mm heatsink and 120x120x38 fan
Re:
OMG Induction Heater
Steve Conner, Sun Mar 25 2012, 07:25AM
Kizmo, from your waveforms you look a bit out of tune.

The inverter current is supposed to be in phase with the voltage so you can have ZCS. That's more important than ZVS, especially when pushing the limits of slow IGBTs.
Re: OMG Induction Heater
Kizmo, Sun Mar 25 2012, 07:37AM
How can it be out of tune with self oscillating driver? :)
This is just drsstc driver and im using tank current to generate feedback signal which is in phase with tank current.
EDIT:
I was told earlier that poor inverter power factor is known "feature" of simple LCLR heaters and there is not much one can do about it.
Re: OMG Induction Heater
Steve Conner, Sun Mar 25 2012, 08:38AM
Well, surely you should be using the inverter output current as the feedback source, not the tank current.
With the series resonant heater, the two currents are in phase because they're the primary and secondary currents of the transformer. But in the LCLR they're out of phase, because a phase shift is necessary to transfer real power through an inductor.
Re: OMG Induction Heater
Kizmo, Sun Mar 25 2012, 08:42AM
I tried taking feedback from inverter current and guess what happened..
I found out that the resonant frequency of my matching inductor and DC block capacitor is about 6kHz. Couldnt get it working at all.
Re:
OMG Induction Heater
Steve Conner, Sun Mar 25 2012, 11:58AM
Oh, I forgot you don't have a proper driver with a PLL.

A simple feedback circuit will oscillate at whichever resonant frequency has the highest loop gain. So, you could include a highpass filter in the feedback circuit to lower the loop gain at 6kHz, and make it prefer the frequency you want.
If you can't easily design a filter that blocks 6kHz without unwanted phase shift at the operating frequency, then design the best filter you can and make the DC block cap bigger to lower the frequency of the unwanted resonance. Although, the phase shift at the operating frequency might even be beneficial as it would work like a "Prediktor".
Re: OMG Induction Heater
Kizmo, Sun Mar 25 2012, 12:06PM
I think im done with this topology. Already got 2 kilos of power ferrite and some copper tubing for series resonant transformer fed tank circuit :)
Re:
OMG Induction Heater
Steve Conner, Sun Mar 25 2012, 01:30PM
I suppose I have to agree with you, since I've only ever built series resonant heaters!
I chose series resonant because:
The inverter output current is in a fixed ratio to the work coil current, so a single overcurrent detector can measure and limit both. If you put a limit on the PLL tracking range, it can also protect the tank cap against overvoltage. (Tank cap voltage is proportional to current and 1/frequency.)
The feed transformer isn't that much bigger/harder to build than the matching inductor of a LCLR. The only problem is the massive water-cooled secondary winding, but we 4hvers enjoy building things like that

The feed transformer isolates the work circuit from the inverter, which is usually not isolated from the mains.
But Richie says the LCLR is theoretically better. I can't remember why, maybe he can comment?
Re: OMG Induction Heater
Kizmo, Sun Mar 25 2012, 01:51PM
The transformer gets rather large when its made from ferrite, drive voltage is high (320V p-p) and highest possible frequency is 32kHz (limited by tank capacitor)
Re: OMG Induction Heater
Kizmo, Sun Mar 25 2012, 04:47PM
Almost done. One question: With transformer fed series resonant topology i have to include transformer high current side winding inductance with work coil and wiring inductance when figuring out the resonant frequency?
Wonder how low it will drop :)
Re: OMG Induction Heater
Steve Conner, Sun Mar 25 2012, 05:47PM
Yes, you do.
To avoid excessive inductance, I built my transformer right into the heat station as an extension of the capacitor's water cooling plates. That also got the secondary water cooled as a bonus. And I wound the primary inside the secondary, on the same core limb, again to minimise leakage inductance. (Since the inverter is a voltage source, it's the leakage inductance that's relevant.)
But a little extra inductance may not be a problem, it will reduce the change in operating frequency with workpiece type.
Re: OMG Induction Heater
Kizmo, Sun Mar 25 2012, 06:00PM
Then its back to the drawing board. I cant have much more than 10uH of extra inductance :)
Re: OMG Induction Heater
IamSmooth, Sun Mar 25 2012, 06:06PM
Kizmo, at your power levels I would suggest liquid cooling. You will loose IGBTs from overheating.
Re:
OMG Induction Heater
Steve Conner, Sun Mar 25 2012, 06:06PM
Well, here's mine :)
I sold it, as far as I know it's now being used for a student project somewhere.
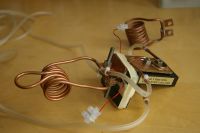
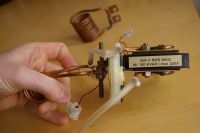
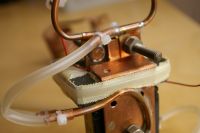
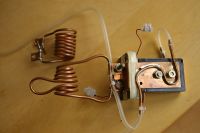
Re:
OMG Induction Heater
Kizmo, Sun Mar 25 2012, 06:27PM
IamSmooth wrote ...
Kizmo, at your power levels I would suggest liquid cooling. You will loose IGBTs from overheating.
Yeps that is of course another option but i would like to fix the main cause of heating which is switching losses during turn off. And that is of course caused by poor power factor of this type of feedback method.
Re: OMG Induction Heater
Kizmo, Sun Mar 25 2012, 06:56PM
This whole transformer idea is starting to feel stupid. I cant have more than 5uH of inductance from transformer or this thing will turn into ear wrecking machine. And there is no way i can fit enough windigs on any of my smaller ferrites :(
Re: OMG Induction Heater
Steve Conner, Sun Mar 25 2012, 07:12PM
How are you calculating the inductance? It's the leakage inductance, so to a first approximation, it's the inductance of the secondary by itself with the primary and core removed. In practice slightly less, if you wind the primary close to the secondary as I did.
That should be much less than 1uH. To keep a sense of scale, I remember that a 10 inch diameter loop has an inductance of about 600nH.
Re:
OMG Induction Heater
Kizmo, Sun Mar 25 2012, 07:22PM
Now you made me feel like ultra stupid

I tought its the inductance that one can calculate from nH/turn^2 value...
Leakage inductance as you described it is no problem at all. I was just about to tear whole days worth of work apart and call it epic fail :p
Re: OMG Induction Heater
IamSmooth, Mon Mar 26 2012, 12:23AM
Steve, the coil you showed...that looks like a levitation coil. What have you suspended?
Re:
OMG Induction Heater
IamSmooth, Mon Mar 26 2012, 12:25AM
Kizmo wrote ...
IamSmooth wrote ...
Kizmo, at your power levels I would suggest liquid cooling. You will loose IGBTs from overheating.
Yeps that is of course another option but i would like to fix the main cause of heating which is switching losses during turn off. And that is of course caused by poor power factor of this type of feedback method.
What is your frequency?
Re:
OMG Induction Heater
Kizmo, Mon Mar 26 2012, 05:28AM
IamSmooth wrote ...
Kizmo wrote ...
IamSmooth wrote ...
Kizmo, at your power levels I would suggest liquid cooling. You will loose IGBTs from overheating.
Yeps that is of course another option but i would like to fix the main cause of heating which is switching losses during turn off. And that is of course caused by poor power factor of this type of feedback method.
What is your frequency?
Limited by capacitor between 16 and 32kHz. This first prototype ran at 44kHz and at this frequecy calculated turn-off losses (=hard switching) are almost 800W/transistor.
Re: OMG Induction Heater
Steve Conner, Mon Mar 26 2012, 06:59AM
Iamsmooth: I've levitated a small piece of aluminium tube, but I had to push the setup to the absolute limit. I turned the current limit up too high, and when the piece melted, it got unstable and fell out of the coil, and my IGBTs went boom.
Levitating a solid sphere of metal would take lots more power.
Re: OMG Induction Heater
Dago, Mon Mar 26 2012, 10:17AM
I wonder why (all?) commercial heaters use the LCLR-topology, cause the poor power factor does make it sound pretty bad? Can you compensate the poor power factor in any way?
Re: OMG Induction Heater
Steve Conner, Mon Mar 26 2012, 10:23AM
Yes, if you drive it at the correct frequency, you get unity power factor just the same as the series resonant.
The correct frequency is not the resonant frequency of the tank circuit, but slightly above, where the tank circuit appears as a capacitive reactance of the right magnitude to cancel the inductive reactance of the matching inductor.
Ameritherm's small heaters use series resonant. I got the idea from some gut shots that were shared in the 4hv chat years ago.
Re: OMG Induction Heater
IamSmooth, Mon Mar 26 2012, 01:25PM
As I mentioned earlier, I used series resonant, got it up to 12kw of power and did all kinds of crazy stuff. At these power levels you need to make sure you stay slightly above as Steve mentioned. If you start get to the true resonance or below the switches will go boom. I put a 60A fast-blow going to the inverter to protect my board from secondary frying if the switches shorted.
I minimized my switching loses with lower frequencies and fast turnon/turnoffs. One issue with faster transitions is the ringing, which has to get snubbed, or else you will have a worse situation. As far as the frequency: while I used lower frequencie for melting bricks of iron, I used frequencies close to 120 kHz, but was still able to get rid of the heat without compromising the mosfets.
You might want to consider using mosfets if you are using frequencies above 20-30khz.
Re: OMG Induction Heater
Gabriel35, Mon Mar 26 2012, 01:41PM
The discussion Is getting Interesting!
Unfortunatly I've never succeded with a PLL driven Induction Heater, But I'll not stop trying...
Currently I'm in doubt of what topology to use...
I'll try some of them and see what happens...
Re:
OMG Induction Heater
Kizmo, Mon Mar 26 2012, 03:40PM
IamSmooth wrote ...
As I mentioned earlier, I used series resonant, got it up to 12kw of power and did all kinds of crazy stuff. At these power levels you need to make sure you stay slightly above as Steve mentioned. If you start get to the true resonance or below the switches will go boom. I put a 60A fast-blow going to the inverter to protect my board from secondary frying if the switches shorted.
DRSSTCs are switched at perfect resonance at current zero crossings and they dont blow up...?
EDIT:
I guess i have to explain my idea of how im going to do this heater.
Series resonant tank circuit. 10µF 1kA celem capacitor, about 3µH work coil + stray inductance. Resonates roughly at 29kHz. Coupling transformer is just large ferrite transformer with 1:10..1:20 ratio. Feedback is taken from tank circuit current with measuring capacitor (150nF cap in parallel with celem and small ferrite CT). Inverter is igbt half bridge powered by rectified 3 phase and im not planning to use any filter capacitance on bridge, just couple µF worth of film caps. Driver is normal DRSSTC driver with interrupter.
Interrupter would be outputting pulses with 0-99% ON time. Idea behind this is to be able to have at least some sort of power control by varying on time. Drsstc has of course zero crossings synchronized over current protection which in this case would be measuring inverter output current. I guess if needed i could add another overcurrent protection circuit that measures tank current via same measuring capacitor. That would serve as tank capacitor over current/voltage protection.
Due to my limited knowledge, i dont see why this kind of contraption wouldnt work. At least it has proven itself in drsstc world. If you see potential problems, please stop me before i waste my time ;)
Mcu controlled PLL driver is *far* too complicated for my knowledge

Re: OMG Induction Heater
GeordieBoy, Mon Apr 02 2012, 11:48AM
> But Richie says the LCLR is theoretically better. I can't remember why, maybe he can comment?
The work-coil circuit is really just an impedance matching network to convert the unfeasibly low impedance of a lump of solid metal up to a figure that is realistic to present to a solid-state inverter running directly off the mains line. I don't think it really matters how you achieve this impedance transformation as long as it is done efficiently because the currents and voltages at work in IH are large.
I prefer the LCLR network for a number of reasons:
1. It keeps the enormous induction-heating current confined to the work-coil / tank capacitor loop. This loop can be made very small and may be located remotely from the inverter.
2. It does away with the need for a high-power high-frequency transformer requiring careful design to minimise core/copper losses and water cooling to carry away the heat from whatever dissipation remains.
3. It is better to alter the impedance matching by varying the air gap in the matching inductor than to change taps on a transformer. A multi-tap transformer implies poor winding window utilisation for certain tap choices resulting in an overall bigger transformer unless series/parallel winding combinations are used.
4. Stray inductance in the wiring between the inverter and the heat station merely adds to the matching inductance, rather than adding to the work coil inductance and reducing coupling to the workpiece.
5. The LCLR network presents a light inductive load to the inverter in the case of a tank capacitor or work-coil short circuit making the system s/c tolerant to faults at the heat station.
6. If the matching inductor is located close to the inverter it reduces HF switching noise leaving the enclosure improving EMI performance.
7. In high-power systems the tank circuit can be fed from several inverters in parallel through several matching inductors. The "ballasting action" of the matching inductors provides inherent current sharing. It also limits the "shoot-between" currents resulting from imperfect syncronisation of the inverters' switching transitions. (This way solid-state systems in the MW and 100's of kHz range can be realised with a high level of redundancy.)
The downsides of the LCLR matching network are:
1. It is more complex to understand the resonance transformation than impedance transformation with a transformer.
2. Leakage fields from the matching inductor can heat nearby metal enclosure!
3. No galvanic isolation of the work-coil from the mains line.
-Richie,
Re:
OMG Induction Heater
IamSmooth, Mon Apr 02 2012, 09:30PM
GeordieBoy wrote ...
I prefer the LCLR network for a number of reasons:
-Richie,
Richie, you must have seen my schematic for the work coil. It is a coupling transformer from the switches (10-20:1) around the wire going to a series LC tank. If I were to improve the tank circuit, what would I need to do? A different topology or is this one reasonable? I was able to abuse it without failure, but I'm always interested in other and better ways of doing things.
Re: OMG Induction Heater
GeordieBoy, Tue Apr 03 2012, 11:50AM
hey, if it aint broke then don't fix it! If it meets your requirements and even survived abuse without catching fire then it doesn't sound like you have anything defficient to improve.
-Richie,
Re:
OMG Induction Heater
Kizmo, Sun Apr 08 2012, 07:10AM
Series resonant version has been great success.
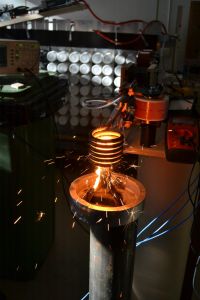
Some youtube clips

Boiling water

Melting car motor parts

Aluminum heating fail :)
Re: OMG Induction Heater
Gabriel35, Mon Apr 09 2012, 01:59AM
Very nice videos Kizmo! Pretty nice to see it in HD.
What's the schematic that are you using?
Re: OMG Induction Heater
IamSmooth, Mon Apr 09 2012, 02:38AM
Nice job. I miss mine.
Schematics. Also, how are you maintaining a frequency lock as the metal heats?
Re: OMG Induction Heater
Gabriel35, Tue Apr 10 2012, 02:26AM
Want to know that too!
Re: OMG Induction Heater
Josh Campbell, Sat Nov 03 2012, 05:01PM
Hey Kizmo, I hadn't asked because I noticed others had already asked for schematics but, ya, would love to see those as well. It looks like a DRSSTC setup and I'm sure it's close, but the devil is in the details. Also I was really curious about your tank coupling. Regarding the inverter connected directly to the tank through a matching inductor and dc blocking caps, aren't you worried about not having isolation from mains on the working coil? Seems dangerous. Maybe I'm not seeing it correctly in the videos but that's what it looks like. I know the LCLR setup is obviously a working proven method, but I would be curious to see the potential difference between your working coil and say earth ground or mains neutral during operation. Anyway, great build, would love to see more of those details.
Re: OMG Induction Heater
Kizmo, Sat Nov 03 2012, 05:35PM
It used to be based on LCLR topology with matching inductor but my big slow 400Amp igbts didnt quite like the way this simple feedback driver makes them hard switch at turn off.
So i converted it later to transformer coupled series resonant thingie. And i power all my builds from 3phase isolation transformer stack so i dont have these grounding issues. Going from LCLR to series resonant reduced transistor heating by a lot :)
Re: OMG Induction Heater
Gabriel35, Mon Nov 12 2012, 07:34PM
And do you have the schematic of this Kizmo?
I would like to see it too!
Re: OMG Induction Heater
Gabriel35, Fri Feb 15 2013, 07:16PM
Hey months passed since somebody posted thing here last time.
Still waiting to see the details of the schematic Kizmo!
Thanks!