Problems with 555 Flyback Driver and Flyback Driver Discussion
Firefox, Fri Jul 04 2008, 02:54AM
I just finished Uzzor's simple 555 flyback driver, pictured
here, and tried testing it, only to have one cooked 200V 10A MOSFET. The driver seemed to be working fine (I'm going to have to find a speaker to hook it to) but the FET didn't like being where it was, and was hot enough to burn my finger after only a couple seconds of power. My power source was the 12V 15A rail of a ATX PSU. Could it be that the impedance of my circuit is too low, and I am drawing more amperage than the FET can handle?
I have also made a few small changes to the circuit. I used a 100k potentiometer and a 10 ohm gate resistor. I also added a 2uF film cap across the power supply.
[Edit] I'm expanding the scope of this thread to include all discussion on flyback driver, due to the wealth of information posted as alternatives and upgrades to the 555 driver. Feel free to add your thoughts and experiences as you see fit.
Re:
Problems with 555 Flyback Driver and Flyback Driver Discussion
Dr. Dark Current, Fri Jul 04 2008, 06:39AM
I have this circuit on my pc and post it every time someone asks about 555 flyback driver

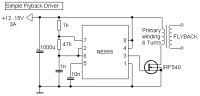
Some notes:
-the fet shoult be rated approx. 6-10 times the voltage of your PSU, but not more as it will have too high Rds(on)
-your 68ohm gate resistor is too big, you can remove it completely or use something like 10 ohms
-your FET has probably too high Rds. Something aroud 50-100mOhm max. should be okay (e.g. IRF540)
-it will get quite hot anyway, there is a "quasi-resonant" mod for this circuit which involves few extra components but makes the fet run often much cooler.
-these drivers work best at around 70V supply voltage (555 has its own supply) and 500V FETs (IRFP460)
Re: Problems with 555 Flyback Driver and Flyback Driver Discussion
cjk2, Fri Jul 04 2008, 02:06PM
A snubber is probably needed to stop the fet from overheating. Try a TVS or chose a capacitor of the correct value.
Re: Problems with 555 Flyback Driver and Flyback Driver Discussion
Marko, Fri Jul 04 2008, 03:45PM
It is normal for mosfets to die in a circuit like this when we attempt to draw arcs, or charge large capacitances which will both 'clamp' the output voltage to some value.
I did not understand it myself until recently, but I now only see a great amount of misconceptions being spread over and over, which I would like to stop.
It needs to be understood that any transformer or inductor can work only with AC, and will represent a dead short to any DC component. Volt-seconds in positive halfwave need to always be same as volt-seconds in negative halfwave; although their shape is irrelevant.
A flyback is just a transformer with relatively low magnetizing inductance due to large air gap introduced in it. It works by putting an amount of energy into this magnetizing inductance while switch is on and releasing it into secondary while it is off.
If we drive the switch by constant duty cycle from NE555, we have predetermined the volt-seconds we put into positive halfwave with each cycle.
The expected problem is, if we loaded the output of the transformer with an arc - there is absolutely nothing assuring that negative half-wave volt-seconds will be the same as what we predetermined.
Due to low impedance of an arc the negative voltage is actually going to be clamped to some very low value. If we attempt to charge a large HV capacitor, like to run a tesla coil, the same will happen as capacitor basically represents a short to DC output.
In any case, when positive and negative Vs aren't trimmed, the current will integrate up for their difference. This is how the DC component appears in the primary -not instantly, but over a period of several cycles. At some point the flux (which follows the integrating current) will saturate the core, decreasing the primary inductance heavily and overheating the switch.
I'm pretty sure this is what happens in all those ''NE555 flyback drivers''.
Snubber like a TVS or RCD clamp will do nothing for this. It will absorb energy put into the transformer in case output is unloaded (which will be a great deal of heat on the snubber).
In case clamp is not present this heat will simply be dissipated in the switch avalanching.
The quasi-resonant scheme is what is used in TV's, IIRC, and it is only that can actually restore energy to supply bus and increase efficiency a bit. Still it does absolutely nothing about the core saturation problem.
Sometimes the circuit can work, but relatively poorly. I think it is because, as the core approaches saturation, the output diminishes, and voltage drop across the arc increases until it gets high enough to balance the volt-seconds and stop the flux walking.
But still it usually results in hot transistor and hot ferrite core.
The industry standard way of solving this problem is called Current Mode Control, which actively prevents the current integration by cutting the cycle off when current reaches predetermined value. Look for datasheets and application notes on UC384* series of SMPS controllers.
Only with current mode control you could safely charge capacitors and draw arcs without problems.
But, still there would be the problem of what happens to the converter when unloaded - this may be solved by quasi-resonant drive, or voltage feedback. Voltage feedback would again, along with all control loop problems, probably make impossible drawing of stable arcs from the output - and who wants a flyback driver he can't draw arcs from!
And after all you have done you would just have a flyback driver, and I guess not a too powerful one.
To cut it short, building an efficient and powerful flyback converter that can perform all feats you guys want is probably one of hardest and most pointless things in electronics I can think off.
So, my advice is:
- Ignore Jan Martis, his site, and all the schematics of ''NE555 flyback drivers'', never build them. And I'm saying that solely because I'm evil. ( :D )
- For driving flybacks at low power levels (up to 500W or so), with all feats you need (drawing arcs, capacitor charging..), I can't think of anything better then ''Mazzili'' flyback driver, or a simple halfbridge of mosfets driven by SG3525, TL494 or some other controller. They each have their + and - but it's mostly about what input voltage do you want to use.
- For higher power levels, it is just that flyback transformers won't stand them for long. But if you own a dedicated transformer, my probably sole recommendation would be an SLR inverter.
Marko
Re: Problems with 555 Flyback Driver and Flyback Driver Discussion
Firefox, Fri Jul 04 2008, 04:37PM
Marko, if I'm understanding what you are typing, are you saying its only luck that people have been able to get 555 drivers to work at all?
Re:
Problems with 555 Flyback Driver and Flyback Driver Discussion
Marko, Fri Jul 04 2008, 08:54PM
Firefox wrote ...
Marko, if I'm understanding what you are typing, are you saying its only luck that people have been able to get 555 drivers to work at all?
Well, you could get it to work, and I mentioned a reason why, although efficiency will always be poor. I don't see a point as equally simple or only slightly more complex circuits can easily achieve what you guys want. There is no point pursuing the wrong way.
Re:
Problems with 555 Flyback Driver and Flyback Driver Discussion
GeordieBoy, Fri Jul 04 2008, 09:35PM
Marko wrote:
Volt-seconds in positive halfwave need to always be same as volt-seconds in negative halfwave; although their shape is irrelevant.
A flyback is just a transformer with relatively low magnetizing inductance due to large air gap introduced in it. It works by putting an amount of energy into this magnetizing inductance while switch is on and releasing it into secondary while it is off.
If we drive the switch by constant duty cycle from NE555, we have predetermined the volt-seconds we put into positive halfwave with each cycle.
...if we loaded the output of the transformer with an arc - there is absolutely nothing assuring that negative half-wave volt-seconds will be the same as what we predetermined.
Due to low impedance of an arc the negative voltage is actually going to be clamped to some very low value. If we attempt to charge a large HV capacitor, like to run a tesla coil, the same will happen as capacitor basically represents a short to DC output.
In any case, when positive and negative Vs aren't trimmed, the current will integrate up for their difference. This is how the DC component appears in the primary -not instantly, but over a period of several cycles. At some point the flux (which follows the integrating current) will saturate the core, decreasing the primary inductance heavily and overheating the switch.
I'm pretty sure this is what happens in all those ''NE555 flyback drivers''.
Totally agree with everything Marko wrote here. This is *exactly* what happens when you short-circuit the output of a flyback converter that has fixed programmed duty ratio. The fixed on-time keeps pushing more energy packets into the core but the shorted output doesn't allow any energy to escape during the off-time. Marko's explanation is spot on.
Snubber like a TVS or RCD clamp will do nothing for this. It will absorb energy put into the transformer in case output is unloaded (which will be a great deal of heat on the snubber).
In case clamp is not present this heat will simply be dissipated in the switch avalanching.
Agreed again. The way that circuit is drawn, with no load on the output the peak voltage developed across the switch immediately after the on-time will be the MOSFET avalanche rating. All of the energy put into the flyback transformer during each on-time will be dissipated in avalanching the MOSFET during the early part of the off-time.
The flyback circuits in TV receivers actually use a quasi-resonant arrangement where a resonant capacitor connected across the switch makes the energy stored in the primary winding re-circulate resonantly if there is no load on the secondary of the flyback transformer. It also fixes the peak voltage across the switch by design, so that it can not go any higher even when the HV output is open circuit. In a TV the on-time is typically something like 52us and the half-sine shaped flyback pulse is produced in the 12us of off-time. Peak switch voltage on the primary side is usually somewhere in the region of 1200V for a 150V supply, but the turns ratio of the flyback transformer steps this up to maybe 20kV on the secondary.
I've never seen a good diagram of the waveforms of a TV's flyback (line output stage) on the net but discussions about this frequently come up here, ...so i've posted my own sketch here to go along with this thread:

-Richie,
Re: Problems with 555 Flyback Driver and Flyback Driver Discussion
Antonio, Sat Jul 05 2008, 01:48AM
The drawing is correct. The idea that a low-impedance load will make the primary current grow indefinitely, limited only by the current that the transistor can handle and resistances in the circuit, is correct too. So, if you want to make arcs, always put some significant resistance in series with the arc, or in series with the primary coil, or use a more powerful transistor at the input. A regular flyback transformer will not last much making arcs without current limitation. A regular transistor will not last much too if used without a snubber, or that diode and capacitor in parallel with it (better than a snubber, as they recycle unused energy).
In working with these 555 flyback drivers, always guarantee first that the oscillator is working before connecting the power supply to the transformer. Any element that is too hot to touch is really too hot, and if this happens something is wrong.
Re:
Problems with 555 Flyback Driver and Flyback Driver Discussion
Dr. SSTC, Sat Jul 05 2008, 07:04AM
Dr. Kilovolt wrote ...
I have this circuit on my pc and post it every time someone asks about 555 flyback driver

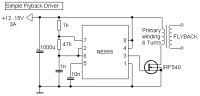
Some notes:
-the fet shoult be rated approx. 6-10 times the voltage of your PSU, but not more as it will have too high Rds(on)
-your 68ohm gate resistor is too big, you can remove it completely or use something like 10 ohms
-your FET has probably too high Rds. Something aroud 50-100mOhm max. should be okay (e.g. IRF540)
-it will get quite hot anyway, there is a "quasi-resonant" mod for this circuit which involves few extra components but makes the fet run often much cooler.
-these drivers work best at around 70V supply voltage (555 has its own supply) and 500V FETs (IRFP460)
i dont think you wanna take the pin 3 resister off go any lowe than 40ohms and your 555 is gone in a very short time use a bd139/bd140 gate driver combo
Re: Problems with 555 Flyback Driver and Flyback Driver Discussion
Steve Conner, Sat Jul 05 2008, 12:26PM
I agree with everything Marko and Richie said, flyback drivers are for kids :P
Although, I thought of one thing. Antonio once mentioned that the single transistor blocking oscillator circuit can have a form of peak current control, because the cycle can be ended by the transistor coming out of saturation, as well as by the core going into saturation. In the light of what was said here, I think this makes it a good candidate for a kiddie friendly flyback driver.
It also explains why it's used to charge camera flash capacitors, and why you hear the rising pitch whine as the capacitor charges. When the capacitor voltage is low, the circuit must run at a low duty cycle to give the core time to reset. The on-time is constant, so the off-time and hence the frequency varies with capacitor voltage.
Re: Problems with 555 Flyback Driver and Flyback Driver Discussion
flannelhead, Sat Jul 05 2008, 12:39PM
But still, there are many newbies around here, who don't like to start with several hundreds of watts, but like to start their experiments with lower powers.
There are generally two options for a low power flyback driver, the 2n3055 driver, and the 555 one. Some beginners choose the 555 circuit because they want to audiomodulate it later. Now you would ask, why not to use SG3525 or TL494 then. The answer is that they aren't available in some places.
Those were some points from the view of a beginner, which I still think I am.
Re:
Problems with 555 Flyback Driver and Flyback Driver Discussion
Marko, Sat Jul 05 2008, 04:30PM
But still, there are many newbies around here, who don't like to start with several hundreds of watts, but like to start their experiments with lower powers.
Well, nobody is preventing you from running Mazzilli or halfbridge circuit at much less than several hundred watts.
Hints: lower supply voltage, higher number of primary turns, reduction of duty cycle of PWM controllers.
I'm sure TL494 is nearly available anywhere NE555 is, and SG3525 very likely too. Look inside computer power supplies for TL494.
Nothing makes one topology ''more powerful'' than another, although there are those that do work and are widely used because of that, and those that don't! :P
Marko
Re:
Problems with 555 Flyback Driver and Flyback Driver Discussion
Antonio, Sat Jul 05 2008, 05:03PM
It's possible to include current limitation in a 555 driver. A transistor senses the drain current and lowers the duty clycle by draining current from the capacitor connected to pin 5. This is a simulation on the Switchercad III simulator. I didn't try it yet in practice, but the simulation works perfectly.
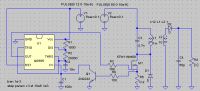
Update: I made a test. The circuit works correctly. I used an IRF630 mosfet and the regular input winding of a monitor flyback transformer, powered with 24 V. This produces 5 mm arcs, as the transistor clamps the voltage over it at 200 V. With an external winding, greater power could be obtained. 1 Ohm at the source limits the current at about 1 A. 0.5 Ohms at 2 A, and so on. The output can be safely short-circuited.
Re: Problems with 555 Flyback Driver and Flyback Driver Discussion
Firefox, Sun Jul 06 2008, 12:26AM
I'll give that a try, Antonio, since I already have the circuit built. Then I'll report back here.
Re:
Problems with 555 Flyback Driver and Flyback Driver Discussion
Dr. SSTC, Sun Jul 06 2008, 01:53AM
Dr. Conner wrote ...
I agree with everything Marko and Richie said, flyback drivers are for kids :P
Well you got to start somewhere
Re: Problems with 555 Flyback Driver and Flyback Driver Discussion
TheBoozer, Sun Jul 06 2008, 11:52AM
"Flyback drivers are for kids" reminds me of a TV commerial. Though I don't watch TV anymore because I took the flyback out and it doesn't work now. The little transformer has provided me with many more hours of entertainment than any amount of reruns could... :)
My last project was a flyback driven jacob's ladder. My recipe was an AtTiny26 with an HCNW3120 optoisolator. In the end I used voltage feedback to maintain a constant current supply to the flyback. It's a convenient microcontroller for the project I chose. The Uc has seven readily available ADC pins. One timer was used for PWM drive. Another timer was to modulate the output. Although the whisper silent jacob's ladder was pretty neat too...
Adding feedback boosted my performance, decreased component temperatures. No amount of fine tuning a manual squarewave (like a 555 output) worked for me. (I like the 555 circuit with feedback up there)
Here's a sample:
]inthetube.mpg[/file]
Re:
Problems with 555 Flyback Driver and Flyback Driver Discussion
quicksilver, Sun Jul 06 2008, 03:21PM
Dr. Conner wrote ...
,...flyback drivers are for kids :P.
And that's why they are so much fun

But I personally have never used a 555 driver in a flyback as (for the reasons Marko pointed out: it is not a "flexible enough switch") it didn't make sense within the component design. But using one in a automotive coil to draw arcs appears to make sense as it substitutes for the mechanical action that the coil was designed for. The Mazilli driver and related concepts have stood up to enormous abuse (with flyback arcs) from this Beginner.
When learning a new hobby I always attempt to chuck my ego and listen to logic; the switching element of the 555 simply doesn't appear warranted in the flyback-arc-drawing phenomenon. I once made a little switching circuit for another project and after blowing out a component the 3rd time, I KNEW that either I had been either sloppy, unprofessional & absent minded or the circuit was junk. I found (much to my chagrin) that the circuit was garbage. Just because it was posted on the internet didn't make it a worthwhile design.
I can understand my own blundering but when I chase a design that is error filled from the start: it's really annoying. That's why I am wary of first versions of software releases!

Re:
Problems with 555 Flyback Driver and Flyback Driver Discussion
Dr. Dark Current, Sun Jul 06 2008, 06:25PM
I'm sorry, I didn't take time to read the thread all the way.
Marko wrote ...
- Ignore Jan Martis, his site, and all the schematics of ''NE555 flyback drivers'', never build them. And I'm saying that solely because I'm evil. ( :D )
Marko, with the quasi-resonant driver I have gotten 200-300 watts of (real) input power with single or "double" (paralleled) IRFP250 switch. The output voltage from the transformer is respectable (I think I had it at 80kV+, arcs initiating at 13cm between two nails) and if you use the right resonant capacitor, the power is renturned to filter capacitor and power draw is low with output shorted!
Here is the quasi-resonant driver in action (ignore the voltages I think they are wrong)

(Sony Trinitron flyback, I had it do more later. Notice the small heatsink, gets just barely warm)

(first attempts, crappy DC transformer found in every other TV)
And here is a schematic that should work for most:
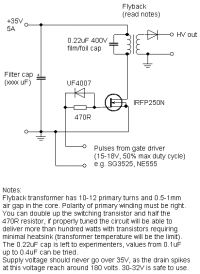
Read the notes. I had good experience with including secondary current feedback to maintain constant secondary current by limiting duty cycle, after this mod the circuit is nearly indestructible.
As the driver does not create such big negative spikes on secondary as half-bridge type drivers do, it can be obtained more output voltage from the transformer before the diodes break down.
Marko, I don't know all the theory like you do, but this topology has worked extremely well for me
in practice. This circuit is built
from experience and experimenting with various lash-ups. You can say what you want, it does and will work well for me.
-J.M.
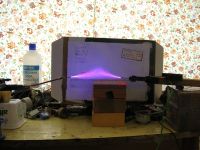
Re: Problems with 555 Flyback Driver and Flyback Driver Discussion
Firefox, Mon Jul 07 2008, 02:21AM
Thats pretty incredible Jan, I have a bunch of salvaged 200-400V 5-30A MOSFETs to try this out with. To the workbench!
Also, I'm going to expand the scope of this thread due to the incredible amount of info presented here, I believe this is a discussion that can be found piecemeal throughout the forums, but I've never seen so much information at one spot. I might even be motivated to compile it into HVWiki format for posterity.
Re:
Problems with 555 Flyback Driver and Flyback Driver Discussion
Marko, Tue Jul 08 2008, 09:09AM
Jan, I've been silently watching your work for a while and was always impressed. Quasi-resonant topology is still great advance from circuit shown in the first post, which is what we were specially referring to - it is spread all over internet and apparently most newcomers see it as something great, which I wanted to debunk.
I just want to end the endless cycling of the 'NE555 flyback driver' (not quasi resonant or with any sort of current control) around the internet which always ends with frustration for most people and is not fruitful.
Pulse-by pulse current limiting is great improvement to, and it is neither included in the circuit shown in the first post!
Jan, did you use current feedback when running at 300W? I would expect heavy loading and especially short circuit of the output to result in dead switches or very poor efficiency in all cases without some means of current control and preventing saturation.
And why did you use two paralleled switches? For efficiently working circuit and just 300W I would expect one IRFP250 to be just fine.
I have offered an explanation why might the circuit ''just work'' without current control, because of negative resistance of the arc ''balancing out'' Vs as output current drops, but saturation still needs to occur in order for that to happen, and high current surges would flow in the switches bo matter what is done.
Marko, I don't know all the theory like you do, but this topology has worked extremely well for me in practice. This circuit is built from experience and experimenting with various lash-ups. You can say what you want, it does and will work well for me.
Well, if theory and practice don't match, something is wrong wither with theory or experiment...
Most of this, more or less, comes from Richie's head anyway, but it did make sense to me (I may be though one of those who got greatly frustrated with 'ne555' circuit in past and lost objectivity :P )
Re:
Problems with 555 Flyback Driver and Flyback Driver Discussion
Dr. Dark Current, Tue Jul 08 2008, 10:21AM
Marko wrote ...
Jan, did you use current feedback when running at 300W? I would expect heavy loading and especially short circuit of the output to result in dead switches or very poor efficiency in all cases without some means of current control and preventing saturation.
Yes I used current feedback, but it will work fine without it if you don't mindlessly short circuit the output for long time. I think in the case of short-circuit, most of the leftover energy in the LC is returned back to the supply rails through the MOSFET body diode.
I used two parallel transistors just because I had them and I liked that the little heatsink got just lightly warm. Of course it will work with one with sensibly sized heatsink.
One problem I ran into with current feedback is the feedback oscillating in the audio range. I have no fix for that and I tried various filters in the fb path.
To the "bare" 555 driver, you are right the transistor will get very hot with more load on the secondary. Because of this, it is good for powering lifters etc. which require high voltage at low current, but for arcing fun it is no good.
Re: Problems with 555 Flyback Driver and Flyback Driver Discussion
Steve Conner, Tue Jul 08 2008, 12:30PM
Dr. Kilovolt did you use primary current feedback, or feedback of the HV secondary current? If the latter, you could have the dreaded right-half-plane zero.
If you take your feedback from the switch current, it should be easier to avoid instability. (just use Antonio's circuit, or a UC384x controller chip since these have peak current control with a built-in sense amp)
If you were taking it from the switch current already, then maybe there's a mistake in the circuit, or maybe it's an interaction between the internal capacitance of a DC flyback and the negative resistance of the arc.
Or, just leave it the way it is... squealing is annoying, but blown MOSFETs are even more annoying.
Re:
Problems with 555 Flyback Driver and Flyback Driver Discussion
Dr. Dark Current, Tue Jul 08 2008, 01:18PM
Dr. Conner wrote ...
Dr. Kilovolt did you use primary current feedback, or feedback of the HV secondary current? If the latter, you could have the dreaded right-half-plane zero.
I got it from the secondary ground return pin, after all I wanted to build a constant current-limited HV PSU. What do you mean by "right-half-plane zero"?
Re:
Problems with 555 Flyback Driver and Flyback Driver Discussion
Marko, Tue Jul 08 2008, 01:48PM
What do you mean by "right-half-plane zero"?
I think it's that bizarre and unexplained instability that happens in negative feedback control loops.
I was always troubled by it, and especially if using opto-couplers in feedback path.
As conner says, implementing current mode control would probably be just easier than messing with negative feedback.
And no IC's like UC3842's are needed (which is still considered 'exotic' by some people); CM control can be easily implemented by just few logic IC's rather easily, and actually getting us rid of all the unnecessary parts of that IC.
Re:
Problems with 555 Flyback Driver and Flyback Driver Discussion
Steve Conner, Tue Jul 08 2008, 02:03PM
The long answer:
In a flyback converter, the current goes to the load during the periods when the switch is off. So the immediate effect of an increase in duty cycle (assuming continuous mode) is a *decrease* in average output current, until the increase in duty cycle has made the inductor current ramp up. This initial setting off in the wrong direction destabilizes the control loop. And, an unstable control loop has a zero in the right half of the s-plane when you model the closed-loop dynamics with Laplace transforms: hence the name. See e.g.

and the articles that it references. Any unstable system has a RHP zero, but when we're talking about boost and flyback converters, we specifically mean the instability caused by the effect described above.
The short answer: Mix the switch current into your feedback loop. In order not to spoil the DC accuracy, put it through a high-pass filter so you use only the AC component.
Shorter answer: Slug hell out of it using an integrator with a long time constant, and it might sort of work.
Re:
Problems with 555 Flyback Driver and Flyback Driver Discussion
Marko, Tue Jul 08 2008, 02:26PM
In a flyback converter, the current goes to the load during the periods when the switch is off. So the immediate effect of an increase in duty cycle (assuming continuous mode) is a *decrease* in average output current, until the increase in duty cycle has made the inductor current ramp up. This initial setting off in the wrong direction destabilizes the control loop.
OK, to get it straight, *why would secondary current ever drop with increase of primary current?* I guess that's the major basic thing I have been missing all the time.
In any case, is this instantaneous drop in current the source of the mysterious 180 degree phase shift, which leads to oscillation?
Does something similar happen with voltage feedback with forward converters?
The short answer: Mix the switch current into your feedback loop. In order not to spoil the DC accuracy, put it through a high-pass filter so you use only the AC component.
How exactly is this 'mixing' done? , you mean current mode control (in which case he doesn't need output current feedback at all), or something else?
Shorter answer: Slug hell out of it using an integrator with a long time constant, and it might sort of work.
I think we would all greatly appreciate if you could explain us how to implement an integrator in the feedback loop, and what does it do.
Re: Problems with 555 Flyback Driver and Flyback Driver Discussion
Steve Conner, Tue Jul 08 2008, 02:49PM
Detailed answers to all of these questions would be outside the scope of this thread. They're meant as brain teasers for Jan or anyone else wanting to experiment with negative feedback in their HV projects. (Yes, even Google can't replace the need for thinking.)
I'll just say that when a flyback converter operates in continuous mode (and I'd be very surprised if these high-powered drivers didn't) there is a steady "flow" of DC amp-turns with a small AC ripple, just the same as in the output filter choke of a buck converter.
I say amp-turns, not current, because we all know that in the flyback circuit the current in any given winding is discontinuous. But overall, though the current commutates between the primary and secondary windings in proportion to their turns ratio, it is a constant current and the magnetizing inductance of the transformer smooths it and resists changes in it.
So, when the duty cycle is increased, this current takes a while to catch up, and until it does, the mean output current decreases, and a control loop sensing average output current would see a destabilizing error signal of the wrong polarity.
That's all I'm prepared to say, at the risk of dragging us off-topic. As for the integrator thing: The compensation capacitor on a TL494, SG3525, UC384x, whatever, makes the on-chip error amp function as an integrator in the feedback loop. You often see a resistor in series with the capacitor, this is because the power supply designer decided that a plain integrator wasn't good enough.
Re: Problems with 555 Flyback Driver and Flyback Driver Discussion
GeordieBoy, Tue Jul 08 2008, 05:50PM
Marko: Current flows on the output side of a flyback converter when the primary side switch is OFF. Therefore increasing the duty ratio of the primary side switch initially leaves LESS time remaining for current to flow on the secondary side. Hence the AVERAGE secondary side current falls initially when the duty ratio is increased. As Mr Conner said, it starts out going in the wrong direction for some time before it turns round and starts increasing instead.
When negative feedback is used the "starting out in the wrong direction" effectively turns negative feedback around the control loop into positive feedback around the control loop and the whole system oscillates.
Some advice: Most flyback supplies will transition into the continuous mode with output s/c because there is no output voltage being developed across the sec winding other than the diode drop to remove energy from the transformer. Cycle-skipping is the way to combat this, and is the way that most flyback converters stop their output current integrating up out of control.
EDIT: In general up to about 40 watts is reasonable for discontinuous current mode flyback, then you want to be operating in continuous mode above that power. At about 80 watts you would want to be into heavy continuous mode and above that power level the flyback is no longer the topology of choice.
Re Instability of Forward derived converters with feedback: Forward converters like buck, half-bridge, full-bridge etc don't have a right-half-plane zero in the open loop transfer function because they transfer power to the output when the primary switch is ON. It is only the boost and flyback operating in continuous current mode that exhibit the moving RHP zero in the open-loop transfer function. There are however many ways to wrongly compensate a forward derived converter that can make it go unstable without the RHP zero problem. If you're interested in this stuff I highly recommend the papers by Lloyd Dixon on SMPSU control theory that I have mentioned previously.
-Richie, <---- who also doesn't want to get into a control theory lecture situation. :)
Re:
Problems with 555 Flyback Driver and Flyback Driver Discussion
Chris Cristini, Wed Nov 12 2008, 04:51AM
i agree with Dr.SSTC i don't think you wanna take the pin 3 resister off go any lowe than 40ohms and your 555 is gone in a very short time use a bd139/bd140 gate driver combo
i never burned the mosfet i only fried 555 timers because i never used a gate resistor until a few weeks ago when i learned a little more about mosfets

Re: Problems with 555 Flyback Driver and Flyback Driver Discussion
JamesH, Wed Nov 12 2008, 05:05PM
I have built most flyback drivers on the web and got all of them to work
Excluding Dr Killovolts one - I will try it in the next couple of days
The most reliable is the one with one 2n3055 and the true flyback mode (2) windings
The Mazilla circuit with the two IRF250 - a ZVS - circuit works very well but as you have found the fet blow easily.
I have a demonstration on YOU TUBE - sparkfishes of how to use a Compact fluorescent Lamp _ Energy Saving Lamp to drive a flly back transformer using the original pins
I hoped to have a display of the different types of Flyback Transformers and the various drivers for the Cambridge Teslathon but could not get there.
I will display the drivers/ flyback transformers etc soon on YOU TUBE
Big sparks can be obtained from Car Ignition coils also - if you can get hold of the old round ones
Re:
Problems with 555 Flyback Driver and Flyback Driver Discussion
Dr. Dark Current, Wed Nov 12 2008, 06:30PM
crazy4 wrote ...
i never burned the mosfet i only fried 555 timers because i never used a gate resistor until a few weeks ago when i learned a little more about mosfets
The resistor probably reduces spiking of the supply voltage so the 555 survives better. It seems to me that you have bad filtering for the 555. Do you use a voltage regulator with film (0.1uF) and electrolytic (~10uF) caps on both input and output? If not, try it.
The 555 should run fine down to ~5 ohms gate resistor, but I have never blown one with no resistor at all. You only need to filter and decouple the supply voltage well.
Re: Problems with 555 Flyback Driver and Flyback Driver Discussion
Chris Cristini, Wed Nov 12 2008, 09:13PM
I use the 5v on a computer psu
Re:
Problems with 555 Flyback Driver and Flyback Driver Discussion
Dr. Dark Current, Wed Nov 12 2008, 10:18PM
crazy4 wrote ...
I use the 5v on a computer psu
5V to the 555?? This is not enough to turn on a MOSFET (are you driving it?), at least 12V should be used.
However, if you use a bipolar transistor, then the thing about the gate resistor is true, you need to use one, and it is better to use lower voltage for the 555...