Triangular Truss.
Patrick, Sun Sept 25 2016, 10:48PM
Iv been looking into controlling not just mass and strength, but now the cost of various drone features.
It seems Mechanical and Civil engineers have been using the truss and "I" beam ideas for quite awhile and they're well understood. I dont understand the statics and calculus, nor do i have a program to visualize working or failing conditions. But the triangular truss really caught my attention.
4 parallel rods seemed unnecessary, 2 doesn't work, so 3 seemed to fit the bill.
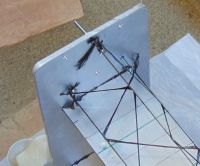
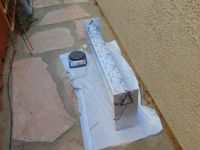
As you can see I used a I-beam with two end plates of aluminum. All the strands are carbon fiber of 6k. Eventually Ill move to 12k on the parallels and keep the 6k's on the shear diagonals. The triangle is 3" on each side, and the screws at both ends tension the parallels. I m trying to arrange the forces to follow the fibers, which generally can only be approximated with like homogeneous materials like metals.
Carbon "tow" as its called is cheap per foot, especially compared to carbon fabric, and its quantity of epoxy needed for fabric.
Re:
Triangular Truss.
Dr. Slack, Sat Oct 08 2016, 06:12AM
To avoid the need for resistance to bending, it's important to structure the truss properly.
A compression member will fail by buckling, see wikipedia page on that term. Basically a thick column is safe, a slender column could fail. In order to support the column from buckling failure, it is supported sideways every so often by cross connection to other members, the trianglular truss.
Your illustration shows an incomplete bracing. Each long element is supported in only one lateral direction. This means that the long element relies on its stiffness for stability in the other direction. Unequal stiffness requirements like this is not efficient.
Interestingly, if you look at stock photos of lattice pylons, they have a similar incomplete bracing structure, like this one. However, the long element is an iron angle, which has inherent stiffness, and fails by twisting. Incomplete bracing *is* sufficient to brace against twisting failure.
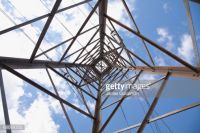
To fully brace a triangular truss, which can then have length elements without stiffness against bending, you need to have 6 elements meeting at a point. This restrains the sideways movement of the brace point in two directions. Unfortunately this does not result in an aesthetically pleasing fully symmetrical structure, as the cross braces need to be at different angles, like this.
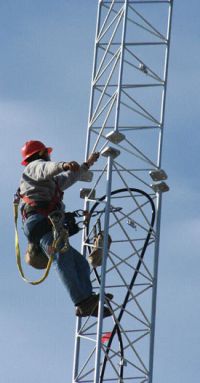
They don't have to be normal and diagonal, as above, which is quite easy to set out and manufacture with bar and welding, and gives important level steps for climbing. To my mind, a more pleasing pattern, and easier to make with tow, would be bracing consisting of a red clockwise spiral with pitch 1, and then a two-start pair of anti-clockwise spirals of pitch 2 in green. You would find it easier to make as well than what you've illustrated, each tow is simply wound round the outside in a single direction, rather than threaded back and forth. Like this ...
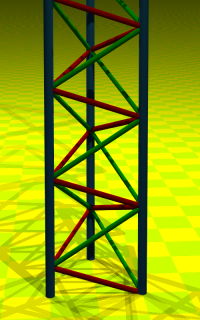