Green-Sand Casting a U-block
klugesmith, Tue Apr 09 2013, 03:47AM
Recently I got out my molding sand and paraphernalia for the first time in many years. People who have done foundry work know it's about patternmaking and moldmaking, as much as about melting metal. (Don't say smelting unless you are chemically reducing ore.)
I wanted to hold a stubby cylinder of titanium very solidly in a milling machine vise, and had no suitable V-block. Instead of machining a V-block from Al or steel, I decided to cast one. Opted for a U-block with the same radius as the workpiece, for no good technical reason.
Made two separate patterns from wood and Bondo. The Ti cylinder is wrapped in box-closing tape as a mold release, over a layer of duct tape to increase the radius. Patterns and molds are generally oversize to compensate for casting shrinkage.
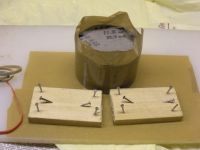
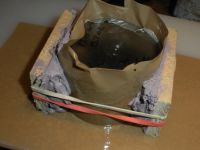

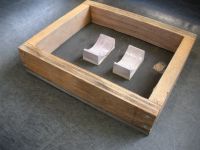
"Green" molding sand looks like dirt, but is intentionally more porous to vapors. A strong bond requires the right amount of water (or oil), which experienced molders can judge by squeezing a ball of sand. Here I added 250.0 ml of water to 1/3 bucket full of dry sand.
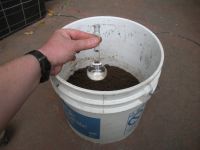
The moldmaking process is well described in many books and online references.
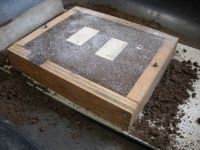
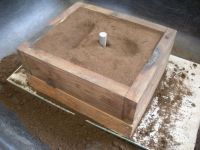
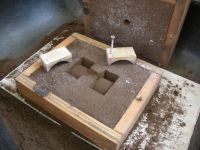
This was the first practical job for my little electric heat-treating kiln. I opted to melt lead instead of zinc pot metal. Later worried that I would end up with a bearing instead of a workholder.
Having no iron pot that would fit in the kiln, I used a two-piece steel soup can with a crudely formed pouring spout. Handled with pliers. Skimmed and poured at indicated temperature of about 800 degrees F.
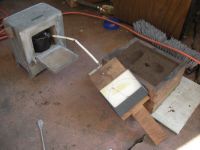
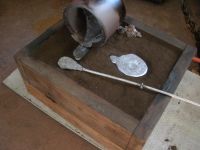
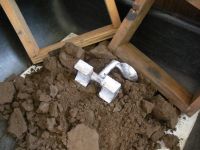
It works!
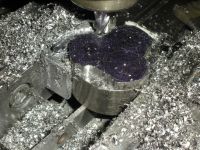