Grooved Bobbins For Segmented Windings
jpsmith123, Sat Jul 17 2010, 06:47AM
I finally got my new Micro100 carbide grooving tool (and it seems to work very well), so I'm about ready to start experimenting with "pie" type windings.
The issue I'm struggling with is: What's the best way to run the wire connecting the sequential "pies" together; i.e., to get from the top of the most recently wound coil, to the bottom layer of the next groove)?
I seem to recall a lengthy discussion here about the subject, but I can't find that thread.
Was there any consensus on what's the best mechanical method to do it, e.g., by cutting an angled "slit" in the "lands"
between grooves?
Re: Grooved Bobbins For Segmented Windings
Proud Mary, Sat Jul 17 2010, 08:42AM
I've just looked at three 1930s RF chokes for you. Two had 45 deg slots cut in the partitions, and one had partitions like cog teeth to reduce the amount of ebonite dielectric between windings, so no special channel had to be cut to lead the wire into the next winding space.
Later RF transmitter chokes used self-supporting wave windings with air 'partitions' between windings, to keep the inter-winding capacitance as low as possible.
Re: Grooved Bobbins For Segmented Windings
RickR, Sat Jul 17 2010, 05:01PM
Which grooving tool did you purchase? I took a look at the Micro100 catalog and am wondering about what type of machine the grooving tools are supposed to be mounted in. Would you elaborate on the tool and the type of material you're planning to cut the grooves in?
I've used a table saw to cut circular grooves in UHMW tubes to create pies, but would be interested in anything that's safer.
When I did the winding, I wound on every other pie. I cut notches in the pies so I could run wire from the top of one winding, through a notch, along the unwound path, through the next notch to the bottom of the next winding. It's a potential waste of space, but it was very effective in isolating the windings. One of the reasons I'm asking about the tool is that I would like a way to minimize the width of the routing channels as opposed to the width of the winding channels.
Thanks,
Rick
Re: Grooved Bobbins For Segmented Windings
jpsmith123, Sat Jul 17 2010, 05:55PM
@RickR:
What I got from Micro100 is a brazed, micrograin carbide, lathe toolbit, part #GS-122002. (I just have a crappy - and I mean crappy - little Micromark 7x14 mini-lathe).
The bits come in different sizes. The one I got cuts a 1/8" wide radial groove (actually 0.122 inches) and it has a 3/8" square shank. It cuts cpvc really well...no grabbing, no melting, no nuthin'...just an easy, precise, nice looking cut.
I wonder what's the best way to cut an angled slit in the "lands" (the partition betweer the winding grooves)? I'm trying to think of how to do it in a precise way, and I'm having trouble.
@Proud Mary:
I'm having trouble trying to visualize the "cog tooth" scheme you're describing.
Re:
Grooved Bobbins For Segmented Windings
Proud Mary, Sat Jul 17 2010, 06:57PM
jpsmith123 wrote ...
@Proud Mary:
I'm having trouble trying to visualize the "cog tooth" scheme you're describing.
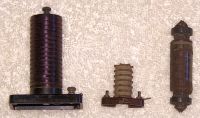
How's that?

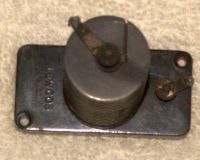
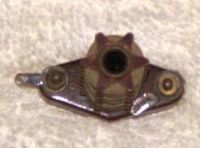
Re: Grooved Bobbins For Segmented Windings
jpsmith123, Sat Jul 17 2010, 08:03PM
Wow look at those things! Thanks...but you didn't need to rob a museum just for my sake...
Anyway, all kidding aside, I see the things you're talking about, and I can see how that design would reduce the capacitive coupling between sections somewhat, however, it isn't clear to me how you can "insulate" the wire to prevent dielectric breakdown as the wire goes from the top of one section to the bottom of the next.
Re:
Grooved Bobbins For Segmented Windings
Proud Mary, Sat Jul 17 2010, 08:44PM
jpsmith123 wrote ...
Anyway, all kidding aside, I see the things you're talking about, and I can see how that design would reduce the capacitive coupling between sections somewhat, however, it isn't clear to me how you can "insulate" the wire to prevent dielectric breakdown as the wire goes from the top of one section to the bottom of the next.
How do you imagine the potential difference would be distributed down the length of the choke?
Re: Grooved Bobbins For Segmented Windings
jpsmith123, Sun Jul 18 2010, 04:59AM
Well the item at issue is a proposed HV secondary, producing approximately 10 kv peak, with 8 sections, so the potential difference across each section, bottom layer to top layer, will be approximately 1250 volts.
The object is to get the winding wire from the top layer of section N to the bottom layer of section N+1, while staying comfortably away from the other layers, and interposing some insulating material therebetween.
Maybe I'm misunderstanding something, but it's not clear to me how a cog tooth partition between adjacent sections can solve this problem.
Re: Grooved Bobbins For Segmented Windings
Proud Mary, Sun Jul 18 2010, 07:29AM
What does the data sheet for your wire say is the RMS insulation breakdown voltage?
Re: Grooved Bobbins For Segmented Windings
jpsmith123, Mon Jul 19 2010, 06:18AM
One problem is that I don't have a data sheet for this 26 gauge magnet wire I'd like to use, so I'm not sure what its breakdown voltage is.
Of course I searched the internet to get an idea of the range of breakdown voltages available in commercial magnet wire, and IIRC, the lowest rated wire I found was specified as "> 1 KV". (I was surprised to see that some magnet wire was rated at 5 KV, and I think there was some rated even higher).
In any case, to be prudent, I'm assuming my magnet wire is rated at 1 KV. Using this number, I can see that I need to be somewhat careful, but I don't need to get carried away.
Re:
Grooved Bobbins For Segmented Windings
Proud Mary, Mon Jul 19 2010, 08:37AM
jpsmith123 wrote ...
One problem is that I don't have a data sheet for this 26 gauge magnet wire I'd like to use, so I'm not sure what its breakdown voltage is.
Of course I searched the internet to get an idea of the range of breakdown voltages available in commercial magnet wire, and IIRC, the lowest rated wire I found was specified as "> 1 KV". (I was surprised to see that some magnet wire was rated at 5 KV, and I think there was some rated even higher).
In any case, to be prudent, I'm assuming my magnet wire is rated at 1 KV. Using this number, I can see that I need to be somewhat careful, but I don't need to get carried away.
If your winding is neat, there's no reason why the PD between any adjacent, subjacent, or overjacent
* turns should exceed the breakdown voltage is there?
A winding style sometimes used at high voltage has a triangular cross section, with each layer having less turns than the one beneath it. This maximizes the slant height distance between the highest voltage turns at the top, and the lower voltage turns at the bottom - it also prevents a higher voltage turn slipping down the side onto the next layer.
* Subjacent is a word usually only found in house conveyancing contracts to mean the flat/apartment below, and I invented 'overjacent' for want of an existing word! 
Re: Grooved Bobbins For Segmented Windings
Matt Edwards, Wed Jul 21 2010, 04:51AM
That is awesome. I was winding a secondary for a TC the other day and a buddy of mine suggested doing something like that for the primary coil. I thought it would look nice.
Re:
Grooved Bobbins For Segmented Windings
jpsmith123, Fri Aug 13 2010, 11:08PM
I finally got a grooved bobbin made...except for the slits (or whatever) to feed the wire from section to section.
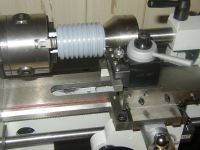
One thing I decided to do was to have the ID of the bobbin a little bigger than the core, so as to have room for a few layers of polystyrene or polyethylene film, and some copper foil (for a shield). This should prevent corona around the core and lower the dielectric loss in the cpvc a little bit.
As far as the "slits" are concerned, I don't have a milling machine, but I do have a drill press with a cross-slide vise attached, so I'm thinking I'll try to mill small angled slits between sections using this arrangement, with a small (1/32") end mill in the drill chuck.
If this method of making a HV secondary ultimately doesn't work out, e.g., if I ruin it trying to put the slits in it, or by way of any other operation, I think the fallback method is to use the teflon wire with the straight bobbin, but to divide it up into 4 or 5 sections in series, using large cpvc washers as seperators.
Re: Grooved Bobbins For Segmented Windings
Andyman, Sat Aug 14 2010, 12:20AM
Have you considered using a slotting saw on a dremel? Those are pretty darn thin. Or even a razor blade, and carve a slot
Re: Grooved Bobbins For Segmented Windings
jpsmith123, Sat Aug 14 2010, 06:13PM
Hello Andyman,
I've tried cutting cpvc with a razor knife, and unfortunately, I found it to be very difficult if not impossible.
The slotting saw idea is a possibility, but I don't have a dremel tool.
For $20 or so, it's probably worth getting one, as I'm sure I'd have other uses for it, but for this application, I wonder: How easy are they are to control?
I may ultimately be forced to try something like this, but I hate to take something I spent a few hours working on, making it all precise and everything, and then go to work on it free-hand, with a cutting tool...I can see myself slipping with it or or misjudging something and ruining the bobbin.
Re:
Grooved Bobbins For Segmented Windings
Martin King, Sat Aug 14 2010, 07:27PM
jpsmith123 wrote ...
I wonder: How easy are they are to control?
Clamp the workpiece in a vice, for a plastic bobbin I would get two scrap pieces of plastic or wood and drill holes the same diameter as each end of the bobbin and use them to hold the bobbin in the vice jaws otherwise you risk damage to the bobbin. Hold the Dremel VERY firmly even bracing your arms against your body. Particularly with a razor saw blade cutting plastic the blade can grab leading to disaster for the workpiece or scars on your fingers (BTDTGTS). Make the cut a little bit at a time, removing the blade and allowing the plastic/blade to cool between each go. If you can, then protect nearby vulnerable parts of the workpiece with some scrap material, cut up bits of a steel can be bent to form shields. Practice on some scrap first if it's a valuable workpiece. Don't let this scare you off using a Dremel, they are very useful tools and I use them a lot, they just need a lot of care and respect!
Martin.
Re:
Grooved Bobbins For Segmented Windings
IntraWinding, Sun Aug 15 2010, 11:23AM
A model makers photo etched saw blade would make a nice thin cut if it can cope with the plastic you're using. A quick search found this example

To get a slip free repeatable cut, build a little jig with a blade guide.
Re: Grooved Bobbins For Segmented Windings
jpsmith123, Mon Aug 16 2010, 08:39PM
Well, so much for the end mill idea.
After much thought, I devised what I thought was an ingenious method to hold the bobbin and steer it into the rotating end mill, but it was all for naught, as despite great care and a light touch, I nevertheless managed to break both of the end mills that I had.
Now it looks like it's either a saw blade on a rotary tool, or back to the drawing board.
Re:
Grooved Bobbins For Segmented Windings
jpsmith123, Sat Sept 18 2010, 04:50PM
Here's the latest (and hopefully final) version:
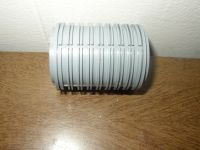
I cut smaller grooves in the "lands" between winding spaces, and then I put it in a cross-slide vise mounted on a drill press and milled slots with a 1/16" end mill. The whole arrangement is cheap and sloppy, and the work came out kind of sloppy, accordingly, but I guess I have to live with it.
Next thing is to try and wind it.
One potential issue I see already is the possibility of losing some space on the bottom layer, due to the finite bend radius of the wire. IOW, when the wire emerges from a narrow groove (through the vertical slot) and into the adjacent winding space, it has to turn a corner. This will probably cause the loss of a turn or two on the bottom layer of each segment...but I should be able to put a few extra turns in the narrow grooves to make up for it.
Re:
Grooved Bobbins For Segmented Windings
Proud Mary, Sat Sept 18 2010, 06:01PM
jpsmith123 wrote ...
Here's the latest (and hopefully final) version:
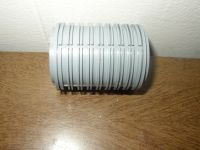
I cut smaller grooves in the "lands" between winding spaces, and then I put it in a cross-slide vise mounted on a drill press and milled slots with a 1/16" end mill. The whole arrangement is cheap and sloppy, and the work came out kind of sloppy, accordingly, but I guess I have to live with it.
Next thing is to try and wind it.
One potential issue I see already is the possibility of losing some space on the bottom layer, due to the finite bend radius of the wire. IOW, when the wire emerges from a narrow groove (through the vertical slot) and into the adjacent winding space, it has to turn a corner. This will probably cause the loss of a turn or two on the bottom layer of each segment...but I should be able to put a few extra turns in the narrow grooves to make up for it.
That's great progress!

I've always found that just dividing the available space by the wire diameter never works out in practice with my casual way of going about things, so I always leave a contingency margin to allow for 'winding creep' or whatever we choose to call it.
Re: Grooved Bobbins For Segmented Windings
jpsmith123, Tue Sept 28 2010, 02:44AM
Proud Mary you're right about having some extra winding room.
I at first decided to go with 28 gauge wire, but when I started winding it, I realized that I just wasn't getting as many turns as I thought I could.
So I had to abandon it and decide to either do some more machining on the plastic or use smaller wire...so I switched to 30 gauge wire. I didn't want to give up copper, but the thought of more cutting scared me.
Anyway, right now it's about half way done, and I also found out that lots of tension on the wire (and constant tension) is an absolute must. So far it's going pretty good but not quite as neat as I had hoped.
If I can successfully complete it (and that's a big if) I'll post a picture here.
Re:
Grooved Bobbins For Segmented Windings
jpsmith123, Mon Oct 04 2010, 09:10PM
Ok I finally got one coil wound.
Many of the segments turned out to be "semi random wound", meaning they're not as nice and neat as I had hoped for, but I think it'll work ok.
The ends of the winding are secured with a drop of "krazy glue".
I'm still debating whether or not I should try to pot the coil...theoretically I shouldn't have to but I might just pot it anyway for the sake of the experience.
Maybe tomorrow I'll try to do some quick electrical tests and if so post the results.
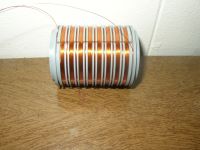
Re:
Grooved Bobbins For Segmented Windings
Patrick, Mon Oct 04 2010, 10:05PM
jpsmith123 wrote ...
I at first decided to go with 28 gauge wire, but when I started winding it, I realized that I just wasn't getting as many turns as I thought I could.
hey im doing exactly the same thing with a PE bobbin and 35Ga wire. i worrry about the same problem of calculated wire turns and actual wire turns per channel. related to your above quote, can you give us an estimate on what you were getting... like 60%, 70% actual turns over theoretical, and such? and i geuss your semi-random wind is the best most of us will be able to do, so just an approximation would do.
that work youve done so far is excellent, mine will be under oil, as solid potting prevents changes/fixes.
Re: Grooved Bobbins For Segmented Windings
Proud Mary, Mon Oct 04 2010, 10:28PM
At the risk of stating the obvious, if you have calculated your windings on the basis of copper wire tables, ensure that the figures refer to the wire plus enamel (or whatever) coating.
Unless you are completely certain of your wire's insulated diameter, measure it at a number of points with a micrometer, and use the average figure in calculation, PLUS a contingency margin as I suggested above.
And now you know what sort of problem it is, the easiest approach in future is to do a trial winding over a mandrel, and count the number of turns per cm actually achieved in practice.
Re:
Grooved Bobbins For Segmented Windings
Patrick, Mon Oct 04 2010, 11:12PM
Proud Mary wrote ...
At the risk of stating the obvious, if you have calculated your windings on the basis of copper wire tables, ensure that the figures refer to the wire plus enamel (or whatever) coating.
Unless you are completely certain of your wire's insulated diameter, measure it at a number of points with a micrometer, and use the average figure in calculation, PLUS a contingency margin as I suggested above.
And now you know what sort of problem it is, the easiest approach in future is to do a trial winding over a mandrel, and count the number of turns per cm actually achieved in practice.
yes i account for wire diamater and id just like to have a comparison to someone elses work for a sanity check.
i use a program from wiretron.com, for
bare copper 35ga i get:
0.0055" min
0.0056" nom
0.0057" max
with
heavy (double) insulation:
i get min build of 0.0009"
therefore:
0.0064" min
0.0067" nom
0.0070" max
the wiretron.com download is free too.
i dont think the 1/10,000" accuracy matters much, so i just use te 0.0067" nominal value for winding calcs.
Re: Grooved Bobbins For Segmented Windings
jpsmith123, Mon Oct 04 2010, 11:17PM
I didn't have a micrometer, but I had a digital caliper which I used.
For my calculations, I added 10% to the wire diameter.
I should say I believe that my failure to get enough turns with the 28 gauge wire was primarily because of my inability to wind the coil as neatly as I would have liked.
And part of the neatness problem was due to some momentary lapses of tension (on the wire) while winding.
@Patrick: What kind of coil are you winding, a single layer coil?
Re:
Grooved Bobbins For Segmented Windings
Patrick, Mon Oct 04 2010, 11:53PM
jpsmith123 wrote ...
For my calculations, I added 10% to the wire diameter.
yes, i add 10% too.
jpsmith123 wrote ...
I should say I believe that my failure to get enough turns with the 28 gauge wire was primarily because of my inability to wind the coil as neatly as I would have liked.
yes, i have this problem too.
jpsmith123 wrote ...
And part of the neatness problem was due to some momentary lapses of tension (on the wire) while winding.
ok, maybe a jig is needed, going to have to build one.
jpsmith123 wrote ...
@Patrick: What kind of coil are you winding, a single layer coil?
the same as yours, a pie-channel type, but instead of turning on a lathe im using overhead projection sheets to make the "grooves" so i gain space for the wire top to bottom change over groove; then yours with your small groove and wide walls your loosing alot of winding space, but youve realized this fact in your above posts.
Re: Grooved Bobbins For Segmented Windings
jpsmith123, Tue Oct 05 2010, 12:39AM
Patrick I'm a little bit confused as to exactly how you're doing it.
As I understand it, you're using a polyethylene tube, and sheets for an overhead projector, but I'm not sure exactly what you're doing with the sheets. Are you cutting the sheets into narrow strips and winding them on the PE tube to make "dividers" somehow?
You don't have a picture of it or anything, do you?
(BTW, I also thought of another possibility: back to the teflon coated wire idea, but winding it in, say, 4 sections. That approach might work, but it would be a real PITA to have to make the large CPVC washers, i.e., dividers, from flat stock).
Re: Grooved Bobbins For Segmented Windings
Patrick, Tue Oct 05 2010, 12:56AM
The PE is a temporary form.
Im looking for pics on my Hard drive now. i think i left the original protoype at my parents place. maybe i have an autocad rendering i can post.
anyway, no i dont cut them into strips. i cut templates and stack them like washers on a bolt shaft. the templates are printed by laser printer (cut with razor blades so theres no toner on the final pieces.) Then stacked, wound, stacked... and so on with the sheets 0.0045" thick.
ive had problem getting the channels and winding staying uniform.
Re: Grooved Bobbins For Segmented Windings
jpsmith123, Tue Oct 05 2010, 01:49AM
Hmmm I guess it's just one of those things that I'll have to see a picture of, before I understand it.
Anyway, I just started winding the second coil, and it's amazing how much better (and faster) it's going, based simply on the experience gained from the first one.
I almost feel like making a few extra ones, so I can pick out the best.
Re:
Grooved Bobbins For Segmented Windings
Patrick, Tue Oct 05 2010, 02:26AM
jpsmith123 wrote ...
Anyway, I just started winding the second coil, and it's amazing how much better (and faster) it's going, based simply on the experience gained from the first one.
well thats good.
ill render some cad stuff and post it here.
Re: Grooved Bobbins For Segmented Windings
jpsmith123, Tue Oct 12 2010, 01:48AM
Well my second coil came out good except for one section. I was talking to someone while doing it, and I got distracted and put too many turns in that section. It should still work, it just doesn't look right - and I'm irritated with myself for doing that.
Anyway, the next step is to pot the two coils - as soon as I decide what kind of potting material to use.
I'm wondering, are you any further along with your efforts, Patrick? I'm anxious to see exactly what your scheme is.
Re: Grooved Bobbins For Segmented Windings
Patrick, Tue Oct 12 2010, 05:25AM
I'll post some stuff soon....
also, for your potting... i like vacuum - oil, or vacuum - polyester epoxy.
100 microns of vacuum, works well.
Re: Grooved Bobbins For Segmented Windings
Niraj Joshi, Thu Oct 14 2010, 05:36PM
good work guys!!!
Re: Grooved Bobbins For Segmented Windings
jpsmith123, Fri Dec 03 2010, 06:17AM
I kept thinking about the 30 gauge wire I used, instead of the 28 gauge wire I wanted to use, and it bothered me, so I made two more coil formers (yes, I know I'm crazy).
Anyway I made the grooves about 0.015" deeper, and that added enough room to get 425 turns of 28 gauge.
I just ordered some epoxy from MG Chemicals to pot it with.
The only issue right now is, I'm trying to figure out what's the best way to secure the loose end of the wire; I need to keep it secured somehow until it's potted and the epoxy cures.
I'm thinking about using a drop of crazy glue, but I'm not sure if the epoxy might weaken or dissolve the crazy glue before it cures. After all the work I've put into this so, far I'd hate for a little detail to go wrong and ruin things.
Re:
Grooved Bobbins For Segmented Windings
Patrick, Fri Dec 03 2010, 07:43AM
jpsmith123 wrote ...
I'm thinking about using a drop of crazy glue, but I'm not sure if the epoxy might weaken or dissolve the crazy glue before it cures. After all the work I've put into this so, far I'd hate for a little detail to go wrong and ruin things.
use the same epoxy your going to pot with, or use any other common epoxy after it cures, epoxies are generally compatable with each other. And i bet you wont have dissolving problems with super glue. cyano's are pretty stable and compatable with common epoxies. you dont need to worry so much about the chemistry.
Re:
Grooved Bobbins For Segmented Windings
Ash Small, Fri Dec 03 2010, 09:54AM
Proud Mary wrote ...
.If your winding is neat, there's no reason why the PD between any adjacent, subjacent, or overjacent
* turns should exceed the breakdown voltage is there?
A winding style sometimes used at high voltage has a triangular cross section, with each layer having less turns than the one beneath it. This maximizes the slant height distance between the highest voltage turns at the top, and the lower voltage turns at the bottom - it also prevents a higher voltage turn slipping down the side onto the next layer.
* Subjacent is a word usually only found in house conveyancing contracts to mean the flat/apartment below, and I invented 'overjacent' for want of an existing word! 
The word you were looking for is 'superjacent'. (subjacent winding, adjacent winding, superjacent winding)
Re: Grooved Bobbins For Segmented Windings
jpsmith123, Tue Dec 07 2010, 01:10AM
Patrick IIRC you were going to just put your transformer in oil.
Can I ask, how are you going to secure the end of the coil so it doesn't become loose and unwind, and also, what kind of oil are you going to use?
Re:
Grooved Bobbins For Segmented Windings
Patrick, Tue Dec 07 2010, 02:08AM
Yes, i wont pot my transformers, because i know i want to change the secondaries out, my pirmaries and secondaries are removeable/fixable. i will use either 100% vegatable oil from safeway, or i will use non-detergent 40 wheight motor oil, but remember 2 things:
-- I have 2.6 gallons of dielectric circulating into and out of a 3kW system, cost prohibits olive oil.
-- corn oil hardens (rock hard) PVC and vinyl aquarium tubing and i hope vegatable oil/motor wont,
if i had a small container, like a pint/quart or less and a transformer, I would use
extra light virgin olive oil.see my reasoning for olive oil here:

for wire handling:
-- i use a single hole in the plastic bobbin, loop the magnet wire through, tie it off, presto.
-- or i use crazy glue/epoxy. (i use the crazy glue with the brush in the bottle, so i can put a droplet down.)
then run a stranded wire or threaded stud nearby.
Re:
Grooved Bobbins For Segmented Windings
jpsmith123, Wed Dec 22 2010, 04:23AM
Patrick here is a paper you might find interesting which compares some properties of various vegetabe oils for purposes of service as an electrical insulating liquid.

I'm thinking more and more about abandoning the potting idea and just dunking everything in yellow olive oil or rapeseed oil.
The transformer is not the problem, but the multiplier seems like it could be problematic (with potting, that is).
For just putzing around making sparks, with low to medium power and/or with low duty cycle use, I think you don't have to worry too much about thermal issues of the diodes and capacitors in the multiplier. But for medium to high power applications and/or where the power supply might be running for a little while, I can see things getting too hot.
I can see the typical 2CL2FM HV diodes dissipating a few watts each, and the ceramic capacitors dissipating a few watts each (I'm trying to get more info on the DF of the cheap ebay ceramic capacitors to get a better idea), but I think with potting you would have to take steps to make sure your components don't overheat. IOW, I don't think you could just slap it together crudely and thoughtlessly and have it last a long time.
It's beginning to seem much easier to me to simply drown all the problems in vegetable oil.
Re:
Grooved Bobbins For Segmented Windings
Patrick, Wed Dec 22 2010, 05:23AM
jpsmith123 wrote ...
It's beginning to seem much easier to me to simply drown all the problems in vegetable oil.
Glad to see you finnaly coming around.

its about time.
anyway my semester just ended, ill be making a new bobin in january... ill post all the devilish details for you in a thread. this way you can see my method, will read that link too.
Re:
Grooved Bobbins For Segmented Windings
Patrick, Wed Dec 22 2010, 05:29AM
EDIT: from earlier: jpsmith123 wrote ...
Patrick here is a paper you might find interesting which compares some properties of various vegetabe oils for purposes of service as an electrical insulating liquid.

i have already read this artical it was decisive in convincing me to switch over to oils in general and food oils specifically. TY to Proud Mary, he posted this for me a long time ago.
OOPs this wasnt supposed to be a double post, been drinking dark Ale, clicky button being deceptive, sorry.
Re:
Grooved Bobbins For Segmented Windings
jpsmith123, Thu Dec 30 2010, 08:16AM
Believe it or not I just changed my mind back again. Yes, I realize this is getting silly now. I hope I'm done changing my mind for a while.
I just confirmed from the manufacturer of the cpvc material I'm using that "cooking oil", i.e., vegetable oil, is not compatible with CPVC.
Every time I endeavor to decide something, I subsequently find out I can't do it for some reason or another. It's starting to become quite burdensome...
Anyway, at first I wanted to use silicone potting compound, but it's hard to find anyone in the U.S. selling a small quantity of suitable material at a reasonable price. And to the extent I do find someone selling a small quantity at a reasonable price, it seems they don't have a complete set of specs on the material.
Same thing with epoxy but even worse.
Maybe I'm just being anal about it, but damn it, how can I compare products and pick the best one if I can't know what the thermal conductivity is, or the thermal expansion coefficient, or the dissipation factor? Or how these parameters vary with temperature?
Some manufacturers e.g., Loctite (formerly Dexter-Hysol) make an effort to provide a lot of this info, while others simply don't bother to mention it. But every time I find one I like, I find they only sell it in gallon or 5 gallon pails for a very high price.
If I'm going to use epoxy, I'd like a product with a relatively low viscosity (which would be easier to get the air out of); a relatively low dissipation factor; a relatively dielectric strength; a relatively high thermal conductivity; a relatively low hardness; a coefficient of thermal expansion that's somewhere close to that of CPVC; a relatively high "glass transition temperature"; and a not-too-short pot life.
If I could get this information on the all the prospective epoxies available at a reasonable price, I could pick one and do a little work with the numbers, and make sure that I won't have any thermal problems or thermally related issues.
But generally, unfortunately, no. Instead I find stuff like this:

, where you can buy two quarts for $30, apparently a good deal, but you don't get any info on thermal properties or dissipation factor.
So what good is that? It's beyond frustrating. I'm back to the beginning again with this potting nightmare.
Patrick wrote ...
jpsmith123 wrote ...
It's beginning to seem much easier to me to simply drown all the problems in vegetable oil.
Glad to see you finnaly coming around.

its about time.
anyway my semester just ended, ill be making a new bobin in january... ill post all the devilish details for you in a thread. this way you can see my method, will read that link too.
Re: Grooved Bobbins For Segmented Windings
Patrick, Thu Dec 30 2010, 08:09PM
what happens to the cpvc when exposed to oil?
Re:
Grooved Bobbins For Segmented Windings
jpsmith123, Thu Dec 30 2010, 09:54PM
Here's what they say about it:
"When CPVC pipe is installed in kitchen areas the pipe must be protected from contact with grease or cooking oils. Certain cooking oils can cause the CPVC piping to crack, leak or break when applied to the piping system. Consideration must be given to not only protecting the pipe from direct contact with cooking oils and/or grease, but also contact that may occur from airborne grease or oil from the environment such as cooking. Exposed piping in areas where CPVC pipe might come in contact with cooking oils and grease should be protected using a soffit system or with a complete coating of high quality water based paint that fully protects the piping system."

Re: Grooved Bobbins For Segmented Windings
Patrick, Thu Dec 30 2010, 11:08PM
whoa! i did not know that.
Re: Grooved Bobbins For Segmented Windings
jpsmith123, Fri Dec 31 2010, 05:33AM
Things may not be as bad as that statement implies, but I'm not going to chance it.
Apparently if one wants to use vegetable oil, one needs to go with a PE or PP coil form...and I'm already sick and tired of machining coil forms, so I'm just going to go ahead and use epoxy, as soon as I find one I like that's available in a small quantity at a reasonable price.
Re:
Grooved Bobbins For Segmented Windings
jpsmith123, Wed Mar 23 2011, 12:58AM
Well here's the latest (and I hope final) arrangement - before final assembly and potting:
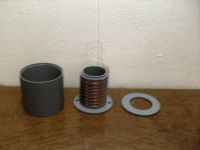
In part because of concerns about high diode current and poor regulation, I decided to go with a full-wave quadrupler, thus necessitating an increase in secondary turns in order to get at least 12.5 kv peak out of the transformer (for 50 kvdc output).
This latest coil has 600 turns of 30 gauge magnet wire on grooved cpvc. What's not shown are the feed-through insulators that I'm still working on. (They will basically have an external geometry similar to a spark plug).
When I made these parts, I labored under the illusion that I was going to encapsulate the assembly with a certain epoxy that I had found, which not only had some available specs., but which specs. I thought would suffice for the application. But when I went to order the stuff from Ellsworth adhesives, they told me that it was no longer available. So the project now has to wait again until I find an affordable alternate material.
Re: Grooved Bobbins For Segmented Windings
Patrick, Wed Mar 23 2011, 01:04AM
Oooooooooo very nice! can we get a pic thats of better resolution?
Re: Grooved Bobbins For Segmented Windings
jpsmith123, Wed Mar 23 2011, 01:09AM
Thanks Patrick. I might have at least one of the insulators done by tomorrow...if so I'll post a better picture with at least one insulator installed.
Re: Grooved Bobbins For Segmented Windings
Patrick, Wed Mar 23 2011, 01:15AM
Have you seen my insulators here on the forum?
Re: Grooved Bobbins For Segmented Windings
jpsmith123, Wed Mar 30 2011, 01:36AM
I thought I'd have the feed-through insulators completed by now, but I should've known better at this point.
Everything I've done so far seems to be just barely at the limit of what's possible and/or practical to do; between limitations with this lathe, limitations with materials, limitations with money for tools, parts, etc., it all adds up to a breathtaking PITA.
Maybe if I have some luck, I'll finally be ready to pot this thing in another week or so.
Re:
Grooved Bobbins For Segmented Windings
Patrick, Wed Mar 30 2011, 02:23AM
jpsmith123 wrote ...
I thought I'd have the feed-through insulators completed by now, but I should've known better at this point.
Everything I've done so far seems to be just barely at the limit of what's possible and/or practical to do; between limitations with this lathe, limitations with materials, limitations with money for tools, parts, etc., it all adds up to a breathtaking PITA.
Maybe if I have some luck, I'll finally be ready to pot this thing in another week or so.
dont abandon your work, keep going, I have the same problems. Being so hard will make our victory even better.
See if you can find small cheap quantities of these for potting:
Henkel E1300 Common Electrical Epoxy, Potting.
Insulcast SET1-140 Thermally Conductive Epoxy, Potting
Quantum Silicones QSIL40 Common Electrical Silicone for small devices, Potting.
Re:
Grooved Bobbins For Segmented Windings
jpsmith123, Wed Mar 30 2011, 01:58PM
Here's the stuff I was attempting to order...when they told me it was no longer available:

Excellent specs, I would say...best combination of properties I've seen so far.
The manufacturer, "Resin Technology Inc." is really "mysterious", and it's hard to talk to anyone directly at the company who can supply any information. They seem to always refer me to third parties who then have to "get back to [me]".
Anyway, I'm now looking at an epoxy marketed by Aavid Thermalloy "Ther-o-Bond 1500". It seems to have good specs (as far as I can see), but guess what, it's apparently also made by the mysterious "Resin Technology Inc.", and it's also very expensive.

At this point I'm still looking, so I'll check out the products you mentioned.
Re: Grooved Bobbins For Segmented Windings
James, Wed Mar 30 2011, 06:01PM
You can get silicone potting compound from TAP Plastics. They have epoxy too, but it's cheaper to get that from US Composites or Aircraft Spruce.
For oil I like to use food grade mineral oil. It's nice and clear, easy to work with, and pharmacies sell it as a laxative. I'm still looking for a local place to get gallon jugs of it though.
Re: Grooved Bobbins For Segmented Windings
jpsmith123, Wed Mar 30 2011, 06:30PM
Hello James,
I've found that there are lots of places to buy relatively cheap RTV and epoxy. The problem is, they usually have no specs (or very limited information) on the material.
Afer having invested many hours of time, some money, and suffering lots of aggravation, I'm not inclined to take chances on the suitability of cheap generic products.
Basically I'm looking for something that has a relatively low viscosity, is at least moderately thermally conductive, has low loss (i.e., a low dissipation factor), high dielectric strength, and a CTE that's somewhere in the ballpark of the CPVC material I'm using. This seems to rule out most cheap, generic materials.
As it turns out, about 10 minutes ago I found a company that seems to have what I want, at a cost of $50 in a pint quantity. I think I'm going to try to order some and see what happens.
Regards,
JP
Re:
Grooved Bobbins For Segmented Windings
James, Wed Mar 30 2011, 10:07PM
I just looked at US Composites

and noticed that they sell rubber potting and molding compounds too. They have datasheets for many of the products.
Re: Grooved Bobbins For Segmented Windings
jpsmith123, Thu Mar 31 2011, 03:37PM
Can you provide a link to some of these data sheets?
Re: Grooved Bobbins For Segmented Windings
Daedronus, Thu Mar 31 2011, 03:57PM
Would white delrin be a good choice for a bobbin?
For something like a flyback transformer...
Re: Grooved Bobbins For Segmented Windings
jpsmith123, Thu Mar 31 2011, 09:39PM
I've never done anything with Delrin, but in looking at its properties, it seems like a potentially useful material for a bobbin.
Depending on how you use it however, one potential issue might be its low surface energy; i.e., most adhesives will not stick to it (unless the surface is corona treated or something).
One reason I decided to go with cpvc is because I can glue/epoxy the pieces together.
In looking at mechanical, thermal and electrical properties, and of course, cost and availability, CPVC seemed like a good choice to me. I wish it had a lower dissipation factor, but I guess you can't have everything.
Re:
Grooved Bobbins For Segmented Windings
James, Thu Mar 31 2011, 10:51PM
Daedronus wrote ...
Would white delrin be a good choice for a bobbin?
For something like a flyback transformer...
Delrin/Acetal is nice stuff. It's not cheap, but it machines beautifully and I've used scraps of it for a number of different things. As far as I know it's quite chemically resistant too.
Re:
Grooved Bobbins For Segmented Windings
jpsmith123, Tue Apr 05 2011, 02:42AM
Well here's the coil assembly with the feed through insulators attached to one flange of the bobbin. I guess it's ready to have the wires attached, the outer cylinder put in place, and then be potted.
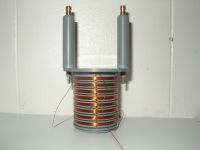
The only thing is, I don't like it very much. Sometimes it's hard to imagine just what something will look like until it's built and sitting right in front of you.
It will probably hold up...but I just don't like the idea of running the lead from one side of the coil to about 0.125" away from the other side of the coil.
If I could only think of how to make some "saddle washers" that would seat against the outside cylinder (i.e., that would match the outer radius), I would bring the terminals out radially, which would reduce the field to a more conservative value.
Re:
Grooved Bobbins For Segmented Windings
Patrick, Tue Apr 05 2011, 05:36AM
jpsmith123 wrote ...
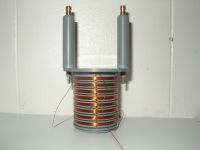
The only thing is, I don't like it very much. Sometimes it's hard to imagine just what something will look like until it's built and sitting right in front of you.
It will probably hold up...but I just don't like the idea of running the lead from one side of the coil to about 0.125" away from the other side of the coil.
Excellent!!! I see you will be using the sparkplug type boots and sockets.
125 x 300V/mil = 37.5kV of standoff, so your probably fine.
Re: Grooved Bobbins For Segmented Windings
Newton Brawn, Tue Apr 05 2011, 01:52PM
Here the other method to wind a 15kV choke;
Re:
Grooved Bobbins For Segmented Windings
Patrick, Wed Apr 06 2011, 12:44AM
Newton Brawn wrote ...
Here the other method to wind a 15kV choke;

I dont see much detail. how was this made? What is its significance?
Re:
Grooved Bobbins For Segmented Windings
jpsmith123, Sat May 07 2011, 05:12PM
Well Patrick I just did a quick low power test of the coil, and it seems quite good. Everything looked flat from 20 to about 40 kHz.
The coil I tested was not the multisegmented one, but the layered one I just wound, which has 560 turns of 26 gauge wire.
I'm going to do some more tests later, but so far I'm happy with it. (The only problem is the fact that it's short about 40 turns because I foolishly didn't measure the wire diameter before winding it).
Apparently making the coil "tall and skinny", along with extra layer insulation, really helps.
With 26 gauge wire, it should be capable of 4 to 5 kw throughput I would imagine. Moreover, there's still quite a bit of room inside the coil housing. It seems to me that I could also reduce the width from 0.75" to 0.5", switch from 26 to 28 gauge wire, and put two coils in series, which would produce much more voltage.
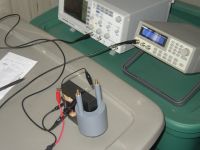
Re: Grooved Bobbins For Segmented Windings
Patrick, Sat May 07 2011, 05:47PM
It looks excellent. A point of advice though...I assume everyone knows about skin effect... but many fail to realise the significance of the proximity effect (With 26 Awg I think youll be fine below 80kHz).
How did you arrive at the 4-5kW number?
--How many turns would your primary normally have?
--What is the core number and maker?
Maybe I could verify some of your math?
Re: Grooved Bobbins For Segmented Windings
jpsmith123, Sat May 07 2011, 11:36PM
The core is a ferroxcube U100/57/25-3C90. (BTW I was satisfied with it until I saw TSC's new "50all" material, which looks much better than 3C90).
My estimate of as-built power throughput capability is based on the wire size (26 gauge, assuming 0.5 A max current), the number of turns (about 560) and a drive level of approximately 23 to 25 volts(peak)/turn.
Anyway, I compared the segmented coil pictured above with the layer-wound coil, and although the layer wound coil seems good, and is quite useable, IMO, the segmented coil appears to have a better frequency response.
Basically what I did is load the secondary coil with a 68k resistor (to present about 50 ohms to the generator), set the generator for a 1 volt output, and then sweep the primary, while looking at the primary and secondary voltages.
The layer-wound coil started to noticeably load down the (50 ohm) generator at about 45 kHz, whereas the segmented coil didn't do it until about 80 kHz, IIRC.
The segmented coil is wound with 30 gauge wire, so it would not be able to handle as much power. I might be able to make a similar segmented coil with 600 turns of 28 gauge, but as a practical matter that would be pushing that particular design right to the limit, IMO.
Re:
Grooved Bobbins For Segmented Windings
Patrick, Sat May 07 2011, 11:50PM
jpsmith123 wrote ...
The core is a ferroxcube U100/57/25-3C90. (BTW I was satisfied with it until I saw TSC's new "50all" material, which looks much better than 3C90).
Yes, your welcome.
jpsmith123 wrote ...
My estimate of as-built power throughput capability is based on the wire size (26 gauge, assuming 0.5 A max current), the number of turns (about 560) and a drive level of approximately 23 to 25 volts(peak)/turn.
Its not the wire guage that limits the curretn you can push through, the Guass, determines V/T, which is overall Vout, the H (in Oersteads or whatever) determines your current passability.
EDIT: assuming 450 Amps/cm^2, then:
26 Awg = 0.0159 nom dia. 0.00795^2 x 3.14 = 0.00198 in^2
0.000198 in^2 = 0.001278 cm^2
450 Amps x 0.001278 = 0.575 Amps for 26 awg.
so...
0.575 Amps for 26 awg.
X.XXX Amps for 28 awg.
X.XXX Amps for 30awg.
Re:
Grooved Bobbins For Segmented Windings
jpsmith123, Sun May 08 2011, 01:25AM
wrote ...
Its not the wire guage that limits the curretn you can push through, the Guass, determines V/T, which is overall Vout, the H (in Oersteads or whatever) determines your current passability.
Huh? You've lost me there...
wrote ...
assuming 450 Amps/cm^2, then:
26 Awg = 0.0159 nom dia. 0.00795^2 x 3.14 = 0.00198 in^2
0.000198 in^2 = 0.001278 cm^2
450 Amps x 0.001278 = 0.575 Amps for 26 awg.
so...
0.575 Amps for 26 awg.
X.XXX Amps for 28 awg.
X.XXX Amps for 30awg.
The wire table I generally use recommends a maximum current based on 500 circular mils/amp, but I suppose you can always squeeze a little more.
Re:
Grooved Bobbins For Segmented Windings
Patrick, Sun May 08 2011, 02:16AM
jpsmith123 wrote ...
wrote ...
Its not the wire guage that limits the curretn you can push through, the Guass, determines V/T, which is overall Vout, the H (in Oersteads or whatever) determines your current passability.
Huh? You've lost me there...
well the fewer turns you use on the primary and higher current per H on the ferrite, then the higher the power the ferrite will allow to be transferred. There is no part in which the secondary plays in deciding power, other than it must survive the V and I it conducts. I think.
Re: Grooved Bobbins For Segmented Windings
jpsmith123, Sun May 08 2011, 03:12AM
I think we're talking apples vs. oranges here.
I was referring to the "as-built power throughput capability"; meaning that, subject to the constraints imposed, the maximum power throughput will be in the range of 4 to 5 kw.
I could've designed it to run the core at a higher drive level, yes, which would require less turns, and thus allow for bigger wire (and more power throughput), but that would've increased the core loss.
But once the output voltage is decided and the secondary wound, now the core volts/turn is fixed, so the maximum power is limited by the I^2*R losses in the windings.
Re:
Grooved Bobbins For Segmented Windings
Patrick, Sun May 08 2011, 03:50AM
jpsmith123 wrote ...
I think we're talking apples vs. oranges here.
I was referring to the "as-built power throughput capability"; meaning that, subject to the constraints imposed, the maximum power throughput will be in the range of 4 to 5 kw.
I could've designed it to run the core at a higher drive level, yes, which would require less turns, and thus allow for bigger wire (and more power throughput), but that would've increased the core loss.
But once the output voltage is decided and the secondary wound, now the core volts/turn is fixed, so the maximum power is limited by the I^2*R losses in the windings.
yeah, ok ill put together a full length PDF, when i get the time after this semester, then we can have a full conversation on all this.
Re:
Grooved Bobbins For Segmented Windings
Ash Small, Sun May 08 2011, 11:21AM
jpsmith123 wrote ...
I think we're talking apples vs. oranges here.
I was referring to the "as-built power throughput capability"; meaning that, subject to the constraints imposed, the maximum power throughput will be in the range of 4 to 5 kw.
I could've designed it to run the core at a higher drive level, yes, which would require less turns, and thus allow for bigger wire (and more power throughput), but that would've increased the core loss.
But once the output voltage is decided and the secondary wound, now the core volts/turn is fixed, so the maximum power is limited by the I^2*R losses in the windings.
I've posted these specs before, but if your cores are similar to these, then 5 kW sounds about right.
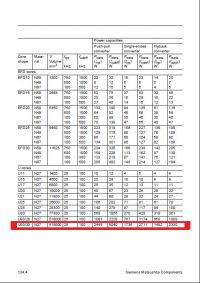
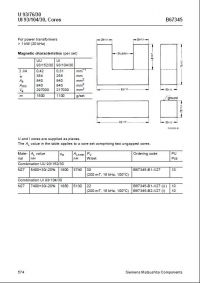
Re:
Grooved Bobbins For Segmented Windings
jpsmith123, Sun May 08 2011, 07:45PM
Here are some data sheets (power loss graphs) for N27, 3C90 and 50ALL ferrites.
Note that the N27 material is by far the most lossy, followed by the 3C90, and then the 50ALL, the least lossy of the three.
So for the same size core running at the same loss, you could have much higher power throughput with the 3C90, or somewhat better yet with the 50ALL material.
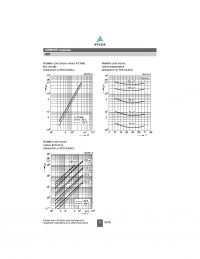
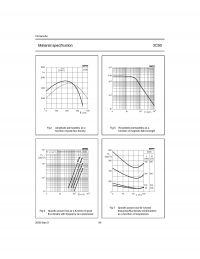
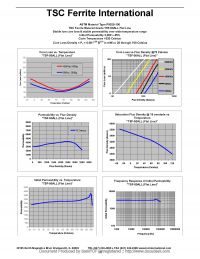
Re: Grooved Bobbins For Segmented Windings
Patrick, Sun May 08 2011, 08:37PM
TSC is cheap, and has many shapes and types, but the have long lead times for me getting my planars, took more than 5 weeks.
Re: Grooved Bobbins For Segmented Windings
Ash Small, Sun May 08 2011, 09:39PM
Thanks for posting that info IP. I'll digest it in the morning when I'm sober.
This is becoming quite an interesting project, with three of us 'perfectionists' each taking a different approach to the same problem.
BTW, are you in UK or US?
Re: Grooved Bobbins For Segmented Windings
jpsmith123, Wed May 11 2011, 12:46AM
I'm in the U.S., Ash.
BTW, the approach that I was originally going to take was to put the HV secondary coil and the multiplier together in the same enclosure and encapsulate the whole thing using some kind of silicone potting compound. (I want the multiplier to be repairable).
What stopped me there was the unexpectedly high cost of the RTV and the fact that all the products I found that I liked, e.g., Momentive RTV12, seem to only be available in gallon sizes (and larger).
Re:
Grooved Bobbins For Segmented Windings
Ash Small, Wed May 11 2011, 09:36AM
jpsmith123 wrote ...
.BTW, the approach that I was originally going to take was to put the HV secondary coil and the multiplier together in the same enclosure and encapsulate the whole thing using some kind of silicone potting compound. (I want the multiplier to be repairable).
I won't be potting anything, at least not to start with, for the following reasons:
First, modifying or repairing anything after it's been potted, even in silicon, is messy, time consuming, and unlikely to achieve good results.
Secondly, if cooling is required, this will be much better accomplished under oil. (I think)
I had thought of using Radhu's idea of smearing epoxy over the coil while winding, but I've pretty much decided against it now. I feel that vacuum impregnation after winding would give better results (no air bubbles) and, if under oil, wouldn't be permanent and would improve cooling if required.
It looks like, from the data you posted above, my cores will run hotter at the same power level than your's or Patrick's, but I'm planning on running at a lower frequency than Patrick, so heating may not be a big problem for me. If this proves to be the case I may then consider potting using vacuum impregnation, although that probably won't work on a coil that has previously been under oil.
I'm also hoping that capacitance will be less of a problem at lower frequencies (25 kHz), which should mean I can get more windings on the core, thus increasing voltage, and, maybe, only using a doubler rather than a multistage multiplier (less losses, I think). I also wish to use it for AC, which will mean running without a doubler or multiplier.
I'm still working on the coil formers, heatsinks, and the gate drive circuit, so I've still got quite a way to go.
(currently playing around with 1mm thick clear polystyrene CD cases and methyl ethyl ketone (butanone) to construct welded plastic segmented bobbins)
I'll probably post some ideas I'm toying with about ferroresonant GDT's, something which Steve Connor mentioned in passing, as I think this could have some advantages, but I'll save the details for another thread, once I've got a bit further with it.
Re: Grooved Bobbins For Segmented Windings
Patrick, Wed May 11 2011, 04:41PM
Where is this text appearing?
Re:
Grooved Bobbins For Segmented Windings
Patrick, Wed May 11 2011, 04:42PM
Dam, This wasnt meant to be a double post.If you pot with silicone meant for heat dissipation, its better than air, but not as good as oil.
For wire related matters go here:

WireTronics. Even if you dont buy their wire, they give out a lot of spec information.
And you can use this tool which I use all the time for deciding wire issues:
look for this link on their main wire page:
***http://www.wiretron.com/wtsetup.exe*** (I didnt want it to be an auto-downloading link so I commented the button-link out.)
This program also gives explanations for the kind of coatings, chemical sensitivity, whether annealing or crazing is a possibility and other important factors too. (single, heavy, triple, quad and the dimensions there of etc.)
Re: Grooved Bobbins For Segmented Windings
jpsmith123, Wed May 18 2011, 11:38PM
I took a few more measurements today: I measured the self-resonant frequency of three coils.
I very loosely coupled the signal generator (inductively) to the coil under test, and then swept the generator output while watching the scope. (I had a tektronix P6122 10x probe across the coil).
The 560 turn layer-wound coil measured about 205 kHz; the 600 turn segmented coil about 307 kHz; and the 360 turn layer-wound coil (with 26 gauge teflon insulated wire) measured about 485 kHz.
Assuming that the scope probe added about 11 pF (and subtracting that amount accordingly), this tranlates to an equivalent parasitic shunt capacitance of about 27 pF or so across the 560 turn layer-wound coil, and significantly less for the 600 turn multi-segment coil.
There's one more coil configuration that I didn't try yet, but I want to see what it looks like: a "tall and skinny" coil wound with 26 gauge teflon insulated wire. I'm going to make a different bobbin and wind one.
Re: Grooved Bobbins For Segmented Windings
Ash Small, Wed May 18 2011, 11:55PM
Keep us posted, IP.
Re: Grooved Bobbins For Segmented Windings
jpsmith123, Fri Jul 15 2011, 01:57AM
Well my first attempt at epoxy encapsulation had to be aborted.
The resin and hardener should be mixed accurately, so I decided to use my digital scale. I bought the scale about a year ago and used it a few times, but I never had more than a few ounces on it. On the box, it says "500g capacity".
So I wanted to mix about 100 ml or so which would be about 210 grams. I poured what I thought would be the approximately correct amount into a cup, and behold the 500 gram digital scale turned out to be only a 100 gram scale. So I had to pour it back into the can. Of course it's so thick that I lost half of it (it stuck to the cup), and it's all running down the side of the can, and somehow it just got on everything...
And this stuff is thick. Way thicker than what I imagined it would be. It's just sloppy and gooey and messy and just a general all around PITA.
So now if I still want to do it (and that's a big if at this point), I have to go spend more money on a bigger digital scale.
Re: Grooved Bobbins For Segmented Windings
Forty, Fri Jul 15 2011, 02:20AM
couldn't you just slowly add the epoxy to the cup, and zero it at every 100g?
if the mixing directions have a volumetric ratio then you don't even need the scale, just some disposable measuring cups
the ratio doesn't have to be absolutely perfect, so long as it is mixed well.
Re: Grooved Bobbins For Segmented Windings
jpsmith123, Fri Jul 15 2011, 02:28AM
Unfortunately zeroing the scale doesn't help. If I put more than about 105 grams on it, the display just says: "ovld".
According to the directions, the epoxy should be mixed by weight. The specific gravity is specified as being 2.1, so I can approximate it by volume, but after putting so much time and effort into the coils, I didn't want to take any chances with an inaccurate mixture.
Re:
Grooved Bobbins For Segmented Windings
2Spoons, Fri Jul 15 2011, 03:59AM
you may find the EPCOS ferrite design tool useful

,locale=en.html . Only has EPCOS cores in it of course, but still useful for getting ballpark figures for similar cores. Has a few nice things such as AC wire resistance, power transfer and air gap calculators
Re: Grooved Bobbins For Segmented Windings
Patrick, Fri Jul 15 2011, 05:34AM
Im going to PM you soon, i have new ideas related to this thread for getting higher V/turn with fewer turns, now that im finished with summer Math-120! Im a little too tipsy at the moment! That Guinness and New Castle packs a wallop!!!
Re:
Grooved Bobbins For Segmented Windings
Ash Small, Fri Jul 15 2011, 08:39AM
2Spoons wrote ...
you may find the EPCOS ferrite design tool useful

,locale=en.html . Only has EPCOS cores in it of course, but still useful for getting ballpark figures for similar cores. Has a few nice things such as AC wire resistance, power transfer and air gap calculators
Patrick wrote ...
. i have new ideas related to this thread for getting higher V/turn with fewer turns,.
Has anyone else looked at the EPCOS program yet?
I'm using these EPCOS N27 cores:
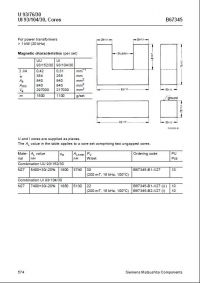
and I'm trying to work out how many primary turns I need (I'm assuming there is an optimum volts per turn ratio).
I'll be using rectified 240 V AC (peak 340 V DC), at 2.5kW per core, so I want a turns ratio of 150 (I think) for 50 kV.
I'm also puzzling over how many amps will be flowing in the primary, as, due to voltage ripple the voltage won't be constant, so it's not simply a case of using the peak voltage and power figures to calculate average current. (do I just use the RMS figure of 240 V, or will smoothing capacitors affect this?)
From looking at the EPCOS program, it would appear that I need to know all this in advance before I can input any relevant figures.
Any help would be appreciated. (Should this be in a new thread?)
EDIT: From what I can work out, the EPCOS program is telling me I need a single layer 160 turn primary of AWG 25, in order to transfer 2.5kW @ 25kHz, .No mention of volts and amps, though. I must be missing something.
EDIT EDIT: Is this where a series inductor is required, to help shape the pulse and limit the current?
Re:
Grooved Bobbins For Segmented Windings
jpsmith123, Fri Jul 15 2011, 03:35PM
That looks like an interesting tool, but for HV stuff, IMO, (especially when using the newest low-loss ferrites, at low to modest frequencies and low to modest flux densities), the most difficult issues are "mechanical" in nature; i.e., problems related to physical layout and construction and proper insulation...avoiding excessive stray capacitance and electric field enhancement resulting in corona.
2Spoons wrote ...
you may find the EPCOS ferrite design tool useful

,locale=en.html . Only has EPCOS cores in it of course, but still useful for getting ballpark figures for similar cores. Has a few nice things such as AC wire resistance, power transfer and air gap calculators
Edit:
Ash, I think getting 50 kv off the secondary is going to be very difficult. It may be possible, but it will be a real challenge, IMO. Can I ask why so high? Is it intended to feed a CW multiplier?
Re:
Grooved Bobbins For Segmented Windings
Ash Small, Fri Jul 15 2011, 05:19PM
jpsmith123 wrote ...
.
Ash, I think getting 50 kv off the secondary is going to be very difficult. It may be possible, but it will be a real challenge, IMO. Can I ask why so high? Is it intended to feed a CW multiplier?
That's just the target I'm aiming for. I was originally contemplating a supply that would power a fusor at 50kV and 50mA, but I'm also planning on having interchangable secondaries, etc, like some of your ideas seem to involve.
Others have said 50kV is reasonable, but 100kV is probably too high. I plan on using multipliers as well (my dream would be to reach 650kV but you appreciate the obstacles involved probably better than I do (there has been talk on other sites about putting multipliers inside vacuum chambers)).
I understood that 50kV was quite 'do-able', but if I really need >150 turn primary to push 2.5kW through one of those cores (I have two sets, which should push 2.5kW each @25kHz, according to EPCOS) I'm going to need ~25,000 windings on the secondary. I'm hoping I've made a mistake somewhere.
BTW, Are you familiar with the original Cockcroft-Walton experiment of 1932, and why they had to invent the multiplier?

(Other threads of mine on here are related to RF/magnetron ion sources/plasma generation for feeding particle accelerators,etc)
My next project is the rectifier for feeding the rectified 240V mains, which I will also use for DC welding (the rectifier, not 240V mains), I'm still doing the research for the HV transformer, .
Re:
Grooved Bobbins For Segmented Windings
Proud Mary, Fri Jul 15 2011, 06:02PM
Ash Small wrote ...
jpsmith123 wrote ...
.
Ash, I think getting 50 kv off the secondary is going to be very difficult. It may be possible, but it will be a real challenge, IMO. Can I ask why so high? Is it intended to feed a CW multiplier?
That's just the target I'm aiming for. I was originally contemplating a supply that would power a fusor at 50kV and 50mA, but I'm also planning on having interchangable secondaries, etc, like some of your ideas seem to involve.
Others have said 50kV is reasonable, but 100kV is probably too high. I plan on using multipliers as well (my dream would be to reach 650kV but you appreciate the obstacles involved probably better than I do (there has been talk on other sites about putting multipliers inside vacuum chambers)).
I understood that 50kV was quite 'do-able', but if I really need >150 turn primary to push 2.5kW through one of those cores (I have two sets, which should push 2.5kW each @25kHz, according to EPCOS) I'm going to need ~25,000 windings on the secondary. I'm hoping I've made a mistake somewhere.
You might want to think about a scaled-down version of this proven push-pull C&W oscillator-driver, which outputs 12kV @ 120kHz, 50kW.
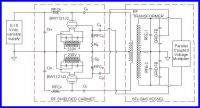
BW1121* is a water-cooled industrial triode with a 6.6V/230A filament - so with the design as it is, you have 460A of filament current to find before you can move your first pawn! (As well as a second mortgage to buy the valves in the first place! They are costly enough to get re-manufactured.)
But you could scale it down to your modest power requirements with the circuit arrangement just as it is.
Re:
Grooved Bobbins For Segmented Windings
Patrick, Fri Jul 15 2011, 07:28PM
Ash Small wrote ...
Any help would be appreciated. (Should this be in a new thread?)
Yes, lets not highajck JP's thread, start a new one Ash, and ill help you with the usuall math, physics and common screw ups, (im still learning though on the secondary power and relational math for H value, Klugesmith has been helpful too).
Re:
Grooved Bobbins For Segmented Windings
Ash Small, Fri Jul 15 2011, 07:35PM
Proud Mary wrote ...
.
You might want to think about a scaled-down version of this proven push-pull C&W oscillator-driver, which outputs 12kV @ 120kHz, 50kW.
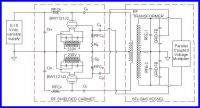
BW1121* is a water-cooled industrial triode with a 6.6V/230A filament - so with the design as it is, you have 460A of filament current to find before you can move your first pawn! (As well as a second mortgage to buy the valves in the first place! They are costly enough to get re-manufactured.)
But you could scale it down to your modest power requirements with the circuit arrangement just as it is.
Well, the 460 amp filament current could probably be obtained from either rewound welding transformers or even rewound MOT's. The valves themselves I could construct myself (depending on the coatings required on the cathode, etc) They possibly wouldn't even need to be under a permanent vacuum if I pump them down before each use, but a scaled down version probably wouldn't require this.
What advantage would a scaled down version, which, to me, looks pretty much like a 'run of the mill' centre-tapped push-pull transformer with triodes, have over a full bridge?
Re:
Grooved Bobbins For Segmented Windings
jpsmith123, Fri Jul 15 2011, 08:43PM
Well thanks for the thought but that's ok Patrick; it's all related enough that I don't think it dilutes the thread very much, in fact maybe it's more infomative/useful to expand it a little bit.
Patrick wrote ...
Ash Small wrote ...
Any help would be appreciated. (Should this be in a new thread?)
Yes, lets not highajck JP's thread, start a new one Ash, and ill help you with the usuall math, physics and common screw ups, (im still learning though on the secondary power and relational math for H value, Klugesmith has been helpful too).
Re:
Grooved Bobbins For Segmented Windings
Proud Mary, Fri Jul 15 2011, 08:52PM
Ash Small wrote ...
Proud Mary wrote ...
.
You might want to think about a scaled-down version of this proven push-pull C&W oscillator-driver, which outputs 12kV @ 120kHz, 50kW.
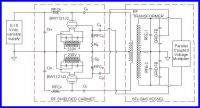
BW1121* is a water-cooled industrial triode with a 6.6V/230A filament - so with the design as it is, you have 460A of filament current to find before you can move your first pawn! (As well as a second mortgage to buy the valves in the first place! They are costly enough to get re-manufactured.)
But you could scale it down to your modest power requirements with the circuit arrangement just as it is.
Well, the 460 amp filament current could probably be obtained from either rewound welding transformers or even rewound MOT's. The valves themselves I could construct myself (depending on the coatings required on the cathode, etc) They possibly wouldn't even need to be under a permanent vacuum if I pump them down before each use, but a scaled down version probably wouldn't require this.
What advantage would a scaled down version, which, to me, looks pretty much like a 'run of the mill' centre-tapped push-pull transformer with triodes, have over a full bridge?
Oh, that's the whole point of showing you the circuit, Ash - to show that it could hardly be simpler, and calls for neither design innovation nor developmental time.
Re-winding large transformers is outside my frame of reference, but no doubt good results could be obtained by a skilful person with the right equipment. I'd be tempted to use 2V 400 AH industrial lead acid cells if I was to have a go at it, as I can't see the need for powering up the filaments for many minutes at a time, and it doesn't need much in the way of initiative or experiment to implement. But it's not something I have the time, space, money or interest to get involved with, intriguing though it most certainly is.
Re:
Grooved Bobbins For Segmented Windings
jpsmith123, Fri Jul 15 2011, 09:32PM
I should rephrase what I said: I think it's possible, but with the constraints you've mentioned previously (using the N27 core, and no potting, IIRC), it would be a hardship.
Having two sets of cores, to make two transformers, would seem to offer some possibilities.
I think it could be done using my "bud box idea", with teflon wire, using say two 500 to 600 turn coils (one on each leg) and potting it with RTV. I think using two "tall and skinny" coils in series will give you low capacitance, and the volume of the box will give you room (to keep the field strength reasonable) and the RTV will make it robust and reliable.
Of course with 1000 to 1200 turns or so you'll have to run at somewhere around 50kHz @ 200mT, or something like that, which, if using a "3C90" or "50ALL" core, means 30 to 40 watts of core loss and 100 watts or so with the N27 material (unless I made a mistake).
Ash Small wrote ...
jpsmith123 wrote ...
.
Ash, I think getting 50 kv off the secondary is going to be very difficult. It may be possible, but it will be a real challenge, IMO. Can I ask why so high? Is it intended to feed a CW multiplier?
That's just the target I'm aiming for. I was originally contemplating a supply that would power a fusor at 50kV and 50mA, but I'm also planning on having interchangable secondaries, etc, like some of your ideas seem to involve.
Others have said 50kV is reasonable, but 100kV is probably too high. I plan on using multipliers as well (my dream would be to reach 650kV but you appreciate the obstacles involved probably better than I do (there has been talk on other sites about putting multipliers inside vacuum chambers)).
I understood that 50kV was quite 'do-able', but if I really need >150 turn primary to push 2.5kW through one of those cores (I have two sets, which should push 2.5kW each @25kHz, according to EPCOS) I'm going to need ~25,000 windings on the secondary. I'm hoping I've made a mistake somewhere.
BTW, Are you familiar with the original Cockcroft-Walton experiment of 1932, and why they had to invent the multiplier?

(Other threads of mine on here are related to RF/magnetron ion sources/plasma generation for feeding particle accelerators,etc)
My next project is the rectifier for feeding the rectified 240V mains, which I will also use for DC welding (the rectifier, not 240V mains), I'm still doing the research for the HV transformer, .
Re: Grooved Bobbins For Segmented Windings
jpsmith123, Sat Jul 16 2011, 02:49AM
Ok, I just potted one coil. I potted a segmented coil with 600+ turns of 28 gauge magnet wire. It's sitting in the vacuum chamber curing right now as I type this.
I went to Harbor Freight and bought a 500 gram scale that was on sale for $11.99. Then I stopped at a dollar store on the way home and bought a cheap plastic measuring cup.
Then I used the scale on the cup to get the approximate amount I needed, then I weighed it, then I added 10% by weight of hardener. (Thankfully, as it turns out, the epoxy is much more manageable after you add the hardener to the resin).
The new scale and the measuring cup were the right tools. And it really helps having the right tools.
Anyway, I then mixed the epoxy for about 5 minutes with a spoon and then poured it into the coil assembly. This is where the first difficulty came in. Even with the pour spout on the measuring cup, it's a sloppy process and it makes a little mess.
In retrospect, I should've designed the coil former a little differently. As it was, I had to fill the coil assembly right to the very brim with epoxy, to make sure I had enough insulation between the end of the wire and the end of the housing. The problem is that when you pump it down, it foams up a little bit and wants to overflow the housing. I was able to pump it down a little bit, but not as thoroughly as I wanted to.
Another thing I thought of after the fact was that I should've filled it maybe 2/3 of the way, then pumped it down, then filled it the rest of the way and pumped it down again.
Luckily however, I don't think this particular coil assembly really needed to be vacuum encapsulated, because at most it'll be maybe 14 kv spread out over 2 inches.
I'll see what it's like tomorrow morning and post a picture if possible.
(Sorry for the double post).
Re:
Grooved Bobbins For Segmented Windings
Patrick, Sat Jul 16 2011, 05:30AM
jpsmith123 wrote ...
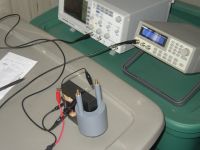
In this pic, is the outer casing a pipe of plastic? or flat sheet wrapped around? is that a seam or pencil line?
Re: Grooved Bobbins For Segmented Windings
jpsmith123, Sat Jul 16 2011, 05:49AM
Yep that's a pencil line. That outer case is made from a slightly turned down 2.5" CPVC pipe. I was going to use that piece in a different way - I was going to bring the HV output leads out radially - thus the pencil line. But then I decided to just machine another piece to do that, because I decided that the piece you see in the picture was too thin.
Re:
Grooved Bobbins For Segmented Windings
jpsmith123, Sun Jul 17 2011, 01:46AM
Well I just potted the other coil (the layer-wound coil with vertical leads). I found out that I couldn't go below a few torr pressure because something boils - I think it's the hardener.
It's still curing but it's looking good so far.
Here's a picture of the first coil (the 600 turn, 32 gauge segmented coil with radial HV output leads) in the vacuum chamber.
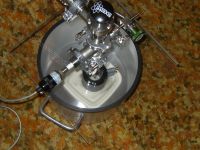
The epoxy was a learning experience. In a way it was "fun", but I hope I never have to learn it again.
I suppose the next thing to do will be to see how much the epoxy changed the frequency response of the coils.
Re: Grooved Bobbins For Segmented Windings
Patrick, Sun Jul 17 2011, 04:56AM
Yep, i think ill stick with bio-oil, more difficulty in liquid containing, but fewer unexpected's.
EDIT: if your vacuum was lowest at a few torr, does that mean the vapor pressure of your hardener is a few torr?
5 Torr = 0.1 PSI, yikes!
Re: Grooved Bobbins For Segmented Windings
jpsmith123, Sun Jul 17 2011, 06:36PM
Patrick, I don't blame you for deciding to go with oil. Epoxy sux, especially the epoxy I got. Yes the "specs" were good but working with it was nightmarish. Most annoyingly, the hardener apparently has a high vapor pressure and it's rather toxic (I think). I was supposed to get an MSDS with it but I didn't.
I hate the mess it makes. And when it started boiling on me, it splattered all over my chamber and I had to clean it all up later...what a PITA.
Anyway, I'm planning on trying my bud box idea, using teflon wire. I really think that might be the way to go. In fact, I'm thinking about putting the whole assembly inside the bud box i.e., HV secondary and multiplier, and filling it with RTV.
Re:
Grooved Bobbins For Segmented Windings
Patrick, Sun Jul 17 2011, 06:49PM
jpsmith123 wrote ...
...Most annoyingly, the hardener apparently has a high vapor pressure...
Shit.
Re:
Grooved Bobbins For Segmented Windings
Steve Ward, Mon Jul 18 2011, 07:21PM
For HV potting at work (fermilab) we use this silicone based stuff called Sylgard:

Its fairly thin, and is used for vacuum potting. You must allow for some overflow when you vacuum it out. I believe that they actually pull the air out of the stuff, after mixing (or maybe even before mixing) before they put it in the part to be potted. Then of course they cycle the vacuum on and off to drive the air out of the potting.
Though, i just checked the price of this stuff now, damn its expensive. Doesnt surprise me, we seem to always pick the most expensive materials possible

.
As mentioned before, oil is pretty nice stuff once you work out the containment details. I avoided it for a long time with my HV work, but really, it allows for the best performance possible compared to other insulation options. Ive got a multi-layered transformer that i'm working on at work for a cap charger that easily does 25kVAC at 60khz. It sits in some diala AX transformer oil, and has been evacuated to removed as much air as possible from the winding and the oil.
Re: Grooved Bobbins For Segmented Windings
jpsmith123, Mon Jul 18 2011, 10:21PM
I think the best or one of the best RTV encapsulants I've seen (in comparing the specs) has to be RTV12 (formerly a GE product, now Momentive Performance Materials).
That's the stuff I originally wanted to use. Unfortunately though, I was not able to find it for sale anywhere, in any quantity under a gallon. And it's expensive. Nor could I get a sample. I pleaded with them on the phone, but they simply wouldn't budge.
Anyway, from what I've learned about potting epoxies, it seems those with the lowest losses (DF) and relatively low viscosities all use some rather nasty chemicals (hardener). For my segmented coil, neither the DF nor the viscosity would have have been too much of an issue, but because of my experimental layer wound coil, I felt I needed both low loss and low viscosity, so I ended up with an expensive product (but luckily the manufacturer was willing to sell me just a pint).
It would've been nice though if the manufacturer had told me beforehand (by way of the data sheet) what the vapor pressure of the hardener was, that way I may have avoided making such a mess when I pumped it down.
Re: Grooved Bobbins For Segmented Windings
Ash Small, Tue Jul 19 2011, 12:27AM
Are you sure it was the vapour pressure of the hardener, JP. I once 'sorted out' the vacuum impreg. in a coil winding factory, and was surprised at the 'apparent boiling' of the 'one pack varnish' when it was 'pumped down'. (it was just the air coming out under vacuum).
Re: Grooved Bobbins For Segmented Windings
jpsmith123, Tue Jul 19 2011, 01:42AM
I'm not 100% sure, but I think so. It seemed to have a sudden onset, and it did not seem to decrease with time. Also, it was large, vigorous bubbles, compared to the "foaming" I saw at higher pressures.
Unfortunately I don't know exactly what the pressure was at the onset, since TC gauges like mine have very low resolution in that pressure range.
Re: Grooved Bobbins For Segmented Windings
Patrick, Tue Jul 19 2011, 03:53AM
Its worth figuring out though, even if you have to waste a shot-glass size container of the epoxy and hardener, un mixed in two seperate containers, then pull a vacuum and see!, with no coil or other stuff in the way you can be sure whether its trapped air in the previous attempt or boiling due to low pressure.
Re: Grooved Bobbins For Segmented Windings
Ash Small, Tue Jul 19 2011, 08:43AM
I've been thinking about this vacuum potting thing and I've come to the conclusion that maybe the way to go is a two-stage process.
first, immerse the coil in the epoxy/whatever and vacuum impregnate it, then, possibly before it has fully cured, pot it in the final package.
I think this must be how flybacks are made, looking at some of my flybacks. I don't think vacuum is used for the second stage. (maybe the potting compound is put under vacuum before being poured to remove any air bubbles)
Using this technique should avoid the 'boiling over' mess.
Re:
Grooved Bobbins For Segmented Windings
Proud Mary, Tue Jul 19 2011, 10:36AM
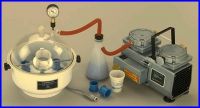
This apparatus allows the mixed potting compound and the objects to be encapsulated to be de-gassed separately before pouring, and for the pouring itself to be done under a vacuum
The mixed potting compound is placed in the centre container - a disposable paper cup - and the objects to be impregnated are placed in the molds round about. Once a suitable vacuum has been developed (550 Torr), the potting compound is then poured into the first mold by turning the external spindle knobs. The remote switch is then pressed to move the inner turntable round to the next mold to be filled.
The chamber is vented to the air, and then pumped down again, a cycle repeated several times, before the molds are taken out and left to cure at atmospheric pressure.
The conical filter flask is charged with Drierite dessicant.
Re: Grooved Bobbins For Segmented Windings
jpsmith123, Tue Jul 19 2011, 09:50PM
Well I'm confused, and I think I have to say that I was wrong about the hardener boiling in the chamber.
I looked up the chemicals by CAS # from the MSDSs (two for the epoxy resin and one for the hardener), and the vapor pressures were all in the range of 10 to 20 u. And since I know I didn't go that low, I have to say that, as Ash suggested, I must have been looking at entrapped air.
The vigorous bubbling and splattering I experienced is an issue. If I ever vacuum encapsulate anything again in the future, I'll have to do it differently.
Anyway, tomorrow I hope to test the coils and see how the epoxy has affected their frequency response...and if I don't like it, they're going right in the garbage...
Re: Grooved Bobbins For Segmented Windings
jpsmith123, Wed Jul 20 2011, 07:48PM
I give up on epoxy...
The second coil that I encapsulated, the layer wound coil, has a problem in that the epoxy is still a little "sticky" after almost two days. Upon being touched, it leaves a fingerprint, yet it's hard in the sense that I cannot gouge it with a fingernail.
And I'm baffled by this because the epoxy left in the mixing cup, from the same batch, seems to have cured perfectly, i.e., it's not "sticky" at all.
And there's a yet a third sample of epoxy from the batch, that I kept, and it too, has no problems, i.e., it's not "sticky".
This makes me think that I really did boil something away in the vacuum chamber, yet when I tested the pump, it pumped right down to the previously measured limit of about 35u, implying to me that no volatile stuff went through it.
Edit:
I just took a rag and wiped it, and now it's not "sticky" anymore, so maybe there's really no problem.
Re:
Grooved Bobbins For Segmented Windings
Patrick, Wed Jul 20 2011, 07:57PM
jpsmith123 wrote ...
I give up on epoxy...
The second coil that I encapsulated, the layer wound coil, has a problem in that the epoxy is still a little "sticky" after almost two days. Upon being touched, it leaves a fingerprint, yet it's hard in the sense that I cannot gouge it with a fingernail.
And I'm baffled by this because the epoxy left in the mixing cup, from the same batch, seems to have cured perfectly, i.e., it's not "sticky" at all.
And there's a yet a third sample of epoxy from the batch, that I kept, and it too, has no problems, i.e., it's not "sticky".
This makes me think that I really did boil something away in the vacuum chamber, yet when I tested the pump, it pumped right down to the previously measured limit of about 35u, implying to me that no volatile stuff went through it.
Welcome back to the oil club bro!
Re: Grooved Bobbins For Segmented Windings
jpsmith123, Wed Jul 20 2011, 08:01PM
I won't go willingly Patrick...Never!...they'll have to come and get me...
Seriously, my next effort is going to be something like what Glassman does.
Everything including multiplier, air insulated in a thick plastic case.
Re:
Grooved Bobbins For Segmented Windings
Proud Mary, Wed Jul 20 2011, 08:02PM
jpsmith123 wrote ...
I give up on epoxy...
The second coil that I encapsulated, the layer wound coil, has a problem in that the epoxy is still a little "sticky" after almost two days. Upon being touched, it leaves a fingerprint, yet it's hard in the sense that I cannot gouge it with a fingernail.
And I'm baffled by this because the epoxy left in the mixing cup, from the same batch, seems to have cured perfectly, i.e., it's not "sticky" at all.
And there's a yet a third sample of epoxy from the batch, that I kept, and it too, has no problems, i.e., it's not "sticky".
This makes me think that I really did boil something away in the vacuum chamber, yet when I tested the pump, it pumped right down to the previously measured limit of about 35u, implying to me that no volatile stuff went through it.
This surface tackiness is normal in unwaxed resins.
If yours is a waxless variety, you can prevent surface tackiness by laying a polymer sheet such as PTFE over the surface while it cures OR coat the surface with a PVA release agent spray, which you can wash off in the kitchen sink when the resin has cured. And as a last resort you can always remove the tacky layer with wet-&-dry sandpaper.
Re: Grooved Bobbins For Segmented Windings
jpsmith123, Wed Jul 20 2011, 08:08PM
The lowly rag...crude but effective...
Re:
Grooved Bobbins For Segmented Windings
Patrick, Wed Jul 20 2011, 08:44PM
Futurama...
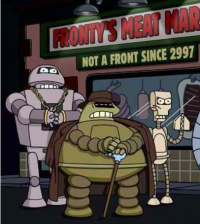
The metallic goons have been deployed, with instructions to make an offer JP cannot refuse.
jpsmith123 wrote ...
I won't go willingly Patrick...Never!...they'll have to come and get me...
Proud Mary wrote ...
This surface tackiness is normal in unwaxed resins.
If yours is a waxless variety, you can prevent surface tackiness by laying a polymer sheet such as PTFE over the surface while it cures OR coat the surface with a PVA release agent spray, which you can wash off in the kitchen sink when the resin has cured. And as a last resort you can always remove the tacky layer with wet-&-dry sandpaper.
There are permanent sparys too.
Its good of you to point this out Proud Mary, whan i do my polyester casting (sourced from Michaels) that surface layer is always a problem and we use that spray to make any air exposed surfaces dry, thus eliminating the "stickiness layer". But why did his two other waste cups dry/cure hard with no stickiness, even when exposed to air?
Im very suspicious he volatized a chemical off, in which case its not a surface defect, but a defect throughout the whole epoxy volume.
Re:
Grooved Bobbins For Segmented Windings
Ash Small, Wed Jul 20 2011, 09:48PM
Patrick wrote ...
.
Im very suspicious he volatized a chemical off, in which case its not a surface defect, but a defect throughout the whole epoxy volume.
I've had a drink, but I'll post anyway.
How do we test this?
Does this not bring us back to the post I made earlier about a two stage process?
Vacuum impregnation in a 'one part' matrix, followed by potting in an epoxy, possibly at lower vacuum?
I still stand by my earlier comments, you'd be surprised at the volume of air in a coil. (I'm speaking from experience).
Re:
Grooved Bobbins For Segmented Windings
Proud Mary, Wed Jul 20 2011, 10:42PM
Patrick wrote ...
Proud Mary wrote ...
This surface tackiness is normal in unwaxed resins.
If yours is a waxless variety, you can prevent surface tackiness by laying a polymer sheet such as PTFE over the surface while it cures OR coat the surface with a PVA release agent spray, which you can wash off in the kitchen sink when the resin has cured. And as a last resort you can always remove the tacky layer with wet-&-dry sandpaper.
There are permanent sparys too.
Its good of you to point this out Proud Mary, whan i do my polyester casting (sourced from Michaels) that surface layer is always a problem and we use that spray to make any air exposed surfaces dry, thus eliminating the "stickiness layer". But why did his two other waste cups dry/cure hard with no stickiness, even when exposed to air?
Im very suspicious he volatized a chemical off, in which case its not a surface defect, but a defect throughout the whole epoxy volume.
Well now, I have no sure answer to that one, Patrick, not knowing much beyond the rudiments of casting - but when air-inhibited waxless resin is cast in a vacuum, using the type of apparatus I described above, then no tacky layer forms because of the relative absence of air to inhibit it. This method is called
dry vacuum impregnation. (As I'm sure you know, air-inhibited waxless resins are used in multi-layer casting, as the tacky surface helps the next layer bond in. Waxed resins are used for glossy top coats - the wax floats to the surface during gelling, and so prevents the resin reacting with the air.)
Re: Grooved Bobbins For Segmented Windings
Patrick, Thu Jul 21 2011, 02:52AM
I propose a test, a small amout of epoxy in a cup under vacuum, and the remainder left atmospheric, then lets see.
Re:
Grooved Bobbins For Segmented Windings
Ash Small, Wed Aug 24 2011, 03:28PM
Following on from my comments in another thread, if you vacuum impreg the coil in this position:
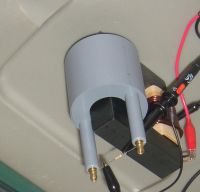
but leave excess tupe on the outside, and put a bung in the hole in the middle, you can overfill with epoxy, and it can bubble off without making a mess. After the resin has cured you can cut it to finished length, etc.
However, while I agree that epoxy encapsulation can have advantages in some applications, I'm sure you'll agree that the 'segmented, tall thin multiple secondaries' do seem to be ideally suited to oil cooling, which has to be the main advantage of oil encapsulation.
Just to clarify what I said elsewhere, the main advantage of oil encapulation is the benefit of cooling. Any advantages that epoxy/silicon encapsulation may have will come at the cost of less efficient cooling. In light of this I'm tempted to concentrate my own efforts in this direction towards oil immersion and cooling.
Re: Grooved Bobbins For Segmented Windings
IntraWinding, Wed Aug 24 2011, 06:07PM
Some high performance industrial epoxy resins are boastfully described as 'Solvent Free', which suggests cheaper stuff is 'watered down' with some solvent or other. I've tried degassing slow setting Araldite with a two stage rotary vacuum pump and it's very ineffective because it bubbles up so much. In fact it forms a stable foam. If you cut off the vacuum pump you can leave it to set that way. I've always assumed that was the mystery solvent boiling off. It didn't cause a sticky outer surface after setting, by the way. I've reverted to degassing Araldite with a temperature controlled hot air gun, which works very well if you heat it enough but not so much as to prematurely set it. No use for potting, of course.
Re: Grooved Bobbins For Segmented Windings
jpsmith123, Tue Sept 20 2011, 03:41AM
I tried to epoxy encapsulate one more coil (which got ruined, incidentally) but I came to the conclusion that the vigorous bubbling I saw was air, and not any volatile ingredient of the epoxy.
I first degassed the epoxy in a cup by itself, and after about 5 minutes, it essentially stopped bubbling. Then I opened the chamber to the atmosphere and poured the epoxy into the coil housing, then I pumped it down again - with more vigorous bubbling. And this time it took about 20 minutes before it stopped bubbling.
Anyway, the coil got ruined because the epoxy never cured. I think what happened is that I simply did not agitate it well enough before I used it - not just this time, but the other two times as well. I think that the stuff left in the bottom of the can was mostly Al2O3 filler, and not enough resin.
I'm really irritated too since the ruined coil was my best one yet. I redesigned the feed through insulators and placed the coil in a better spot. Mechanically and electrically, the coil assembly was a masterpiece. It sucks spending several days working on something and then having to throw it in the garbage.
I don't like working with thermally conductive epoxy, mainly because the unmixed resin is extremely viscous. I shook it a little bit before using it, but it apparently wasn't enough, and in retrospect I think it needs to be vigorously mechanically mixed somehow.
It seems to me that all non thermally conductive epoxy-resin systems have a relatively high dissipation factor, with the best ones being in the range of 0.01 to 0.02 or something like that. Apparently the only way you can get better performance (maybe in the range of 0.003 to 0.005) is by replacing some of the lossy resin with Al203.
In light of this, I guess I have to conclude that one more advantage of a "pie" wound secondary over a layer wound secondary is that you can use cheap, lossy epoxy, without suffering very much power loss - maybe on the order of a few tens of mw. Whereas with with a layer wound coil, depending on the operating frequency and the voltage between layers, I can easily see a few hundred mw to a few watts of dielectric loss.
Re: Grooved Bobbins For Segmented Windings
Patrick, Tue Sept 20 2011, 07:49PM
yep that solid stuff scares the hell out of me, ill be winding my own secondary soon, it will be a solid secondary of epoxy immersed in oil.
Re:
Grooved Bobbins For Segmented Windings
jpsmith123, Tue Sept 20 2011, 08:51PM
Well I've made some improvements to the design of my segmented coil former. I also now turn them on a mandrel between centers, and that works better when using the 0.125" grooving tool. The last one I made really came out nice. It should easily hold at least 600 turns of 28 gauge wire and I think it should be good for at least 15 kv without any potting.
I'm going to wind one later this week and then I'm going to pot it with this stuff:

(BTW maybe I could send you a coil former to wind your coil on?)
Re:
Grooved Bobbins For Segmented Windings
Patrick, Wed Sept 21 2011, 02:30AM
jpsmith123 wrote ...
Well I've made some improvements to the design of my segmented coil former. I also now turn them on a mandrel between centers, and that works better when using the 0.125" grooving tool. The last one I made really came out nice. It should easily hold at least 600 turns of 28 gauge wire and I think it should be good for at least 15 kv without any potting.
I'm going to wind one later this week and then I'm going to pot it with this stuff:

(BTW maybe I could send you a coil former to wind your coil on?)
Id rethink that carbon black epoxy.
Re: Grooved Bobbins For Segmented Windings
jpsmith123, Wed Sept 21 2011, 03:06AM
Why what's wrong with it?
Re: Grooved Bobbins For Segmented Windings
Patrick, Wed Sept 21 2011, 03:11AM
I generally try to avoid carbon black in my HV devices, carbon soot just doesnt sit right with me.
Re:
Grooved Bobbins For Segmented Windings
Ash Small, Wed Sept 21 2011, 11:06PM
Patrick wrote ...
I generally try to avoid carbon black in my HV devices, carbon soot just doesnt sit right with me.
Yep. Avoid carbon black at all cost.
Carbon is a conductor, not an insulator.
Re: Grooved Bobbins For Segmented Windings
jpsmith123, Thu Sept 22 2011, 01:10AM
At first I was apprehensive too, but it seems lots of manufacturers use it as a black pigment in their epoxy...as long as there's not enough in there to make it a bulk conductor it should be ok.
Re:
Grooved Bobbins For Segmented Windings
Patrick, Thu Sept 22 2011, 02:34AM
jpsmith123 wrote ...
At first I was apprehensive too, but it seems lots of manufacturers use it as a black pigment in their epoxy...as long as there's not enough in there to make it a bulk conductor it should be ok.
Really? Ive seen black dye used in paint and epoxy for HV devices, but not Carbon black.
It just seems to me that if carbon tracking is bad, then carbon "loading" should be too? Maybe im crazy though.
Re: Grooved Bobbins For Segmented Windings
jpsmith123, Thu Sept 22 2011, 03:51PM
I have to take back what I said about "lots of manufacturers" using carbon black in their epoxy. I could've sworn I saw it as an ingredient listed in many different epoxy resin MSDSs, but when I went back to look again, I only see it in the MSDS for the Epoxyset product I already used (and of course for the GC Electronics product).
The potential problem I see is settling of the carbon black. The concentration by weight may be only 0.5% or so, which would not be a problem if it's evenly distributed, but what if it settles and you don't mix it up good enough?
I wish GC made a clear product.
Re: Grooved Bobbins For Segmented Windings
Patrick, Thu Sept 22 2011, 05:59PM
Yeah, so far choosing an epoxy has not been a simple matter for me either, cure time, cost, properties, its all pretty complicated.
Also the problem im having now is that if i use mylar film, the epoxy wont stick to it, and ill have voids. So im thinking i should keep the secondaries under oil. So the voids when, they occur, immeadiatley fill with oil.
Re: Grooved Bobbins For Segmented Windings
Pinky's Brain, Thu Sept 22 2011, 06:18PM
For what it's worth, carbon is used for conductive resins, if you go beyond the percolation limit it becomes conductive ... even if it is not, it can't be good for the dielectric strength and constant.
Re: Grooved Bobbins For Segmented Windings
jpsmith123, Thu Sept 22 2011, 07:40PM
It's like most everything else...the dose makes the poison.
BTW Lawrence Livermore Lab has been working on a new generation of engineered insulators, and IIRC, these new "High Gradient Insulators" are a combination of insulating material and conductors. Apparently the conductors even out the electric field or something.
Re:
Grooved Bobbins For Segmented Windings
Patrick, Thu Sept 22 2011, 11:08PM
jpsmith123 wrote ...
BTW Lawrence Livermore Lab has been working on a new generation of engineered insulators, and IIRC, these new "High Gradient Insulators" are a combination of insulating material and conductors. Apparently the conductors even out the electric field or something.
Yes i watch their work with great interest, the conductive elements of an insuloator is fascinating.
Re:
Grooved Bobbins For Segmented Windings
jpsmith123, Fri Sept 23 2011, 03:51AM
Epoxy generally doesn't stick to mylar?
Anyway, depending on your design, trapped air pockets may not matter very much.
If you make a layer wound coil, for example, and the volts/layer is not too high, I don't think you'll have a problem. Check out figure 4 of this Dupont brochure:

There is also the issue of dielectric loss in the insulating medium: mylar + epoxy or mylar + oil or whatever. If Fig 8 is representative of most mylar films, I guess you could say it's a fairly lossy material...in the same range as typical [non-thermally conductive] epoxies.
Patrick wrote ...
Yeah, so far choosing an epoxy has not been a simple matter for me either, cure time, cost, properties, its all pretty complicated.
Also the problem im having now is that if i use mylar film, the epoxy wont stick to it, and ill have voids. So im thinking i should keep the secondaries under oil. So the voids when, they occur, immeadiatley fill with oil.
Re: Grooved Bobbins For Segmented Windings
Patrick, Fri Sept 23 2011, 04:16AM
I may use paper soaked in epoxy insteadof the mylar, as i only need 0.002-0.004 inches of spacing.
Ill show you my spool/former/bobin thingy once i get my physics and math homework done.
Re: Grooved Bobbins For Segmented Windings
jpsmith123, Sat Sept 24 2011, 05:13PM
How many volts-per-layer will you have and at what approximate frequency? If your interlayer voltages are moderate and your insulating materials are not too lossy, you shouldn't have any problems.
But I've seen a few epoxies supposedly intended for electrical potting that are really lossy; with some having a DF as high as 0.08 or so in the frequency range of interest. At 800 to 1000 Vrms/layer, @ 30 to 50 kHz and using one of the lossy epoxies, I can easily see 10 to 20 watts of dielectric losses in your coil, far exceeding your copper loss.
Re:
Grooved Bobbins For Segmented Windings
Patrick, Sun Sept 25 2011, 01:47AM
jpsmith123 wrote ...
How many volts-per-layer will you have and at what approximate frequency? If your interlayer voltages are moderate and your insulating materials are not too lossy, you shouldn't have any problems.
But I've seen a few epoxies supposedly intended for electrical potting that are really lossy; with some having a DF as high as 0.08 or so in the frequency range of interest. At 800 to 1000 Vrms/layer, @ 30 to 50 kHz and using one of the lossy epoxies, I can easily see 10 to 20 watts of dielectric losses in your coil, far exceeding your copper loss.
It works out to 1kV per layer, at 100kHz. Maybe i should work out a device to measure dissipation factor for epoxies and food oils? Any idea anyone?
Re: Grooved Bobbins For Segmented Windings
jpsmith123, Sun Sept 25 2011, 03:46AM
A while ago I calculated the approximate capacitance between two corresponding turns, in adjacent layers, using the dimensions and materials of one of my coils, and it was about 6 pF, IIRC. (In that calculation, I think the layer insulation was 0.014" thick).
So if you have for example 800 Vrms between two corresponding turns in adjacent layers, and an associated capacitance of 6 pF (although you may have more than that with thinner layer insulation), and a DF of, say, 0.015 at 100 kHz, you'll have about 36 mw of dielectric loss associated with those two turns, according to my calculations. This is a rough estimate, in part because there are usually multiple dielectrics involved with different loss factors and dielectric constants. With some materials there is also a significant temperature dependence. But it seems clear to me that dielectric losses are something that can get out of hand if you're not somewhat careful. (I seem to remember a discussion here a few years ago where someone built a transformer and was having some serious trouble with heat in the windings...and I think the culprit turned out be dielectric loss).
Re: Grooved Bobbins For Segmented Windings
Patrick, Sun Sept 25 2011, 05:00AM
Well then we'll have to figure out how to measure it then.
Re:
Grooved Bobbins For Segmented Windings
jpsmith123, Wed Sept 28 2011, 12:38AM
I think for my second set of experimental coils I will use this (clear) epoxy:

I was going to use the following (black dyed) one, but it supposedly has more thermal expansion.

For some reason they don't specify a dissipation factor for the clear epoxy, but it shouldn't matter too much in this case.
Re:
Grooved Bobbins For Segmented Windings
jpsmith123, Mon Oct 10 2011, 02:56AM
Well I now have a few "second generation" coil assemblies ready for potting. I think tomorrow I'll order the epoxy from mgchemicals.
I reduced the width of dividing sections between the coils, making room for another coil section. The end grooves on each side are also offset towards the center a little bit, making more room for insulation (epoxy) at the ends. The plastic is also somewhat thicker (radially), which should lower the capacitance.
The feedthrough insulators are also redesigned and should have even less field enhancement (although there wasn't much to begin with).
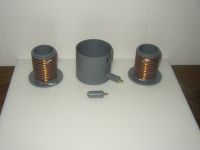
Re: Grooved Bobbins For Segmented Windings
Patrick, Mon Oct 10 2011, 03:34AM
You do exceptional work JP, that looks real good!
Re: Grooved Bobbins For Segmented Windings
jpsmith123, Mon Oct 10 2011, 12:44PM
Well thanks for the compliment, but I have to give credit where it's due: that's the OCD talkin'.
(BTW, when are you going to get yourself one of these semi-crappy little lathes so you can suffer making round things too?)
Re: Grooved Bobbins For Segmented Windings
Patrick, Mon Oct 10 2011, 05:05PM
What i really need is a CNC vertical mill, but im sure my apartment neibors wont like hearing it.
Re: Grooved Bobbins For Segmented Windings
jpsmith123, Tue Oct 25 2011, 08:06PM
I got the epoxy from mgchemicals today and I went to use it to encapsulate the coils, but when I opened it I found that the resin had undergone "crystallization"...supposedly the result of being stored at a relatively cold temperature.
So now according to the instructions I have to warm it up and stir it to restore it to normal. What a PITA epoxy is.
Edit:
It's taking forever to get the air out of the first coil assembly. It's been pumping for about 30 minnutes now and it's still bubbling, it's slowing, yes, but I'm amazed at how long it's taking.
And then right in the middle of everything, my vacuum TC gauge decides to die. I smelled that unmistakable burning electronics smell, and that was it.
Re: Grooved Bobbins For Segmented Windings
Patrick, Tue Oct 25 2011, 10:50PM
It sounds like you would have the same or fewer problems with oil.
how much $ was the sensor?
Re: Grooved Bobbins For Segmented Windings
jpsmith123, Tue Oct 25 2011, 11:46PM
With the exception of the "crystallization" issue (although I suppose that would happen with any epoxy), this epoxy is somewhat nicer to work with than the first stuff I used; although I'll reserve final judgment until I see how it cures.
Right now it actually has me a little worried, as I'm not seeing much of an exotherm yet. I'm sure I mixed it accurately...so I'll give it the 24 hours that the data sheet says it takes to cure and see what happens.
I think if CPVC was compatable with vegetable oil I would've made one experimental oil filled system, but as it is right now I'm determined to make epoxy work.
Anyway, my TC gauge uses Varian #531 TC tubes. The tubes usually go for $50 to $80. I took a quick look at the circuit board and I saw a burnt resistor. Maybe tomorrow I'll try to check it out and see what went wrong with it.
Re: Grooved Bobbins For Segmented Windings
Patrick, Wed Oct 26 2011, 01:42AM
If a resistor burned out often it means something else went wrong first, so dont just replace the resistor and think all will be well. Find the initial cause first.
Re: Grooved Bobbins For Segmented Windings
jpsmith123, Wed Oct 26 2011, 03:23AM
Ok well now I'm getting worried about the epoxy. It just doesn't look like it's going to cure. It's been about 7 hours now since I mixed it up, and it's still like syrup. It didn't get very warm, and the heat didn't last very long.
If I have to throw another coil assembly in the garbage, I'm going to be really, really irritated. I'm going to want the manufacturer to compensate me not only for the cost of the epoxy, but for the loss of the coil as well.
Hopefully I'm wrong and this epoxy just has some weird chemistry going on...hopefully tomorrow morning I'll find it as hard as a rock...but if not there's always beer and the comforting effect of a nasty phone call to mgchemicals.
As far as the burnt resistor is concerned, yes, I agree, as it's been my experience that a burnt resistor is usually not the primary problem.
Re: Grooved Bobbins For Segmented Windings
Patrick, Wed Oct 26 2011, 03:36AM
I will pray for your success tonight.
Re: Grooved Bobbins For Segmented Windings
Ash Small, Wed Oct 26 2011, 09:12AM
WARM IT UP.....80 degrees F should do it.
Re:
Grooved Bobbins For Segmented Windings
jpsmith123, Wed Oct 26 2011, 01:10PM
Well thanks Patrick, I think that helped!
I checked it this morning, and surprisingly, it hardened up nicely. You could've knocked me over with a feather.
Now I better go delete that nasty email in my "drafts" folder...the email I wrote after I got a head start on the beer...
Patrick wrote ...
I will pray for your success tonight.
Re:
Grooved Bobbins For Segmented Windings
Patrick, Wed Oct 26 2011, 04:15PM
No problem, i would have sugggested Ash's idea of heating it too if it didnt hardend as expected.
Remember the epoxies are generallly exothermic, but the slower curing ones (many hours) generate less delta temp due to the longer reation time, than epoxy which setup in minutes. ( given the same delta heat )
When i made one of my first HV probes i used several cubic inches of 5 minute epoxy, which generated enough heat to make the plastic start to SMOKE !

thermochemistry matters peeps.
Re: Grooved Bobbins For Segmented Windings
jpsmith123, Wed Oct 26 2011, 05:39PM
I just potted the other coil assembly. Now I'll be nervous...very nervous...until it hardens.
I had it in the vacuum chamber for about 30 minutes and it never stopped bubbling, but I had to end it at some point...before the epoxy got so tacky that I could no longer top it off (using the remainder of the batch left in the mixing cup).
Thus I know I didn't get all the air out, but since my previous analyses show a max Efield well below the corona threshold, hopefully it won't matter.
I also learned another important lesson: make sure you have a nice level spot available to place the potted assembly until it cures.
Re: Grooved Bobbins For Segmented Windings
Patrick, Thu Oct 27 2011, 01:08AM
Is it possible to build an "L" shaped vacuum chamber, then evacuate the coil fully of air, then tip the epoxy in? it seems like the viscosity (and tiny spaces) of the epoxy/coil is whats slowing the escape of the air and causing the foaming.
I wonder if studying how aircraft oil pumps strian out bubbles and prevent foaming would help...
Or see how other corps do it..
Re: Grooved Bobbins For Segmented Windings
jpsmith123, Thu Oct 27 2011, 01:41AM
If I had a lot of coils to encapsulate, and/or the Efield was higher, I think I would have to do it in a manner similar to what you're suggesting. Probably what I would do would be to feed the epoxy in from the top, down through a tube and into the coil housing. I can envision using something resembling a separatory funnel (used in chemistry) with a valve on the bottom (and which is also pumped down, so that only gravity acts on the epoxy).
The down side of something like this is that it would probably be messy. It's actually quite difficult (in my experience) to get the epoxy into the housing, neatly, filled up close to the edge, without getting it all over the place and runnning down the sides.
Re: Grooved Bobbins For Segmented Windings
Ash Small, Thu Oct 27 2011, 09:04AM
I picked up a brand new, unused, large high vacuum rotary feedthrough from Egay for £50 a while back.
For your application, which doesn't require 'high vacuum' you could knock up a rotary feedthrough using viton seals, especially as you have access to machining equipment. (you won't need ferro-fluidic seals)
You could then just tip the resin in.
Re: Grooved Bobbins For Segmented Windings
jpsmith123, Thu Oct 27 2011, 11:20AM
Tipping it in sounds good in theory, but in practice I've found it's difficult to do it without making a mess.
In my case I have about 0.5" of clearance between the two cylinders, and I'm pouring a viscous mixture - something like heavy syrup. Even when I use a measuring cup with a well-defined pouring spout and I rest the pouring spout on the outer cylinder, I still have to be very careful or it goes all over.
Re: Grooved Bobbins For Segmented Windings
Patrick, Thu Oct 27 2011, 02:21PM
I wonder if you should be filling it in progressive stages.
first fill it a third full at STP.
draw down to 50 microns.
fill second third full at STP.
draw down to 50 microns.
fill last third at STP.
draw down and leave for setup/cure.
Re:
Grooved Bobbins For Segmented Windings
Ash Small, Thu Oct 27 2011, 04:07PM
jpsmith123 wrote ...
Tipping it in sounds good in theory, but in practice I've found it's difficult to do it without making a mess.
In my case I have about 0.5" of clearance between the two cylinders, and I'm pouring a viscous mixture - something like heavy syrup. Even when I use a measuring cup with a well-defined pouring spout and I rest the pouring spout on the outer cylinder, I still have to be very careful or it goes all over.
Sounds like you need something like a conical flask, something with a 'neck'.
Re: Grooved Bobbins For Segmented Windings
jpsmith123, Thu Oct 27 2011, 05:09PM
Basically I do it in a few stages right now.
As soon as I mix the epoxy, I put the epoxy (still in the mixing cup) into the chamber and pump it down for 15 minutes.
Then I pour it into the coil assembly, filling it enough to just cover the last coil segment - which leaves about 1/4" inch room on the end for foaming/bubbling. (And this is not much room, so I have to pump it down slowly and carefully).
Then after about a half hour in the chamber, I remove it and top it off with more epoxy, and then I let it cure.
When the epoxy cures it leaves a concave meniscus (maybe it shrinks a little when it cures?), so I mix up a little more epoxy and top it off again.
The fundamental problem is that the multiple windings take up a lot of room and there's not much room between the last winding and the end of the coil. If there was at least a 1/2" of space, it would be a lot easier.
Anyway, I don't think doing it in more stages, would help very much, mainly because of the finite "pot life" of the epoxy. (In this case 1 hour). Don't forget that as soon as it's mixed, the reaction starts and the viscosity starts to slowly increase. If you filled it and pumped it down in multiple stages, by the second or third addition/pump down cycle, it'd already be thicker and harder to de-air accordingly. Doing it in stages like you suggest would probably help if you were using an epoxy with a longer pot life, however.
Re: Grooved Bobbins For Segmented Windings
Ash Small, Thu Oct 27 2011, 07:56PM
If you pump it down, then pour it under vacuum, it avoids all of the problems mentioned above.
Re: Grooved Bobbins For Segmented Windings
jpsmith123, Thu Oct 27 2011, 10:58PM
If you design and build it properly, then yes, I think it would solve the problems (hopefully without creating any new problems).
I seriously considered trying to do it, but I concluded that to do it right it would be a fairly involved project, and I didn't feel like bothering with it just to encapsulate a few coils.
Re: Grooved Bobbins For Segmented Windings
Patrick, Fri Oct 28 2011, 12:57AM
i like my oil filled project, looks cool in a clear case and fewer problems, or at least the same as your vaccuum drawn epoxy.
Re:
Grooved Bobbins For Segmented Windings
Ash Small, Sat Oct 29 2011, 10:07AM
jpsmith123 wrote ...
If you design and build it properly, then yes, I think it would solve the problems (hopefully without creating any new problems).
I seriously considered trying to do it, but I concluded that to do it right it would be a fairly involved project, and I didn't feel like bothering with it just to encapsulate a few coils.
I'm planning a similar system for vacuum induction casting, which will also be usable for pouring epoxy, etc.
Ther are alternatives to using rotary feedthroughs, but these consist of using bellows or magnets.
Re: Grooved Bobbins For Segmented Windings
jpsmith123, Sat Oct 29 2011, 01:34PM
If I were to try it, I think I would make two separate vacuum chambers - the one with the epoxy being directly vertically above the one holding the coil assembly.
Then I would pump both chambers down, and then after reaching a predetermined level of vacuum, open a valve or something and let a measured amount of epoxy pour straight down through a tube into the coil assembly.
Re: Grooved Bobbins For Segmented Windings
ZakWolf, Sat Oct 29 2011, 09:08PM
I check this thread when ever there is an update, but im not quite sure what your building?
what ever it is it looks great, awesome job.
could someone fill me in on whats going on, thanks
Re:
Grooved Bobbins For Segmented Windings
Patrick, Sat Oct 29 2011, 11:03PM
SublimeVolts wrote ...
could someone fill me in on whats going on, thanks
Big ferrite transformer for HV, HF, at high current without paralleling ridiculous numbers of poorly matched flybacks. High reliability and long lived too.
Re: Grooved Bobbins For Segmented Windings
ZakWolf, Mon Oct 31 2011, 06:01PM
ahh..... thank you Patrick. Looks like its going well
Re: Grooved Bobbins For Segmented Windings
Patrick, Mon Oct 31 2011, 09:42PM
Yep, YW.