The Tesla Thermionic Valve Wireless Energy Transmitting Apparatus
Cesiumsponge, Fri May 01 2009, 05:07AM
Gather around and witness the fruits of Tesla's lifelong work! Expeditiously, I shall be unveiling an unrealized dream of his, a masterful thermionic valve apparatus of superlative wonder and whimsy after many a sleepless night of scheming and laborious toil.
A mechanism of excessively high potential and very considerable frequency.
A contraption to capture the wild possibilities of a dawning age of industrialism.
A device to astound and mystify the youth,
A machine to bewilder and confound the old!
Fascination and fear,
Stupor and surprise!
More lively than an electrotherapy session and twice as delicious as a cool radium tonic, guaranteed!
Before the grand unveiling, verification, and tuning takes place scant weeks from now with all notes, I will tantalize this kind audience with some previews.
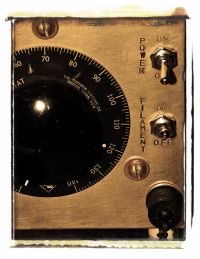
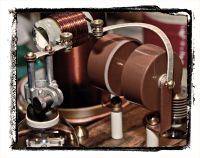
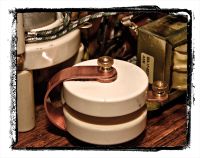
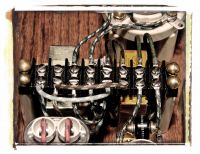
Re: The Tesla Thermionic Valve Wireless Energy Transmitting Apparatus
Alex, Fri May 01 2009, 05:14AM
Excellent work! I've been following along elsewhere of course, but it's good to see that you're putting it up here.
Re: The Tesla Thermionic Valve Wireless Energy Transmitting Apparatus
Finn Hammer, Fri May 01 2009, 05:35AM
Funny as _some_ of these yanks sound more brittish than most englishmen do.
Anyway, nice teaser.
Cheers, Finn Hammer
Re:
The Tesla Thermionic Valve Wireless Energy Transmitting Apparatus
Proud Mary, Fri May 01 2009, 08:14AM
I do like the vintage cloth-covered wire. A wonderful touch!

Re: The Tesla Thermionic Valve Wireless Energy Transmitting Apparatus
aonomus, Fri May 01 2009, 08:17AM
Wow, I have to say it looks beautiful, practically museum piece quality.... good build, now lets see what it can do. :D
Re: The Tesla Thermionic Valve Wireless Energy Transmitting Apparatus
Coronafix, Fri May 01 2009, 08:59AM
This looks fantastic, so steampunk!
Re:
The Tesla Thermionic Valve Wireless Energy Transmitting Apparatus
Dalus, Fri May 01 2009, 12:10PM
Looks great. A lot of detail and time stuffed in a small space a very nice build.
Kinda funny I was asked to build a DRSSTC in steampunk style. Too bad the company had no idea how much they cost

Otherwise this would have been a great project for me to nick some design features from.
Looking forward to see the completed device in general. Hope to see some /dev/random

Re: The Tesla Thermionic Valve Wireless Energy Transmitting Apparatus
ElectricalEngg., Fri May 01 2009, 12:52PM
wow cant wait to see it work :)
Is it something like Wardenclyffe Tower???
Re: The Tesla Thermionic Valve Wireless Energy Transmitting Apparatus
teravolt, Thu May 07 2009, 07:23PM
Beutifull work, do you have a full size picture of your aperatus? aslo I am looking for one of those clamps on the plate with the finger nuts,second picture from the left, where can I get 4? thanks if you can help me N.B
Re: The Tesla Thermionic Valve Wireless Energy Transmitting Apparatus
Cesiumsponge, Thu May 07 2009, 10:06PM
A full write-up with large images is about a week or two away. I'm currently doing some final work on it. Everything is about 95% done. I'll verify it works, then post, then do tuning and get input/commentary. My subsequent projects will be actual running logs with updates. It's just that I've gotten so far on this before I realized I should start a project thread...so I'm going to finish it before posting details.
The plate cap heatsinks with axial fins I am currently using were found on ebay as a pair. I couldn't find anyone else that has them. The only commercial ones I've found are the aluminum radially finned heatsinks (by Eimac I believe) and white porcelain socket caps. I've also seen bakelite units available.
Re: The Tesla Thermionic Valve Wireless Energy Transmitting Apparatus
teravolt, Fri May 08 2009, 12:45AM
thanks, can't wate
Re:
The Tesla Thermionic Valve Wireless Energy Transmitting Apparatus
Cesiumsponge, Sat May 09 2009, 09:18AM
Change of plans! I was made aware that OMJ plugged my project as a feature of the week on the main page so I'm going to plug what I have so far as it'll only be up for a week. It would make little sense for everyone visiting my project only to see a couple photos. I'm lagging a bit on updated photos but this installment of photos should keep most folks happy.
A note:
Some of the photos are outdated or do not correspond to the final build, or seem to be anachronistic. I changed a couple components here and there, and didn't think it worthwhile to redo for the photo documentation as nothing important has changed. All wiring has been cable laced as of today. The grid leak resistor shown is different from the variable unit used, and so on. I will do a final round of photos of the finished coil when it's completely ready. Let me preface this post that it's subject to changes/edits as necessary; its 2AM and I barely assembled this post as it was.Project Inception and Goals:The project was named the Tesla Thermionic Valve Wireless Energy Transmitting Apparatus as a throwback nod to turn of the century terminology. It's inspired by vintage and antique high voltage devices from the 20th century and the modern steampunk movement of revitalizing the victorian age industrialism with a modern twist. The design elements of this tesla coil are largely based on the types of meterials used. Steel, aluminum, and plastics would create a sleek modern feel while brass, copper, and wood materials create a vintage feel of yesteryear. With all the stunning coils being built with modern materials like lexan and acrylic, I decided to go counterculture and introduce something familiar to the old guard. I suppose in this manner, both extremes of tesla coil construction methods are covered. However, I took care to use materials that should last for a very long time. Wood was completely sealed with pure tung oil. Wiring, despite being braided cloth, use modern materials that haven't had 50 years to degrade, for example.
My goal for this project was to rebuild an existing single 810 VTTC circuit I had constructed about five years earlier, based off of Steve Ward's coil. It performed remarkably well, peaking at 17", and it was reasonably slick looking, utilizing HDPE construction. However it never really warmed up to me and eventually I dismantled it. I took a liking to old vintage high voltage devices over time and the steampunk movement was a nice revitalization of old world craftsmanship and skills you don't often see today.



By designing a coil utilizing the dicotemy between past and present, I modeled up a coil that keyed in on being visually attractive and unique in appearance, while being fairly easy to manufacture (with my given tooling) with prefabricated components requiring minimal machine work since I do not have access to many tools or any machine tools. The highest end tool I have at home is a large tabletop drill press. My Mitutoyo calipers cost more than my drill press. The layout is different so I expect some tuning issues to deviate from what worked on the original build but I expect performance to be similar. The addition of a variable grid leak resistor (not a feature on the last one) should give me the ability to reduce plate heating.
This is the original model which I constructed and did dimensional figures with. Things have changed a bit since then but it's remained relatively close to original intent.
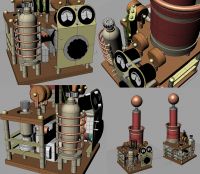
Here is the original coil as it was constructed a half decade ago:
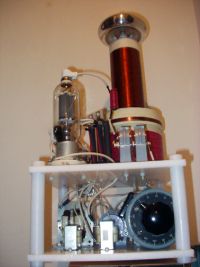
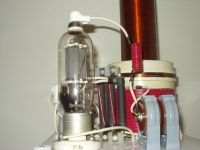
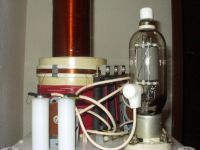
And a schematic that is up to date (I believe) reflecting the current coil configuration:
Building materials:The key to design is to pick a theme and one or two central focal points. The triode and triode guard on this project is probably considered the focal point as it takes up an entire corner quadrant. The triode guard consists of pieces of .250" copper tubing that is pounded and worked to shape. These are used as running spacers between stacks of ceramic standoffs.



I utilize an excessive amount of ceramic insulators in the build, over 50 by a rough estimate. Lots of accents were added in the way of brass and copper. Copious use of brass spheres, half spheres, and knurled thumbscrews were used to terminate threaded rods and machine screws at choice points in addition to cosmetic effect. Items such as the two tiers of brass railing serve to strengthen the inherently weak tensile strength of ceramic threads in the standoffs I used as pillars and the tube guard was comprised of lengths of formed copper tubing and ceramic spacers.




Red oak was utilized for it's durability and toughness as a hardwood which is readily available and affordable, sealed in pure tung oil which prevents moisture absorption. Everything utilizing machine screws and rods were attached to the oak decks by way of threaded wood inserts. This gives the strongest connection and also the most reusable assembly method. You can assemble and disassemble indefinitely until your fingers go numb. Wood screws have a tendancy to vary in thread pitch from one another, and constantly removing or installing them can strip out or chew up the hole because you aren't aligning the lead thread of the screw with the lead thread of the hole each and every time.



For example, the brass rails required rabbets to fit into one another at the corner joints. This would be trivial with a mill but since I had none, I used brass stock at half the finished thickness requirement and cut the half-segments to proper length before brazing them together and hand fitting/filing the perpendicular pieces until they fit neatly into one another. It ended up taking much more effort and doesn't look as good, but where there's a will, there's a way.






Pretty much every single item is raised off the mounting surface by way of some sort of standoff or spacer. This serves no practical purpose but gives it a more interesting appearance.



Many mundane items were built with special attention to make them interesting in appearance. For example. the grid leak resistor is made up of three units in series for a more compact package. The tank capacitor assembly was stylized to add visual interest, as is the RF bypass capacitor assembly.







Tubes:I settled on using the 810 tube because it's a very robust transmitting triode that's had a history of successful use in the tesla coiling world. It's relatively compact size and narrow diameter makes it a reasonably-sized installation. The graphite plate ensures it's very tough and many people reported running this way over spec with no issues, even with the plate glowing bright red. They're relatively affordable and easy to find and the internal build quality makes it one of the most rugged tubes I've come across. There are several large ceramic support forms inside the tube with numerous reinforcement struts and signifigant glass support at the base. There aren't any wimpy mica supports in this thing! I have seen the larger tubes like the 833 cited as brittle and requiring kid gloves. The 810 utilizes a jumbo 4-pin base which feeds the pins through a metal/ceramic base into a bayonet sleeve socket which securely holds the tube. These sockets are also dirt cheap compared to sockets for 833's or 304TL's. They run on a 10V filament voltage with 4.5A current draw.



Since I decided to go with the steampunk and vintage theme, the decision was made to completely avoid silicon devices. the voltage doubler on the high voltage side was handled with a 3B28 xenon gas rectifier in place of a high voltage diode. This adds complexity to the project but the components still had enough room to fit nicely on the platform. The 3B28 is a drop-in replacement for the 866A mercury rectifier (my first choice) but with the major benefit of double the current handling, giving plenty of operational overhead. These operate at 2.5V with a 5A current draw. The 3B28 come in several flavors. The first one I bought had a mica shield at the top, blocking the blue glow of the tube whilst in operation. Another I purchased did not have this shield and lets an observer watch the colors while it's under load, growing brighter and larger as current increases.


Secondary coil:The secondary coil is wound on a conduit-grade 3.5" PVC tubing, which are designated by a light gray coloring. While coloring is not generally prefered when given a choice, I have seen no harm from color pigments so far. The design called for a completely sealed interior. PVC end caps were fabricated for both ends with provisions to insulate any metallic conductors such as the threaded mounted inserts and the breakout point. It consists of roughly 885 turns of #26AWG standard build magnet wire. The entire coil is baked and then coated several dozen times with polyurethane, resulting in a coating that is roughly .100" thick at the most. The top and bottom inch of the coil itself, with it's spacewound turns, is wrapped with kapton tape on top of the polyurethane coating, resulting in an amber darkening that blends it much closer to the main coil body itself, in addition to extra dielectric strength.

The top end-cap consists of a .250" thick PVC disk with the same OD as the PVC tubing itself. A secondary disk was cut from .250" phenolic sheet which was then epoxied on top of the PVC disk. The wire at the top of the coil is then routed into a recessed channel on the end cap, preventing it from abrasion and damage. The breakout point is a piece of 1/4-20 stainless threaded rod with the top half of the threads removed and the point machined to a dull point (a much more acute point would overheat very quickly and oxidize or melt). This is then fed through a beehive-type ceramic insulator. The magnet wire itself is fed underneath the ceramic insulator and makes electrical connection to the threaded rod via two washer/nut stacks to ensure electrical connectivity and reliability since it cannot be brazed to steel (assuming one can do so with silver braze, the magnet wire probably won't survive the elevated temperatures and oxidize under open flame from a torch)


The base end-cap consists of a .250" thick PVC disk with the same OD as the PVC tubing itself. A secondary disk was cut from .500" PVC sheet with an OD that matched the ID of the 3.5" tubing. These two disks were glued together. Four holes were drilled partially through and four steel 1/4-20 threaded inserts were used. These inserts allow me to mount the barebones secondary coil to a flanged base designed for this particular project, but the modularity allows me to use the coil for other purposes, if I so desired to.


The magnet wire at the base of the coil is routed through a recessed channel on the end cap, preventing it from abrasion and damage. The end is soldered to a 3.25" diameter copper sheet which has an identical four-hole bolt pattern drilled into it to match the bolt pattern of the threaded inserts in the end cap. This disk is then epoxied to the end cap, serving as the terminating junction for the base of the coil.



The base flange is a 5.500" OD .250" thick phenolic disk which serves as the mating part to the secondary coil. This flange has two patterns of bolt holes, one matching that of the secondary's end cap and another larger diameter pattern 45 degrees radially opposed for ceramic standoffs to attach the flange to the deck of the tesla coil. This base also has a copper ground sheet of 3.5" OD (with addition of a tab) which mates to the 3.25" disk on the bottom of the secondary itself when it is mechanically fastened together from underneath using 1/4-20 machine screws into the threaded inserts. An RF ground connection then can be tapped from the tab of the copper plane on the flange to an insulated feedthru directly underneath the deck to a central ground block system.
Wiring:The wiring took the longest out of everything to do. Wiring up the tesla coil took about 20 hours, mainly because I redid multiple connections multiple times in order to get wire bundled routed properly and to the right length, with neat, approvable terminations. All terminals use non-insulated crimps so they had to look presentable and not mangled by a crimping tool. The insulative jacket had to butt up against the crimps within reason and everything needed to look uniform. This was hard with cotton braided wiring because the cotton tends to fray if not stripped perfectly.


I'm using old techniques of running bundles and includes the "lost art" of cable lacing with waxed twine, which is the traditional lacing material. Cable lacing utilizes a single piece of waxed silk or cotton (nylon or similar for modernists) twine which is half-hitched (or similar running knotwork) along the length of a bundle, essentially locking wires together into a monolithic while retaining flexibility and visibility. It's main purpose was making it easy to trace, keeping the individual wires in the bundle parallel throughout the run. This technique was used heavily in avionics, telcom, and maritime wiring before the advent of zipties and it's still used today, though to a much lesser degree due to labor involved. It's mostly seen in spot tying bundles, not a full lacing job. It covers less of the wire (giving higher visibility), is less abrasive on jackets, and does not deform the jackets as much as zipties. Zipties form a circular bundle. If its too tight, it'll deform the insulative jackets. If it's too loose, individual wires can shift in the bundle, leading to difficulty in tracing runs. With cable lacing, you can lash together round, square, or any shape bundle with great security. The wax lets it grip very well so once laced up, it's very solid. It also looks darn cool!



Control Panel:The control panel is made with a piece of antique, solid brass kickplate from a demolished school. It was relatively soft annealed material so working with it was simple and straightforward. Layouts were dykemed and scribed, and holes, radii, and bends were made. The panel meter holes were done with a "fly cutter" on a drill press. A stepped sheet metal drill was used for all panel holes to minimize burrs. Bends were made with the high tech method of clamping two bars of metal and pounding the bend in with a rubber mallet, and fixing and mishapen parts with more application of rubber mallet against the panel on a flat surface.


One of the last steps was letter punching. I don't have access to an engraver and it would be unbecoming of a project like this, so I resorted to a brass ball peen hammer and some handheld letter punches to stamp out some labels. The control panel has a 7.5A variable autotransformer to control line voltage to the triode plate. There is a master switch labeled "filament" in which turning this off kills all power. Turning this on will juice the filaments only. The slave switch "power" turns on power to the grid itself. A neat looking panel-mounted 3AG fuse holder is used at the bottom near the power input. Up top are two neon indicator lights for filament and power, and the two miniature panel meters monitor line voltage and line current draw. They don't have meters of this diameter (2.5") that come in other useful configurations. Ideally I'd have one to monitor filament voltages but it's fun to crank the variac and make the voltmeter climb!


With the triode assembly dominating the left quadrant, the control panel balances it by dominating the right quadrant. This gives it an asymmetrical look, which was what I as after. The photos below show what the tesla coil looked like about two weeks back. Progress is much further now but I haven't had a chance to upload photographs.



Current specifications of the coil itself:
Secondary coil wire: XXXX turns of 26awg single build magnet wire, dozen layers of polyurethane
Secondary coilform: 3.5" gray PVC conduit, dessicated internal volume sealed with end caps.
Primary coil: 30 turns of 14awg cotton braided, lacquered stranded wire, base winding level with secondary base winding
Primary coilform: 6.275"OD x 12"L sewer/drain rated PVC pipe (not SCH40/80)
Tank capacitor: 1nF 80kV, two 2nF 40kV TDK XXXXXXX RF rated pulse doorknob capacitors in series.
RF Bypass capacitor: 10.6nF 15kV, two 5300pF 15kV Murata RF rated doorknob capacitors in parallel
Voltage doubler capacitor: 2.06uF 2.2kVAC, two 1.03uF 2.2kVAC microwave oven capacitors in parallel
grid leak capacitor: 700pF 8kV mica transmitting
grid leak resistor: three variable resistors in series (set at 3kohm, max of 9kohm)
Voltage doubler rectification: Cetron 3B28 high voltage xenon gas rectifier
High voltage transformer: Samsung 1kW ~2.1kV microwave oven transformer
Variable autotramsformer: Superior Electric Powerstat 7.5A, 0-140VAC
Monitoring: Simpson 2.5"OD 0-150VAC voltmeter, Simpson 2.5"OD 9-15A AC ammeter
Indicators: NOS vintage neon indicator packages w/ integral current limiting resistor.
The entire collection of photos can be viewed here. There will be photographic updates as I go on as well as photos documenting other projects (which will have a simultaneous project thread running with it):

Re: The Tesla Thermionic Valve Wireless Energy Transmitting Apparatus
uzzors2k, Sat May 09 2009, 03:04PM
Awesome. Just awesome. You've definitely captured the steampunk look. When did you start working at it?
Re:
The Tesla Thermionic Valve Wireless Energy Transmitting Apparatus
J. Aaron Holmes, Sat May 09 2009, 03:17PM
Awesome stuff, especially the panel and wiring. The look reminds me a bit of some of my 1920's Leeds and Northrup test gear. Very slick! You and Dr. Plexiglass

have both ends of the spectrum firmly covered now! When I was contemplating a VTTC, the idea of using a rectifier tube occurred to me as a cool thing to do, so I can't wait to see how it works for you. As it seems you're not far away, let me know if you come into the need for replacements, since I've got NOS mercury and gas rectifiers (3B28's and 866's) coming out my ears! Got them all for free, so I don't mind giving them away for, say, a first-hand look at your coil running?
Can't wait to see some sparks!

Cheers,
Aaron, N7OE
Re: The Tesla Thermionic Valve Wireless Energy Transmitting Apparatus
101111, Sat May 09 2009, 03:45PM
This might just become one of the best looking tesla coils there is.
Re:
The Tesla Thermionic Valve Wireless Energy Transmitting Apparatus
Dalus, Sat May 09 2009, 08:31PM
It's the best looking VTTC ever for sure

Love the style. Though I'm curious to see what you plan to do with the reciever coil.
Re: The Tesla Thermionic Valve Wireless Energy Transmitting Apparatus
..., Sat May 09 2009, 08:36PM
Holy crap that coil is insane! Can't wait to see it finished!
Re: The Tesla Thermionic Valve Wireless Energy Transmitting Apparatus
aonomus, Sat May 09 2009, 11:48PM
That is a work of art... I have to ask where did you even find all the ceramic insulators and cloth covered wire?
Re: The Tesla Thermionic Valve Wireless Energy Transmitting Apparatus
Myke, Sun May 10 2009, 12:45AM
Wow. I really like the style of wiring. Reminds me of the old styles of construction they used for tube instruments. It looks really pretty and has that nice vintage look to it.
Re:
The Tesla Thermionic Valve Wireless Energy Transmitting Apparatus
Cesiumsponge, Sun May 10 2009, 02:30AM
Thank you for the kind comments so far. If anyone sees something worth criticizing, please don't hesistate to bring it up. I've been working on this tesla coil for about 2-3 months now. The original design work was done about the beginning of this year when my workload dropped and I had excess free time.
I have a bunch of ceramic insulators that I've scrounged and sniped on ebay for several months so it wasn't any particularly lucky find. It just took a lot of work and diligence (and frustration). Sorry if I sniped any of you folks in the process on ebay :) You can also get some free samples from
Keystone Electronics Corp but please don't abuse it if you use that route. Companies have a tendency to start shutting down or nerfing sampling services when a ton of people max them out. Worst case scenario is buying from a place like Surplus Sales or similar. I've done this a couple times when it was an oddball size I couldn't find.
The cloth wiring is brand new production wiring with a modern PVC dielectric jacket so I wouldn't have to worry if the insulation was cracked, worn, or dirty. I purchase from
Rhode Island Wiring. You can buy by-the-foot with a 10' minimum. This is basically the only place that'll do this. Every other wiring supply house wants you to buy 500' spools because cloth wiring isn't a normal item. Rhode Island Wiring specializes in reproduction cloth wiring and literally have hundreds of combinations in multiple gauges. The power cable wiring was purchased from this
ebay seller before I found RI Wire.
I took a few more pictures to update it a little with all the cable bundling that wasn't shown on the previous images. It looks like the insulation in some places pulled back from the terminals after I bundled and wired it up. I'll have to redo them since exposed copper strands look ugly. I don't really want to replace the wire and re-wrap everything. I don't think tugging on the insulation will help in the long run either since it might shrink again. I don't think I left much excess to cut off the terminal and solder on a new one. We'll see.






Anode cap of the 3B28 sticking through a hole in the upper deck. Two feedthrus--one which is the HV feed from the transformer/doubler and the other leads back down to the lower deck to the RF bypass capacitor assembly. The anode cap also has the last lead feeding the tank capacitor assembly.

Bakelite case, mica capacitor. Rated to 700pF 3kV for the grid leak capacitor unit. I replaced all the steel or nickel-plated hardware with brass.

Two sets of ceramic standoffs arranged in a circular pattern. The larger inner pattern provides the four mounts that attach to the phenolic secondary flange. The short feedthru with the copper bus is the RF ground point which feeds through to the lower deck and connects to the protruding tab on the secondary flange ground plane.

Here is a close-up of the feedthru to ground the secondary coil. It's just a piece of copper strap bent to a U-shape.

Re: The Tesla Thermionic Valve Wireless Energy Transmitting Apparatus
Firefox, Sun May 10 2009, 04:51AM
If you're having trouble with nasty looking ends, try using a rope whipping technique to tidy up the ends with some of your twine. Though you may have to undo some of your lacing to get at the affected wires, I imagine. I am enjoying looking at the pictures of the build (and thank you for not using imageshack).
Is that ball going to be sitting on top of your breakout point all the time, or are you going to take it off/put it on when you feel like it? Also, can the mechanical contacts hold up to the RF power passing thorough them, or might they get corona on those surfaces?
Re: The Tesla Thermionic Valve Wireless Energy Transmitting Apparatus
Dalus, Sun May 10 2009, 12:43PM
A copper/brass cover for your MOT would make it even nicer. Though it might get hot.
Re:
The Tesla Thermionic Valve Wireless Energy Transmitting Apparatus
Mads Barnkob, Sun May 10 2009, 04:39PM
Its looking great Cesiumsponge!
The amount of dedication to your theme is overwhelming :)
Dalus wrote ...
A copper/brass cover for your MOT would make it even nicer. Though it might get hot.
or simply paint it black, thats what I did with the mot/moc in my vttc, looks good.
Re:
The Tesla Thermionic Valve Wireless Energy Transmitting Apparatus
Renesis, Sun May 10 2009, 08:08PM
or simply paint it black, thats what I did with the mot/moc in my vttc, looks good.
I know this is going to make me look like an idiot, but how about electroplating the core with brass or copper? Would that affect the performance of the MOT? It sure would look great.
Cesiumsponge, i havent commented your project yet. What a stunning tesla coil! I love the old style cable lashing, and the choice of materials. I tend to prefer the more modern look, but this has definately caught my attention. Your attention to detail is beyond anything i have ever seen. I cant wait to see it finished.
Edit: What CAD program are you using?
Re:
The Tesla Thermionic Valve Wireless Energy Transmitting Apparatus
Dr. Drone, Mon May 11 2009, 04:34AM

Re: The Tesla Thermionic Valve Wireless Energy Transmitting Apparatus
Hazmatt_(The Underdog), Mon May 11 2009, 08:47AM
It's looking really good. I would have heatshrunk the crimp lugs to finish off the wire/lug connection with a clean look, but that's just me.
> you don't plate a transformer core. Laminations are electrically isolated with a layer of varnish and are carefully treated so as to reduce eddy currents. If the core were allowed to conduct to each adjoining lamination, enormous currents would build in the core and cause tremendous power loss and quite a bit of heating.
Re: The Tesla Thermionic Valve Wireless Energy Transmitting Apparatus
Dalus, Mon May 11 2009, 11:54AM
He could take the MOT completely apart. Clean the varnish of then electroplate it put new varnish on there and reassemble it. Though I have a feeling this would be to much work even for Cesiumsponge.
Re:
The Tesla Thermionic Valve Wireless Energy Transmitting Apparatus
Dr. Dark Current, Mon May 11 2009, 01:31PM
Dalus wrote ...
He could take the MOT completely apart. Clean the varnish of then electroplate it put new varnish on there and reassemble it. Though I have a feeling this would be to much work even for Cesiumsponge.
That would not work, clear the varnish and electroplate EVERY lamination? They are welded together. Or just the core? That would short it out anyways. And the magnetising current of a re-assembled MOT is always monstrous.
By the way, amazing work Cesiumsponge.
Re: The Tesla Thermionic Valve Wireless Energy Transmitting Apparatus
Dalus, Mon May 11 2009, 01:51PM
I've seen cores that aren't welded together. It will be a lot of work to strip the varnish of then plate every lamination and revarnish them. Don't know about how much the magnetizing currents would increase not a lot when the core gets put together nicely I guess.
From a practical standpoint it would be a lot simpler to make a housing from a few brass/copper plates.
Re:
The Tesla Thermionic Valve Wireless Energy Transmitting Apparatus
Cesiumsponge, Wed May 13 2009, 02:33AM
Firefox wrote ...
If you're having trouble with nasty looking ends, try using a rope whipping technique to tidy up the ends with some of your twine. Though you may have to undo some of your lacing to get at the affected wires, I imagine.
Is that ball going to be sitting on top of your breakout point all the time, or are you going to take it off/put it on when you feel like it? Also, can the mechanical contacts hold up to the RF power passing thorough them, or might they get corona on those surfaces?
I think it would look quite odd too for my tastes. I redid most of the offending terminals and redid the entire cable lacing job, this time switching to proper cable lacing material. What I used before was a waxed twine, which does work fine, but the proper cable lacing material almost like dental floss, but more waxy and no minty. It was good practice.
As far as the breakout point, I just put the ball on there because it was handy for the photo and I didn't want to jab myself with the sharp breakout point underneath. Which mechanical contacts are you referring to? If something is going to create an electric potential high enough to ionize air, the method of contact wouldn't change anything, unless it was such a poor mechanical contact that it established an arc.
On the MOT:
I once considered doing a brass casing or a gloss black sheet metal case to cover the transformer, much like a tube audio amplifier. However I thought twice and dropped the idea because the premise behind the steampunk aesthetic is to have the guts exposed, to show the mechanical goodness of what's underneath, all the wires, gears, and stuff you normally don't see. Keeping that in mind, I ended up lacquering the MOT a bit to protect it from corrosion. One of the filament transformers is a vintage Stancor so it already looked old with it's coat of shellac or lacquer. The other was a new Magnetek transformer. I actually lacquered it like crazy to give it an off-brown lacquered look as well. The transformers look like transformers as a result, and I just dolled them up a bit to make them look somewhat aged.
[quote]
Outstanding work sir!
One little suggestion that may save a tear down the road is to ensure all connections to the tube are floating (Plate, grid and filaments) as once tube heats up things move and you do not want to hear a tink! This is good as plate cap can float on wire @ 
Spark On,
ChThe plate and grid connections actually look a -lot- more rigid than they really are. The bus wire I used has a fair amount of flex and the connections from the tank cap and plate cap are both bolted to the solder tabs on the resistor, which is pretty flimsy. I believe it should be fine with expansion of the glass envelope. I'm fairly certain moving the coil around for transport introduces much more twisting and flex than what the tube will see in stationary operation. I also have some split lock washers on the thumbnuts used on the choke so the connections at the resistor tabs can swivel a bit as I didn't torque the sucker so much that the split rings are completely flattened.
Ironically, on my original 810 VTTC, the plate cap wire actually nearly broke off at the tank cap terminal because the wire was so stiff that after repeated actions of taking off and popping on the plate cap, the wire strands finally broke one by one until it was just hanging there. It was some 20kv+ high voltage wire with hard insulation (not like that flexible silicone GTO wire).
I will keep this in mind though. I've had the filament warming for about an hour and I had no issues, but I do have a couple extra tubes. I am fairly confident on the toughness of these tubes.
The one currently being used is actually my beater tube. I had to use a torch to remove the silver solder on end of the grid cap once. The ceramic spacer piece had the ceramic-glass glue joint break loose, leaving the terminal jiggly since it was only attached to the invar feedthru, which could forseeably lead to the ceramic spacer scraping the glue clean off the glass, then eventually scoring the glass, causing it to fail down the road. I glued it back and re-silver brazed it back on. The cap was a dull cherry red from the heat and I had to use scotchbrite afterwards to clean up the oxidation. These things are pretty tough!
Dr. Kilovolt wrote ...
They are welded.
Yep, mine happens to be welded too. Not just a cheesy tack weld, but two parallel beads down the bottom and two more at the top perpendicular to the laminations. I couldn't seperate the laminations unless I took an end mill and machined a big groove to remove each weld.
Had stuff to do this weekend so I didn't touch the coil at all. I am also planning a dual 810 VTTC in a similar style and got a handful of canister-type mica transmitting caps in the mail, and waiting for my variable vacuum cap (didn't come yet D: ) so I have been sidetracked. I did manage to work on the ground connections today. Ran most of the wires and roughed in the bundles as I want them to break out nice and even to the ground block, as well as fabricated half of the grounding block and tapped the holes (copper is gummy!) This project is fairly simple as far as wiring goes too and its a burden to cleanly route stuff and lace it up. I think I might shoot myself in the face if I had to do cable lacing on something much more complex like Dr. Spark's Quadzilla with all his monitoring and control circuitry.
As long as I put in at least a couple hours a day, this thing should progress fairly quickly. Wiring and the primary are basically the only things left. Now that it's near completion, I've slowed down my pace a bit to smell the roses.
Re:
The Tesla Thermionic Valve Wireless Energy Transmitting Apparatus
Steve Conner, Wed May 13 2009, 08:38AM
CS, this is beautiful!

I can't believe you even made a vintage-looking line cord. Where did you get a brown IEC connector, or did you paint one? Anyway, I can't wait to see it working!
Re: The Tesla Thermionic Valve Wireless Energy Transmitting Apparatus
Sulaiman, Wed May 13 2009, 11:10AM
Very nice looking project!
Hope it works out as well as you hope.
Good luck !
Re: The Tesla Thermionic Valve Wireless Energy Transmitting Apparatus
Sparrow338, Wed May 13 2009, 11:21PM
Wow! That is incredible work, the steampunk style is awesome. Great attention to detail, looks beautiful, can't wait to see it finished.
I love that spacer you made to go between the two 40kv doorknob caps. I'll have to give that a try sometime, looks just like you ran it on a lathe.
I have a question for you; where are you getting all the brass hardware? Epically those ball screw "end-caps."
-Sparrow
Re:
The Tesla Thermionic Valve Wireless Energy Transmitting Apparatus
Cesiumsponge, Thu May 14 2009, 12:23AM
I painted the IEC connector. I would absolutely kill for a real brown one! I tried hard but couldn't find anything like it. The brown krylon I used isn't holding up well so I'll have to look for something else. I guess the plastic is kind of oily or something. Making the mains cord was fun.
The brass spheres are pre-tapped and threaded units I buy from
toolsupply on ebay.
Brass hardware like nuts and bolts are purchased at Home Depot in small quantities but I feed off large purchases at McMaster Carr. It is actually cheaper to buy in 100pc bulk at McMaster than the nickel/dime bags at the local hardware store, but it requires a larger financial investment up front. I bought my threaded thumbscrews, brass and copper washers, and some bolts through McMaster. Since I don't know what length I need, I ended up buying longer bolts and cutting down the length to what I need. Cheaper than buying multiple boxes in 1/4" increments.
I got the larger diameter "end caps" came from an insanely expensive internet store called Grand Brass Lamp Parts. I would
never buy there again (shipping was $20 on top of the insane prices. I think my order ended up being $60 for 8pcs plus the adapters). No other stores had what I need though and a redesign would require changing the diameter of the standoffs that make the pillars (which would be even more expensive). If I had a lathe...this would all be much easier/cheaper!
Re: The Tesla Thermionic Valve Wireless Energy Transmitting Apparatus
aonomus, Thu May 14 2009, 07:57AM
Cesiumsponge:
Try taking a new clean IEC connector and using vinyl dye instead. Its like spray paint but its meant for plastics.
- Take a new clean connector, dump it in isopropyl alcohol to clean it, let it dry. (and handle with gloves from this point onwards)
- Hang the connector by one of the solder tabs, mask off all the metal parts
- Spray, dry, check for any thin/uncoated portions, recoat if neccessary
- Dry and bake if neccessary (depending on the vinyl dye instructions, it might take a while for it to fully dry).
Re:
The Tesla Thermionic Valve Wireless Energy Transmitting Apparatus
Cesiumsponge, Mon May 18 2009, 03:12AM
A small update. There are a lot more fine details but I have been getting lazy and tired due to the warm weather and life in general. I'm nearing the end of this project and I have a four-day weekend coming up and I intend to do most, if not all the remaining work then.
I wired up most of my ground wire runs into bundles but haven't photographed them yet since I need to take apart the top deck to get good photos. I need to finalize terminations and then cable lace them together. Every other bit of wiring is done other than that and the primary/feedback coil is in place, including installation of all feedthroughs.
I finished my grid leak resistor assembly today. The design changed quite a bit from the initial inception and it got overly complex for the sake of aesthetic steampunky goodness but it has been completed and mounted. It is comprised of over 50 individual pieces.


It consists of three 0-3kohm variable resistors set in series. It's currently set at 1kohm each, giving 3kohm total, the same value I used for my previous coil. Each is rated at 50W dissipation and will be sufficient. The variability will give me flexibility in testing grid leak values.
They are sandwiched together with two pieces of brass, insulated with a phenolic spacer. The needlessly complex bracket is in place so that I can visually "wrap" the grid leak resistor around the curvature of the primary coil. The two bracket assemblies pivot at the axis through the resistor on either end and is tensioned with the knurled thumbnut up top. Each bracket is attached at the base of the assembly into the deck. I used copper bus material as my brackets and phenolic to tie the top and bottom brackets together. I used plenty of tapped brass spheres and knurled thumbscrews to continue the theme.
The mica cap seen in the photo next to it is the grid leak capacitor I will parallel with the resistor assembly to form the grid leak network.
aonomus wrote ...
Cesiumsponge:
Try taking a new clean IEC connector and using vinyl dye instead. Its like spray paint but its meant for plastics.
- Take a new clean connector, dump it in isopropyl alcohol to clean it, let it dry. (and handle with gloves from this point onwards)
- Hang the connector by one of the solder tabs, mask off all the metal parts
- Spray, dry, check for any thin/uncoated portions, recoat if neccessary
- Dry and bake if neccessary (depending on the vinyl dye instructions, it might take a while for it to fully dry).
How well does dye show up on a black plastic? Doesn't it require bleaching first?
Re:
The Tesla Thermionic Valve Wireless Energy Transmitting Apparatus
Cesiumsponge, Mon Jun 01 2009, 07:52AM
I finally had first light. I made a terrible assumption that the rectifier tube's symbol =(> |)--- is the same as the symbol for a diode -->|--. I assumed that the diode's schematic representation evolved from the tube rectifier symbol so they were identical. No, the cathode ended up being anode and anode was cathode. I actually ended up wiring my rectifier in reverse. That'll teach me to make assumptions! I spent some time redoing the wiring and re-lacing all the cables.
Everything except the primary and feedback coils are in their final state of assembly. I got sidetracked once I got first light so I spent the rest of the night tinkering with it instead of taking photos of the progress. I'll take pictures of the coil soon, possibly tomorrow.
Here is the grounding stuff all wired up and bundled, and the dressed-up IEC jack.


I'm going to start a thread on this since I seem to have some questions with proper tuning. Here are a couple of "wild" shots at 100-110VAC input. The sparks have lost linearity of the stereotypical "sword-like" appearance and branch out in an unpredictable manner. They're also quite hot. The linearity and sword-like appearance reappears once the voltage is turned down. I can't keep it running like this without having the plate start to get cherry red, though it can run indefinitely around 85-90V without any noticeable plate glow. They're right around 17" or so to a grounded sheet above the coil.



This looks to be the Fres, roughly 389kHz.

70VAC, 3A draw. 4.5-5" streamers.

80VAC, 4A draw. 6.5-7" streamers.
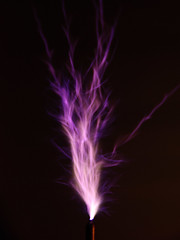
90VAC, 7A draw. 9.5-10" streamers.

100VAC, 11-11.5A draw (needle dances). 15.5-16" streamers

At 105VAC, it'll hit the 17" grounded foil sheet suspended above the breakout point and draw 13-13.5A
Re:
The Tesla Thermionic Valve Wireless Energy Transmitting Apparatus
Myke, Mon Jun 01 2009, 10:58PM
Wow. Nice arcs. I really like how the camera picked up that short of a wavelength. Makes it look really pretty with that violet in there.

*dies from being crushed by the amazing-ness*
Re:
The Tesla Thermionic Valve Wireless Energy Transmitting Apparatus
Cesiumsponge, Tue Jun 02 2009, 12:43AM
The streamer colors vary a bit when captured on camera depending on other ambient lighting. The auto WB is usually fairly good at judging but if there is other lighting nearby, it'll make the streamers look much bluer. I had almost all the lights out when I took the last few images. For example, the first three images I have above are unnaturally bluish because I had a halogen and fluoro light in the shop on which caused the auto WB to shift the hue so the streamers turned out inaccurate in hue.
The primary on there right now just has some household wire making up the primary with lots of tape and ugly slits where I'm using a gator clip to experiment with taps. I ran out of vertical room on my workbench with a variable height grounded strike plate (replaced the suspended foil because it wasn't flat enough to get an accurate reading). About 1" above that is the steel rail that the garage door arm rides on so I tried moving my grounded strike plate out of the way for a direct strike to the garage door opener rail. I successfully made several streamer strikes to it at 120V (roughly one strike every 2-3 seconds) which puts the length at 19.25"!
Except the grid feedback was very unhappy and it arced across a good 6" of PVC primary coilform and ruined the primary coilform so now I can't use it because it'll arc at the slightest provocation. Also the plate was starting to incandesce a dull cherry red, indicating it isn't going to stay cool for much longer so it's definitely not a steramer length achieved under normal operational circumstances. This was at turn 33. I had charted 50-120V measurements from turn 30 to 33 up until my primary coilform crapped out.
I'll have to dig up another length of 6" PVC and prep it as a coilform.
Here is a no-nonsense overview of the coil as it stands right now, and also a picture of the arcover that has halted my process until it is fixed. The primary coilform can be fixed but the feedback coilform is toast...it charred that baby!
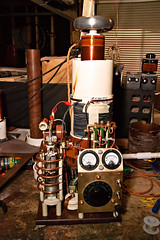

Here is a photo of the bleeder resistors I have for the voltage doubler capacitor bank.

Re:
The Tesla Thermionic Valve Wireless Energy Transmitting Apparatus
Dr. Drone, Tue Jun 02 2009, 01:55AM

Re: The Tesla Thermionic Valve Wireless Energy Transmitting Apparatus
Cesiumsponge, Tue Jun 02 2009, 02:58AM
Hi Chris,
It's magnet wire, but its not my final tickler coil. Its a leftover junker from an old coil so I'm kind of using while I fine tune the coil. For my final coil, I have some insulated braided cloth wire that I'm going to use. Then I'm going to soak the cloth in polyurethane, possibly vacuum suck it so it'll draw the polyurethane into it. Then I'm going to coat it over and over and over with polyurethane to give it better insulation properties.
Then I'll probably stress test it at 140VAC bursts to see if it arcs over. I might have to figure out a way to make a lip on the top of the coilform to discourage it from arcing. I might also try a gradient ring to see if it can make any difference. Given the nature of this build, it wouldn't look correct if I added a plexiglas tube between the primary and secondary for additional insulation value.
I've already noticed many strange things now that I'm paying attention when tuning this thing. How you hook up your feedback coil leads seems to affect it, as well as rotating it on the coilform one way or the other. Even tuning it to Fres with and without the toroid seemed to produce slightly different streamer characteristics. It's very neat indeed and I am sure all this headache up front will pay off when it runs dead reliably!
I haven't tried changing coupling at all yet by moving the primary up or down with respect to the secondary. I might have to try this tomorrow.
Also does running the tickler below the primary seem to make any sense? I tried it temporarily and it seems to work, but I notice almost no one does this. I guess there is no shortage of stuff to explore!
Re: The Tesla Thermionic Valve Wireless Energy Transmitting Apparatus
Dr Hankenstein, Tue Jun 02 2009, 03:04AM
Very nice use of much old gear assembling your coil. Thanks for sharing this with us!
Hank
Re: The Tesla Thermionic Valve Wireless Energy Transmitting Apparatus
Steve Conner, Tue Jun 02 2009, 10:26AM
This is a work of art! :D What's the overall height of it? It's hard to gauge the size.
Re: The Tesla Thermionic Valve Wireless Energy Transmitting Apparatus
Coronafix, Tue Jun 02 2009, 02:06PM
Beautiful work!
Have you been able to get any footage of it yet?
Would love to see it working ! :)
Re:
The Tesla Thermionic Valve Wireless Energy Transmitting Apparatus
Proud Mary, Tue Jun 02 2009, 03:11PM
A wonderful, imaginative, and beautifully realized piece of work.

Re: The Tesla Thermionic Valve Wireless Energy Transmitting Apparatus
Renesis, Tue Jun 02 2009, 09:29PM
It is stunning, even with that ugly bucket and primary. It looks like it was stolen from Tesla's lab with a time machine. I love the fact that even though this coil looks ancient, most parts are new and modern. Steampunk at its best!
Re: The Tesla Thermionic Valve Wireless Energy Transmitting Apparatus
Cesiumsponge, Wed Jun 03 2009, 02:03AM
Thanks for all the kind words! The next few days are supposed to be in the mid to high 80's which is 10-15F above normal. It also means 10-15F above ambient in the garage so I'm going to take a break from working on this thing. I get sluggish when it's over 75F.
Conner, the base pieces are 12x12" pieces of oak. The overall height is just over 31".
Re: The Tesla Thermionic Valve Wireless Energy Transmitting Apparatus
Proud Mary, Wed Jun 03 2009, 08:01AM
An insulation technique for HV wiring in hot places that was very popular in the Thermionic Age was to use thread-on ceramic (porcelain) beads. This does mean that the wire is only insulated to a point, and must be specially routed, but ceramic beads had a role to play on the top caps of big valves where the temperature might exceed 200 Celsius.
Re: The Tesla Thermionic Valve Wireless Energy Transmitting Apparatus
SurfBum96818, Fri Oct 29 2010, 12:08AM
Amazing look ! The amount of detail that has gone into this piece is inspiring! I know you have heard a lot of great things about your project and many people have thanked you for posting it, but I had to personally say thank you ! I work in R& D and so much of the emphasis is on numbers and how small we can make it. I really enjoyed seeing something as esthetically pleasing as this.