Induction heater as an induction launcher (now with control circuit discussion!)
uzzors2k, Tue May 27 2008, 07:10PM
I've been playing with somewhat more powerful induction heater over the last few days, and when attempting to heat various work pieces I noticed I couldn't get a coin to sit still. The coin is 75% copper, 25% nickel, otherwise known as a Norwegian enkroning. It was perched atop a bolt, and when I tuned for resonance it would jump off. I've just made a Rube Goldberg machine!
Video. This shows how much current there is circulating in the work piece!
Anyway now that I got your attention I can ask a quick question. What kind of coupling do I want in an LCLR induction heater? As high as possible? I'm using incredibly low coupling right now and I don't seem to be getting anywhere near the power transfer I expected. At the same time I've found large work pieces damp the work coil current so much that it hardly heats anymore, and with no load the current drawn from the inverter sky-rockets. So will higher coupling damp the resonance so much that it stops heating? Or can I increase the coupling, reduce the matching inductance, and never run it without a work piece anymore?
Re: Induction heater as an induction launcher (now with control circuit discussion!)
GeordieBoy, Thu May 29 2008, 10:02AM
Re The rotation of the workpiece. You ideally want high-coupling between the IH coil and the workpiece. If un-constrained a coil will rotate in such a way that it minimises it's cross-section that couples with the magnetic field lines. Essentially it will stand on edge and stay relatively cool because only a very thin cross-section cuts the field.
As you discovered the power transfer is highly dependant on the coupling factor and the damping that a particular workpiece creates (Q-factor) when inserted into the work coil.
It is unlikely you will find one combination of work-coil and impedance matching components that will allow you to heat a variety of different materials and sizes of workpiece satisfactorily without adjustment! That is why real induction heating setups almost always have the work coil made specifically for the job in hand, and there are hundreds of different coils. Even then they still allow a component in the matching network (such as the L part of L-match network) or a transformer tap to be changed to suit different loadings.
Current draw from the inverter increases when there is no workpiece present because the tank Q tends towards infinity and you must be tracking the resonant frequency. What you really want to do is sense the work-coil current and control the inverter frequency in such a way to keep the work-coil current constant. With this control in place, the work-coil current (and cap current) will not sky-rocket to dangerous levels if the workpiece is removed. Since Q factor increases as the workpiece is removed the actual power supplied by the inverter to maintain a specified work-coil current decreases. If you get the coupling and control right, you can expect the line-current draw to increase noticeably when you insert a workpiece into a previously empty coil.
-Richie,
Re:
Induction heater as an induction launcher (now with control circuit discussion!)
Tonskulus, Thu May 29 2008, 01:18PM
Yes, i have noticed that too. Look at my induction heater video to see some induction launching happening:
http://www.youtube.com/watch?v=iDg4pXpS-Xk Actually, it is possible to levitate some workpieces putting that piece beetween two workcoils. Bottom coil should be a bit larger than top coil.
Re: Induction heater as an induction launcher (now with control circuit discussion!)
uzzors2k, Thu May 29 2008, 02:25PM
It makes sense now Richie, thanks. I've only been monitoring the current drawn from the inverter and forgot that the tank current behaves differently. It would take some fancy control circuit to do constant current control by frequency given how the LCLR responds, I'll have to see about that one. I just wonder how it would behave since once it passes to the wrong side of the frequency hump everything becomes inverted. As long you don't try regulating the current too high, and thus force the circuit to lower the frequency over to the capacitive region it should remain stable I think.
Tonskulus, I saw your video this morning actually. Are you using Kim's circuit?
Re:
Induction heater as an induction launcher (now with control circuit discussion!)
Tonskulus, Thu May 29 2008, 02:49PM
Uzzors wrote ...
Tonskulus, I saw your video this morning actually. Are you using Kim's circuit?
Yes, it is almost like kim's circuit but there are some different solutions anyway. Basic circuit is the same. It seems to be reliable so I don't see any point about making it more complex. My system has also system that keeps input current constant. Like 20Amps or so, what ever I want it to be. It is not active forward converter, it is just automatic L-match adjusting system (Ferrite core is moved by solenoid).
Re: Induction heater as an induction launcher (now with control circuit discussion!)
GeordieBoy, Thu May 29 2008, 02:55PM
Hi Uzzors,
You always want the inverter driving on the high side of the LCLR network's pole frequency (maxiumum power point.) This ensures ZVS of the switches under all load conditions. And ideally at very high power you would like the operating frequency optimised to be somewhere close to this resonant frequency so that the power devices don't have to interrupt too much current. In a rough "one size fits all" DIY design, this won't be the case though.
As it shows on my IH web page, power control can be achieved in many ways. Varying the drive frequency is just one method. (A controlled thyristor bridge to vary the DC bus voltage is another common technique.)
In the variable-frequency case you have two control loops: one that tracks the resonant frequency, and one that controls the power level. The strategy is basically as follows:
Start with a high drive frequency and sweep the drive frequency down until EITHER the requested work coil current is reached _OR_ the resonant frequency of the LCLR network is reached (maximum power point). If the resonant frequency is reached first, and the power throughput at this point is way too low, then the matching inductor or coupling needs to be changed to get more power throughput. Most commercial heaters will indicate this as a tap change required inside the heat station.
If you use a VCO, there are basically too things that can "increase" its running frequency. If the phase angle between tank voltage and inverter voltage is less than 90 degrees, or if the tank current (or tank voltage) is greater than requested. Whichever one of these criteria that dictates the highest operating frequency is the one that wins the battle and takes control of the VCO at that moment.
So for example, if there is no workpiece installed tank circuit Q is very high and the power control loop will push the operating frequency right up to keep the work-coil current under control. As a lossy workpiece is added, the Q-falls. The power control loop will request progressively lower frequencies in order to maintain the requested work-coil current as the Q decreases. Power sourced by the inverter will increase and become more in-phase as the resonant frequency of the LCLR network is approached. Eventually the resonant frequency of the LCLR network is reached by the VCO and the tank circuit voltage lags inverter output voltage by 90 degrees. Adding further load to the workcoil will cause the frequency tracking loop to take over. This will act to keep the VCO operating at the resonant frequency where maximum power is delivered as the properties of the workpiece alter the resonant frequency of the tank circuit. If we quickly remove a lossy workpiece from the workcoil, the power control loop will instantly take control again and the drive frequency will shoot up to stop the tank current going sky high due to excessive Q.
I hope this explanation helps.
-Richie,
Re: Induction heater as an induction launcher (now with control circuit discussion!)
Experimentonomen, Thu May 29 2008, 04:35PM
I had the idea of letting the tank current control a servo motor which would adjust the gap in the matching inductor.
But i never got that far cuz i wrecked the core i intended to use.
Re:
Induction heater as an induction launcher (now with control circuit discussion!)
uzzors2k, Thu May 29 2008, 07:18PM
Tonskulus wrote ...
Yes, it is almost like kim's circuit but there are some different solutions anyway. Basic circuit is the same. It seems to be reliable so I don't see any point about making it more complex. My system has also system that keeps input current constant. Like 20Amps or so, what ever I want it to be. It is not active forward converter, it is just automatic L-match adjusting system (Ferrite core is moved by solenoid).
Mechanical current control?

Have you posted your heater in the projects section yet, or did I miss it?
I've made a preliminary circuit which needs a sanity check. I expect there are flaws in the phase comparator section since I don't quite understand how it works. First the soft start which ensures the VCO starts at max freq. In the meantime the tank voltage rises and is stepped down and averaged, later compared to what the safe value is. Error is feed into the VCO. The phase comparator does what it does...
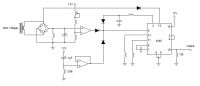
Re: Induction heater as an induction launcher (now with control circuit discussion!)
GeordieBoy, Thu May 29 2008, 10:30PM
Uzzors, conceptually your schematic looks fine - It includes all the important elements. There are a few things that you might need to change though:
1. There should be a pull-down resistor at the VCO control voltage input pin after the point where the control signals are OR'ed together with the signal diodes, (pin 9.)
2. You will also need some kind of pull-down, and possibly and amplifier or clamp on the tank-voltage sense line feeding into the phase comparator (pin 14.)
3. The other input to the phase comparator should come from the inverter output voltage. Without looking at the PLL datasheet i'd guess that it's currently coming from the VCO output instead.
4. You might need some compensation components around the error amplifier that senses and controls peak tank circuit voltage. At the moment the loop gain and bandwidth will be very high so it may oscillate wildly instead of smoothly and quickly settling to the power level you request.
5. The analogue "soft-start" circuit you show might need a diode across the resistor to quickly reset it if you turn the power off and back on again. If you wind up supply voltage slowly with a variac (or have soft-start on the DC bus, you can probably do away with this part, and the over-current detect should be fast enough to catch it anyway.)
6. You might need to buffer the output from the PLL loop-filter to prevent it's response being messed up by the diodes and pull-down resistor that follow the loop filter.
7. You will have to choose the resistors on pins 11 and 12 so the VCO runs over a suitable range. You don't want it to start at a frequency that is too high and damages the power electronics, due to improper gate-drive etc.
At this point I should also say that Steve C has reported good success with a similar (but possibly simpler) PLL based controller for induction heating. However his design is very close (if not identical?) to what he used to control a DRSSTC. In a similar way to current limiting in a DRSSTC it achieves control over induction heating current by turning off the drive for a few cycles when the current gets too high. This may be "closer to home" for those familar with DRSSTC operation and apparently worked well.
-Richie,
Re:
Induction heater as an induction launcher (now with control circuit discussion!)
Steve Conner, Fri May 30 2008, 09:58AM
Yes, I just used one of my Mk2 DRSSTC drivers without any mods. The current limiter provided a kind of rough power control, and a variac did the rest.
The only drawback I found was that the PLL sometimes wouldn't lock by itself when DC bus voltage was applied. It needed a poke at the tuning pot to nudge it into lock. I think this was a Catch-22 situation: if the frequency started far enough away from resonance, it couldn't develop enough tank current to get any feedback signal. I've seen a sweep oscillator used in other applications to break vicious circles like these. It basically flaps the VCO frequency around until it locks.
I also used the series resonant setup, just because I like it more than the LCLR. I don't know how my driver would behave with an LCLR.
Connecting the phase comparator straight to the VCO output is a cheap and nasty shortcut, and I'm to blame for promoting it, since I've always done it in every PLL circuit I've published. The only advantage of it is to avoid the hassle of high-speed isolation circuitry for sensing the inverter output voltage.
I tried making a "bucking coil" like Tonskulus described, and was just able to levitate some pieces of aluminium. I had the current limiter disabled and the variac turned right up to 270V, and it was all going fine until the levitating workpiece melted, went unstable and fell out of the coil. You can probably guess what happened next
Re: Induction heater as an induction launcher (now with control circuit discussion!)
uzzors2k, Fri May 30 2008, 11:18AM
Wouldn't LCLR behave the same as series resonance when we use frequency power control? Running above fres will just increase the inductive reactance.
About the VCO shortcut, how much phase shift is there between the inverter output and VCO anyway? I thought the inverter output would be pretty close to the current VCO frequency, making it suitable. At least when it's only function in this case is insuring that the VCO is never running in the capacitive region. I'll try to keep the tank current large enough that I'll need to run on the inductive side most of the time, so an exact frequency lock on fres isn't necessary.
All I really want from this IH driver is control over the inverter output current, which I'm sort of loosing. I guess I'll either have to settle on constant inverter output control, or constant tank current control. Given that I'm limited to IRFP450s my inverter will be the limiting factor, so maybe inverter current control is best.
Re:
Induction heater as an induction launcher (now with control circuit discussion!)
Experimentonomen, Fri May 30 2008, 02:38PM
GeordieBoy, is this how you mean with the suggested changes ?
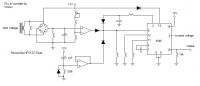
Re: Induction heater as an induction launcher (now with control circuit discussion!)
uzzors2k, Fri May 30 2008, 02:49PM
See my next post.
Re: Induction heater as an induction launcher (now with control circuit discussion!)
Experimentonomen, Fri May 30 2008, 05:57PM
Mebbe i can also experiment with this circuit and see what i can do. Tho i´d also add a tank and inverter current sense so that i can make it also regulate if current go too high.
Re:
Induction heater as an induction launcher (now with control circuit discussion!)
uzzors2k, Fri May 30 2008, 07:19PM
Be my guest, I won't be able to try it right away as is. I drew up most of the schematic now, all that's missing is mosfet drive amplification, which is just two UCC's and a GDT. Inverter current regulation has been added as well. Quite the beast this thing is becoming.
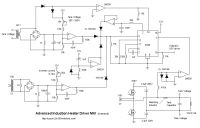
Re: Induction heater as an induction launcher (now with control circuit discussion!)
Experimentonomen, Fri May 30 2008, 07:27PM
But remember when using opamps on single supply, the unused inputs must be referenced to half the supply voltage or connected to the output.
Re:
Induction heater as an induction launcher (now with control circuit discussion!)
GeordieBoy, Sat May 31 2008, 12:20AM
Wouldn't LCLR behave the same as series resonance when we use frequency power control? Running above fres will just increase the inductive reactance.
The LCLR circuit is a third-order resonant network so it has one impedance minimum and one impedance maximum. These are caused by series resonance and parallel resonance respectively, whereas the series resonant tank circuit only has the impedance minimum point caused by the series resonance. Above the maximum power point both networks do present an inceasingly inductive load to the inverter.
About the VCO shortcut, how much phase shift is there between the inverter output and VCO anyway?
I don't know, you tell me! - It depends on the design: Deadtime settings, propagation delay through logic & gate-drive chips, GDT leakage inductance and damping resistance and the switching speed of the power semi's. If the PLL uses the drive signal to the inverter instead of the inverter output voltage as the control variable then it will control the VCO in such a way that the inverter's DRIVE signal is at 90 degrees to the tank voltage instead of the inverter output. The actual inverter output voltage waveform will lag the drive by some time delay and will therefore be less than 90 degrees ahead of the tank voltage. I _think_ that the outcome of doing this is that the inverter sees a slightly capacitive load when tracking resonance. It's a long time since I did this stuff, so you'll have to check the calculations. You might be able to tune out this phase shift by tweaking the PLL phase comparator to make it aim for more than 90 degrees. If it was me i'd just sense the right two waveforms.
I thought the inverter output would be pretty close to the current VCO frequency, making it suitable.
Inverter output frequency is always the same as the drive signal that is controlling the switches. Only the propagation delay (or phase shift) changes with various loadings and operating freqencies.
All I really want from this IH driver is control over the inverter output current, which I'm sort of loosing.
You can build in over-current protection for the inverter if you want, but what you really want to protect for is over-current/over-voltage in the tank circuit. With no workpiece present the tank circuit voltage and circulating current can be pumped up to tremendous values with relatively little power from the inverter because of the high Q-factor.
-Richie,
Re:
Induction heater as an induction launcher (now with control circuit discussion!)
uzzors2k, Sat Jun 14 2008, 03:49PM
Well, it took some time to clear some projects from the waiting list but I've started on the induction heater again. I'm having problems getting the phase angle to lock at 90 degrees. While shifting through the frequency range and scoping the phase comparator output I saw that a little before 90 degrees the output (from the lowpass filter) would peak. On either side it would decrease, and at 90 degrees it was a little lower than the peak value. I'm not sure what causes this, but it seems to be messing with my control circuit. Not only that, but how can the 4046 tell where 90 degrees is if it's neither top nor bottom? The 4046 is locking to the maximum point right now I assume, which is where 90 degrees should be but isn't. The voltage and current regulators are disabled, and I'm running the circuit from low-voltage.
Fresh schematic:
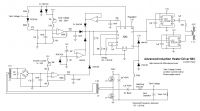
Tuned by hand for 90 degree phase shift, no feedback.
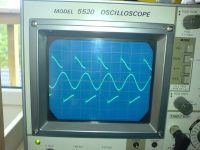
This is where the 4046 locks to when left to do as it pleases. The time div is different than the other scope shot.
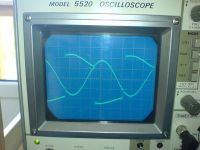
Re: Induction heater as an induction launcher (now with control circuit discussion!)
GeordieBoy, Sat Jun 14 2008, 04:22PM
Eirik what are the two waveforms being scoped in the photos?
It is the inverter output voltage and the tank circuit voltage that should be at 90 degrees to each other at the maximum power point. Both of these waveforms should be "squared up" by the time they arrive at the PLL's phase comparator, so looking at them there should show two squarewaves at the same frequency but in quadrature. The raw output of the phase-comparator should be a squarewave at twice this frequency with a 50:50 duty ratio when the inputs are exactly at 90 degrees. This is the condition that the PLL should lock to. It looks like one of your scope traces might be inverter load current from the fact that it is almost sinusoidal?
Re: Induction heater as an induction launcher (now with control circuit discussion!)
uzzors2k, Sat Jun 14 2008, 04:40PM
Whoops, forgot to mark them. The sine wave is the tank voltage, and the semi-square wave is the inverter output before the matching inductor but after the DC blocking capacitor. No squaring up or other waveform fixture yet.
I did some scoping of the XOR inputs, and the signals are no where near as square as they should be. The inverter voltage is mainly triangle, while the tank voltage is a weak sine wave. The XOR probably doesn't see their duty cycles as being 50%, and thus messes up when comparing phases. I'll fix the feedback and see if that rectifies the situation.
Re: Induction heater as an induction launcher (now with control circuit discussion!)
GeordieBoy, Sat Jun 14 2008, 04:46PM
Agreed. They are supposed to look like two squarewaves at 90 degrees to eachother at f going into the XOR phase comparator. The output of the phase comparator should be a squarewave with 50:50 duty at 2f. And the output of the loop filter should be half the supply voltage plus a small residual triangular ripple at 2f.
Re:
Induction heater as an induction launcher (now with control circuit discussion!)
uzzors2k, Sun Jun 15 2008, 06:45PM
Alright! Prefect and automatic 90 degree phase lockage! After improving the input waveforms I found it acted strangely. When sweeping the frequency down, the XOR output would start at around V/2 and rise to V way before resonance. It would stay at V until I got close to fres, at which point it would decrease to V/2 at fres, and when dropping the frequency further below fres the output dropped to around V/4 or so. Which is exactly backwards of what I need. Hence the additional 180 degree phase shift I planted in. Worked like a charm.
Scoped Inverter output VS Tank voltage again. There is ringing at the inverter squarewave's edges regardless of being in tune or not. It could be caused by numerous things I don't even want to think about. Should I worry about it?
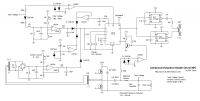
I'm quite satisfied with this circuit now. All that remains is testing the the voltage and current limiting circuits.
Re: Induction heater as an induction launcher (now with control circuit discussion!)
GeordieBoy, Sun Jun 15 2008, 07:09PM
Waveforms look good.
It seems strange to add a common-emitter amplifier to invert the phase when you could have just swapped the inputs over to one of the LM393 comparators?
The HF ringing is probably caused by cross-conduction of the MOSFETs because there should be relatively little load current flowing at the switching instants. How much deadtime do you have in the gate-drive signals?
Re:
Induction heater as an induction launcher (now with control circuit discussion!)
uzzors2k, Sun Jun 15 2008, 08:23PM
GeordieBoy wrote ...
It seems strange to add a common-emitter amplifier to invert the phase when you could have just swapped the inputs over to one of the LM393 comparators?
I tried that first but for some reason the diode clipper behaved strangely, giving a high frequency pulsed output. I narrowed it down to the inverting input being the cause of the problem. Non-ideal components are a pain.
GeordieBoy wrote ...
How much deadtime do you have in the gate-drive signals?
None. The only simple way I can think of to introduce some deadtime is increasing the GDT damping resistance. I'll watch the waveform and if problems occur at higher powers I'll know what may be the cause. I thought GDTs made for shoot-through proof designs?
Oh, and the ringing has become less pronounced since last time I checked. Being in the lash-up phase with long, curly ground leads everywhere makes even the best waveforms look messy.
Re: Induction heater as an induction launcher (now with control circuit discussion!)
GeordieBoy, Sun Jun 15 2008, 11:01PM
In a bridge leg you always want devices to turn-off quicker than they turn-on. Otherwise you get cross-conduction and a shoot-through current flows down the bridge leg at the switching instant. It is this intense but brief current spike that shock excites stray inductance in the supply wiring loop into HF ringing. Once this takes place, that HF ringing will appear on practically every signal in your circuit that you choose to look at with your scope.
You ideally want a small dead-time of 200ns or so where both devices are guaranteed to be off. You can introduce this into the gate-drive signals using RCD circuits before the gate driver ICs. Or using RD slowdown circuits at the MOSFET's gates to slow down turn-on should also be effective.
When operating correctly an LCLR induction heater's current from the inverter is either in phase or very slightly lagging the inverter output voltage. This means that the current at the switching instants is small and slightly inductive. This is the ideal situation for a MOSFET bridge. Under these conditions the output voltage waveform should be relatively free of overshoot and ringing. The rise and fall times can be quite leisurely and the waveform can have noticeably sloping sides when viewed on a scope.
-Richie,
Re: Induction heater as an induction launcher (now with control circuit discussion!)
Marko, Mon Jun 16 2008, 02:00PM
I don't think shoot through is a possible problem, as so many people have built working SSTC's for power levels in kW range without really having any means of providing deadtime, even without the reverse diodes on gate drive circuit which are sometimes used.
mosfets are apparently just too damn fast.
I myself used pre-programmed deadtime but never really saw a benefit. I never observed anything like shoot-through and devices would be cool and ZVS even then (which implies there was still 'enough' deadtime happening).
Re:
Induction heater as an induction launcher (now with control circuit discussion!)
uzzors2k, Wed Jun 18 2008, 04:22PM
While working on tank voltage feedback I've become increasingly aware of the ringing, which like Richie said is on every signal I scope. Even the 12V line! Although I can regulate the tank voltage it seems to be oscillating, ie the scope trace becomes fuzzy so I can only estimate what the tank voltage is. Right now I'm not sure if it's the ringing messing with the feedback or if it's just my control loop.
So I tried to add some dead time to the gate drive signals with a RD circuit at each gate. I think it worked, but the ringing didn't go away.
Inverter output
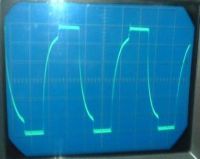
Inverter output and tank voltage
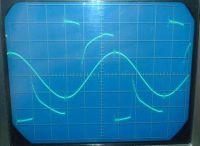
Tank Voltage and 12V line. 12V is AC coupled and at 0.5V div.
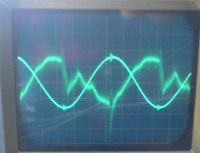
So does anything come to mind? Or is it even worth worrying about? It stays locked in phase well, so I assume the ripple on the supply line isn't affecting the 4046 in anyway.
Re: Induction heater as an induction launcher (now with control circuit discussion!)
Experimentonomen, Wed Jun 18 2008, 06:02PM
Shorten the ground wire on your scope probe!!!
Re: Induction heater as an induction launcher (now with control circuit discussion!)
Experimentonomen, Wed Jun 18 2008, 06:05PM
use a porcelean/steel/graphite crucible and a propane/mapp gas torch, as simple as that.
Re:
Induction heater as an induction launcher (now with control circuit discussion!)
uzzors2k, Wed Jun 18 2008, 06:14PM
That halved the amplitude, but the ripple is still there. I think your other post was meant for a different thread.

Re: Induction heater as an induction launcher (now with control circuit discussion!)
GeordieBoy, Wed Jun 18 2008, 06:15PM
Okay. The top trace at least proves that you can introduce plenty of deadtime into the drive waveforms. The flat tops and bottoms of the inverter output are where the MOSFETs are conducting, and the curved sections in between are where the free-wheeling load current is charging and discharging the MOSFETs output capacitance during the deadtime.
The deadtime in this picture seems to be a rather large percentage of the total switching period, and is probably a little excessive. You only need sufficent to prevent conduction overlap and horrendous ringing on the inverter output voltage. (Notice how the voltage waveform now has no overshoot or ringing.) Do you have snubber capacitors across the MOSFETs??? The reason I ask is that I would have expected the voltage to slew more quickly from rail to rail. If not, then I would guess the tests were done at reduced DC supply voltage or with a very light load current??? At full supply voltage and with plenty of amps flowing the voltage will slew more quickly between rails and you don't need so much deadtime.
As for the 2nd scope trace. I don't have a clue what is happening there! It looks like the conduction time of the MOSFETs is very small again compared with the total period and the deadtime is too large a % of the period.
As for the 3rd scope trace, make sure you have a 10uF tantalum cap and 100nF ceramic capacitor across each gate drive IC right at the pins of the chip. Also make sure that you keep the control electronics well away from the power bits that are carrying high current, and in particular away from the work-coil/capacitor tank circuit. That goes for scope leads too!
I wouldn't worry at all about tiny little wiggles on signal lines at the switching instants, because these can appear just because of the fast gate drive signals. It is big wiggles, overshoot and ringing on the power side you need to erradicate to keep the power semi's happy. It's worth noting that this control scheme you're using is very robust - It takes a whole lot of noise to knock it out of frequency lock. The neat thing about it is that during normal operation the two inputs to the phase comparator from the tank circuit and the inverter output are 90 degrees out of phase. So any noise that appears on one signal resulting from a transition in the other signal does not adversely affect the operation!
Hope this helps,
-Richie,
Re: Induction heater as an induction launcher (now with control circuit discussion!)
uzzors2k, Wed Jun 18 2008, 06:25PM
Yeah, the dead time was a bit excessive and nothing I plan to keep. I just wanted to eliminate the shoot-through suspicion. As you guessed I'm running about 1/10th of full voltage and current. (Just one 1.8µF decoupling cap across the supply, no individual snubbing)
But I guess the ripple is nothing to worry about then. The voltage regulation did work so I'll just keep moving forward as planned. (After some vacation! See you guys in a few weeks)
Re: Induction heater as an induction launcher (now with control circuit discussion!)
uzzors2k, Mon Jul 07 2008, 04:27AM
Why aren't air cored inductors used instead of ferrite cored inductors for the matching inductor? You wouldn't have to worry about saturation, or core heating. More wire is required for a given inductance increasing the resistive losses, but that's the only drawback I can see. What am I missing?
Re: Induction heater as an induction launcher (now with control circuit discussion!)
Experimentonomen, Mon Jul 07 2008, 08:42AM
Because a air core matching inductor cannot be put inside the chassi of the ih, cuz it radiated fields everywhere and can itself induction heat things as well, also it´ll be much larger than a cored one.
Re: Induction heater as an induction launcher (now with control circuit discussion!)
GeordieBoy, Mon Jul 07 2008, 12:31PM
That's basically it. A properly optimised design with gapped ferrite and litz wire will have the lowest total losses (when Cu and core losses are added together) and be more compact than an air cored coil. The leakage field of the gapped ferrite core set will also be more localised to the non-magnetic gap than a large air core inductor which will induce currents into everything around.
-Richie,