coilgun 250v 6800microfarads
Effilcdar, Sun Apr 22 2007, 05:32AM
Hey I have recently built a mid sized coilgun and am having some
recurring sparking problems.
The sparks are mostly between 16 gauge magnet wire and post terminals.
I was wondering if you would have any advice on how to deal with that.
Anyway I will include as much information as I can and would really
appreciate any feedback. First of all my charging circuit is 120 ac to
a variac to a step up transformer to a full wave rectifier through a
switch to the caps. It will give the caps a final charge of about 250
volts. My caps are two 350v 3400microfarad electrolytics wired as a
6800ufd bank. That goes through to a large thyristor and around a 40
turn coil back to the other side of the caps. The thyristor is 2000v
and a couple hundred amp rated(I don't have the specs in front of me).
All the wiring to in the discharge loop is 16awg magnet wire and
soldered to post connections. Anyway almost all the connections have a
problem with sparking intermittently so I would appreciate any
feedback you might have
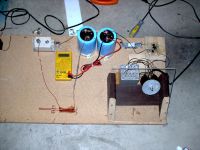
Re: coilgun 250v 6800microfarads
Electroholic, Sun Apr 22 2007, 07:31AM
1 get a freewheel diode in there
2 you will need a lot more turns
3 beef up the wirings, use atleast 12ga with proper mounting lugs.
4 its not clear in the pic, but it looks like youve been trying to solder wires directly to the posts. don;t do that.
btw that looks like a 350a semikron
Re: coilgun 250v 6800microfarads
Effilcdar, Sun Apr 22 2007, 08:00AM
Mabee I misrepresented myself. You seem to asume that I know what I am doing.
1 What is the proper way to attach to these caps
2 what in the world is a freewheel diode, I know of rectifier diodes, photo diodes, diode bridges, LEDs and I have never heard of a freewheel diode.
Mod: merged double post
Hey I just had to tell someone but my project just put its first hole in a pop can. :D
I still have the ocasional spark but no major ones in the past few firings.
By the way that was at about a one foot range.
Mod: I just have to tell you it must be 48 hours between double posts in threads.
Re: coilgun 250v 6800microfarads
Effilcdar, Thu May 03 2007, 02:47AM
Well It looks like this section of the forums is getting pretty dead but I would really apreciate an explination of how a freewheel diode is used. I have managed to get the conections to work reasonably well but I would still be interested in how they would be properly conected.
Re:
coilgun 250v 6800microfarads
Barry, Sat May 05 2007, 03:16AM
Another resource about freewheel diodes is:
Inductive Loads and Diode ProtectionCheers, Barry
Resistors are futile.
Re: coilgun 250v 6800microfarads
rupidust, Sat May 05 2007, 03:17PM
Where exactly do the sparks occur? Sparks happen from cold solder joints, intermittent crimps, and arcs between low and high potential terminals or wires. Its hard to tell from the image but do these steps anyway:
1. Coat the magwire terminals with solder.
2. Make sure a magwire layer is insulated from its opposite end layer (lowest insulated from highest potential).
3. Do not wrap magwire around conductive barrels. If so use good mylar or at least 2 layers of tape around the barrel before wrapping wire. 250+ voltages arcs through magwire insulation like a hot blade through butter. In fact get rid of any conductive barrels period.
4. Attach the prior suggested anti-parallel compulsory diodes.
4. Terminate the magwire properly with ring or spade connectors. Would save you your problems and me my post.
As for performance from that single layer coil, huge cap and metallic barrel, you are on your own.
Re:
coilgun 250v 6800microfarads
Barry, Sat May 05 2007, 06:28PM
Effilcdar wrote ...
The sparks are mostly between 16 gauge magnet wire and post terminals.
The sparks you describe are probably caused by a tiny amount of remaining insulation on the magnet wire. This results in high surge current concentrating into the small area of best contact, causing local heating to blow out tiny bits of molten copper.
When working with magnet wire, it is essential to completely clean the varnish insulation down to the shiny bare copper. It is not good enough to scrape off the coating with a sharp edge. I've had good results with a few square inches of sandpaper, typically 150 or 200 grit. Wrap the sandpaper around the wire and turn-and-pull several times to clean it nicely. Always re-clean the wire if you work on the connection, to remove the copper's surface oxidation.
I like to tightly screw down copper wire directly onto terminal posts, using flat washers to increase the contact's surface area. I also sand the washers and nut to remove corrosion and reduce resistance. Every single milliohm hurts. Although spade lugs are convenient, they do add yet another connection which has resistance and can fail.
By the way, from your picture I see almost as much magnet wire between components as in the coil itself. You will get better results with
much shorter connections, and better yet with very heavy hookup wire. If you don't have copper braid, then stranded automotive hookup wire can be doubled or tripled for good connections. Use solder to tin the ends and crush it firmly under the screw-down terminals.
Good luck!
Barry Resistance is futile, but higher voltage always helps.