Building a ZVS Flyback SGTC
Fiddy, Mon Sept 26 2016, 10:33AM
G'day,
My girlfriend wants to build a tesla coil with me so ive gone about designing and ordering parts, just need a once over by someone more familiar with flyback driven coils than I.
See attached photo, am i in the ball park?
I ran JavaTC and it looks ok to me, I attached the load file to this post, it will resonate at ~500kHz is that acceptable?
Is 5-7 turns on the primary of the flyback ok or should i go higher/lower?
I have bought 10x 3kV 0.1uF caps for the tank, i think 30kV @ 10nF should be ok, 30kV is a bit high i think but can pull capacitors off to lower voltage and gain capacitance yes?
I plan on using 99.5% 3.6mm tungsten electrodes for TIG welders for the spark gap, is 3.6mm too small? should i run a few in parallel?
Anything you could tell me to benefit the output or construction would be great.
Things i have thought about but dont want to play with: I dont want to setup/build a rotary gap. I dont want to use a NST.
Cheers! Mitch.
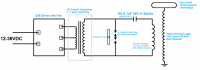
]javatc_load_file.txt[/file]
Re: Building a ZVS Flyback SGTC
Hazmatt_(The Underdog), Tue Sept 27 2016, 01:07AM
1. You're going to use a flyback to drive the primary tank at ~30KV? how do you plan to insulate the primary from arcing over all the time?
2. If you are charging at 30KV, then you have no safety margin for your capacitor for overvoltage
3. Primary tank circuits ringdown at 2X Vin, if charging at 30KV, ringdown is 60KV peak to peak, also insulation breakdown, should be an interesting fire.
4. I'm betting your gap is going to power-arc quite a bit, this will be a problem for optimal performance
5. Your gap will need an excess of 1", that is pretty lossy from an energy standpoint.
6. 10KV is probably more realistic for the gap/energy delivery/capacitor life/corona/insulation issues.
7. You will want an inductor between your charging system and the capacitor if using a typical flyback or the diode might go "poof"
Just some of my thoughts.
Re:
Building a ZVS Flyback SGTC
Fiddy, Tue Sept 27 2016, 04:03AM
Hazmatt_(The Underdog) wrote ...
1. You're going to use a flyback to drive the primary tank at ~30KV? how do you plan to insulate the primary from arcing over all the time?
2. If you are charging at 30KV, then you have no safety margin for your capacitor for overvoltage
3. Primary tank circuits ringdown at 2X Vin, if charging at 30KV, ringdown is 60KV peak to peak, also insulation breakdown, should be an interesting fire.
4. I'm betting your gap is going to power-arc quite a bit, this will be a problem for optimal performance
5. Your gap will need an excess of 1", that is pretty lossy from an energy standpoint.
6. 10KV is probably more realistic for the gap/energy delivery/capacitor life/corona/insulation issues.
7. You will want an inductor between your charging system and the capacitor if using a typical flyback or the diode might go "poof"
Just some of my thoughts.
1. I didnt say i was driving the flyback at 30kV
2. I know this, again I didnt say i was driving the flyback at 30kV, thats just the MMC rating.
3. Again I didnt say i was driving the flyback at 30kV.
4. Going to power arc? what do you mean by this?
5. 1" Gap where did you derive this from?
6. Yes.
7. Why is this inductor needed? and what typical value should it be?
Re:
Building a ZVS Flyback SGTC
hen918, Tue Sept 27 2016, 06:16PM
Fiddy wrote ...
Hazmatt_(The Underdog) wrote ...
...
7. You will want an inductor between your charging system and the capacitor if using a typical flyback or the diode might go "poof"
Just some of my thoughts.
...
7. Why is this inductor needed? and what typical value should it be?
When the spark gap fires, it is going to short out the charging circuit, also there will be large current spikes and high voltage with a horrible looking waveform happening in your primary tank. The rectifying diode will see a lot of that, and it won't like it! an inductor helps smooth out the current spikes that the primary tank produces.
The value will have to be guessed at but I should think you should start with something quite high, maybe in the range 1-10mH +. the only problems with high voltage inductors happen when either they don't do good enough job (the higher the better), or the turn to turn insulation breaks down, when it ends up with lots of voltage across it. To mitigate this, many smaller inductors can be put in series.
The only upside to high voltage inductors is that they don't generally have to have very high current ratings, so a few cheap little ones should do the job.
Disclaimer: I have never built this circuit, so others with more experience with TCs might want to comment :)
Re: Building a ZVS Flyback SGTC
Hazmatt_(The Underdog), Wed Sept 28 2016, 01:24AM
I was thinking closer to 10H, but that's like an impossibility.
1" gap comes from 30kv per inch roughly.
You have to have the gap wide enough that it is not constantly "on", the system has to charge then breakdown causes it to fire when the capacitor is sufficiently charged, hence a wide gap for high voltages. If it is constantly on and not "quenching", just a bbbbzzzzaatttttt and not bang bang bang bang.. then it is power arcing.
Rotary gaps get around this problem because they close and open the gap mechanically, but as you stated, you already know all of this stuff.
You asked for input without specifying enough criteria.
You have not mentioned the arc goal either, so don't fault others when you ask for input.
Tesla coils have some 60 or more variables, so getting your design to fit what you want off of your short list is going to have a lot of input/suggestions and mismatch.
Re:
Building a ZVS Flyback SGTC
Fiddy, Wed Sept 28 2016, 02:04AM
hen918 wrote ...
Fiddy wrote ...
Hazmatt_(The Underdog) wrote ...
...
7. You will want an inductor between your charging system and the capacitor if using a typical flyback or the diode might go "poof"
Just some of my thoughts.
...
7. Why is this inductor needed? and what typical value should it be?
When the spark gap fires, it is going to short out the charging circuit, also there will be large current spikes and high voltage with a horrible looking waveform happening in your primary tank. The rectifying diode will see a lot of that, and it won't like it! an inductor helps smooth out the current spikes that the primary tank produces.
The value will have to be guessed at but I should think you should start with something quite high, maybe in the range 1-10mH +. the only problems with high voltage inductors happen when either they don't do good enough job (the higher the better), or the turn to turn insulation breaks down, when it ends up with lots of voltage across it. To mitigate this, many smaller inductors can be put in series.
The only upside to high voltage inductors is that they don't generally have to have very high current ratings, so a few cheap little ones should do the job.
Disclaimer: I have never built this circuit, so others with more experience with TCs might want to comment :)
I see, ive been looking at richieburnett's website on resonant charging, he has a formula for the calculating the charging inductor value for specified power at specified maximum BPS.
LP = 2xVDC^2 / (pi^2 x Power x BPS)
I get astronomical numbers when i use 240W, 200BPS and 10kV.
Ill have to make some inductors and try, also should i use a De-quing diode aswell?
Re: Building a ZVS Flyback SGTC
Sulaiman, Wed Sept 28 2016, 08:36AM
Fiddy,
Assuming that this girlfriend is a 'keeper',
Have you considered a small 'slayer' type of TC ?
A USB power pack is a sufficient power source
I think that Hazmat was refering to the use of an inductor to isolate the flyback diode from the spark gap / primary resonant circuit transients and oscillations.
richieburnett's website on resonant charging is good,
a good choice for a flyback powered RSGTC
the peak voltage on the primary cap reaches almost 2x the dc eht supply voltage,
so the strain on your flyback/inverter is much less as it provides lower, constant voltage
the dc eht capacitor(s) do not need to be rated for the same current as the primary capacitor,
mylar/pet/MKT/MMKT or any 'poly-' will do.
Yes you should use a de-Q-ing diode for resonant charging
Yes, the required charging inductnce is high.
Re:
Building a ZVS Flyback SGTC
Fiddy, Wed Sept 28 2016, 11:34AM
Sulaiman wrote ...
Fiddy,
Assuming that this girlfriend is a 'keeper',
Have you considered a small 'slayer' type of TC ?
A USB power pack is a sufficient power source
I think that Hazmat was refering to the use of an inductor to isolate the flyback diode from the spark gap / primary resonant circuit transients and oscillations.
richieburnett's website on resonant charging is good,
a good choice for a flyback powered RSGTC
the peak voltage on the primary cap reaches almost 2x the dc eht supply voltage,
so the strain on your flyback/inverter is much less as it provides lower, constant voltage
the dc eht capacitor(s) do not need to be rated for the same current as the primary capacitor,
mylar/pet/MKT/MMKT or any 'poly-' will do.
Yes you should use a de-Q-ing diode for resonant charging
Yes, the required charging inductnce is high.
Yeah id rather not waste my time with slayer or USB units, they dont have enough power for the wow factor. Also girlfriend has studied electronics.
can i use the resonant charging inductor for a static gap coil?
I ordered some 15kV 550mA diodes for the de-Q-ing diode.
I will use a similar sized inductor to that of my secondary, seems to be about 10mH.
Re: Building a ZVS Flyback SGTC
Sulaiman, Wed Sept 28 2016, 12:40PM
A static gap will work using dc resonant charging
but usually will not self-start without help (screwdriver across gap :)
Do not forget to provide airflow in the gap
a fuzzy spark is bad, a thin bright loud spark is required for performance.
Also, the zvs topology makes poor use of ferrite
(because of the resonant current which MUST be much more than the (transformed) output current for true zvs operation)
I would go for flyback mode myself,
preferably using the original primary winding and about 100 to 150 Vdc supply.
For the spark gap I use 3 kV/mm as a rough guide.
Re:
Building a ZVS Flyback SGTC
Fiddy, Wed Sept 28 2016, 12:53PM
Sulaiman wrote ...
A static gap will work using dc resonant charging
but usually will not self-start without help (screwdriver across gap :)
Do not forget to provide airflow in the gap
a fuzzy spark is bad, a thin bright loud spark is required for performance.
Also, the zvs topology makes poor use of ferrite
(because of the resonant current which MUST be much more than the (transformed) output current for true zvs operation)
I would go for flyback mode myself,
preferably using the original primary winding and about 100 to 150 Vdc supply.
For the spark gap I use 3 kV/mm as a rough guide.
hmmm why wouldnt it self start?
Hmmm ill see how i go in continuous mode then maybe goto flyback mode.
sweet thanks for your input!
Re: Building a ZVS Flyback SGTC
Sulaiman, Wed Sept 28 2016, 05:16PM
one more thought;
with a flyback you can trade off peak charging voltage (spark gap setting) vs. b.p.s.
(do not forget the primary capacitor ratings :)
"hmmm why wouldnt it self start?" ..... a clue is in the name ... 'resonant charging'
e.g. for a 10 kV dc supply, the spark gap would be set for 18 - 20 kV
Re: Building a ZVS Flyback SGTC
Fiddy, Thu Sept 29 2016, 12:24AM
fair enough, ill see how i go.
Re: Building a ZVS Flyback SGTC
Benjamin, Thu Sept 29 2016, 12:48AM
I once built a zvs flyback sgtc running on 36 volts with a single static gap and a 7nf mmc and it produced sparks as long as 5 inches. It had no charging inductor, simply the half wave rectified output of the flyback directly across the spark gap.
Re:
Building a ZVS Flyback SGTC
Fiddy, Thu Sept 29 2016, 05:33AM
Benjamin wrote ...
I once built a zvs flyback sgtc running on 36 volts with a single static gap and a 7nf mmc and it produced sparks as long as 5 inches. It had no charging inductor, simply the half wave rectified output of the flyback directly across the spark gap.
Impressive got any pics or vidz?
Re: Building a ZVS Flyback SGTC
Hydron, Thu Sept 29 2016, 10:40AM
Another thought:
You're wanting to reduce the effort of building a rotary gap, which is the standard way to do DC resonant charging as it stops the power arcing problem and allows reliable gap operation and power control
Is it a possibility to turn the driver on and off to stop the power arcing etc, and allow for a smaller gap for more reliable triggering?
- Set the static gap to break down at the right voltage for dumping the tank cap into the primary
- OR trigger the gap somehow
- Turn off the flyback driver when the gap fires, possibly using a photodiode to detect the arc?
- Turn the flyback on again after a delay (at least long enough for the tank to ring down and the gap to quench) to charge the tank cap up for the next pulse
- Can adjust the delay to control the power level.
Just some random musings, never done or looked in detail at any of this myself!
Re: Building a ZVS Flyback SGTC
Benjamin, Thu Sept 29 2016, 05:00PM
No sorry, I don't have any pics or videos but I can try to give you the coil specs because it is dismantled now. It had a 2 by 8 inch toroid and a 2 by 7 inch secondary wound with 30 gauge wire. the primary was about 10 turns of 14 gauge solid bare copper wire in a flat pancake with about 3/8 inch between turns. the spark gap was I think three pieces of 3/4 inch copper pipe evenly spaced parallel to each other. I wouldn't bother with a rotary gap or resonant charging for something this low powered, it's simply not necessary. You can get the same results with a static gap. I have a dual mot coil that makes 5 foot sparks with a half wave doubler, no charging reactor, and a high speed async rsg, and the four microwave diodes right across the spark gap haven't died yet!
Re: Building a ZVS Flyback SGTC
Sulaiman, Thu Sept 29 2016, 05:32PM
some decades ago I had to stay a few weeks with my wife at her mother's house
after the first few days of repairing or scrapping various domestic electrical products
I had time to play with a little 7 kV @200 uA inverter module from a laser printer that I'd scrapped,
In anticipation I had a 4" x 12" c700 turn coil in the car ...
Improvised rolled caps, spoon spark gap, house wiring primary, aluminium cooking pot topload,
no test instruments other than cheap multimeter,
I found that I could easily get c100mm (4") arcs ... with one spark every 3 seconds ..
I later estimated the actual dc input power to be c 0.7 W ... 140 mm/W !
for the small SGTCs that I have built it seems that arcs do not grow from spark to spark
the output spark length is proportional to topload voltage, determined by spark gap voltage
which is in good agreement with John Freau's empirical formula
spark length = 1.7" x SQRT(input power) (60 Hz)
Re:
Building a ZVS Flyback SGTC
Fiddy, Fri Sept 30 2016, 12:46AM
Benjamin wrote ...
No sorry, I don't have any pics or videos but I can try to give you the coil specs because it is dismantled now. It had a 2 by 8 inch toroid and a 2 by 7 inch secondary wound with 30 gauge wire. the primary was about 10 turns of 14 gauge solid bare copper wire in a flat pancake with about 3/8 inch between turns. the spark gap was I think three pieces of 3/4 inch copper pipe evenly spaced parallel to each other. I wouldn't bother with a rotary gap or resonant charging for something this low powered, it's simply not necessary. You can get the same results with a static gap. I have a dual mot coil that makes 5 foot sparks with a half wave doubler, no charging reactor, and a high speed async rsg, and the four microwave diodes right across the spark gap haven't died yet!
Interesting, i might just give it a go without the inductor and diodes first and see the results.
My secondary is similar but with a 4" toroid and smaller 32AWG wire on the secondary.
Thanks for sharing!
Sulaiman wrote ...
some decades ago I had to stay a few weeks with my wife at her mother's house
after the first few days of repairing or scrapping various domestic electrical products
I had time to play with a little 7 kV @200 uA inverter module from a laser printer that I'd scrapped,
In anticipation I had a 4" x 12" c700 turn coil in the car ...
Improvised rolled caps, spoon spark gap, house wiring primary, aluminium cooking pot topload,
no test instruments other than cheap multimeter,
I found that I could easily get c100mm (4") arcs ... with one spark every 3 seconds ..
I later estimated the actual dc input power to be c 0.7 W ... 140 mm/W !
for the small SGTCs that I have built it seems that arcs do not grow from spark to spark
the output spark length is proportional to topload voltage, determined by spark gap voltage
which is in good agreement with John Freau's empirical formula
spark length = 1.7" x SQRT(input power) (60 Hz)
Haha thats pretty good for the input power!
So theoretically a bigger toroid would have a higher breakout voltage but would take longer to charge yeah?
Re: Building a ZVS Flyback SGTC
Sulaiman, Fri Sept 30 2016, 10:00AM
approximately;
most of the energy stored in the primary capacitor (E = 0.5 x C x V^2)
is transfered to the secondary capacitance (coil, topload, extras)
so for a given TC, output voltage is (nearly) proportional to input voltage.
So, with re-tuning, if you increase the topload capacitance the voltage (and frequency) reduce,
so a large topload may require a breakout point
as the topload capacitance is reduced the voltage increases
(for fixed primary capacitance and voltage)
when the voltage exceeds about 3 kV per mm radius, breakout occurs
so the topload radius determines breakout voltage
and the primary capacitor voltage determines maximum voltage with no breakout,
plus
higher frequencies put more strain on the primary capacitor for the same voltage
somewhere above 300 kHz the arcs from TCs become more sword-like at higher power.
P.S. programmes like JavaTC are great,
but with simple electronics rules plus
Wheeler (for inductance) and Medhurst (for capacitance) formulas/tables/graphs
you can get a good estimate of expected performance,
and a greater understanding of/feel for your coil.
If you connect your inverter directly to the spark gap (no inductor etc.)
put a suitably rated resistor of about 10 kOhm in series with the inverter output
Re:
Building a ZVS Flyback SGTC
Fiddy, Mon Oct 03 2016, 07:11PM
Sulaiman wrote ...
approximately;
most of the energy stored in the primary capacitor (E = 0.5 x C x V^2)
is transfered to the secondary capacitance (coil, topload, extras)
so for a given TC, output voltage is (nearly) proportional to input voltage.
So, with re-tuning, if you increase the topload capacitance the voltage (and frequency) reduce,
so a large topload may require a breakout point
as the topload capacitance is reduced the voltage increases
(for fixed primary capacitance and voltage)
when the voltage exceeds about 3 kV per mm radius, breakout occurs
so the topload radius determines breakout voltage
and the primary capacitor voltage determines maximum voltage with no breakout,
plus
higher frequencies put more strain on the primary capacitor for the same voltage
somewhere above 300 kHz the arcs from TCs become more sword-like at higher power.
P.S. programmes like JavaTC are great,
but with simple electronics rules plus
Wheeler (for inductance) and Medhurst (for capacitance) formulas/tables/graphs
you can get a good estimate of expected performance,
and a greater understanding of/feel for your coil.
If you connect your inverter directly to the spark gap (no inductor etc.)
put a suitably rated resistor of about 10 kOhm in series with the inverter output
I see thanks for the information, ive been using javatc for the design of coils for a while now :)