Progress with my lathe.
Ash Small, Wed Jun 17 2015, 08:37PM
I finally lifted the bed of my lathe back onto it's supports today, after being stored in an outbuilding for years and in my drive since last summer. I still need to clean it up, set it all up, bolt on the 'missing bits' (motor, etc).
It was made by Pffeil of London, who produced these during the late 19th century. I believe they went out of business around 1910, so it's well over a hundred years old.
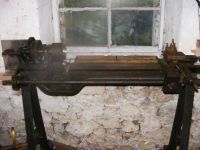
Re:
Progress with my lathe.
Ash Small, Fri Jun 19 2015, 08:51PM
Well, I've cleaned it up a bit, fitted the intermediate drive shaft, and I thought I should sort out some 'proper' switches this time (in the past it's just been plugged into a switched socket).
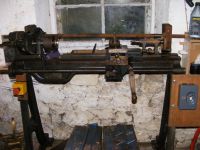
The MEM switchbox comes courtesy of Dr Slack, and I think I've left enough room on the 'switchboard' for coolant pump switch, and maybe a light switch as well. Not sure where I got the 'STOP' button from. A skip in a place I used to work, I think, but I've tested it and it works. Maybe I should fit a warning light to indicate when it's been operated? it seems to be wired for it, or maybe it's wired to operate a relay? There doesn't appear to be a current rating on it, but the terminals look good for more amps than the motor will draw. I figure a relay is just one more thing to go wrong.
Next job is to clean up the motor before I re-fit it and wire everything up. I'll be using the old drive belts initially, as I think I need to strip the headstock to replace the secondary belt. I thought it was going to fall apart 25 years ago, but it just seems to keep going. They don't make them like they used to
The only link I've found on the internet on Pfeil lathes is this one, which shows how the original treddle mechanism would have worked, although the lathe shown is a more basic model than mine.

Re:
Progress with my lathe.
Dr. H., Sat Jun 20 2015, 04:23AM
Hi Ash,
beautiful machine

I am glad you are taking the time to restore it and not throw it for scrap metal (as many nice machines have that fate these days).
Ash Small wrote ...
Next job is to clean up the motor before I re-fit it and wire everything up. I'll be using the old drive belts initially, as I think I need to strip the headstock to replace the secondary belt. I thought it was going to fall apart 25 years ago, but it just seems to keep going. They don't make them like they used to
Amen to that

I can't understand how it is possible with the progress of new materials and manufacturing techniques to be produced such garbage today....
Cheers and keep us posted.
Re:
Progress with my lathe.
Ash Small, Sat Jun 20 2015, 09:58PM
You can say that again, this is seriously over-engineered. I've used it almost exclusively for stainless (tried monel a few times too) and I've really abused it. I did crack a casting once on the gearing for the screw feed (change wheels), I've not got to that bit yet
I've decided, as I need to wire up the switches, to re-wire the motor too (see photo). What I can't decide is whether I should use 'armoured cable' (the stuff with the strands of steel around it), and the appropriate earthed glands. It's not a lot more expensive than the normal stuff.
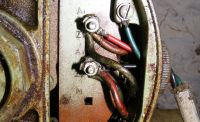
Re: Progress with my lathe.
Hazmatt_(The Underdog), Sun Jun 21 2015, 12:04AM
I'd get a heavier cord on the motor, instead of the Vacuum cleaner cord..hehehe.
And get some proper lugs on the wires there, that guy is a fire hazard.
If you had a 90 degree elbow strain relief exiting the housing you'd be fine.
Re: Progress with my lathe.
Sulaiman, Sun Jun 21 2015, 03:05AM
although i would be inclined towards putting ring crimps, cable supports etc.
my first concern would be the integrity of the insulation of the original wires
which may be (look like) natural rubber, which time, temperature, atmospheric oxygen and OIL tend to degrade.
(plasticised pvc was not invented until 1926, and pvc insulated wires were not in general use until the 1950's)
I would 'megger' at at least 500V the insulation of the wires with respect to the frame.
no point adding excellent external wiring if the internal wiring is 'leaky'
Re: Progress with my lathe.
Ash Small, Sun Jun 21 2015, 12:56PM
Thanks for the feedback I've already removed the 'vacuum cleaner lead' (the reason for taking the photo was as a reference when I re-wire it) and managed to screw a metric plastic compression gland into the old imperial thread (it cut it's own thread in the plastic).
I've not seen my Megger for a decade or so. I assume you are referring to the internal motor wiring, Sulaiman. I'm tempted, at present, to just disturb the internal wiring as little as possible, and make sure the motor is well earthed. I don't want to strip the motor at the moment and replace internal wires, etc. Maybe I'll look for a cheap DMM with 'insulation testing' function? (I will strip the motor if the consensus here is that I should, there are probably some bits of swarf inside anyway)
My current plan is to open up the gland hole to take a 20mm brass gland, and fit some 2.5mm steel re-inforced armoured cable (is it known as 'SWA'?). I also plan to run some four cored armoured cable to the STOP button. It has two switches inside, one that switches 'off' and one that switches 'on' when the button is operated. I plan to use the one that switches 'on' to operate a warning light......Hang on a minute, I only need three core, one 'positive feed', one to the motor, and one to the warning light. .....That will save buying four core as well.
Re: Progress with my lathe.
Hazmatt_(The Underdog), Sun Jun 21 2015, 04:22PM
Is it possible to wire in a reverse switch on that motor? Or do you have a reverse gear on the lathe already?
I have a motor that came with my Atlas and somebody wired in a reverse switch, but I think you have to have access to the field winding... I could check into it when I have some time.
Re: Progress with my lathe.
hen918, Sun Jun 21 2015, 07:21PM
Ash, FYI the extra contacts on Emergency stop buttons are usually used to tell a PLC or other controller that the E-stop is in, but could be used for anything within its current rating. SWA stands for Steel Wire Armoured, however I would go for "SY" cable which is a similar braided, flexible cable designed for just such machines.
Re:
Progress with my lathe.
Ash Small, Sun Jun 21 2015, 07:38PM
Hazmatt_(The Underdog) wrote ...
Is it possible to wire in a reverse switch on that motor? Or do you have a reverse gear on the lathe already?
I have a motor that came with my Atlas and somebody wired in a reverse switch, but I think you have to have access to the field winding... I could check into it when I have some time.
I can reverse the leadscrew using the change wheels. I can't see any reason why I'd need to reverse the chuck rotation, except possibly when using a tailstock die holder, but I usually rotate it by hand when using taps and dies.
EDIT: You do want to reverse the drive if you are cutting a thread in more than one pass, as it enables you to keep the tool synchronised with the thread, so it should be worth implementing a reverse switch if it's simple to do.
EDIT: I've just been reading up on AC motors, and I'm none the wiser really, there are so many different types. If it's a 'universal motor' I'd expect the rotor and stator windings to be in series, but this motor seems to have two parallel windings (or two sets of windings). I suppose I'd have to open it up and post photo's if I want to ascertain what type of motor it is.
Does this tell us anything?
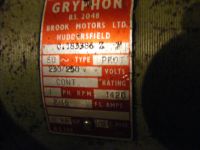
It seems to draw more current than a current Brook Compton capacitor start motor of the same power. 2.3 A comparesd to 1.75A.
A current capacitor run motor draws 1.3A. All motors rotate at the same (nominal)1500RPM. (actual around 1420-1430)
I'm guessing from this that it's probably capacitor start, but I'm only guessing at the moment.
EDIT: Found this, from 1957, which seems to have my motor on it:
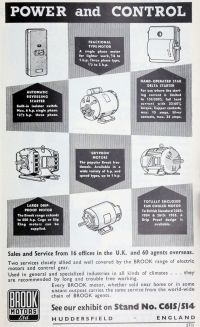
From what I've read, Mine was produced somewhere between 1961, when BS 2048 came in, and 1967, when the company name changed to Brook Victor.
EDIT: I think I found what I needed to know. A1, A2 is the main winding, Z1,Z2 is the start winding, and, if reversed, should reverse the direction of the motor.

It's not obvious which wires are which, though. It will require a bit more investigation tomorrow.
I guess I'm not quite ready to buy the cable, glands and switches yet. I'll have to do a diagram, it's getting more complicated all the time, but I may have a look inside the motor tomorrow.
EDIT: Found this as well

EDIT: This link was useful, looks like the red wires are Z1 and Z2.

It has a centrifugal switch inside for the start winding.
Re: Progress with my lathe.
Ash Small, Wed Jun 24 2015, 02:28PM
Ok, I've been giving this some more consideration, and I've decided an NVR (no volt release) switch is essential, along with a DPDT (double pole, double throw) switch for reversing.
I think I pretty much have everything covered now. I need to ensure that the Stop button triggers the NVR switch to isolate the supply, so that re-setting the stop button doesn't re-connect power to the motor without operating the NVR switch.
Also, the forward/reverse switch MUST be wired in such a way that the NVR switch isolates if the forward/reverse switch is moved to the intermediate 'off' position, to prevent switching from forward to reverse while the motor is rotating.
I think I'm now ready to draw the circuit.
Re:
Progress with my lathe.
Mads Barnkob, Fri Jun 26 2015, 01:23PM
Have you considered using the most widely used concept for motor reversing, self hold and emergency stop/protection relay there is?
I could only find an example in Danish, but the schematics are drawn in english ;)
Use the drop down box to see them at item 2 and 3.

Re:
Progress with my lathe.
Ash Small, Fri Jun 26 2015, 01:52PM
Mads Barnkob wrote ...
Have you considered using the most widely used concept for motor reversing, self hold and emergency stop/protection relay there is?
I could only find an example in Danish, but the schematics are drawn in english ;)
Use the drop down box to see them at item 2 and 3.

I think this is pretty much what I'm doing. I either need a four pole double throw switch, or a single pole double throw switch (ON-OFF-ON) and four double pole relays.
See related thread here:

(From what I can gather, the Danish link you posted depicts a three phase motor, mine is single phase, But I appreciate that the principle is similar)
Re:
Progress with my lathe.
Ash Small, Sat Jun 27 2015, 02:10PM
New information, progress so far:
I've started drawing the motor reverse circuit. I've drawn two four pole relays, but I've been offered some three pole relays by Dr Slack which I suppose I could use if I 'hardwire' the neutral 'motor run' connection, and just use the relays to switch the live 'motor run' connection, and the two 'motor start' connections.
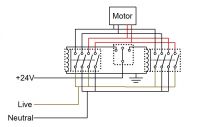
The 'motor start' wires are shown in red on the diagram.
The single pole double throw (on-off-on) switch can only switch one relay in at a time.
Also, yet to be drawn, is the NVR (no volt release) switch, which will 'trip out' if the 'forward/reverse' switch is moved from either the forward or reverse position to the 'off' position, which 'should' ensure that the motor can't be switched from forward to reverse while it is turning.
Any comments at this stage will be appreciated. Obviously the circuit needs fuses, etc, and isn't completed yet.
EDIT: I considered using four of the three pole relays wired as double pole, but I feel just using one relay for both run and start windings would avoid the possibility of only one winding being energized in the event of a relay failure, which can't be good for the motor.
I think, as mentioned above, that hardwiring the neutral 'run' wire, and using the three pole relays to switch the live 'run' wire and the two start wires should work ok.
EDIT: Here's the motor reverse circuit using three pole relays:
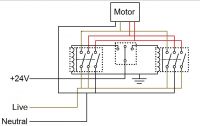
------------------------------------------------
------------------------------
EDIT: I've been googling NVR switches and this one has 'live' and 'neutral' in and out, and has a 'jumper' between 'A1' and '24'. This, I think, means it will only 'cut out' if the supply 'before' it is interrupted. From the look of it, if the power is interrupted 'after' it, it stays on.
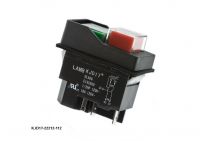
(I think, if I connect A1 to the 'live' feed into the motor, after the relays, and make sure '23' and '24' are the 'neutral' in and out, then it should 'cut out' if the relays are both 'off', even momentarily. It's just a question of getting the 'circuit logic' right.
Re:
Progress with my lathe.
Ash Small, Mon Jun 29 2015, 04:32PM
Ok, I think this is the correct circuit:
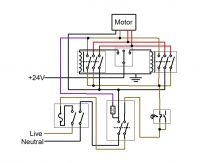
The purple wire connects to terminal 'A1' on the KJD17 NVR switch, pictured above.
The instructions say it should have a jumper to terminal '24' (live out in the schematic), but if it connects directly to the live motor run wire at the motor, it should trip if for any reason, the live feed to the motor is interrupted anywhere before the motor.
If anyone can shed any light on this I'd appreciate it. I've ordered two switches. I'll also try and clean the above post up a bit later.
EDIT: there are still some problems with this circuit, for example, the 'normally open' contact in the 'stop' button won't conduct when closed because the NVR switch will have tripped. I'll sort this later.
Re:
Progress with my lathe.
hen918, Mon Jun 29 2015, 04:39PM
Ash Small wrote ...
Ok, I think this is the correct circuit:
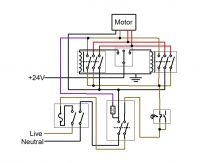
The purple wire connects to terminal 'A1' on the KJD17 NVR switch, pictured above.
The instructions say it should have a jumper to terminal '24' (live out in the schematic), but if it connects directly to the live motor run wire at the motor, it should trip if for any reason, the live feed to the motor is interrupted anywhere before the motor.
If anyone can shed any light on this I'd appreciate it. I've ordered two switches. I'll also try and clean the above post up a bit later.
This one looks right to me, your previous one had the lathe powered through the relay coil of the NVR.
Re:
Progress with my lathe.
Ash Small, Mon Jun 29 2015, 04:46PM
hen918 wrote ...
This one looks right to me, your previous one had the lathe powered through the relay coil of the NVR.
Yes, I've deleted that one now, just to save any confusion. It came about by googling the wrong symbol for an NVR switch. I've used what's actually marked on the switch this time.
I've ordered a three position rotary switch as well for forward/reverse. They should be here by the end of the week.
EDIT: Well, the switches arrived this morning, which is excellent service, but the switches aren't wired as per the photo posted above. These. although the part number is the same, have an internal jumper fitted between A1 and 24. I can use one on my pillar drill, where an external jumper would be fitted here anyway, but they are no good for the lathe circuit as posted above.
I've E-mailed the supplier asking if they have any with a separate A1 terminal.
EDIT: Ok, the supplier, Axeminster tools

does stock a five terminal KJD17 NVR awitch, but it isn't presently listed on their website. The part number is BURT001236 and current price is £14.26, although I'm certain they only charged me £25 inc postage for two.
It was confusing because the four terminal version is on the website, although the accompanying photo shows the five terminal version. I've now pointed this out to them.
Apart from the above confusion, service from Axeminster tools was excellent, and I now have a couple of five terminal NVR switches on the way.
EDIT: They have now updated their website. If you want the five terminal switch you need to quote the above mentioned part number as they only have the four terminal switch on the website.
EDIT: They now have other NVR switches listed with 'four and five terminal versions available'. Looks like they listened. Service was excellent by the way, and they did say to 'contact them if you can't find what you want on the website as they stock some 25,000 items and can't put them all on the website'
Re:
Progress with my lathe.
Ash Small, Wed Jul 01 2015, 08:11PM
Ok, here is pretty much the complete circuit.
There is a revised version of this drawing below I should probably add some appropriate fuses to the 24V system, but apart from that it's looking fairly complete, I think. I'll probably add a few more 'idiot lights', but all the wiring for them will be contained inside the main control box. I think I've accounted for all wires to and from the main control box.
Any further comments at this stage will be appreciated
I'm just collecting everything together so I can work out what dimensions the main control box needs to be.
Re:
Progress with my lathe.
klugesmith, Sun Jul 05 2015, 02:32AM
Nice lathe you got there, Ash. If it hasn't been abused, a man of your talent ought to be able to turn out (NPI) work as large and as nicely finished as with a modern lathe of that size. Just remember to keep those spindle oilers full, turned on when running, and off when done.

Your motor controls are certainly not 19th century. But can you find room for nice-looking start and stop buttons? Like at

or:
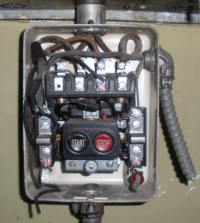
Oops, recent posts show you're way ahead of me there.
Re:
Progress with my lathe.
Ash Small, Sun Jul 05 2015, 03:04AM
klugesmith wrote ...
Nice lathe you got there, Ash. If it hasn't been abused, a man of your talent ought to be able to turn out (NPI) work as large and as nicely finished as with a modern lathe of that size. Just remember to keep those spindle oilers full, turned on when running, and off when done.

This lathe has earned me thousands over the years. Like a lot of lathes from this era, it was fitted with a single phase motor at some point in the '50's or '60's, with a 13 amp 240V plug, when I bought it over 25 years ago and I (guiltily

) never got around to sorting it out properly until now, although I've hardly used it for 15 years or so. (I was predominantly working 'on site', using the client's fitting shop where necessary since my previous premises was demolished to build luxury flats, until I gave up work five years ago.)
It's been in storage for a while but I'm finally getting my shed sorted out, and almost every project I have underway is waiting for this and some of my other equipment to be 'checked over' and gotten operational again.
I always keep an oil can handy to keep the oilers topped up, even though there is some wear in one of the countershafts that can't be adjusted.
I mostly used this lathe for machining stainless components 'slowly'. These 'old lathes' are so over engineered they are ideal for stuff like this. I've also machined monel on it.
Last time it was accurate to ~1/3 thou, but I think I can probably set it up for greater accuracy now (I was young and impatient then). They don't build 'em like they used to.
I could hardly post details on here without sorting out the wiring properly, could I

Re:
Progress with my lathe.
Ash Small, Thu Jul 09 2015, 06:16AM
I'm just drawing up the layout of the main switchbox, and I've decided, now that the circuit has 24 volts as well, it makes more sense to put the emergency stop button in the 24V circuit before the forward/reverse switch.
This would mean the 'stop' button would cut the 24V supply to the relays, which would release, tripping the NVR switch as well, due to the 'A1 (fifth) terminal of the NVR switch being connected to the live 'motor run' feed after the relays.
I should have the relays on Monday, if all goes to plan.
EDIT: Here's the revised circuit diagram, with 24V 'stop' switch, and a first drawing of the layout of the main switchbox.
I'll probably add some fuses to the 24V circuit, and I want to improve the layout a bit before it's finalised.
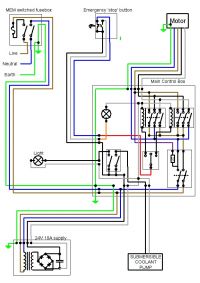
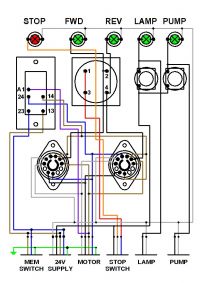
Re:
Progress with my lathe.
Ash Small, Sat Jul 11 2015, 12:35PM
I've now divided the circuit into two. The right hand side below shows the 'front panel' of the main control box, with some terminal blocks mounted on the reverse, and the left hand side below shows the layout inside the box.
It's still 'work in progress', but I know I now need a box around 200mm by 200mm by 75-100mm.
I'll tidy the drawings up a bit more, and I now have most of the components.
I was looking at some plastic enclosures, but I don't think a modern plastic control box is really suitable for this lathe. I'll see what else I can find.
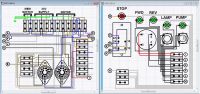
EDIT: just noticed I've not put wires 'L' and 'M' into the laft hand side circuit. It was a late one last night. I'll sort it later.
If anyone can see any other issues, or has any suggestions, I'd appreciate it.
I've still not put any fuses in. I also left out the live run wire from the left hand relay to the motor, I'll add that too.
This is still 'work in progress', the final drawing shouldn't take much longer, though.
Re: Progress with my lathe.
doctor electrons, Sat Jul 11 2015, 01:31PM
I might just be splitting hairs here but here goes. To me it looks like your e-stop circuit would work just fine. That said, typically
when i work on control system designs we would use a safety relay or safety contactor. Your e-stop will drop out the 24v to the
coils on your reversing circuit (which should be electrically or mechanically interlocked). Since your motor is not a 3 phase unit,
it might be better to add a 4 pole contactor with a 24v coil as a "safety relay". 4 normally open contacts, 1 for your 24vdc feed from
the supply (before any devices, excluding your led e-stop indicator and the switch itself) and 2 to break the ac that feeds the reversing setup.
You can add redundancy to the contact blocks on the e-stop button if you chose to but they rarely fail.
The reason i suggest the additional relay is just incase you get a stuck relay in your reversing setup. If you had a brake wire to the
motor you could also use the relay to control that. You would just need the correct contact arrangement on the relay.
That said, what you have, again, should work fine. Where i work overkill is pretty much standard when it comes to safety.
Edit: Give ebay a look for hoffmann enclosures, you can usually find a box and panel pretty cheap!
Re:
Progress with my lathe.
Ash Small, Sat Jul 11 2015, 09:25PM
doctor electrons wrote ...
I might just be splitting hairs here but here goes. To me it looks like your e-stop circuit would work just fine. That said, typically
when i work on control system designs we would use a safety relay or safety contactor. Your e-stop will drop out the 24v to the
coils on your reversing circuit (which should be electrically or mechanically interlocked). Since your motor is not a 3 phase unit,
it might be better to add a 4 pole contactor with a 24v coil as a "safety relay". 4 normally open contacts, 1 for your 24vdc feed from
the supply (before any devices, excluding your led e-stop indicator and the switch itself) and 2 to break the ac that feeds the reversing setup.
You can add redundancy to the contact blocks on the e-stop button if you chose to but they rarely fail.
The reason i suggest the additional relay is just incase you get a stuck relay in your reversing setup. If you had a brake wire to the
motor you could also use the relay to control that. You would just need the correct contact arrangement on the relay.
That said, what you have, again, should work fine. Where i work overkill is pretty much standard when it comes to safety.
Edit: Give ebay a look for hoffmann enclosures, you can usually find a box and panel pretty cheap!
What you are basically saying is I should have another relay 'in series' with the feed to the coils on the other relays, in case a relay sticks, as it's very unlikely that both will fail to open simultaneously?
Seems to make a lot of sense. Another three pole relay, but what happens if the first relay sticks?......nothing happens......I don't quite follow.
What am I missing?......do you mean that just one contact in a three pole relay could stick, and if it was the 'live feed' the motor would stay on, but an additional three pole relay would still kill the motor as long as one set of contacts opened?
EDIT: Wiring up 'idiot lights' to tell you when one contact has stuck, but it's still 'apparently' working ok sounds like a real headache.
EDIT: I did wonder if I needed a relay in the E-stop circuit

Re: Progress with my lathe.
doctor electrons, Sun Jul 12 2015, 01:26PM
Sometimes i do have a little trouble explaining ;) The additional relay would break the dc to the two coils as well as the
motor power to them.
E-stop pressed would kill 24v system wide (except the e-stop circuit) and break the mains feed to the motor. (the feed to both motor relays)
The stuck relay: Where i work one of our standards is to have backup safety for relays or contactors that see a lot of cycles.
The logic is that the more they operate the better the chances of a stuck contact, we have seen it happen quite a few times.
More so with dc circuits as they tend to arc more, but it does happen with ac motors that aren't driven by a vfd.
The number of operations your safety relay would see is going to be incredibly less than the number of operations the motor relays
will see over the life of the machine.
A note on safety relays: Normally a safety relay will be a red color. The contacts inside are different than normal relays, they are whats called
"positive displacement" with most newer high end components like Allen Bradley for example, all of their contactors now come with positive
displacement contacts regardless if they are labeled safety or not.
Normally in our e-stop circuits the e-stop button will drop out the safety relay and require pressing a "control power on" button after the
e-stop button is reset. The control power on button pulls the safety relay back in (or turns it back on). One coil is all that you need to control.
The safety relays will kill power to areas of the machine that would be considered a hazard, such as motors, cylinders, etc. Motion or any operation
that needs to be disabled to render the machine safe. At the same time, using the safety relay in that manner allows you to keep power on
in areas that are not a hazard and would be required for fault handling, like a plc or hmi operator interface.
Hope that makes more sense!
Edit: One relay to rule them all!
Edit: Quote:What am I missing?......do you mean that just one contact in a three pole relay could stick, and if it was the 'live feed' the motor would stay on, but an additional three pole relay would still kill the motor as long as one set of contacts opened?
Yes! As long as the additional relay operates the motor relays could totally fail closed and you would still have a safe condition. Coils can also short,
and cause a failure to open as well as contacts sticking or welding themselves.
Re:
Progress with my lathe.
Ash Small, Sun Jul 12 2015, 07:43PM
I think it makes sense to add a safety relay on the E-stop circuit.
I'm just puzzling over how to add indicator lights to tell me the actual positions of the relay contacts, as there is no power to the contacts ubtil the NVR switch is activated to start the motor.
Maybe I need to use four pole relays instead of the three pole relays depicted, and wire 24V 'on' and 'off' indicator bulbs to the NO and NC contacts?
The only other way I can think of to ascertain whether one relay has 'stuck' would be to switch the direction and power up, and see if the fuse blows.
EDIT: I've decided to include another relay in series with the fwd/rev relays. I'm thinking I can use a three pole relay and use two poles for live and neutral (I only really need to interrupt the live feed, but interrupting the neutral as well gives additional protection, I think.
Releasing either the safety relay or the fwd/rev relays will release the NVR switch. I can't see a reason to have an additional reset button, unless the NVR switch has also stuck closed.
I do have a spare four terminal NVR switch wgich I could place between the safety relay and the main NVR switch. It would then have to be operated before the main NVR switch, thus acting as a 'reset' button, I think. If it was also placed before the 24V power supply feed it would also reset the safety relay, I think.
I'll have to do a drawing, no point trying to explain it
EDIT: Ok, I need the safety relay AFTER the 24V relay, otherwise I can't reset it (pretty obvious really). I can't use one of my spare NVR switches as a 'reset' switch because I need to momentarily apply 24V to the safety relay coil to 'reset' it. The three poles on the safety relay are live, neutral, and the 24V supply to the safety relay coil, so that whae the E-stop button is operated, it cuts the 24V supply to the safety relay, thus releasing it, and once the E-stop button has been reset, you need to momentarily apply 24V to the relay 24V output/coil input to reset the relay. (If it was a 240V relay, you have an NVR switch made from a relay and a 'momentary on' switch).
Now I need to order a suitable switch.
I acquired six relays and three bases earlier today from a fellow 4HV'er, and I think I've found a suitable enclosure on Ebay..
Next job is to redo the circuit diagrams to include the safety relay and reset button.
EDIT: I think I could use a five terminal NVR switch as a 'reset' button if I place the NVR switch first, then the 24V supply, then the safety relay, and then connect the 'A1' terminal to the live output from the safety relay, so the NVR switch can't be switched back on until the E-ston button has been reset. The NVR switch will then act as a reset button for the safety relay, I think. I'll have to draw it.
Re:
Progress with my lathe.
Hazmatt_(The Underdog), Wed Nov 25 2015, 02:48PM
Hey, I just got a lathe too! Now I'm in the club... hahah.
It's similar to yours, but its a post-war model, '57 I believe.
It has a similar drive system, and back-gear for higher torque for harder cuts. You have to make sure to disengage the pin from the bull gear to the main drive pulley when you have the back-gear "in" otherwise the drive train is locked-up, also locking up the drive train is one way to remove the chuck.
This one also uses the rocker tool post, which is hard to setup. You have to be aware of the height and angle at which the tool faces the work. The rocker key under the tool holder gives a fairly wide adjustment range for the tool height, so paying attention to "tool center" is very important.
If you can't face-off a round completely, you will need to re-adjust the cutting tool height a bit higher.
Most of the tooling is HSS and has to be hand-ground, this is because of the tool holder itself. The tool holders have a 16 deg. back-angle, and today's tooling has a 0 degree back-angle, so that has to be factored in, unless you purchase a tool holder with 0 degree back angle, then you need to shim-up your tool holder so it is back on center-line.
I am using a right hand threading/facing ground tool with a straight tool holder and it is working fairly well. Getting setup to cut and cutting properly are a bit daunting for me, this is my second time with a lathe and I'm fairly inexperienced, but youtube helps.
This one is an Atlas TH-54, with the screw cutting quick change gear box, which is pretty neat. I also have a forward/reverse switch, which is probably going to come in handy, and of course it has a lamp cord that needs to be changed out.
Another thousand dollars or so, and it will be fully tooled with sharp bits, quick change tool post, etc. (don't toss the rocker post, but we do both need quick changes so we can use modern tools and inserts)
I also found out that now I need a bench grinder to grind tools and sharpen! That's another setback, but if you're going to use a lathe be prepared to grind tool bits.
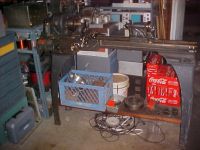
Re:
Progress with my lathe.
Ash Small, Mon Nov 30 2015, 11:06PM
Very nice, HazMatt. I've not made any progress with mine since early July, as the shed ended up getting filled with junk again over the summer.
I think I now have a suitable enclosure for the switchgear, etc. I just need to clear sufficient space in the shed to get back to work on it, although with it now being a day away from December, and not having any heating in the shed, I'm not expecting to have a great deal to report until the spring.
I used the back gear on mine pretty much all the time, for slow cutting stainless steel.
Incidentally, if yours is belt drive (it's difficult to see the drive train in the photo) keep it that way, it's much better to have the belt slip than to have any other mishaps, in my opinion. If the belt slips while cutting it usually means you either need to sharpen the tool, or you're trying to take off too much material in one pass. Give the lathe an easy time

Re: Progress with my lathe.
Hazmatt_(The Underdog), Tue Dec 01 2015, 04:19AM
Oh yea I definitely agree. Most people I know see a belt as detrimental, but I see it as a benefit. Limited slip is a good thing, it prevents over-loading of the machine and a possible explosion when something goes a-miss.
Mine is not flat belt, its more modern V-belt, but like any belt drive it will eventually slip if the load is great enough.
For my Atlas milling machine it has more slip than usual because I had to replace the drive belt with a link belt and they tend to slip quite a bit, which is not really helpful, but it is hard to replace belts on Atlas machines (have to take the spindle apart to do so)
In the meantime, you can read up on sharpening tools and practice for spring. I have to get a grinder now and a 80 grit and 120 grit wheels, so one new toy is forcing me to buy ANOTHER toy.... the saga continues.
Re:
Progress with my lathe.
Ash Small, Tue Dec 01 2015, 10:40PM
You could just get a wheel on an arbour, and put it in the chuck
No need to buy a separate machine, a lathe does pretty much everything.
( A grinding wheel in a drill in a vice (vise) also does the job.)
You don't want to get the tool too hot during grinding.
Re: Progress with my lathe.
tobias, Wed Dec 02 2015, 11:55AM
Ash,
I would not mount a grounding wheel in the lathe. The abrasive dust will get into the rails and other moving parts in the lathe and over time (a long time) it will increase the clearances. If the spindle has a thru hole for material feed I would make a shaft to mount it on the opposite side.
Re: Progress with my lathe.
hen918, Wed Dec 02 2015, 06:56PM
I completely agree with Tobias, grinding dust often ruins slides of a machines designed to do grinding, let alone the slides of a lathe.
I have only seen one lathe - grinder conversion: someone just bolted a big three-phase motor to a table of a old Colchester and turned it into a lethal death machine. Quite apart from the H&S, the lathe was scrap after a few years. (although it was probably scrap before it was converted)
Re:
Progress with my lathe.
klugesmith, Wed Dec 02 2015, 08:15PM
Of course there
are lathe jobs that need a grinding wheel, not in the spindle but as a tool for generating precise surfaces on hard materials. You can grind bearing surfaces to finishes and tolerances so close that the work must cool down before it's measured. Newbies can look up "tool post grinder".

In my experience, exposed surfaces on the lathe are all draped with cloth before any toolpost grinder work.
Like covering a surgical patient before the first incision.
Re:
Progress with my lathe.
Ash Small, Wed Dec 02 2015, 09:43PM
Yes, it is sensible to take a few precautions. I have bolted an angle grinder to the tool post before. I was just pointing out that it is possible to grind tools using the lathe and a wheel if nothing else is available.

Re: Progress with my lathe.
tobias, Thu Dec 03 2015, 11:35AM
I believe I might be too conservative when doing machine work. There are machines specifically designed for surface grinding, and the surface grinding machines allow tolerances unmatched by a lathe tool post grinder. It's mainly due to the deflection of the part and lower tolerances on bearings and slides in the machine. Some surface grinding machines actually have a "support wheel" on the opposite side of the grinding wheel that both provides supports and advances the part during the grinding process.
I understand doing grinding work in a lathe is a good compromise for the hobbyist who does not have access to a machine designed specifically for the job. But if done without the proper care it is bad for the machine and it might be dangerous to the operator. Today it gives me goosebumps to remember using fine grit sandpaper in a lathe to improve surface finish. :)
PS: one can find attachments that "convert" a drill press into a lathe. I would advise against them, too. :)
Re:
Progress with my lathe.
Ash Small, Thu Dec 03 2015, 05:32PM
tobias wrote ...
I believe I might be too conservative when doing machine work. There are machines specifically designed for surface grinding, and the surface grinding machines allow tolerances unmatched by a lathe tool post grinder. It's mainly due to the deflection of the part and lower tolerances on bearings and slides in the machine. Some surface grinding machines actually have a "support wheel" on the opposite side of the grinding wheel that both provides supports and advances the part during the grinding process.
I understand doing grinding work in a lathe is a good compromise for the hobbyist who does not have access to a machine designed specifically for the job. But if done without the proper care it is bad for the machine and it might be dangerous to the operator. Today it gives me goosebumps to remember using fine grit sandpaper in a lathe to improve surface finish. :)
PS: one can find attachments that "convert" a drill press into a lathe. I would advise against them, too. :)
I disagree. I learned to grind using a surface grinder as a teenager, I think, when I was taught all about 'spark out',
If you apply the same process to any other grinding process, the same levels of accuracy can be accomplished, pretty much.
If you require greater accuracy, just reduce the amount ground in each pass. Bearing backlash, and all those other factors remain constant.
It all comes down to the skill of the operator

(On the surface grinder I used, the workpiece remained bolted to the bed, while the grinding head moved)
Re: Progress with my lathe.
tobias, Thu Dec 03 2015, 05:55PM
Well, we agree to disagree :)
Going back to the controls, not sure if you already finished it but all this discussion reminded me of a lathe I used to operate that had a 5-position lever. ON (top), Coast, Break (center), Coast, REV (lower position). The lever was bolted to the car. I believe the center position shortened all windings in the motor causing it to stop way faster than to just keep them openned. I loved that. The circuit should be interesting.
Re:
Progress with my lathe.
Ash Small, Thu Dec 03 2015, 07:49PM
tobias wrote ...
Well, we agree to disagree :)
Going back to the controls, not sure if you already finished it but all this discussion reminded me of a lathe I used to operate that had a 5-position lever. ON (top), Coast, Break (center), Coast, REV (lower position). The lever was bolted to the car. I believe the center position shortened all windings in the motor causing it to stop way faster than to just keep them openned. I loved that. The circuit should be interesting.
I was just pointing out that a common mistake a lot of people seem to make is trying to take too much off in one pass, and not waiting for full 'spark out'.

I've used lathes like that in the past too, I often wondered how they stopped so quick. I think the belts would slip if I implemented that on mine, I usually run mine with the reduction gear, so it's not usually a problem anyway.
Re:
Progress with my lathe.
Ash Small, Fri Nov 18 2016, 02:53AM
Well, I finally got it running earlier this week, and have now made a new chuck key as I've not found the old one yet, already to continue with several projects that have been on hold until it was working again.
I only currently have one direction of rotation, but it's now wired through an MEM switch and and NVT switch, as opposed to just a plug on a frayed lead.
I did design another control circuiy last year utilising three relays, but my laptop died before I could post them and I've still not managed to retrieve the data from the hard drive. I do remember that the new circuit did away with the NVT switch, and had two push buttons, one for start and one for stop on the 24V circuit.
I don't yet have a coolant pump wired in, I need to rig up a tray to catch it first, but I can use it for a number of jobs I have that don't require coolant.
I should be able to start posting details of progress with some of my other projects now
