Selfmade High Voltage caps for a Marx Gen
Reaching, Wed Sept 27 2006, 10:47AM
i searched the web for some good ideas on how to build a hig voltage capacitor and made some calculations. within the next few weeks i wanted to build a new marx generator . cause doorknob caps are never really available here in germany or are very expensive , i thought i could build some myself. my idea is to use a 20cm long 25mm outer diameter and 19mm inner diameter glass tube for a cap. the calculated capacitance is 270pF at 44kV for 3mm glass. in the inside of the glass barrel i want to stick a 18mm copper tubin with around 16cm in lenght. then solder a pin on the copper and melt the glass on both sides of the barrel to enclose the copper . then i want to build some isolator like glass rounds on both ends. and then a alutape with 16cm lenght around the barrel or so.with some expirience in glass working i should be able to build some really nice hv caps, and 270pf 44kv are more than enough for a big marx when i put 2 or 3 in parallel for each stage. the output voltage of the marx should be around 600kv or so for 15 stages. but what do you think about the idea? is there any way to metalize the glass barrel on the inside and outside? some metal spray or so?
Re: Selfmade High Voltage caps for a Marx Gen
Wilson, Wed Sept 27 2006, 12:52PM
oooh. now thats an interesting idea. Perhaps if you can find an aluminium tube which snuggly encloses the glass tube, however, personally, i think you're better off with tape, as you get tigher contact, hence increasing the capacitance.
You'll need to find a sturdy way to attach everything together though. Perhaps if you have a section of the copper tube protruding, which you can drill crimp flat before drilling a hole into it for mounting?
Re:
Selfmade High Voltage caps for a Marx Gen
Eric, Wed Sept 27 2006, 06:09PM
I have metalized glass and plastic using the brashear process (silver plating). Pretty easy to do once you have the chemicals but might be more than you want to get into. I then plated copper over it.
A couple example pics, base material is silicone rubber:
Silvered Plated I think this would work well for making the type of HV capacitor you are considering.
Re: Selfmade High Voltage caps for a Marx Gen
Marko, Wed Sept 27 2006, 06:14PM
That's cool!
Could it somehow work for boards, perfboards and those trough-vias?
I saw this longer ago but I don't think I'm good enough with chermistry nor able to get required chemicals.
Nice done...
Re: Selfmade High Voltage caps for a Marx Gen
Electroholic, Wed Sept 27 2006, 07:06PM
arn't the plated Ag/Cu layer a little too thin for a pulse cap?
Re:
Selfmade High Voltage caps for a Marx Gen
Eric, Wed Sept 27 2006, 07:11PM
Firkragg wrote ...
That's cool!
Could it somehow work for boards, perfboards and those trough-vias?
I saw this longer ago but I don't think I'm good enough with chermistry nor able to get required chemicals.
Nice done...
Thanks, I bet you could get it to work on boards, as long as there was no exposed metal on them. Plating thick layers and small through vias well requires a better plating process than what I used. The process works well on glass as-is but plastics work far better with a dip in Tin II Chloride first, you might have to do that with boards.
Speaking of boards, you could use double-sided circuit boards as HV capacitors. You might have to use two in series to get a high enough voltage rating. For example, two 6"x6"x1/16" sheets in series would give you 300pf @62KV.
Electroholic wrote ...
arn't the plated Ag/Cu layer a little too thin for a pulse cap?
The Ag layer is very thin and fragile without some kind of protection. The electroplated copper layer can be as thick as you want. You'd have to run some numbers to see where internal resistance would start reducing performance. Big HV pulse caps actually do use very thin conductor foils, I bet even 1 mil of copper would be enough.
Re:
Selfmade High Voltage caps for a Marx Gen
Hazmatt_(The Underdog), Wed Sept 27 2006, 07:21PM
Well.. The trouble is getting the glass to seal to the copper. Copper requires the right kind of glass, which is leaded glass. Leaded glass is not as available now as it used to be. I have a lot of trouble finding leaded glass for sealing electrodes. I have only one piece of it now. And a Neon shop isn't likely to have a large ID thickwall piece of it.
Fusing a large piece of glass to seal the end is not as easy either. You will need a hot long flame from a hand torch or if you have a welding torch around, the flame will probably need to be 9" long or so with a sharp cone.
The seal itself will be a bit difficult because you can't just melt the glass onto the copper. It will have to be an annular seal to the copper to minimize stress. Basically a very small zone will need to touch the glass because both the glass and the Copper expand at different rates. A lateral seal will crack the glass.
Next I'd be concerned with annealing. This will be critical with the soft glass. I still have to make an oven for my stuff.
Glassblowing isn't easy either. I'm still working at it off and on because of college, but what I can tell you is that the suggested work time is 4 hours a day! just for practice >.<
What I would suggest to you is do some reading on how to silver glass. Soldering the copper to the glass is much easier then trying to fuse it. And you don't even have to use silver. There are other ways of putting other metals on the glass too.
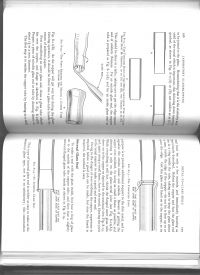
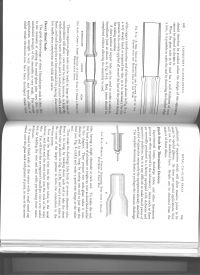
Re: Selfmade High Voltage caps for a Marx Gen
Reaching, Thu Sept 28 2006, 04:41AM
yeah hazmatt, i know thats not easy especially sealing the copper tube,. but i have another idea on how to seal when the glass trick wont work,. i can model some isolators on both sides which should not be a real problem, i have some expirience in glass working, and since i have more than enough glass from the same material i can build several prototypes to test my ideas. i can leave the ends of the glass barrel open and fill the inside with some sort of polyester or epoxyd, that should work better than just sealing the ends , cause the epoxyd leave no air in the tube , better for prevent corona discharges inside the cap.
i made a small test capacitor with a 1mm thick glass barrel and a lenght of 6,2cm for the inner copper tube (6mm) the calculated capacitance is 97pF. today i want to do a exact capacitance test to see if my calculation was right, and i´ll make a hv test with the cap to see if it can withstand 40kv AC , thats the maximum i can test here
Update
I made a few tests with parallel Plate caps using polystyrol sheets of 2mm thickness which should give a voltage rating above 100kv, the difficulty here is to get all the air out of the cap and glue the parts together. that is the current problem i have. i build a cap with 20 parallel caps measured 780pF , but the cap wont stand up 100kv or so, i tested it up to 40kv fine, but until 60kv are reached the cap died.