linear induction motor/maglev project
BigBad, Fri Jun 20 2014, 01:58AM
Building a multiphase linear induction motor and inverter from scratch.
Ordered the parts for a software driven 3/4 phase, 3kW (peak) inverter. Have more or less simulated it in LTSpice, although the exact components didn't seem to have models. Power on transients were surprisingly large. Going to be driving it from an arduino I have. I went this route because it was cheaper and I wanted to understand it, and I also wanted it to do some weird stuff, run it as a servo, and also add another 3 phases to have two independent motors; I didn't think I'd be able to do all this with a standard inverter.
The electronics and heatsinks arrived today, I showed them to my father, who's a battled hardened switch-mode power supply designer, he started mumbling about 'blowing up' and 'transients' although he didn't find any actual specific problems. LTSpice certainly showed impressive transients at times, and closer examination showed the undervoltage was out of spec. This was fixed in the simulation with an RC snubber across the drain and source of the FETs I'm using, together with some resistors on the gate and Vs to adjust the ringing and turn on speed.
I've modelled the actual motors in FEMM; seems OK. However, FEMM is 2D and the reality is 3D so I'm expecting discrepancies. The power dissipation is fairly frightening, but did the thermals on it today, apparently I should be able to drive it at full power for about 2 seconds before the insulation catches fire; but I was planning on mostly driving it at greatly reduced power, so not particularly bothered.
I've mostly wired up the half bridge for one of the phases of the driver, I'm testing that on its own, initially at low voltage to see how big the glitches are.
At one point I thought I needed a huge inductor to smooth the current from the mains, but I showed that a small panel resistor in conjunction with my smoothing capacitor forms an RC which limits the current very well, so it's under control (the slightly idealised simulation was predicting 15-60 amp pulses even though the average was a long way below 13A.)
It's quite an interesting circuit really.
I could do with a slightly larger panel resistor to smooth out the current taken from the mains, although it still works. I have written some inverter control software for the arduino. With some fiddling, it's running at a chopping period of about 5 microseconds, which is fairly good and gives a pretty reasonable 200hz waveform on four channels simultaneously.
Assembled 8 FETs on the heatsink and made a low inductance +ve and -ve bus using unetched straight copper PCBs. Currently 4 phase, since I have the FETs and the microcontroller and I have plans to do clever stuff. I have only built a single hi-lo driver so far though.
Sourced the U-cores (powder cores for high frequencies and pretty decent saturation ~1.4 T.)
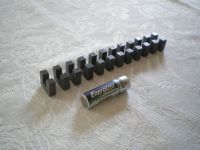
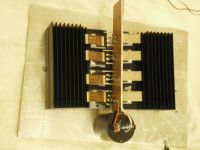
Gonna have to start winding some coils...
Ok, I've run my inverter half bridge up at full mains voltage now, but switching at very low output amplitude. Test coil got to about 45C or so, but none of the inverter components were even faintly warm. I checked various points on the circuit looking for excessive spikes, but it seems OK. The scope doesn't handle it very well in differential mode which made doing that entertaining and somewhat confusing, but so far as I can tell, everything is within spec.
Also, I found a bug that could have been blowing the fuse during power-on. The gates were floating during power-on, and probably switching on due to Miller capacitance. I've added 1k pulldowns from gate to source and that should fix it.
Re:
linear induction motor/maglev project
Steve Conner, Fri Jun 20 2014, 10:14AM
BigBad wrote ...
a battled hardened switch-mode power supply designer, he started mumbling about 'blowing up' and 'transients'
Sounds about right. He is obviously familiar with Murphy's law of power electronics

The 3-phase motor drives I've seen use IGBTs switching at relatively low frequencies, with no special care taken to avoid transients. Current sensing and limiting is by resistors in series with the low-side device emitters in small drives, and Hall effect CTs on the outputs in larger ones.
The biggest problem you'll probably come across is if using integrated high-side drivers like the IR2181, they are easily destroyed by excessive spikes, negative ones in particular. Drivers with true optical or magnetic isolation will make your life easier.
Re: linear induction motor/maglev project
Thomas W, Fri Jun 20 2014, 11:31AM
Wow! i can't wait to see this, i have been hoping to do somthing like this myself oneday, please, do show all the pictures you can! im very interested in this.
Re:
linear induction motor/maglev project
BigBad, Fri Jun 20 2014, 08:17PM
Steve Conner wrote ...
The biggest problem you'll probably come across is if using integrated high-side drivers like the IR2181, they are easily destroyed by excessive spikes, negative ones in particular. Drivers with true optical or magnetic isolation will make your life easier.
Good job I'm not using that specific device.... oh wait; doh.
I already downloaded the application note about undervoltages. The issue seems to be mostly stray inductance around the switches; I plan to keep the leads very short.
I have a spare set of switches and drivers, I'm probably going to assemble one leg on its own and see how it goes with an inductive load; just run it PWM as an oscillating voltage source, see how bad the glitches are and to allow me to optimise.
Re: linear induction motor/maglev project
BigBad, Sun Jun 22 2014, 10:42PM
I haven't got a LTSpice model of the particular switch I'm using but my SWAG based on modelling other devices is that the undervoltage switch transients with plausible stray inductances is right around the ragged edge of destroying the IR2181 (about -18 volts). The device is hardened to negative voltages down to -20v and it may theoretically work, but...
I might have to build a step-down switch stage to drive the 3 phase switches, and wind the cores to take more current at lower voltage; the switching transients seem to go with voltage.
Or I could bin the IR2181 and use a different drive approach.
hmm
I think I'll build a single phase leg first and run it at low supply voltage and low duty cycle via a small variac we have and see what undervoltage I actually get; it may not be as bad as I think; although probably it will be worse.
Re:
linear induction motor/maglev project
Sulaiman, Sun Jun 22 2014, 11:11PM
I'm not endorsing any product but for the price you should consider somethong like this

or similar / higher power.
It will allow you to concentrate on the hard part ( mechanics )
inbuilt protection methods, speed ramping, remote control etc.
later you may wabt to build your own inverter
but when you consider the design effort and cost,
a ready made inverter makes a good choice.
there are ready made inverters for up to 60,000 rpm or 100's kW. (scary!)
Re: linear induction motor/maglev project
BigBad, Mon Jun 23 2014, 10:46AM
I get where you're coming from, but I'm doing something slightly unusual, the peak power and current looks too low for what I'm trying to do at the moment, it's also rather heavy, one of my aims is to carry the power supply on the maglev and use passive cooling if at all possible. The standard power supplies are sized for continuous loads.
Anyway, I think I've solved the undervoltage issue, a lot of it is that the reverse diode takes ~1 microsecond to switch on, but LTSpice seems to agree that an RC snubber right across the source and drain of the FET will take out the transient while not burning power at other times; it just shorts out the diode for a moment and gives it breathing space to start to conduct as it reverses and also damps out the stray inductances.
I tried lots of other things from the FET app notes, but they made hardly any difference; I think it's because my circuit is running at relatively high rail voltages, a lot of motor drives run below 100 volts; mine is over 300 volts, so I'm getting proportionately bigger transients.
I'll soon find out whether the real world agrees with the simulation; judging by the simulation behaviour running the real circuit on a variac for testing seems to be a very, very good idea indeed.
Re: linear induction motor/maglev project
BigBad, Thu Jul 03 2014, 12:51AM
I've built a single leg, and am powering it from ~36 volts AC on a variac, and additionally pulsing the FETs at a quarter power (giving a 200 hz 'sinusoidal' waveform). It's giving a rather funky waveform right now, I think partly because the rectifier/smoother feeding it is a bit underpowered. But I nevertheless drove a coil from it (about 150 turns, I already had it kicking around) around one leg of an E-core.
It easily lifted a kilogram of iron running it just as a conventional attractive electromagnet. I would have run it at higher power, but the variac is fairly small. and I need to check stuff before turning it up.
It's going to be scary powerful. I'm running it at about 1/20 current at the moment...
Re: linear induction motor/maglev project
BigBad, Mon Jul 07 2014, 07:40PM
Have been running it at 1/3 voltage, 100+ volts on a variac.
I tried going above this, but the Vbs transients started getting out of hand- over 20volts doesn't make me or Mr Controller happy, but Vs looks fine. Subtle changes in board layout should (in principle) completely negate all the parasitic inductances on the drain side which are probably a lot of the problem, I modelled it in LTSpice and it looks promising, and I'm ordering some bigger and better capacitors to help damp. I'm expecting it will be able to run at full design voltage/power; my fall-back idea is simply to run it at lower voltage via a step-down, but that would be a pain.
Re: linear induction motor/maglev project
Steve Ward, Thu Jul 10 2014, 12:17AM
Having designed somewhat big BLDC drives "from scratch", the main feature id say you should not go without is fast over-current protection. Its real easy to blow up a bunch of silicon with a stalled motor.
Also watch out for braking currents and over-volting the bus from regenerative charging.
Re: linear induction motor/maglev project
BigBad, Fri Jul 11 2014, 01:23AM
On the regenerative braking; I plan to monitor the main bus and cut the output waveform if it's getting too high. The field in the secondary will then decay, and the volts will reduce. That's one nice thing about induction motors; you can turn them off; BLDCs have PMs and can't do that quite so easily.
I haven't got a firm plan for the overcurrent, but I was tentatively thinking of putting a linear hall effect sensor on a small inductor somewhere. and just monitor with software perhaps.
At the moment, I'm only using a fuse for overcurrent. I can report that it seems to be working; got through 3 so far; there seems to be a power-on transient. But whatever is causing it, the silicon is probably not in much danger, although there's certainly no guarantee, but I'm running it at such low voltage right now, the FETs are yawning, I just don't want to blow the variac. (edit: I think it's possibly due to Miller capacitance when the gates are floating at power-up switching on both FETs simultaneously, I've added resistors to stop them floating, I'll see whether that has fixed it).
inb4 fets blow
Re:
linear induction motor/maglev project
BigBad, Mon Jul 14 2014, 02:05AM
Assembled 8 FETs on the heatsink and made a low inductance +ve and -ve bus using unetched straight copper PCBs. Currently 4 phase, since I have the FETs and the microcontroller and I have plans to do clever stuff. I have only built a single hi-lo driver so far though.
Sourced the U-cores (powder cores for high frequencies and pretty decent saturation ~1.4 T.)
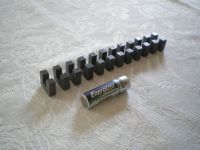
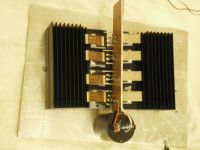
Gonna have to start winding some coils...
Re: linear induction motor/maglev project
Thomas W, Mon Jul 14 2014, 06:39AM
Wow, those are some lovely heatsinks... where did you get them? :)
Neat work, keep it up, im following this project, its very interesting.
Re: linear induction motor/maglev project
BigBad, Mon Jul 14 2014, 11:15AM
I got them from RS, I'll dig out the part number for you later. They were much bigger than I expected, I may replace them with thick aluminium plate later for lower weight; at the moment they're a couple of hundred grams each I think.
They've got a pretty low thermal resistance (~2K/W), which is why I got them, but they'd probably be very underpowered for continuous high power unless I put a fan on them. They're mainly there as a thermal reservoir right now and to handle the instantaneoous temperature rises. The bit the chip sits on is about 6 mm thick or something.
I really like the clip thing, although under extremely heavy vibration the chips could theoretically move.
Re: linear induction motor/maglev project
BigBad, Mon Jul 21 2014, 02:36AM
I've run a half bridge at full voltage now; seems basically OK, but a bit marginal maybe on the transients.
The half bridge simulates fairly well, but I've been trying to simulate a 3 phase configuration on LTSpice, but for some reason it's even more glitchy and the convergence is quite poor; I've been reading around I think I need more stray capacitance and resistances modelled. Apparently particularly for high transient, inductive circuits like this, the capacitance/resistance has to dominate at high frequency, otherwise the integration diverges at short timescales. It's tricky, because when it doesn't work, you don't know what it is about the circuit that isn't correct. It tends to not simulate at all or go unbelievably slowly.
Anyway, I've got 3 phases more or less wired up now, I should be testing them on the variac soon. I used veroboard; it seems to work surprisingly well.
I wound a coil, using impact adhesive for the 'potting' it seemed to work more or less; and set off quite quickly (epoxy is better in most respects, but the epoxies I have to hand set off a little too fast or too slow); but I accidentally blew it by overpowering it from my bridge.
Anyway, looks basically good, although things are taking longer than I would have hoped.
Re: linear induction motor/maglev project
BigBad, Thu Jul 31 2014, 02:27AM
So, I wired up 3 half bridges, and wound 6 coils and wired them to the inverter. I ran it at low volts on the variac, and it seemed perfectly OK, although it was running at very low power, so it was difficult to be sure.
So I bypassed the variac and ran it at full voltage, and adjusted the arduino to only switch the FETs on about 1/20 of the time, which should have given quite modest power, a few watts.
Unfortunately there was a big flash of white light and the panel resistors (presumably aluminium clad) I had in the circuit to act as a ballast burnt like a magnesium flare and set fire to the blanket I had on the table, so I immediately unplugged things and blew out the blanket.
So far I've worked out the panel resistors are toast, and the full wave rectifier seems to now be short circuit internally, so it will have put both positive and negative mains across the FETs. The 6 FETs seem to now be short circuit as a group; the coils are fine, the controller chips are fairly hardy to 500v or so but don't like negative voltages, so are presumably destroyed. The arduino seems fine; although it wasn't isolated, I tried to design it to make sure it couldn't be destroyed by this kind of failure and that seems to have worked at least.
It's not clear what caused the failure, but it didn't happen until the arduino started to drive the FETs. Perhaps the FETs were turning on at the same time due to noise coupling across the controller chip or something; although I did have caps to try to prevent these kinds of issues, and the simulation suggested it should work. Alternatively, if one or more of the FETs were static damaged, then perhaps that failed, and that took out the rectifier.
It's highly likely that all the FETs are toast, but we'll see. They wouldn't have liked the reverse voltage after the rectifier went out; they're only specced for 192 Amps, and I doubt the fuse would have been quick enough, and the inline panel resistance (0.6 ohms) wouldn't have been enough to limit the current down to that.
Still, in spite of this, I definitely understand the ins and outs of this kind of stuff a lot better, and I'm confident that it should work in the end.
Re: linear induction motor/maglev project
BigBad, Tue Aug 05 2014, 01:38AM
Further measurement has shown that the rectifier didn't blow, when I disassembled the circuit and tested the components individually, only a couple of the FETs had failed short circuit and the panel resistors but that was all.
I think one of the drive circuits had allowed both of the FETs to conduct at the same time; the newer design driver circuit I was running on the others seemed to protect them; and so I've built another one of the newer spec drivers and replaced the failed FETs and wired it all up.
So I've got the system up and running at low volts on the variac again, and I'm now sporting a full set of proper wound coils. The waveform I'm seeing looks a bit wonky though, so I'm trying to figure out whether the circuit needs changes or not before running it at full voltage.
I've also done a bunch of theoretical analysis; I had been planning to add more phases to control motors, but it looks like I'm best off using TRIACs to switch 3 phase onto groups of wound cores; mainly because they're a lot cheaper than FETs and don't require caps to stabilise them (normally you would need reasonably big caps for snubbing, but I can momentarily turn off the inverter when I switch the caps and thus avoid the need for snubbers.)
edit: had it up to full voltage for a short time, at low power, while checking circuit waveforms on the scope, and driving my test motor. Seemed OK. But I rearranged the probes and ran it back up to 70% volts, and one of the FETs promptly blew (shorted) on the phase I was checking and took out the fuse. It's unclear why, although the probes are one suspect due to the capacitive loading.
edit2: strongly considering binning the MOSFETs and going with IGBTs, the MOSFETs are too highly strung for this kind of thing, and the scope and other equipment I have access to is incredibly marginal for debugging the high frequency switching transients.
Re: linear induction motor/maglev project
BigBad, Fri Sept 19 2014, 02:23AM
I managed to get the bridge back up again, but I ran it with no load- which should have worked, but it was only to discover I was hitting a resonance on the driven side. This apparently was due to the lack load which had been damping it. This seems to have caused an undervoltage that blew all the controllers and one further set of FETs.
So I replaced the controllers, and put extra big (80 ohm) resistors on the gates, and it now seems to be working again, at full voltage, both with and without a load, although only a single H-bridge right now.
I've also worked out how to control the output using TRIACs. Initially I figured I wouldn't need a snubber, but the hard voltage edges of the switch mode inverter exceeded the dv/dt's of the available TRIACs so I had to snub them. It took a while to work out how to do this, but I've got the hang of it now, and it works fine.
I've also wound a set of 6 coils, mounted them on three of the u-cores and fixed them to a board.
I'm now able to drive them at 400hz from the H-bridge, and I'm getting noticeable force from them, even though I'm actually running the bridge at comparatively low power still, about 1/30 of maximum current.
Overall, looking quite positive right now, nothing has blown up in a while, and I managed to get to the bottom of some weird/scary traces I was getting on the scope. It looked like for sure I was hitting controller diode limits as I turned it up towards full voltage, but, except for the no-load resonance, it turns out that most of it was that the scope was saturating internally at high voltage in differential mode. However, it's still a little marginal nevertheless.
Per my thermal calculations, everything except the coils seem to be running cool, and even the TRIACs are switching on and off correctly. I did look at changing to IGBTs and even bought at set (they're not particularly expensive) but when I ran the numbers they use a LOT of power.
Re: linear induction motor/maglev project
BigBad, Fri Oct 17 2014, 02:46AM
I had got the snubber circuit to work, but it failed as I turned up the current and voltage, and the TRIAC was conducting all the time. It was unspectacular; the coils just wouldn't switch off. A second snubber was working fine, but I hadn't wound up the voltage on that yet.
Further analysis showed I'd hit a resonance; it had overvoltaged the capacitor (which seems to have shorted-it was still good at low voltage when I put a meter on it, but I worked out it had probably failed by replacing everything around it, without the problem going away) and the TRIAC also showed signs of damage.
I had been trying to avoid having to use large resistors which would have damped it nicely, but I calculated that they would have used quite a lot of power, so it was deliberately underdamped, and this was the wages of my sin.
Anyway, so I replaced the capacitor and TRIAC and wired in some heavy duty diodes to limit the overvoltage, figuring they wouldn't quite use as much power. The original circuit already had diodes in the power supply, and I had mistakenly though they would have protected it, but of course they needed to be right between the cap and the inductive load to protect the circuit.
I simulated it, and it looked promising. But after wiring it in, I powered it on fine, but when I excited it at 400 hz, some of the tracks blew off the snubber PCB with a loud pop.
Ce la vie.
Not clear what went wrong yet. I'm hoping it hasn't blown my inverter bridge up, but I wouldn't bet on it.
I'm definitely finding it entertaining building circuits where almost all of the components have to have heat sinks...
Re: linear induction motor/maglev project
BigBad, Wed Feb 18 2015, 01:25AM
OK, I designed two circuit boards and had them fabbed for me; a TRIAC board and an inverter board.
Made a couple of minor errors on the TRIAC board, the clamping diode's holes were the wrong size, and I'd picked the wrong package for the TRIACs, but in both cases I've managed to make it work.
The Inverter board was nearly perfect, although I should have placed the IR2181s closer to the FETs, but it just about works anyway, although I had some tense times as I wound up volts on the variac, the overshoots are a bit marginal, but it seems to be a volt or two inside the absolute max in both directions. I had a lot of trouble with a ~15MHz ringing on the low sides but I found that a 10 ohm resistor on the earth side between the IR2181s and the earth plane of the FETs seems to kill that just nicely.
So I potted up a couple of the u-cores with windings and applied power and then changed the settings on the inverter.
I've got significant lift, a few Newtons momentarily although there's a whole bunch of heat from each pulse and it's not anything like full power on the inverter; this from a tiny single phase motor that's about 4cmx4cm. The inverter itself seems to be stone cold.
Probably sounds almost a bit lame, but that's what I'm aiming for I want something that can pump out a lot of power for a short period, just to center my maglev, and then I can do the static lift with permanent magnets.
The triac control seems to be working properly, it stays off when it's off, and goes on when it's supposed to be on. The current TRIAC board should be able to handle up to 9 motors.
I may well respin both boards at some point, but they seem to be working right now.