Another Flyback Driver circuit... Why use 24 volt power supply? I want to use 169.70 VDC
tarakan2, Thu Apr 17 2014, 10:46PM
Hello.
I want to build another flyback driver circuit.
I built one before but it wasn't so great.
I am thinking about using 120Volts from the electric socket, rectifying this voltage using a bridge and smoothing it out with a large capacitor filter.It makes no sense to convert 120 volts AC to 24 or 48 volts DC and than step it up to kilovolts.
More current = more losses...
I want to make something like this:


This is what I used to have before I burned it in an experiment:

but IRFP 250 Mosfets limit my input voltage to 40 Volts.
Why not use 120 volts in my next project?
This way I won't have to worry about the current rating of my 12 to 48 volt power supply that I would probably have to get from an LED lighting supplier...
The top two links show some Flyback driver circuits that use mosfets rated up to 500 volts drain source voltage.
IRFP 250 can handle 200 volts maximum...
What determines my input voltage in the circuits mentioned above is a voltage divider that consists of the resistors in series with the Gate pins of the MOSFETS and those resistors that connect them to the ground rail.
Am I correct?
Voltage on the gate must remain slightly below Gate opening Vgs and Zener diodes have to purge the gate once the voltage on the gate exceeds 12 V.
Is this pair of Zener Diodes a safety measure to protect the gate or is this to make this circuit oscillate?
I am a novice with MOSFETS so I am not sure why Vgs threshold for IRFP250 is 2 to 4 volts even though all circuits with this mosfet seem to use 10 to 12 volts to open the gate... I don't see 10 to 12 volts anywhere in the datasheet...

But this is just case study for IRFP250.
I am not sure if I should pick a different MOSFET to run off ~170 volts (120VAC rectified -- 120*sqrt(2) = 169.705627485 -- peak DC voltage).
So should I increase resistance of the resistor that is in series with the gate, get a 0.5A or more powerful zeners or a combination of both?
What should be my MOSFET choice and how do I determine the optimal Gate voltage for it to fully open?
Thank you.
Re:
Another Flyback Driver circuit... Why use 24 volt power supply? I want to use 169.70 VDC
Microwatt, Thu Apr 17 2014, 11:20PM
your never going to get a zvs to run at over 100 volts. which is why you don't see them used in computers. use this circuit
http://danyk.cz/igbt_2_en.html
Re: Another Flyback Driver circuit... Why use 24 volt power supply? I want to use 169.70 VDC
Antonio, Fri Apr 18 2014, 12:55AM
This circuit can, in principle, run with 100 V or more, but:
The inductances from the primary coil and of the series coil must be much larger than the ones required for low-voltage power supplies, and if their cores saturate the circuit may easily be destroyed.
The gate drive through resistive dividers is already inefficient al low voltages, and much less efficient at higher voltages.
In any case this circuit is dangerous because nothing impedes the symultaneous conduction of both mosfets.
The question about 12 V drive is because the threshold vgs voltage of 2-4 V is the minimum for the mosfet conduct, but the maximum current that it can conduct and the conductance when conducting are higher with higher vgs.
Re:
Another Flyback Driver circuit... Why use 24 volt power supply? I want to use 169.70 VDC
tarakan2, Fri Apr 18 2014, 02:12AM
Antonio wrote ...
This circuit can, in principle, run with 100 V or more, but:
The inductances from the primary coil and of the series coil must be much larger than the ones required for low-voltage power supplies, and if their cores saturate the circuit may easily be destroyed.
The gate drive through resistive dividers is already inefficient al low voltages, and much less efficient at higher voltages.
In any case this circuit is dangerous because nothing impedes the symultaneous conduction of both mosfets.
The question about 12 V drive is because the threshold vgs voltage of 2-4 V is the minimum for the mosfet conduct, but the maximum current that it can conduct and the conductance when conducting are higher with higher vgs.
Interesting.
I am still unsure how optimal Vgs is determined. It is not on the datasheet...
Higher inductance? I need to wind 10X the amount of turns to get the same inductance? Is there a way to increase the frequency along with voltage to compensate for that?
Were there any circuits where 120AC was rectified and used directly to drive the primary coil of the flyback transformer?
It makes sense for someone to develop such circuit, even if it doesn't use voltage dividers or uses TRIACs instead of MOSFETs.
It would make sense to use inductive or capacitive feedback instead of resistive feedback in such oscillator.
Maybe even a small transformer to trigger the gates (or bases) of semiconductors of the oscillator.
Maybe this 47 - 100 uH choking coil in Mazzilli circuit can be replaced with some sort of a transformer that can be used for feedback purposes - to open gates.
It would make sense to use semiconductors with higher Vgs all together or to use thyristors.
Did anybody ever build something like this? I am too inexperienced to develop my own circuit.
Re: Another Flyback Driver circuit... Why use 24 volt power supply? I want to use 169.70 VDC
Andy, Fri Apr 18 2014, 02:52AM
Hi
I've been wondering the same thing, is it that the fly-back isn't designed for that input, flux density/cross section?
Mains voltage with current behind it, at high frequency wouldn't be to safe for me, have noticed that high frequency seems to propagate through insulators over a longer distance.
EDIT, I miss understood what you said, didn't release you are limiting current, just assumed with the large filter cap....that it was on the ac side, maybe not the dc side
Re:
Another Flyback Driver circuit... Why use 24 volt power supply? I want to use 169.70 VDC
tarakan2, Fri Apr 18 2014, 02:59AM
Andy wrote ...
Hi
I've been wondering the same thing, is it that the fly-back isn't designed for that input, flux density/cross section?
Mains voltage with current behind it, at high frequency wouldn't be to safe, have noticed that high frequency seems to propagate through insulators over a longer distance.
12 volts 120 volts - difference of one order is not that great. If you are afraid of the mains voltage an high currents - put a fuse in the circuit or limit current with a ballast.
A chopper is a more modern way of controlling current... I would reduce the pulse duration on primary to limit current consumption and prevent saturation from happening.
More voltage would saturate the core as much as less voltage... Compensate by reducing currents or pulse duration.
It would make sense to make this circuit work faster with higher voltage.
If this circuit used feedback that was wound onto the primary of the flyback, than saturation could be avoided because if the core is saturated, the feedback would not work.
Re: Another Flyback Driver circuit... Why use 24 volt power supply? I want to use 169.70 VDC
Sulaiman, Fri Apr 18 2014, 09:42AM
I have succesfuly run a zvs/royer on full wave rectified 110 Vac
but I used a separate 12 Vdc supply for the gate drive.
I did not use it to draw arcs as I'm sure that would have blown something.
Using rectified 240 Vac I had one instant failure and one delayed failure and gave up.
I would not reccomend rectified mains for a zvs/royer.
On the bright side,
the original primary in most flybacks is designed for around 110 Vac rectified supply
so a conventional flyback circuit using a 555 or smpsu ic driver works excellently.
Re:
Another Flyback Driver circuit... Why use 24 volt power supply? I want to use 169.70 VDC
Antonio, Fri Apr 18 2014, 01:37PM
tarakan2 wrote ...
I am still unsure how optimal Vgs is determined. It is not on the datasheet...
Higher inductance? I need to wind 10X the amount of turns to get the same inductance? Is there a way to increase the frequency along with voltage to compensate for that?
Were there any circuits where 120AC was rectified and used directly to drive the primary coil of the flyback transformer?
Look at the curves showing current x voltage for different vgs. The minimum vgs depends on the maximum drain current. It's safe to use 12V, as the maximum is usually 20V.
Inductance is proportional to the square of the number or turns, for the same core. So, if you increase the voltages 10 times and want the currents 10 times smaller (same power), you need inductances 100 times larger, or 10 times more turns.
Usual flyback transformers in TV/monitor applications operate with around 100V primary voltage. Just copy the circuits from the schematics of the boards. The same boards usually have also an useful multi-output switching power supply that can be copied too and used to power the flyback circuit.
Re:
Another Flyback Driver circuit... Why use 24 volt power supply? I want to use 169.70 VDC
tarakan2, Fri Apr 18 2014, 02:16PM
Sulaiman wrote ...
I have succesfuly run a zvs/royer on full wave rectified 110 Vac
but I used a separate 12 Vdc supply for the gate drive.
I did not use it to draw arcs as I'm sure that would have blown something.
Using rectified 240 Vac I had one instant failure and one delayed failure and gave up.
I would not reccomend rectified mains for a zvs/royer.
On the bright side,
the original primary in most flybacks is designed for around 110 Vac rectified supply
so a conventional flyback circuit using a 555 or smpsu ic driver works excellently.
I am glad that you had successfully done it.
I live in United States so our mains are 120VAC.
It makes sense to use a small transformer to power the gates or to make a capacitor voltage divider.
Some way of controlling current by limiting the amount of time gates remain on can be applied to draw arks and not to burn anything.
Maybe some native flyback transformer windings can be used with rectified mains...
555 may be used. I can even make it with a microcontroller to adjust the chopper and other characteristics inside a program.
So what circuit have you used?
Re: Another Flyback Driver circuit... Why use 24 volt power supply? I want to use 169.70 VDC
Sulaiman, Fri Apr 18 2014, 03:41PM
I have used 555 to drive an igbt with c150 Vdc for the flyback primary,
I did not use any voltage feedback for that circuit
so output voltage varied as the load current changed.
I used lots of 1.5KE350CP TVS diodes (because I bought a lot cheap from eBay)
to protect the transistor from over-voltage spikes
with one eht diode in series to reduce capacitive charge/discharge losses.
I think I used 3x series by 5x parallel to absorb full power input with no output load.
(not enough, thay got quite hot at full power setting with no load)
I should have built in voltage regulation
So
I have since then bought a few UC2825 smpsu IC
(for an improved version with output voltage regulation and current limit)
and 10x 35kV flyback transformers ... as usual, another project waiting .......
Re: Another Flyback Driver circuit... Why use 24 volt power supply? I want to use 169.70 VDC
Erlend^SE, Fri Apr 18 2014, 06:01PM
Actually.. the parts you need for flyback operation is already in the monitor.
There is the HOT-transistor, the base-drive transformer for it, does capacitors, they are even assembled on the board, as far as you can use that. The tricky part may be to remove the need for the yoke, given you use the board as-is.
Re:
Another Flyback Driver circuit... Why use 24 volt power supply? I want to use 169.70 VDC
tarakan2, Fri Apr 18 2014, 06:09PM
Erlend^SE wrote ...
Actually.. the parts you need for flyback operation is already in the monitor.
There is the HOT-transistor, the base-drive transformer for it, does capacitors, they are even assembled on the board, as far as you can use that. The tricky part may be to remove the need for the yoke, given you use the board as-is.
I thought of this. Not sure what the yoke is but there is a high voltage, powerful transistor that drives the flyback. Not sure what voltage it uses but it would make perfect sense to just use existing components and circuitry. I was planning on using a flyback transformer that is very old to make sure there is no rectifier diode built into the output.
CRT tvs mostly come from the era of current-controlled semiconductors vs voltage-controlled MOSFETs.
I like to work with voltage-controlled semiconductors since it is so easy to design circuits with them where something is either on or off.
Re: Another Flyback Driver circuit... Why use 24 volt power supply? I want to use 169.70 VDC
Erlend^SE, Sun Apr 20 2014, 07:06PM
Yoke = deflection coils.
Hard to miss the part.
Re:
Another Flyback Driver circuit... Why use 24 volt power supply? I want to use 169.70 VDC
tarakan2, Tue Apr 22 2014, 05:54PM
Anybody used TRIACs or power thyristors for this purpose?
I am really curious.
Anybody knows anything about this:

???
I feel like current-controlled circuit with two transistors instead of MOSFETs is a better choice in this case...
Maybe something else...
I want to know what was done before I build my own.
Did anybody ever drive a flyback transformer with a full bridge (4 semiconductors?).
I feel that this is safer if I use rectified mains.
Re:
Another Flyback Driver circuit... Why use 24 volt power supply? I want to use 169.70 VDC
tarakan2, Tue Apr 22 2014, 08:12PM
Would it be possible to modify Mozilli circuit to use rectified mains?
Would it be possible to use this circuit with a capacitiva voltage divider to power the gates of MOSFETS with less voltage than 170VDC?
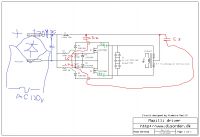
W0uld it make sense to install C8 to make both gates of two MOSFETs "compete" for current and to keep two MOSFETS from opening at once?
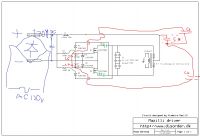
Re: Another Flyback Driver circuit... Why use 24 volt power supply? I want to use 169.70 VDC
Antonio, Tue Apr 22 2014, 08:40PM
You disconnected the mosfets by adding capacitors in series with them and disabled the feedback through the diodes...
Re:
Another Flyback Driver circuit... Why use 24 volt power supply? I want to use 169.70 VDC
tarakan2, Wed Apr 23 2014, 04:44AM
Antonio wrote ...
You disconnected the mosfets by adding capacitors in series with them and disabled the feedback through the diodes...
I see what you are talking about.
So if I leave the feedback through diodes, but disconnect the shifting voltage (or the voltage used to help open gates through resistive voltage dividers) would it work off 170VDC?
The goal is to have less than 20 volts at gates and not to loose too much power in voltage dividers.
Would it be wiser to use capacitive voltage dividers?
Would it be possible to replace R3 and R4 with a capacitive voltage divider?
Did anybody successfully run this circuit with voltages above 40 volts?
Is it possible to disconnect this branch with r3 and r4 and still open gates?
I cannot model this circuit in dynamic.
Re:
Another Flyback Driver circuit... Why use 24 volt power supply? I want to use 169.70 VDC
tarakan2, Sat Jun 07 2014, 09:24AM


Would any of the two circuits make sense?
Do I need to have 50X50 windings on my primary to reduce the current?
Do I need 470 ohm resistors still?
I can use 24 volts if the maximum gate voltage of my mosfets is greater than 24 volts. Am I correct?
I want to use mains voltage, but to have the right to control the current by screwing in the light bulb of an appropriate wattage in to the supply circuit.
Thank you very much.
Re: Another Flyback Driver circuit... Why use 24 volt power supply? I want to use 169.70 VDC
Sigurthr, Sat Jun 07 2014, 01:46PM
Why are you trying to use a Royer oscillator when you could much more easily use a standard half bridge to drive the flyback transformer at whatever input voltage you like. A standard SSTC style driver and half bridge inverter circuit being fed by a variable frequency oscillator will let you adjust output power by moving closer to or away from the resonance point of the flyback, giving you precise control of the output without needing a variac.
It could be as simple as a 555 feeding a UCC37321/UCC37322 pair into a GDT, which drives a half bridge of FDL100N50F MOSFETs. You'd be good up to ~480V DC Bus and capable of switching more amps than your wall can deliver provided you cool the fets well.
Re:
Another Flyback Driver circuit... Why use 24 volt power supply? I want to use 169.70 VDC
Mads Barnkob, Sat Jun 07 2014, 02:07PM
Sigurthr wrote ...
Why are you trying to use a Royer oscillator when you could much more easily use a standard half bridge to drive the flyback transformer at whatever input voltage you like. A standard SSTC style driver and half bridge inverter circuit being fed by a variable frequency oscillator will let you adjust output power by moving closer to or away from the resonance point of the flyback, giving you precise control of the output without needing a variac.
It could be as simple as a 555 feeding a UCC37321/UCC37322 pair into a GDT, which drives a half bridge of FDL100N50F MOSFETs. You'd be good up to ~480V DC Bus and capable of switching more amps than your wall can deliver provided you cool the fets well.
Sigurthr is right, there is no reason to try and brute force a Royer oscillator to do things it can not handle with the kind of switches available, the self oscillating nature of this circuit works fine within some limited boundaries and outside of them it burns or needs auxiliary circuits where it gets even more complex than just building a half bridge driver with something like the TL494 IC.
I made a TL494 driver that easily kills the flybacks from over voltage before the bridge explodes:

Re:
Another Flyback Driver circuit... Why use 24 volt power supply? I want to use 169.70 VDC
TwirlyWhirly555, Sat Jun 07 2014, 02:16PM
I Say go half bridge too its a lot less of a pain to get going and gives just as good results and better
With 60V 50A cheap mosfets and a PLL driver ( Can be fixed Frequency driver ) from a 50V DC bridge supply I was getting This
With the correct FETs or IGBTs and driver it can run at 120V no problems and its a lot less failure prone .
Re:
Another Flyback Driver circuit... Why use 24 volt power supply? I want to use 169.70 VDC
tarakan2, Sat Jun 07 2014, 06:08PM
Mads Barnkob wrote ...
Sigurthr wrote ...
Why are you trying to use a Royer oscillator when you could much more easily use a standard half bridge to drive the flyback transformer at whatever input voltage you like. A standard SSTC style driver and half bridge inverter circuit being fed by a variable frequency oscillator will let you adjust output power by moving closer to or away from the resonance point of the flyback, giving you precise control of the output without needing a variac.
It could be as simple as a 555 feeding a UCC37321/UCC37322 pair into a GDT, which drives a half bridge of FDL100N50F MOSFETs. You'd be good up to ~480V DC Bus and capable of switching more amps than your wall can deliver provided you cool the fets well.
Sigurthr is right, there is no reason to try and brute force a Royer oscillator to do things it can not handle with the kind of switches available, the self oscillating nature of this circuit works fine within some limited boundaries and outside of them it burns or needs auxiliary circuits where it gets even more complex than just building a half bridge driver with something like the TL494 IC.
I made a TL494 driver that easily kills the flybacks from over voltage before the bridge explodes:

I like this circuit.
I am lazy to do math, so I would like to ask if you know what
AL value (nano-Henries-per-turn-squared or nH/N2) your ferrite core had.

MAX4420 is a buffer amplifier and a comparator that brings the logic 1 to the supply voltage and switches off when logic voltage is near 0V.
As I understand, I can drive this circuit with various sources of AC signal that is above 2.4V

ucc37321 is another IC that you have used in the Tesla coil driver that can be used with 1 volt logic input according to the datasheet. Am I correct?

So I can drive my Flyback with an AD9851 (outputs 1.5V), an Arduino microcontroller and a dial in frequency input.
I like that antenna in the circuit. I made a discovery that Ne-2 neon bulb can be used to trigger low voltage events with high voltage since if gas is ionized by an intense electric field, Ne-2 starts to conduct current through the leads. High voltage is isolated by the glass and is delivered to the bulb by a single wire conductor. This is also how I measure HV alternating currents with an oscilloscope and it works up to 100kHz...
---------------------------------------
----
I have two 1950s flyback transformers. They have no rectifiers inside and I want to use them. I am afraid of burning them because I had to acquire two 1950s TVs to pull them out of.
Thank you.
Re:
Another Flyback Driver circuit... Why use 24 volt power supply? I want to use 169.70 VDC
Mads Barnkob, Sun Jun 08 2014, 07:01AM
tarakan2 wrote ...
Mads Barnkob wrote ...
Sigurthr wrote ...
Why are you trying to use a Royer oscillator when you could much more easily use a standard half bridge to drive the flyback transformer at whatever input voltage you like. A standard SSTC style driver and half bridge inverter circuit being fed by a variable frequency oscillator will let you adjust output power by moving closer to or away from the resonance point of the flyback, giving you precise control of the output without needing a variac.
It could be as simple as a 555 feeding a UCC37321/UCC37322 pair into a GDT, which drives a half bridge of FDL100N50F MOSFETs. You'd be good up to ~480V DC Bus and capable of switching more amps than your wall can deliver provided you cool the fets well.
Sigurthr is right, there is no reason to try and brute force a Royer oscillator to do things it can not handle with the kind of switches available, the self oscillating nature of this circuit works fine within some limited boundaries and outside of them it burns or needs auxiliary circuits where it gets even more complex than just building a half bridge driver with something like the TL494 IC.
I made a TL494 driver that easily kills the flybacks from over voltage before the bridge explodes:

I am lazy to do math, so I would like to ask if you know what
AL value (nano-Henries-per-turn-squared or nH/N2) your ferrite core had.
MAX4420 is a buffer amplifier and a comparator that brings the logic 1 to the supply voltage and switches off when logic voltage is near 0V.
As I understand, I can drive this circuit with various sources of AC signal that is above 2.4V

ucc37321 is another IC that you have used in the Tesla coil driver that can be used with 1 volt logic input according to the datasheet. Am I correct?

So I can drive my Flyback with an AD9851 (outputs 1.5V), an Arduino microcontroller and a dial in frequency input.
I have two 1950s flyback transformers. They have no rectifiers inside and I want to use them. I am afraid of burning them because I had to acquire two 1950s TVs to pull them out of.
Thank you.
I used AL:5750nH cores, maybe it was N30 material.
You can use any MOSFET driver that is capable of driving your MOSFETs, the MAX4420 was no specific choice, but what I had at hand.
The old disc flyback transformers are lovely, since they do not have the built-in rectifier you can use them for experiments that require high voltage AC, f.ex. a plasma globe.
Re: Another Flyback Driver circuit... Why use 24 volt power supply? I want to use 169.70 VDC
Sulaiman, Sun Jun 08 2014, 11:15AM
Forgot to ask the obvious question;
What do you want to do with the eht output?
For just making arcs the 1/2-brdge is probably the best,
if you want very high voltage d.c. at low current for 'serious' experimental work,
I suggest simple flyback topology as it puts the least voltage stress on the o/p diode(s)
Re:
Another Flyback Driver circuit... Why use 24 volt power supply? I want to use 169.70 VDC
tarakan2, Mon Jun 09 2014, 06:14AM
I want to build a high voltage AC supply for Tesla Hairpin circuit, and other sperk-controlled experiments.
I want to stick with
http://kaizerpowerelectronics.dk/high-voltage/tl494-flyback-driver/I want to know what kind of ferrite was used on the GDT. What are the nanoHenries per turn?
Thanks.