Royer induction heater component and design considerations -
Meatball, Tue Mar 11 2014, 07:18AM
I'm building the royer induction heater as referenced here:


Its the design posted and built by several of you guys.
Since this setup has no center tap on the work coil, each side of the tank needs a choke to limit in-rush current to the tank.
Next, I'll refer to the next two photos:

and

which depict two types of DIY chokes. Unfortunately, I have no ATX PSUs lying around to steal ferrite rings from, and I don't have any two identical spare transformers I can just unwind and use like seen here previously.
So instead I'll go and buy one. I've already selected two possibilities:

(Miller)
and

(Coiltronics)
since mouser is really the only place I know to go to, when I'm looking for something specific enough as this.
The Miller product just looks like its wrapped around a short rod, and the coiltronics product is the more popularly seen toroid.
I've never seen anyone here use one of the former.. is there a problem with it? Its far cheaper and it can handle more current than the latter.
But maybe there's something even better out there that I could be doing...
Do you guys have any guidance you can offer? This is one of the things that has me stuck....
Another thing that has me stuck is the use of an isolation transformer between the coil and the MMC. Is this element necessary for this particular setup as it is? Will I short the FETs if the work piece shorts across the work coil? I see lots and lots of heater designs with this element - but other builds don't. Why is this?
If I needed one to protect my silicon, where the heck do you guys find such huge ferrite cores that transfer so much power? I can only find them for <20W.
I'm aiming for ~900W with a 36VDC input of a MOT and a tank capacitance of 4-5uF. My 1/4" Cu tubing might be a bit lossy, but I can surely cool it.
And finally, I see lots of notes that mention how "this particular build" would be better with conduction cooled caps, airflow cooled caps, and I've ever seen a setup with the cap bank and work coil all submerged in vase of ice water. This, coupled with running a water loop through the work coil doesn't sit right with me. High frequencies+High VAC + high peak currents + water seems counter intuitive. Are there any safety considerations I should be aware of? What if the work coil puts the water loop at some find of AC potential? Is this possible? I would much rather mount a muffin fan over the MMC. It seems so much simpler. Why haven't I seen that done before?
I apologize if it seems like I'm in over my head here -I'm asking a lot of questions after letting them build up after a month of hard reading and searching. I've built a nice zvs flyback driver, a DRSSTC kit, and other interesting things, but this is my first induction heater.
What do you all think?
Regards,
Tyler
PS - Attached are all the parts I have so far. I have a total of 5,000uF to smooth out the rectified MOT with. I hope that will be enough..
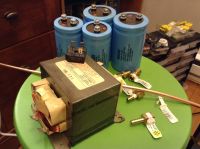
Re:
Royer induction heater component and design considerations -
IamSmooth, Tue Mar 11 2014, 05:16PM
I know you are going for a Royer design, but you asked at the end about water-cooled caps and components. If you read my tutorial (different design) you can see that I use water-cooled caps, work-coil and mosfets.
Here is the tutorial

Go through the pages and you will see the sections on the water-cooling. In fact, I was very meticulous to cover almost every aspect of a good design, regardless of the topology.
First, the water is pure, so there is little conduction if any. Second, the cooling loop is different for my work-coil/cap and mosfets. Each mosfet had its own cooling loop just in case there was an issue. Third, I used an isolation transformer so my heater was floating with respect to ground.
My coil did over 12kw so 900W should not be a problem.
Re: Royer induction heater component and design considerations -
kamelryttarn, Mon Jan 16 2017, 12:47PM
I am also planning my own build of the same circuit. I bought a finished induction heater from ebay first to get a feel for it before I started to build my own. I have a couple of questions and the first one is regarding the two chokes. I plan for a frequency around 40-50kHz and I hope to eventually reach 1000-2000W. How do I calculate the optimal value of the choke in regards to cost vs function?
I have used the micrometal software to calculate a DC biased choke rated for 55A @ 50kHz but do I need to factor in the frequency of the induction circuit? If so I seem to need a 4inch toroidal core made of a special compositon that turned out to be rather expensive. The skin effect at just under 60kHz would suggest I should make the wire from 20 individually isolated strains of 24 AWG enamelled copper for a total rating of roughly 55-60A at the desired frequency, but again, that may not be necessary. I should perhaps mention that my power supply gives me 37V no load so I expect somewhere near 35V under full load.
Can anyone help me out here?