Electronic ignition thread
Ash Small, Sat May 18 2013, 10:00AM
I want to build an electronic ignition system. Requirements as follows:
Multiple spark (each time it fires I want it to have a series of sparks to lengthen the effective ignition time for better burning, especially with leaner mixtures). I'm not sure what the optimum duration is.
must be HIGH ENERGY ie BIG SPARKS
I don't need 'advance mapping' or anything at this stage. It will be 'fixed ignition' or 'manual advance/retard'.
Not sure whether to 'wind my own' pickups, use 'off the shelf' pickups, or trigger it with points.
Any ideas how I can achieve these goals SIMPLY and RELIABLY?
Re:
Electronic ignition thread
johnf, Sat May 18 2013, 10:09AM
Ash
Buy a MSD ignition unit
like

Re:
Electronic ignition thread
Proud Mary, Sat May 18 2013, 10:16AM
The transfer efficiency of ignition coils is very low.
This paper claims that adding a peaking capacitor of 90 pF at the plug increases the transfer efficiency from less than 1% to "approaching 50% with peak current discharges of over 1000 amps."

Re:
Electronic ignition thread
Ash Small, Sat May 18 2013, 12:23PM
You should know me better than that by now, John

.
The Interspan unit would probably be my 'unit of choice' if I wanted to buy one

.
I can't get that link to work, PM. I managed to get to the main website, though, but not much technical info there.
This article has quite a bit of info regarding using a capacitor and a couple of MOSFETs to achieve multiple sparks:

I'm still reading it.
I've done some quick calculations, and worked out that I want the 'spark burst' to last 'of the order of' one millisecond (I believe some commercial systems last ~0.5mS), and my first thoughts are (giong right back to 'first principles') that it might be possible to build a resonant 'tank circuit' utilising the spark gap, a capacitor and an inductor, which resembles the primary circuit of an SGTC, which produces a burst of sparks lasting ~1mS each time the capacitor is charged by a coil. The coil will fire at ~50Hz max, I think. (The 1mS burst length figure is a maximum, 0.5mS or less will probably suffice)
Efficiency isn't really an issue here, as an alternator will be fitted, unlike a lot of racing engines which rely on batteries, etc.
Re: Electronic ignition thread
Patrick, Sat May 18 2013, 01:53PM
well the HEI coils are better at energy transfer than the old oil-can types with the "I" cores, your planning to make your whole system an elaborate SMPS, but I think your better off with some commercial product like the MSD stuff.
Re:
Electronic ignition thread
Ash Small, Sat May 18 2013, 03:05PM
Patrick wrote ...
well the HEI coils are better at energy transfer than the old oil-can types with the "I" cores, your planning to make your whole system an elaborate SMPS, but I think your better off with some commercial product like the MSD stuff.
Yep, HEI coils may well be the thing to use, but I've also thought about using flyback topology with some fast (>=100kHz) magnetics, and just giving it a 1mS blast fifty times a second. 50mS is ~5% duty cycle, so I could really push the Bmax, etc. (I assume a big gap on some fast 'E' cores, or whatever, could work quite well at 5% duty cycle?)
I can't believe that people here on a 'make your own BIG sparks' forum are actually advising me to go out and BUY something
EDIT: Does flyback topology have a Bmax?
Re:
Electronic ignition thread
Proud Mary, Sat May 18 2013, 04:30PM
The link I posted above works for me, Mr Ash, so I don't know what is wrong there.
Here is a paper that describes a set up similar to what you have been describing:
High Frequency Ignition System for Gasoline Direct
Injection Engines 
Re:
Electronic ignition thread
Ash Small, Sat May 18 2013, 07:10PM
Proud Mary wrote ...
The link I posted above works for me, Mr Ash, so I don't know what is wrong there.
It's working now. It's quite interesting. I use un-suppressed plugs anyway, which, as the article suggests, have ~10pF of capacitance anyway.
The other article is also very interesting, it demonstrates that a 'tesla coil' approach could work quite well. Maybe some form of SSTC, or even DRSSTC circuit could be employed here, operating in 'burst mode', very similar to an interruptor?
Re:
Electronic ignition thread
Proud Mary, Sat May 18 2013, 11:44PM
There's a paperback book about developments in RF plasma sparking plugs for sale on Amazon here:
Radio Frequency Plasma Spark Plug Development and Engine Testing: Design of a quarter-wave coaxial cavity resonator for use as an ignition source for an internal combustion engine 
I think all this stuff about transmission line spark plugs is fab - such a refreshing change to all those dreary laminated cores drowning in oil inside a tin can like so many copper and iron sardines.
Re: Electronic ignition thread
Sulaiman, Sun May 19 2013, 07:22AM
Although there are possible benefits with multiple ignition sparks
I believe that a reliable spark at the correct time is better.
How will you map the ignition timing to the engine for different speed/load/demand?
I worked on an ignition system that does not need a map,
fit a piezo-sensor to the block to detect pre-ignition ('knocking', 'pinking' etc.)
with a micro and crank position sensor keep advancing the spark until pre-ignition then keep the engine on the edge of pre-ignition.
This gives the maximum power and efficiency for any air/fuel ratio.(best spread of flame front)
This was using a 70's cpu and I don't think that we patented it.
I haven't re-visited this area for decades (can't even remember the best frequency range for pre-ignition detection) but thought it may interest you.
Don't forget, any electronic delays are equivalent to timing delays
(time between 'spark' command and actual ignition spark occurence)
(e.g. @6000rpm 1rev.=10ms, so 100us delay = 3.6 degrees timing error relative to low rpm)
We tried something similar with feedback control of a carburetor air/fuel ratio based on feedback from a CO/NO sensor, but the response was too slow.
Re: Electronic ignition thread
Ash Small, Sun May 19 2013, 09:52AM
Thanks, PM, I've been reading some papers and associated patents relating to QWCCR, but I think I'll stick to conventional spark plugs for now.
Sulaiman, The piezzo-sensor concept also sounds interesting. I can implement 'mapping' or other forms of advance/retard control later if required. All it involves is a sensor at ~40 degrees BTDC, and an algorythm to delay the spark. (along with other sensors like gas flow meters, Llamda sensors, etc.)
Initially I'll run with fixed ignition, or manual advance/retard. (A lot of racing engines actually run with fixed ignition, especially if maximum torque is at low RPM.)
Multiple spark ignition systems do give a better burn, especially at leaner mixtures where ignition is more difficult, and will allow more advance before pinking, etc.
As I see it, there are basically three ways to achieve multiple sparks:
Some form of spark tank that is charged initially, and then rings until it decays.
A high speed coil that is fired repeatedly for a short burst of sparks.
Gradually charging a tank until breakdown is achieved, then continuing to supply power to maintain the discharge for a brief period.
Most of the systems currently available seem to be similar to the third option mentioned above, but I may experiment with the other two options.
Re:
Electronic ignition thread
Ash Small, Sun May 19 2013, 07:24PM
Well, the simplest solution I can think of, and I've no idea if it will work, is to trigger a 555 monostable with the ignition sensor, points, or whatever, the monostable then turns on a 555 astable for ~one millisecond, the astable is set to ~150kHz, so in one millisecond it switches ~150 times. This drives a 1200V MOSFET, which switches a flyback (wound on N87 core material?) primary which is fed from ~300V(?). Flyback secondary connects to spark plug.
]pdf_n87.pdf[/file] (N87 datasheet)
This will give a burst of 150 sparks in one millisecond every time it is triggered, or will it?
Can anyone point out any expected problems?
I know I'll be 'pushing' the ferrite, but duty cycle is less than 5% so a bit of overheating shouldn't be a problem.
What problems can I expect?
Re: Electronic ignition thread
Proud Mary, Sun May 19 2013, 08:19PM
Each pulse will have an oscillatory tail of damped waves, so you'd have to check that the gap is extinguished when you want to be.
Re:
Electronic ignition thread
Ash Small, Sun May 19 2013, 09:10PM
Proud Mary wrote ...
Each pulse will have an oscillatory tail of damped waves, so you'd have to check that the gap is extinguished when you want to be.
Are we talking a millisecond or two here? That won't be a problem at all. Would putting a snubber on the primary help?
Might it actually work if I use a suitable ferrite and get the gap right?
Re:
Electronic ignition thread
Proud Mary, Sun May 19 2013, 10:58PM
Ash Small wrote ...
Proud Mary wrote ...
Each pulse will have an oscillatory tail of damped waves, so you'd have to check that the gap is extinguished when you want to be.
Are we talking a millisecond or two here? That won't be a problem at all. Would putting a snubber on the primary help?
Might it actually work if I use a suitable ferrite and get the gap right?
I don't know what effect (if any) the combustion of hydrocarbon gases inside the arc might have on the extinction of the arc. You'd have to ask someone like Sulaiman that has a good understanding of ignition systems. :)
Re: Electronic ignition thread
Ash Small, Sun May 19 2013, 11:04PM
Five to ten milliseconds shouldn't be a problem here, but I can 'scope it when I get it going.
Re:
Electronic ignition thread
Proud Mary, Mon May 20 2013, 07:07AM
Ash Small wrote ...
Five to ten milliseconds shouldn't be a problem here, but I can 'scope it when I get it going.
Ah, Mr Ash, I found out some info that may help you while I was supposed to be getting on with something else this morning:
There may be time constraints in implementing your multi-spark ignition system. Turbulence may suck the burning mixture away from the plug and if fresh un-combusted mixture is present, it may be ignited by the next spark. Apparently, the sparks need to be less than a few degrees apart to work effectively.
If you look at the relationship between time, angle, and r.p.m., you can see the time constraints imposed: At 1000 r.p.m. the crank will travel 6° in only 1ms. 1° will pass in just 170 µs.
Perhaps multi-sparking may only be effective at low engine speeds.
Re: Electronic ignition thread
Steve Conner, Mon May 20 2013, 07:10AM
The method Sulaiman described, adjusting ignition timing on the fly with feedback from a knock sensor, is pretty much standard in modern car engines.
Ignition of lean mixtures is still a "hot" research topic as far as I know. The classical ignition system produces a quite long duration spark that does a better job of it than CDI. One old trick was to set up the fuel injection system for a "stratified charge": a pocket of relatively rich mixture around the spark plug that would ignite easily and set off the rest.
Lean burn engines ran into some problems when limits were introduced on NOx emissions. A lean mixture makes more NOx and a catalyst does nothing about it.
Re:
Electronic ignition thread
Ash Small, Mon May 20 2013, 10:27AM
Proud Mary wrote ...
Ash Small wrote ...
Five to ten milliseconds shouldn't be a problem here, but I can 'scope it when I get it going.
Ah, Mr Ash, I found out some info that may help you while I was supposed to be getting on with something else this morning:
There may be time constraints in implementing your multi-spark ignition system. Turbulence may suck the burning mixture away from the plug and if fresh un-combusted mixture is present, it may be ignited by the next spark. Apparently, the sparks need to be less than a few degrees apart to work effectively.
If you look at the relationship between time, angle, and r.p.m., you can see the time constraints imposed: At 1000 r.p.m. the crank will travel 6° in only 1ms. 1° will pass in just 170 µs.
Perhaps multi-sparking may only be effective at low engine speeds.
I've read that some of the systems on the market produce 'up tp ten sparks in 0.5mS', and as a starting point I chose 150 sparks in one mS, as this equates to 150kHz, which is easily attainable by the flybacks used in 150kHz monitors, so should be achievable.
This is only a starting point, though, I could reduce the burst length to 0.5mS and still have 75 sparks. Any residual ringing won't be an issue for another 360 degrees or so (on a four stroke engine).
I'm also not concerned with emissions, only increasing power and achieving smoother running, although any increase in burn efficiency will improve emissions. I also don't want additional sensors (at this point) as reliability = simplicity.
In my opinion the 'knock sensor' method is not ideal because a better ignition system would allow more advance, and therefore more power (more reliable ignition at more advance).
The engine in question here was successfully raced (second and two thirds in national championships) with fixed ignition @32 degrees BTDC, and was fitted with an Interspan ignition unit (see link above). (the length of the spark burst is adjustable on these units- they run from a battery pack for reliability, so you set the burst length so you can get to the end of the race. This won't be an issue for me as I'm fitting an alternator).
The engine will also be fitted with carburettors, not fuel injection. Probably SU's, probably two, as it is a parallel twin with a 180 degree crankshaft, which means (I think) that there will be an overlap where the inlet valves on both cylinders will be open at the same time, which means a single carb won't work (from what I've read elsewhere). I will also need two coils, one for each cylinder, as I can't use the 'wasted spark' system used on most 360 degree twins.
I could just fit points and coils, or a single spark electronic unit, but if a multi-spark unit is as simple to build as I've outlined above, I may as well build it as it should have benefits. I can always add 'advance mapping' later if I decide to.
As far as I'm aware I don't need to worry about emmissions regulations, but a multi-spark system should improve efficiency.
The task is now to design and build a suitable flyback transformer, which only needs to run at a maximum of <=5% duty cycle. (realisticly, if I reduce burst length to 0.5mS, and if it's running at cruising speed, it's only ~1% duty cycle, so I should really be able to 'push' the ferrite, etc).
Re: Electronic ignition thread
Proud Mary, Mon May 20 2013, 11:32AM
Perhaps it would help if you drew up an equivalent circuit for the transformer, the HT cable, and the plug, with all the different inductances, capacitances, and resistances, just to make sure it could really fire 150 pulses in a millisecond.
Re:
Electronic ignition thread
Ash Small, Mon May 20 2013, 01:13PM
Proud Mary wrote ...
Perhaps it would help if you drew up an equivalent circuit for the transformer, the HT cable, and the plug, with all the different inductances, capacitances, and resistances, just to make sure it could really fire 150 pulses in a millisecond.
That's easier said than done. The flyback in a 150kHz monitor fires at this rate, but I probably want more volts and amps than these flybacks produce.
My thinking is tha I can reduce secondary windings (and associated capacitance) by dumping huge amounts of power into the primary (some of the other systems I've read about put 300V into the primary). This 'might' enable me to use a 'basket weave' secondary, thereby reducing capacitance even further, and assisting in cooling. (see other recent threads on HV transformers/coil winding machines).
I imagine the ferrite will be pushed well into saturation, but at these duty cycles that shouldn't be a problem. As I understand it, the energy is stored in the airgap in a flyback transformer, so getting the airgap right will be the biggest problem. (I think)
I can reduce the frequency if I have to, but 150kHz for 1mS seems like a reasonable figure to aim for initially.
I may be able to push more power through a slower ferrite, which will get hot at these frequencies, but with a duty cycle of only a few % it might work.
I guess I need to do some more reading on flyback topology and reluctance, etc.
EDIT: I guess a capacitor accross the spark plug could be of huge benefit in a multi-spark system. Voltage would build up until breakdown was achieved, after which a lower voltage discharge would occur.
Re:
Electronic ignition thread
Proud Mary, Mon May 20 2013, 02:05PM
Here's something that might help you, Mr Ash:
Clarke, John,
A high-energy capacitor discharge ignition system, Silicon Chips, September 1997.
The whole thing fits inside what looks to be an Eddystone diecast metal box, the author provides a circuit diagram and parts list, and claims it produces "beyond 1000 sparks per second", which he seems to think very fast indeed.
As this paper is fifteen years old, I expect you could adapt it to run faster using more recent silicon technology. It would be a place to start.
Re: Electronic ignition thread
Ash Small, Mon May 20 2013, 02:38PM
Yes, that says ~10 sparks in 5mS, but I think I read elsewhere that modern systems produce ~10 sparks in 0.5mS. Also, I think he's using a conventional automotive coil, which isn't fast enough to work efficiently at those discharge rates. I imagine the first spark will be much bigger than subsequent sparks. (The modern systems don't have a separate ignition coil, the HT lead comes straight from the diecast box)
I'm pretty certain that what's needed is something more like the flyback from a 150kHz monitor, which is capable of firing at that rate.
That circuit does suggest putting a 1uF capacitor in series with the primary, though. I may be able to 'borrow' a few ideas from it.
Thanks for posting it, though. I couln't access the 'high res' version.
Re:
Electronic ignition thread
Proud Mary, Mon May 20 2013, 03:04PM
Ash Small wrote ...
I'm pretty certain that what's needed is something more like the flyback from a 150kHz monitor, which is capable of firing at that rate.
Won't a 150 kHz monitor LOPT have diode-split construction, so that the output pulse train emerges as DC?
Re:
Electronic ignition thread
Ash Small, Mon May 20 2013, 03:29PM
Proud Mary wrote ...
Won't a 150 kHz monitor LOPT have diode-split construction, so that the output pulse train emerges as DC?
Yes, I'd assume so, and I'm guessing I'll require ~3 times the voltage, so I couldn't 'just use a 150kHz monitor flyback'.
DC wouldn't be a problem, though, as long as the voltage, current and speed ratings are suitable.
I've only seen a capacitor in series with the primary on push-pull topology before (full and half bridges). I can't see it working with flyback topology, as flyback topology requires that the pulse is switched off at maximum current. A series capacitor would 'snub' any subsequent voltage peak, or does it protect the MOSFET totem pole? Would a series capacitor work with a flyback primary?
Re:
Electronic ignition thread
Steve Conner, Mon May 20 2013, 04:01PM
wrote ...
In my opinion the 'knock sensor' method is not ideal because a better ignition system would allow more advance, and therefore more power (more reliable ignition at more advance)
I have an old book by Sir Harry Ricardo, where he rejects the idea that some ignition systems are "better". He basically says that the mixture either ignites and burns completely or it doesn't. If it doesn't, the result is an obvious misfire.
In other words, if the engine is already running without misfiring, improvements to the ignition system will make no difference to the performance.
Re:
Electronic ignition thread
Proud Mary, Mon May 20 2013, 04:01PM
Don't you think the half-wave rectified DC coming from your 150 kHz LOPT module might view all the stray capacitances and inductances in the ignition circuit as opportunities for a bit of unofficiial filtering to get away from the raw DC look that make it socially unacceptable to most respectable circuit elements? Then where would all your seperate little sparks be - plink, plink, plink, in ze dustbin mitt dem?

Re:
Electronic ignition thread
Ash Small, Mon May 20 2013, 04:21PM
Steve Conner wrote ...
wrote ...
In my opinion the 'knock sensor' method is not ideal because a better ignition system would allow more advance, and therefore more power (more reliable ignition at more advance)
I have an old book by Sir Harry Ricardo, where he rejects the idea that some ignition systems are "better". He basically says that the mixture either ignites and burns completely or it doesn't. If it doesn't, the result is an obvious misfire.
In other words, if the engine is already running without misfiring, improvements to the ignition system will make no difference to the performance.
Sir Harry Ricardo was writing back in the days of magneto ignition. I've run magnetos before and they are brilliant, the spark gets bigger as the RPM increases. I'd require two magnetos for this engine, due to it being a 180 degree parallel twin.
Also it's been proven that bigger sparks/multiple sparks do have benefits. Racers wouldn't bother with them otherwise.
Mass produced engines are built down to a price. All kinds of improvements are possible. This is why racers modify engines and get greatly improved performance from them.
And to get back to the original point, a bigger spark/multiple spark will ignite the mixture earlier, if lots of advance without knock is what's required.
The downside is accelerated electrode erosion, which is something that vehicle manufacturers try to keep to a minimum.
Proud Mary wrote ...
Don't you think the half-wave rectified DC coming from your 150 kHz LOPT module might view all the stray capacitances and inductances in the ignition circuit as opportunities for a bit of unofficiial filtering to get away from the raw DC look that make it socially unacceptable to most respectable circuit elements? Then where would all your seperate little sparks be - plink, plink, plink, in ze dustbin mitt dem?
So is the answer to use an AC (unrectified) flyback transformer, or to opt for a push-pull AC transformer?
I assume it will be easier to reach ~50kV using flyback topology. Do the integral diodes reduce self capacitance in the flyback?
Re:
Electronic ignition thread
Proud Mary, Mon May 20 2013, 05:22PM
Ash Small wrote ...
Proud Mary wrote ...
Don't you think the half-wave rectified DC coming from your 150 kHz LOPT module might view all the stray capacitances and inductances in the ignition circuit as opportunities for a bit of unofficiial filtering to get away from the raw DC look that make it socially unacceptable to most respectable circuit elements? Then where would all your seperate little sparks be - plink, plink, plink, in ze dustbin mitt dem?
So is the answer to use an AC (unrectified) flyback transformer, or to opt for a push-pull AC transformer?
I assume it will be easier to reach ~50kV using flyback topology. Do the integral diodes reduce self capacitance in the flyback?
My point, not perhaps well made, is that as the LOPT frequency increases, the amount of filtration required to turn the output into 'pure' DC decreases, and this is one of the reasons that makes using these much higher frequencies attractive to circuit designers. At 150 kHz, I would expect the amount of filtration provided by stray L and C would tend to produce a 'raw DC' waveform - no clearly separate current pulses as you are hoping for.
I'm no expert on flyback technology, but there are many here who don't feel happy if they haven't fried an LOPT before breakfast, and picked the bacon from their teeth with the charred shards of an overcooked SMPS board. Ask them, Mr Ash! There's lot of 'em in here!
Re:
Electronic ignition thread
Ash Small, Mon May 20 2013, 06:06PM
Proud Mary wrote ...
My point, not perhaps well made, is that as the LOPT frequency increases, the amount of filtration required to turn the output into 'pure' DC decreases, and this is one of the reasons that makes using these much higher frequencies attractive to circuit designers. At 150 kHz, I would expect the amount of filtration provided by stray L and C would tend to produce a 'raw DC' waveform - no clearly separate current pulses as you are hoping for.
Well, that might not be a problem. If we put a capacitor accross the spark plug, it will charge up until breakdown is achieved. Current will continue to flow at a reduced voltage after breakdown. This is pretty much the ideal scenario. Thanks PM.

Re:
Electronic ignition thread
Proud Mary, Mon May 20 2013, 06:29PM
Ash Small wrote ...
Proud Mary wrote ...
My point, not perhaps well made, is that as the LOPT frequency increases, the amount of filtration required to turn the output into 'pure' DC decreases, and this is one of the reasons that makes using these much higher frequencies attractive to circuit designers. At 150 kHz, I would expect the amount of filtration provided by stray L and C would tend to produce a 'raw DC' waveform - no clearly separate current pulses as you are hoping for.
Well, that might not be a problem. If we put a capacitor accross the spark plug, it will charge up until breakdown is achieved. Current will continue to flow at a reduced voltage after breakdown. This is pretty much the ideal scenario. Thanks PM.
Doesn't the spark have to happen at a very precise point on the stroke? That wouldn't happen if you left it up to the spark gap to decide when it wanted to break down - far too many variables, like erosion and/or deposits on the elctrodes, cylinder pressure, ionized gas flow around the electrodes, and so on.
Re: Electronic ignition thread
Steve Conner, Mon May 20 2013, 07:07PM
The book actually includes schematics for a few electronic ignition circuits (one based on tubes!) and has a discussion of CDI vs. ordinary ignition. He mentions that the spark from a CDI system is better at overcoming dirty plugs, but somewhat less effective at igniting weak mixtures, because of its short duration.
It is an old book, but Ricardo was well ahead of his time.
Re:
Electronic ignition thread
Ash Small, Mon May 20 2013, 07:14PM
Proud Mary wrote ...
Doesn't the spark have to happen at a very precise point on the stroke? That wouldn't happen if you left it up to the spark gap to decide when it wanted to break down - far too many variables, like erosion and/or deposits on the elctrodes, cylinder pressure, ionized gas flow around the electrodes, and so on.
Yes, but we're talking ~6uS, I think, between pulses, 360 degrees @ 6000RPM = 0.01S. 1 degree is ~30uS, so even if it takes five pulses before ignition, that would only be one degree, which won't be critical. In reality it should only vary by a pulse or two (I'd expect), so that shouldn't be an issue here.
This engine probably won't be efficient at 6,000RPM anyway, it will delelop most power at around half those revolutions per minute.
The spark plug has ~10pF anyway, so additional capacitance may not be required anyway. Voltage will just increase until breakdown occurs, then current will flow at reduced voltage.
That pretty much resembles some of the waveforms I've seen, so maybe I'm not so far off target?
EDIT:
Proud Mary wrote ...
My point, not perhaps well made, is that as the LOPT frequency increases, the amount of filtration required to turn the output into 'pure' DC decreases, and this is one of the reasons that makes using these much higher frequencies attractive to circuit designers.
Do you have any idea how they drive them at these frequencies? Any 'tricks' they use?
Steve Conner wrote ...
He mentions that the spark from a CDI system is better at overcoming dirty plugs, but somewhat less effective at igniting weak mixtures, because of its short duration.
I'm aiming for the 'best of both worlds' here.
Ricardo was way ahead of his time.
Re:
Electronic ignition thread
Proud Mary, Mon May 20 2013, 11:16PM
I'd always thought that the production of microsecond pulses in the range 25 - 50 kV at some power, as you have proposed, required circuit topologies and techniques rather different to the ones that seem to interest you - such as transmission lines, which I mentioned near the beginning of this thread, or even pseudo-spark switches.
And then again, what advanage would be gained by supplying the sparking plugs with 50 kV?
It's all a bit too deep for me, I'm afraid, but there will be others here who have a clearer idea how you might best proceed with this.
Re:
Electronic ignition thread
Ash Small, Tue May 21 2013, 09:45AM
Proud Mary wrote ...
I'd always thought that the production of microsecond pulses in the range 25 - 50 kV at some power, as you have proposed, required circuit topologies and techniques rather different to the ones that seem to interest you - such as transmission lines, which I mentioned near the beginning of this thread, or even pseudo-spark switches.
And then again, what advanage would be gained by supplying the sparking plugs with 50 kV?
It's all a bit too deep for me, I'm afraid, but there will be others here who have a clearer idea how you might best proceed with this.
You may well be correct, PM. I'm approaching this by reading the claims the existing units on the market, and looking at the claimed waveforms. Also, monitor flybacks operate at these frequencies, although at lower power levels, without the kind of matching networks I assume you are hinting at.
The leads to the plugs appear to be conventional, un-suppressed (copper) HT leads. I've come accross no mention of matching transformers, spark tanks, etc.
The point you make about the individual pulses 'merging' into one long pulse interests me though, as this could/would explain some of the waveforms I've seen. The 'stray' capacitances in the plug, etc. would allow the voltage to rise until breakdown, then the discharge would continue at a lower voltage.
I also can't be certain what peak voltages these units are achieving. Claims of up to 50kV have been made, although breakdown usually occurs at lower voltages,
I guess I'm just going to have to try it and see what happens.

Re:
Electronic ignition thread
Proud Mary, Tue May 21 2013, 10:15AM
Perhaps it would be helpful to first define the needs of the application, and then consider the various ways in which those needs can be met.
What is an ignition system but a pulse generator with external sync?
What is the pulse amplitude, duration, and repetition frequency required by the application?
Once you have defined these basics - adding the fast burst mode pulsing of your particular experiment - you will be in a much better position to choose among the different means of achieving these ends.
So turn off your mind, relax and float down stream, until you come up with the best solution, rather than trying to pin your hopes on a monitor flyback from the outset.
Re:
Electronic ignition thread
Ash Small, Tue May 21 2013, 01:41PM
I've not pinned my hopes on anything yet
The flyback topology is one option. There are two others, one is to just produce one spark, and try to get it to oscillate accross the gap, the other is to use push-pull topology, at the resonant frequency of the stray capacitances and inductances, and ring it up until breakdown, which is what I believe some of the other units do.
I appreciate that, due to the capacitance of the plug, etc. that it might take several pulses from a flyback before the voltage is high enough for breakdown to occur, and that it won't be a clearly set burst of pulses, as they will tend to merge into one,
I'm sure there are plenty of (more complicated) ways to achieve this, possibly 'borrowing' from Tesla coil technology, but the 'flyback topology', due to it's simplicity seems a good place to start, especially since we know it works in monitors at these frequencies.
Re:
Electronic ignition thread
Ash Small, Tue May 21 2013, 07:00PM
I've found a paper on high voltage flybacks with resonant elements, which I'm currently reading:
]1-jpe09133.pdf[/file]
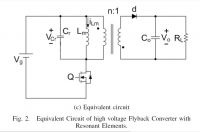
EDIT I think, from reading another paper (I'll try to post it later), that, if the output pulses 'merge' into one, then that constitutes continuous mode operation. The above paper clearly relates to discontinuous mode operation, because the output current drops to zero before the primary switches on, so the above paper is irrelevant here.
Re:
Electronic ignition thread
paris, Wed May 22 2013, 08:28AM
damn!! I was gonna mention silicon chip article by J Clarke.
I thought nissan skylines had ferrite cores and the coil is direct on the spark plug so theres no inductance of the leads etc
I few weeks ago I was reading IH article on polarity of sparks using a pencil = old school tricks

what about the guy who holds the record using cadillac coils , hes up around 100Kv . he might have a few ideas
I reakon youll come up with something interesting, weve been using coil ign for over 100
years .
also Ford model T had the trembler coil that oscillated each "spark" not just once
Re:
Electronic ignition thread
Ash Small, Wed May 22 2013, 10:02AM
paris wrote ...
what about the guy who holds the record using cadillac coils , hes up around 100Kv . he might have a few ideas
I've not read about that, but Terry Fritz got 250kV out of an HEI coil after removing the core completely:

Re: Electronic ignition thread
paris, Wed May 22 2013, 08:52PM
thats the guy ,thought Id be conservative and say 100kv . :)
so air cores are the way to go hmmm....
Re: Electronic ignition thread
Steve Conner, Wed May 22 2013, 09:26PM
I've worked on motorbike engines that had the coils mounted directly on the plugs. I don't know about the Skyline GTR, but my humble Swift Sport has one coil per plug, mounted separately with short flying leads to the plugs.
Many modern engines have a "coil pack" that combines one coil per plug and IGBTs to drive them from logic-level signals provided by the ECU, into one big, expensive, unreliable plastic lump.
Another popular device is the double-ended coil. Each end of the secondary winding drives one spark plug. Since the gaps are effectively in series, they always fire together, but only one has anything to ignite. This is known as a wasted-spark system.
I once had a fine head-scratching time trying to get a Honda ECU designed for two double-ended coils to fire four single ones.
Re: Electronic ignition thread
Aragorn, Wed May 22 2013, 10:01PM
I think the biggest gains to be had here (in power and economy terms) will come from having proper mappable spark timing which you can properly adjust against load and rpm.
Having some massive spark at the wrong time is not going to help you extract maximum power from the engine, and fixed spark timing is a massive compromise, much like Carburettors over EFI.
You should be looking at something like Megajolt, driving an individual coil-per-plug (or coil-on-plug) or a wasted spark type arrangement as Steve mentioned in his post.
While you are right in suggesting that modern engines are built to a price point, THE biggest factor in any modern engine design is fuel economy, and a big part of that means optimising the spark timing to eeke out every last drop of energy from the injected fuel quantity. Those aims are exactly the same as trying to get maximum power.
Re:
Electronic ignition thread
Ash Small, Wed May 22 2013, 10:56PM
paris wrote ...
thats the guy ,thought Id be conservative and say 100kv . :)
so air cores are the way to go hmmm....
I've been considering some form of 'Tesla coil' ignition system, but I think I'm starting to 'get my head round' the 'black art' of flyback design.
Aragorn wrote ...
While you are right in suggesting that modern engines are built to a price point, THE biggest factor in any modern engine design is fuel economy, and a big part of that means optimising the spark timing to eeke out every last drop of energy from the injected fuel quantity. Those aims are exactly the same as trying to get maximum power.
I disagree on two points. Firstly, while correct 'mapping' will give the best performance, a bigger spark helps considerably, and doesn't take so long for full combustion to occur, so can be more retarded, but will also ignite the fuel at more advance. Also, a longer burn spark (or 'burst') will ignite leaner mixtures. The 'mass producers' of vehicles have two objectives. one, keep costs down. two, smaller sparks = longer spark plug life = greater reliability over time.
EDIT: My current thinking is that you only require sufficient voltage to achieve breakdown, from the point of breakdown you want as much current as possible.
Re: Electronic ignition thread
paris, Wed May 22 2013, 11:41PM
the international harvester link I put up also talks about the thermionic emission theory especially with wasted spark ignition.
1 electrode has to emit electrons thats why they come up with diff metals for spark tips. theres a pencil trick for polarity too.
I like the possibilities your conjuring up even tho I cant see anything at the mo
Re:
Electronic ignition thread
Ash Small, Thu May 23 2013, 12:35AM
This is an interesting article:

I've read quite a few, and it's looking quite promising. I still have a few questions, eg 'right half plane zero'?

etc..If I can't answer them by googling, I'l post some questions tomorrow.
Steve Conner wrote ...
I once had a fine head-scratching time trying to get a Honda ECU designed for two double-ended coils to fire four single ones.
The way to get a bike that was set up for four coils to run the 'wasted spark system' is to use two six volt coils in series (on a 12V system).
The same for double ended coils.
Re:
Electronic ignition thread
Steve Conner, Thu May 23 2013, 07:45AM
Ash, yes, we ended up connecting the primaries of the coil-on-plug units in series pairs to emulate the double-ended coils. It worked fine even though the coils were only getting 6V each.
We started out with them in parallel pairs, but that gave some really weird symptoms. The plugs seemed to spark fine when we tested them out of the engine, but the engine just wouldn't run. Turned out that all the magnetic energy stored in both coils was dumping into whichever gap broke down easiest: the one in the cylinder that wasn't under compression and ready to fire. It was the ultimate wasted-spark system: every single spark was wasted.

I tend to side with Ricardo. I don't think a bigger spark ignites the mixture better, and I don't believe the claims of super ignition systems that add horsepower. Combustion is an all-or-nothing affair. The hot, compressed fuel-air mixture is basically ready to explode. If the spark is strong enough to ignite even one tiny bit of it, the whole lot will go off, and you'll get all the horsepower. If the spark isn't strong enough, nothing will happen.
To be sure, some engines need super ignition systems. A F1 engine at full speed needs almost 1,000 sparks per second, which requires a lot of power. One coil per plug helps a lot, by splitting the problem into 8 ignition systems each firing at 125Hz.
And a nitro-burning dragster probably needs some serious voltage, because the charge is so dense and highly compressed, giving it a high breakdown strength. Although I've heard it said that nitromethane is so volatile, and the compression so high, that once the engine really got going, turning off the ignition would hardly make a difference.
But a twin bike engine running off pump gas is nothing special from an ignition point of view.
Re:
Electronic ignition thread
dex, Thu May 23 2013, 09:31AM
Ash Small wrote ...
paris wrote ...
what about the guy who holds the record using cadillac coils , hes up around 100Kv . he might have a few ideas
I've not read about that, but Terry Fritz got 250kV out of an HEI coil after removing the core completely:

13" rod gap has 50% breakdown voltage somewhere between 175 kV and 230 kV (single shot).
therefore,200 kV figure would be better estimate.
except gap geometry and polarity ,breakdown voltage depends also on impulse shape.
Re:
Electronic ignition thread
Ash Small, Thu May 23 2013, 09:42AM
Steve Conner wrote ...
If the spark is strong enough to ignite even one tiny bit of it, the whole lot will go off, and you'll get all the horsepower. If the spark isn't strong enough, nothing will happen.
But a twin bike engine running off pump gas is nothing special from an ignition point of view.
I've run twin bike engines with every type of ignition system there is, fixed ignition, manual advance/retard, mechanical auto-advance and electronic ignition with auto-advance, magnetos, and points and coil.
The best were magneto and electronic ign., and a correctly mapped advance does have advantages, but a weak spark ALWAYS causes problems with erratic running. a bigger/longer spark results in a hotter flame front which travels through the mixture quicker, resulting in quicker and more complete combustion under any conditions.
I basically have three choices here:
fit points and coils.
fit/build some form of electrinic ignition pickups and amplifier.
look into building something along the lines of the MSD/Interspan multi-spark racing units mentioned at the beginning of this thread.
We are talking here about big twins and singles here, fairly low revving engines that produce bucket loads of torque at low RPM, and a lot of people who race them find that fixed ignition, but with a big spark gives the best results. I was initially surprised myself when I found out that Hunt magnetos, which many people fit to Harleys for better performance are fixed ignition. As you said yourself, Steve, a longer duration spark will ignite leaner/weaker mixtures, and a higher voltage spark will overcome dirty/fouled plugs, etc., so there are advantages to be had.
I certainly wouldn't advise fitting fixed ignition to an F1 engine, or any other engine where maximum power is at high RPM, but I'm sure that one of the variables in the complex engine management systems they use is variable length sparks, etc. especially when they are running in 'fuel conservation mode'.
I've pretty much ruled out using a complex advance mapping system here, because fitting all the required sensors, and everything else involved just isn't worth the effort. This is a big, low revving twin that will run quite happily on fixed ignition, or manual advance/retard.
When I used to run fixed ignition on twins, if I was going on the motorway, I'd pull over and adjust the timing to 38 degrees BTDC, then, when I came off the motorway, I'd pull over and retard it again, to make the engine more flexible around town or the country lanes or whatever. You don't need 100 plus BHP in those conditions, just a flexible, low revving engine with loads of torque.
This engine, which is by far the biggest capacity twin I've had, was raced successfully with fixed ignition of 32 degrees. It doesn't have anywhere I can easily fit a magneto to, but did come with Interspan pickups for a 360 degree crank with 'wasted spark'. It also came with a 180 degree crankshaft and camshafts. the two choices I have are to either fit two sets of points, or two pickups. (or buy a 360 degree crankshaft and cams, easier said than done).
Due to these constrictions, and baceause the timing won't always be at the optimum advance, and because of the risks of fouled plugs, and to allow me to run leaner mixtures, a hotter, longer lasting spark sounds like the best plan, although I wouldn't necessarily reccommend the same approach for a high revving multi-cylinder engine.
If I am to build some form of electronic ignition amplifier, a multi-spark system does seem to make the most sense. After all, the racers wouldn't use them if they didn't have advantages. The downside, as I've mentioned before, is accelerated erosion of the electrodes.
EDIT: When it was racing, this engine ran on methanol, but multi-spark systems are also used with petrol/gasoline.
dex wrote ...
except gap geometry and polarity ,breakdown voltage depends also on impulse shape.
Can you enlighten us further regarding this point? Specifically, what impulse shape is best?
Re:
Electronic ignition thread
dex, Thu May 23 2013, 11:35AM
Ash Small wrote ...
Specifically, what impulse shape is best?
in what sense "the best"?
Re:
Electronic ignition thread
Ash Small, Thu May 23 2013, 11:56AM
dex wrote ...
Ash Small wrote ...
Specifically, what impulse shape is best?
in what sense "the best"?
The best for lower breakdown voltage.
Re:
Electronic ignition thread
dex, Thu May 23 2013, 12:15PM
Ash Small wrote ...
The best for lower breakdown voltage.
for spark gap,short impulse,systems i don't know.speaking generally,it is probably qcw mode with a long excitation time.
Re:
Electronic ignition thread
Steve Conner, Thu May 23 2013, 12:26PM
I think the voltage will be limited by what would flash over the spark plug insulator on the outside. Maybe 50kV or so in clean dry lab conditions. Out on the road, who knows?
If I wanted big sparks, I'd just buy a heavy duty double-ended ignition coil like a MSD Blaster, and use plain copper ignition leads, not the ones with resistive cores. It will kick out a lot of RF interference, but with a good-sounding engine there is no need for a radio.

Drive it with an optical sensor picking up reflective patches on the flywheel, and some variant of the old Lucas transistor ignition amplifier, using an IGBT. (Ignition IGBTs with built-in overvoltage protection are available and used in almost all modern car ignition systems.)
Re:
Electronic ignition thread
Ash Small, Thu May 23 2013, 02:39PM
Steve Conner wrote ...
I think the voltage will be limited by what would flash over the spark plug insulator on the outside. Maybe 50kV or so in clean dry lab conditions. Out on the road, who knows?
If I wanted big sparks, I'd just buy a heavy duty double-ended ignition coil like a MSD Blaster, and use plain copper ignition leads, not the ones with resistive cores. It will kick out a lot of RF interference, but with a good-sounding engine there is no need for a radio.

Drive it with an optical sensor picking up reflective patches on the flywheel, and some variant of the old Lucas transistor ignition amplifier, using an IGBT. (Ignition IGBTs with built-in overvoltage protection are available and used in almost all modern car ignition systems.)
Well, the MSD Blasters claim 45kV. A double ended coil with wasted spark is no good here because it's a 180 degree crankshaft, so I'll need two of everything. I use copper cored HT leads anyway (although the suppressed ones do make good HV resistors

).
I'll have to drive it from the exhaust camshaft, to get the correct timing (pickups/points set at 90 degrees on the camshaft = 180 degrees +540 degrees (720 degrees total) on the crank. I believe the reluctor shape on the old Lucas units provided the advance/retard curve, the amplifiers themselves had no advance mapping or anything (Lucas RITA units).
That is the 'Plan B', if I need one, though.
Re: Electronic ignition thread
Aragorn, Thu May 23 2013, 02:44PM
Your point about modern engines running smaller sparks doesnt agree with my findings in the world of VAG 1.8T engines, and i'd expect you'd find the same in general across most manufacturers.
The first models using that engine built ~95-'00 had simple dumb coils (one per cylinder), with an external IGBT module like steve describes, in this case mounted on top of the airbox with a big heatsink.
These worked well enough, but later they switched to a combined Coil/IGBT unit for each cylinder. Many folk have converted to the newer system in search of stronger sparks, because when tuning the engine waay beyond how it left the factory, the dumb-coil setup starts to struggle, requiring the spark gap to be closed right down to prevent missfires.
These later coils still suffer issues, at big power levels, and very recently, people have started experimenting using the coils from the newer direct injection "TFSI" engines, which are an almost direct drop in replacement for the combined coil/IGBT units, and have found further increases in spark strength. The TFSI engines use larger spark gaps from the factory (1mm vs 0.8mm), and as a result the coils are more powerful to match. The end result being you can retain the stock gap, and get smoother running without missfires at big boost pressures.
Theres most certainly a move towards stronger sparks, certainly in turbocharged engines, and concerns over electrode wear are largely mitigated with most vehicles coming from the factory with platinum spark plugs, which in the factory tuned engines can last for 60-80k miles.
Re:
Electronic ignition thread
Ash Small, Thu May 23 2013, 04:12PM
Aragorn wrote ...
Many folk have converted to the newer system in search of stronger sparks, because when tuning the engine waay beyond how it left the factory, the dumb-coil setup starts to struggle, requiring the spark gap to be closed right down to prevent missfires.
I didn't mean they use smaller sparks, just that they can't justify the cost of more powerful systems with platinum plugs, or whatever, on most mass-produced vehicles, and therefore resort to compromises like anti-knock sensors, etc.
Closing up the gap increases the dwell angle, which allows the coil to 'charge' to a higher voltage before discharge. Turbo engines (or any engine with a higher effective compression ratio will require a higher voltage spark before discharge occurs.
I think we're mostly in agreement regarding the advantages of bigger/longer sparks here.
Re: Electronic ignition thread
Sulaiman, Thu May 23 2013, 07:01PM
Steve, " and some variant of the old Lucas transistor ignition amplifier "
I was part of the team that developed that amplifier !
the designer of the green logo on the heatsink earned more than my annual salary at the time!
This project is why I left, it was to have been part of a simple reliable fully electronic system to replace the complex un-reliable electronic/mechanical system in production,
unfortunately the designer of the old system was promoted to a position where he could keep his baby in production - effectively blocking development.
+1 to using ignition igbt.
I think that;
a double-ended coil would not give the spark performance of two separate coils
you will have significant insulation problems, especially in wet conditions
smearing everything in "vaseline" (petroleum jelly) helped, and can be cleaned off.
some spark plug types are much better than others .. I'm out of date
choosing the 'temperature' (hot/cold) of the plug is also important for reliable ignition.
Theoretically,
a small cap near the plug with inductance between the ht/lead/cap and plug
forms an rf resonant tank .. more plasma-like than arc-like .. difficult to physically implement reliably, or at least it used to be, not up to date.
Re:
Electronic ignition thread
Ash Small, Thu May 23 2013, 07:36PM
Sulaiman wrote ...
I was part of the team that developed that amplifier !
Are we talking about the RITA system, Sulaiman? If so, can you confirm whether the ignition advance was controlled by the shape of the reluctor? This is what I was told when I bought mine. ( I think mine was the '5PU' type with 'AB11' amplifier.)
Re: Electronic ignition thread
paris, Thu May 23 2013, 09:37PM
Ash,
61 - 64 Harley had 2 coil/2 points/2 caps and 1 lobe.
Crane ign today uses the fly weights but replaces points with a plastic disc with 2 small magnets that trigger a sensor.
180 degrees must be BMW .....or zundapp altho theyre a 170 degree v twin
Re:
Electronic ignition thread
Ash Small, Thu May 23 2013, 10:16PM
paris wrote ...
180 degrees must be BMW .....or zundapp altho theyre a 170 degree v twin
No. Although the crank on a BMW IS 180 degree, the cylinders are also opposed by 180 degrees, so a BMW actually fires like a 360 degree twin.
This is a parallel twin with a 180 degree crank, so one piston rises as the other falls. (recent innovations have also seen 90 degree, and even 76 degree cranks, in attemps to improve balance factors).
I have read, this afternoon, that I could run a wasted spark, as long as I don't run it on methanol.....but I've only read that once so far.
Re: Electronic ignition thread
paris, Fri May 24 2013, 01:35AM
I never knew there was such a thing = learning some thing every day
swear to god Im not going off topic ...... Pendine sands (UK) is happening june 22 , 3 x Indians so far .
Re:
Electronic ignition thread
Ash Small, Fri May 24 2013, 09:30AM
Thanks for that info Paris. The link to the official website for the event is here:

Will you be there?
EDIT: There is also this event for cars coming up in September:

EDIT: Paris, are you FLH on HAMB?
EDIT: There is a post (dated 5-11-06) in this thread comparing 90 degree and 76 degree cranks in the same parallel twin engine. The 76 degree crank was smoother. Offhand, I think the cylinder angle on a Harley is also 76 degrees. There is another thread on the same forum discussing the theory involved, somewhere.
EDIT: Here's a theory thread....not sure if it's the same one I read before, but loads of info:

Re:
Electronic ignition thread
Steve Conner, Fri May 24 2013, 04:06PM
What's the deal with the 180 degree crank? Does it make the firing times of the two cylinders close enough together that in a wasted-spark system they would both have ignitable mixture in them when the spark goes off? If this is the case, you could be shooting some impressive flames out of your carbs.

Re:
Electronic ignition thread
Ash Small, Fri May 24 2013, 04:21PM
Steve Conner wrote ...
What's the deal with the 180 degree crank? Does it make the firing times of the two cylinders close enough together that in a wasted-spark system they would both have ignitable mixture in them when the spark goes off? If this is the case, you could be shooting some impressive flames out of your carbs.

I think the theory goes something like 'because the two pistons aren't going up and down together, you don't need so much counter-ballance on the crank, so the crank is lighter, so acceleration is quicker. The 90 degree and 76 degree cranks mean you can go lighter again, as one piston is stationary while the other is at maximum speed'. The current discussion is over whether 90 or 76 is better.
I was reading yesterday that, if running on methanol with a wasted spark, the cylinder 180 degrees behind would also be ignited, but, according to that article, if running on petrol/gasoline, it wouldn't be a problem. I think I read earlier today that someone is running a 90 degree crank with wasted spark, but I'd have to check again.
So I may be able to run a wasted spark system after all. (but do I really want to waste sparks?...I might if I'm running a 'conventional' ignition system, but it may to too much for what I'm trying to build here.)
Re:
Electronic ignition thread
Steve Conner, Fri May 24 2013, 07:19PM
Well, if you're willing to go to the extra complexity of two timing pickups, two amplifiers and two coils, there is no reason to use a wasted spark system. You'll get more power because each coil only fires one gap, and they have more dwell time to charge.
I still don't believe that a bigger spark can provide the same benefit as a knock sensor. Having a knock sensor to regulate the timing means the engine can run right on the edge of detonation all the time, giving the maximum fuel efficiency and torque.
Without the knock sensor, you have to set the timing so it won't detonate excessively at full throttle and low RPM. This can mean it ends up too far retarded for maximum power output. Retarded timing means the mixture gets ignited too late, and never gets a chance to do its work on the piston before it is thrown away down the exhaust. This is why the centrifugal advance was invented.
This probably doesn't matter a great deal in a racing engine that will always be revving in its powerband, and probably doesn't like running at low RPM anyway because of its racing cams. It is probably OK to set the timing for max horsepower and leave it there, but don't expect a smooth ride to the shops.

The only time a more powerful ignition system helps is as mentioned earlier, when high compression or supercharging give a charge so dense that a standard ignition system can't force a spark through it reliably.
Re: Electronic ignition thread
paris, Fri May 24 2013, 09:18PM
Ash = yep! I have a FLH , thats why Im interested in the out come of this . Theres 3 indians running at Pendine , one is Grizz on 27 Chout (chief Mot / Scout frame) be great to be there. Im building a 26 scout at the mo.
Im not gonna ask what your bike is I want to figure out the mystery in time, a who done it ? thread
Re:
Electronic ignition thread
Ash Small, Fri May 24 2013, 11:05PM
Steve, firstly, mechanical advance/retard with bob weights and springs never worked, not as intended, anyway. At low rpm the ignition would be retarded (mostly), above 300rpm they'd be at full advance, and in between, where you want a smooth advance curve, they'd be all over the place, due to power pulses through the crank, and everything else that's going on. Electronic advance/retard is another thing though.
Secondly,while you are correct about most of the points you make, initially, I'll fit a manual advance/retard lever, which, in my opinion, is much better (in some applications) than any mechanical system. You are correct about the racing cams and high compression ratio, which is why I'll keep the ignition retarded so that it will be rideable around town, etc, where you don't require anything like full acceleration. This should also take the edge off of the exhaust, which will be 'anti-social' at the best of times. I've also not yet completely ruled out fitting a supercharger, although I have no short term plans to do this. (I would need to fit a 360 degree crank and cams first, unless I fit two blowers).
I'ts not so much the 'do I need it?' (who NEEDS a bike like this anyway?), but the 'can it be done?' and the 'What difference will it actually make?' that are the reasons for this thread. (and the other one on 555 timers, etc.)
And what was the reason you gave for building a Tesla coil?
I've built several points and coil based ignition systems in the past, it's time to try building an electronic unit.
Paris, It's only a couple of hours from here, I'll look out for the Chout.
EDIT: Steve, How would you drive the Z-FETS I mentioned in the 'other' thread?
EDIT: Paris, What is it with you New Zealanders and 'the world's fastest Indian'?

Re:
Electronic ignition thread
Steve Conner, Sat May 25 2013, 02:00PM
This reminds me of years ago when my dad and I finally figured out the ignition timing (or lack of) on the family Vauxhall Nova. It was never quite right since the conversion to unleaded fuel, which basically involved turning the distributor a bit to retard the timing.
Eventually we figured out that the timing was changing as the points wore down. At one extreme it would pull like a (1.0 litre

) train accompanied by loud knocking. At the other extreme it would buck like a kangaroo when accelerating away from traffic lights (no doubt due to the centrifugal advance) and refuse to start on cold mornings. Somewhere in between was a sweet spot, shrunken by the unleaded conversion.
The method we eventually came up with was to fiddle with the points and then razz up and down a steep hill to see how much power we were getting. If it knocked, the gap was too wide, if it bucked the gap was too narrow.
After 134,000 miles of this "tuning" method the car was a rust bucket but the engine was still going great.

Re: Electronic ignition thread
Ash Small, Sat May 25 2013, 02:25PM
Yep. that's the beauty of a manual advance/retard lever, you just adjust it to suit the conditions. I'm not saying it's better than a properly mapped electronic system, but it does give you more control.
This engine will need to be retarded, just to make it drivable around town, etc.
Re: Electronic ignition thread
Steve Conner, Sat May 25 2013, 02:41PM
I agree, a manual timing adjustment would certainly have been better than the random timing on the old Nova.
Might be tricky to implement on an electronic ignition system though. Maybe you could have a pickup that gave, say, 10 pulses spaced evenly over the range you would want to adjust the timing, a digital counter that would fire the ignition after N pulses, and a 10 position rotary switch to set N.
Re:
Electronic ignition thread
Ash Small, Sun May 26 2013, 11:15AM
Steve Conner wrote ...
I agree, a manual timing adjustment would certainly have been better than the random timing on the old Nova.
Might be tricky to implement on an electronic ignition system though. Maybe you could have a pickup that gave, say, 10 pulses spaced evenly over the range you would want to adjust the timing, a digital counter that would fire the ignition after N pulses, and a 10 position rotary switch to set N.
In the past I've just mounted the points plate on a large ID roller bearing, with a cable and return spring. Set it to full advance when the spring is pulling against the stop, and adjust a lever (like an old lawnmower throttle lever) to pull the cable to retard the ignition to where you want it.
The same system could easily be implemented using pickups.
Re:
Electronic ignition thread
Avalanche, Mon Jun 03 2013, 06:45PM
I've been trying to dig out some information for a motorbike ignition system I built back in 2008, but all I have been able to find is the software.
It's not that important, because it didn't work (or at least, it worked well until I enabled the advance/retard part of the code).
The pickup was in the form of a reflective piece stuck to the flywheel, and an optical transistor/photodiode combo. The ignition system itself was implemented on a PIC microcontroller, using the CAPCOM module to work out the speed of the engine. A single interrupt which occurred at TDC was used to both calculate the engine speed, and work out a delay until beginning the ignition sequence for the next rotation. The ignition sequence consisted of a fixed 3mS delay for 'core magnetisation' followed by the switch-off and spark. Ideally this should have occurred in the right place, i.e. the right number of timer 'ticks' before the TDC interrupt - and the software used number of ticks between spark and TDC interrupt as an error signal for the timer control.
The problem was that on the single cylinder engine I tried it on (old Honda CG125) the engine speed could change too much in one revolution - so it was completely unstable and impossible to start! I always imagined it being completely stable whilst running at a constant speed though... not much use in reality! A more accurate speed measurement would have been required for any sort of 'predictive' advance/retard like this.
In the end I cheated, and re-arranged the optical pickup to generate an interrupt at I think 20* BTDC, and always 'spark' on this interrupt. That worked great, but I found the CG engine absolutely requires working advance/retard to rev beyond about 2000RPM.
Hardware wise, I had the original '6V' coil on a 12V system switched with a power MOSFET, and from testing I'd already found that the necessary delay was 3mS to magnetise the ignition coil. Any longer and it would saturate and probably pop the MOSFET so the 3mS was fixed before sparking. The MOSFET was driven from an opto-isolated gate drive IC, and the floating gate drive supply was provided by one of those little 1W DC-DC converters, which was a bit of a cheat. As a fixed ignition system it worked great!
But with advance/retard it was a complete failure. Here's a block of comments from the code that says it all :
/* Variable Initialisations */
/* The values chosen here should roughly match the starter motor */
/* speed, or the predicted kick start speed, to make the engine */
/* easier to start. 25000 ticks = Approx 300RPM */
Well it was impossible to start and kept trying to break my foot when I tried

Re:
Electronic ignition thread
The Lightning Stalker, Mon Jun 03 2013, 09:38PM
Sorry I'm late to the thread, but I have
a circuit which works very well. With some slight modifications, it should be able to do whatever your little heart desires. Sorry about the ad whoring, but it makes me some money.
Re:
Electronic ignition thread
Steve Conner, Tue Jun 04 2013, 07:47AM
Avalanche: Yup.

As far as I know, commercial systems use a magnetic pickup with several teeth distributed over the range of crank angle where sparks are wanted. Each tooth generates one pulse as it passes the pickup, so the software just has to count them, "fire after the third pulse" and so on. Worst case it has to interpolate between two of the pulses, but that's a lot more accurate than extrapolating from TDC using a speed estimate from the TDC before that.
Re: Electronic ignition thread
Sulaiman, Tue Jun 04 2013, 12:28PM
Steve, in the 70's I used an 8048 to do ignition timing using just one 'pickup'/index per revolution,
even at low MHz cpu clock there's plenty of time to calculate the timing based on the previous few cycles
(and the vacuum pickup was also on/off so pulse by pulse incremental advance/retard AND dwell time were simultaneously implemented)
All that in 1K RAM and 64 bytes RAM, I'm sure newer uC can do it easily.
Re:
Electronic ignition thread
Steve Conner, Tue Jun 04 2013, 08:36PM
Sure. The problem is that with one pulse per revolution you can't measure too well how the instantaneous speed varies over the course of a cycle. It actually slows down quite a lot on the compression stroke and then speeds back up on the power stroke.
This probably shows itself worst in cold starting. You get the problem where the piston slows down more than expected, so working on data 1 rev old, the ignition fires it too early and the kickstart tries to break your foot.

Avalanche would doubtless have got better results if he had put his single pickup point, not at TDC, but just ahead of the largest timing advance he would ever want. Say 45' BTDC. That would mean far less time for the speed error to compound itself. The timer would be reset just before firing the spark, rather than almost 1 rev ago.
Re: Electronic ignition thread
Ash Small, Wed Jun 05 2013, 08:51AM
I'd implement firing at ~6 degrees AFTER TDC for the first few revolutions after start-up, and then move to 'mapping' once the engine has fired.
EDIT: I believe a lot of 'commercial' systems have the sensor at TDC.
Re: Electronic ignition thread
Avalanche, Wed Jun 05 2013, 11:43AM
Another drawback that made it tricky for my system was that I could not 'spark on demand', but there was always a fixed 3mS delay (coil 'magnetisation') before sparking. So the number of degrees before or after TDC would always change with engine speed with this fixed 3mS delay, without using some kind of flywheel position prediction from engine speed. In the original 'direct transfer' ignition, the coil was pretty much held in saturation until the points open, but my hardware made this impossible!
If I was doing it again I'd probably eliminate the 3mS delay by building a capacitive discharge system, so the spark energy is stored in a capacitor instead of inductively in the coil, then it could be discharged into the coil so that the spark would occur sooner due to transformer action rather than inductive storage and release (I'm guessing this is how CDI systems work?)
The pickup point 45* BTDC sounds interesting, I'd given up on the idea of a single pickup point but I suppose if it were working on newer data it could be possible.
Re:
Electronic ignition thread
Ash Small, Wed Jun 05 2013, 12:19PM
Avalanche wrote ...
If I was doing it again I'd probably eliminate the 3mS delay by building a capacitive discharge system, so the spark energy is stored in a capacitor instead of inductively in the coil, then it could be discharged into the coil so that the spark would occur sooner due to transformer action rather than inductive storage and release (I'm guessing this is how CDI systems work?)
From what I've read recently, I think the advantage of CDI may be a faster rise time (this is related to the 'volt-seconds' thing I mentioned in the 'other thread').
Re: Electronic ignition thread
MR-ZAPPY, Tue Jun 18 2013, 06:55PM
555 timer set to how often hooked up to a relay controlling power going into a MOT. Connect a microwave capacitor in parallel with the output of the MOT
Re: Electronic ignition thread
MR-ZAPPY, Tue Jun 18 2013, 07:03PM
Oops I kinda screwed up on the comment but what you do is use pots for a 555 timer in astable mode set to the fire rate then you take the output of you 555 timer oscillator and hook it up to a small transistor. The output of the transistor is hooked up to the coil of a realy which is wired in series with the live wire going to a MOT. Wire a Microwave capacitor in parallel with the output of the MOT
Re:
Electronic ignition thread
Ash Small, Tue Jun 18 2013, 11:09PM
Mr.Plasma-CRAZY wrote ...
Oops I kinda screwed up on the comment but what you do is use pots for a 555 timer in astable mode set to the fire rate then you take the output of you 555 timer oscillator and hook it up to a small transistor. The output of the transistor is hooked up to the coil of a realy which is wired in series with the live wire going to a MOT. Wire a Microwave capacitor in parallel with the output of the MOT
An MOT will not run at ~1 MHz. It gets hot at 50Hz. I do think it's possible with flyback technology though.
Re: Electronic ignition thread
MR-ZAPPY, Wed Jun 19 2013, 03:36AM
The 555 is just to turn on and off the MOT around 10 times a second so that is will spark fast the AC is still 50 hz is is just chopped up so that is will go bang bang bang 10 Times a second. That should ignite almost anything
Re:
Electronic ignition thread
Ash Small, Wed Jun 19 2013, 11:21AM
Mr.Plasma-CRAZY wrote ...
The 555 is just to turn on and off the MOT around 10 times a second so that is will spark fast the AC is still 50 hz is is just chopped up so that is will go bang bang bang 10 Times a second. That should ignite almost anything
It's just occured to me that the flyback core from an inverter microwave oven might be worth considering here.
They seem to have two airgaps, one for the primary and secondary, and one for just the secondary. They also have a reasonable CSA.
I'll dig one out, and wire something up.
Re:
Electronic ignition thread
Ash Small, Sun Jun 23 2013, 10:14PM
paris wrote ...
Theres 3 indians running at Pendine , one is Grizz on 27 Chout (chief Mot / Scout frame) be great to be there. Im building a 26 scout at the mo.
Just for you Paris, Here's a photo of Chris Ireland taking his supercharged Indian up the Pendine sands earlier this afternoon.
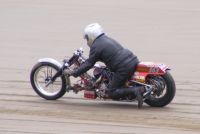
It was an amazing weekend, I've hundreds of photo's. Thanks for the tip-off.
Re: Electronic ignition thread
paris, Mon Jun 24 2013, 12:01AM
Ine been hangin out , wasnt gonna say any thing cause I would sound like an impatient brat but now Im like a giggly girl!!!
chris ireland is a custom guy and magazine editor, that bike "bella" has been reincarnated many times , its 1942 741 army indian 500cc , eventually rat bike chopper(80s) , then custom chopper(90s), then trike ,then salt bike in USA(2012) ,then that bike there,
its a well known bike, even in some books!! also on the net if google bella/chris ireland.
how about Grizz chout?
I am jealous as hell , the sound mustve been great, bet I know where youll be going next year
= hate you in advance :0) cheers
Re:
Electronic ignition thread
Ash Small, Mon Jun 24 2013, 09:00PM
I only saw the one Indian there, but you might appreciate this pic:
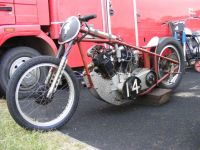
Re:
Electronic ignition thread
paris, Tue Jun 25 2013, 12:02AM
those are the only JAP bikes I truely love!!
grizz has been preparing for 5 years or so.....:0(
feel terrible.....kinda off topic.....but HEY :0)
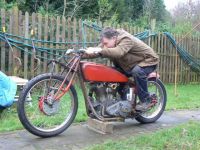
Re:
Electronic ignition thread
paris, Tue Jun 25 2013, 11:38PM
have to do the responsible thing and contribute...
with cars vacuum advance , the plate moves , heres a HD advance = the cam moves and the plate is stationary
heres a crane cams ign module with a plastic rotor that goes on fly weight assembly and has mech advance so the firing as far as I know is just triggered by the placement of the 4 little magnets
pic = std parts on left, the fly weight has a pin sticking out at the centre about 11 oclock , cant see it, that is just a locator pin. the cam lobe has a flat on lower right side that corresponds to that pin just for orientation.
the plastic 1 has the same cut out "flat" so goes in the same and bobs ya uncle!
this is just 1 example of mech advance with out using a hand grip advance.
also... I dont know how the magnets are positioned , degrees etc , what I see is just whats there in the pics, rotor spins 1/2 crank speed so that stuffs my thinking process.
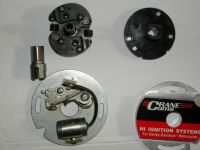
Re: Electronic ignition thread
Ash Small, Wed Jun 26 2013, 10:21AM
I think cars also had the bob-weights, the moving plate was to do with 'vacuum retard' under acceleration, from what I remember.
As mentioned above, the bob-weight system is very 'hit and miss', especially when worn. It will get to max advance by ~3000 RPM, but will be all over the place at lower RPM.
The 'half crankshaft speed' thing, the camshaft turns once every cycle (two revolutions of the crank), so the crank turns 720 degrees for each revolution of the camshaft(s). You still place the timing disc on the crankshaft to measure the number of degrees BTDC or whatever for ignition.
Re: Electronic ignition thread
paris, Thu Jun 27 2013, 08:11AM
your right , I went and got one pulled it apart , dont know what its from , 80s jap car.
wanted to see for myself whats in there .
with ford model T it had a fly wheel magneto with 16 coils so at 1000 rpm , 16 x 1000 / 60 = 266 hz , that went to a comutator on the cam shaft (1/2 speed) from there it went to 4 individual trembler coils each being triggered on , but also the 266 hz is running thru primary so the spark plugs have multi sparks, crude version of what your after.
also the comutator body was connected to a lever onto the steering column for adv retard.
Ive got T fly wheel mag set up Im flogging off at the moment ,weighs 22 kg!!
16 pan cake coils in series.
another idea is twin plug on each cyl but then I spose the racing rules dont allow that for classic racing ,best idea = joe hunt or morris but thats rediculous money
Re:
Electronic ignition thread
Ash Small, Thu Jun 27 2013, 02:33PM
paris wrote ...
another idea is twin plug on each cyl but then I spose the racing rules dont allow that for classic racing ,best idea = joe hunt or morris but thats rediculous money
Not a lot of room for any more plugs
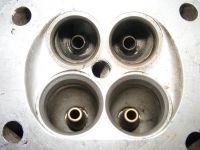
I wasn't actually planning on racing it, but after last weekend.............
I've run magnetos before, but if I can build something out of a MO inverter and an SiC fet, plus a couple of 555's, which sits on the plug, and is fed ~300V from a small SMPS, with maybe a couple of smoothing caps, it should be lighter than a mag and I'll have less rotating mass.
Re:
Electronic ignition thread
Ash Small, Fri Jun 28 2013, 09:52PM
Carburettors arrived this morning, I've just designed some manifolds, but will have to wait until my lathe is here before I machine them.
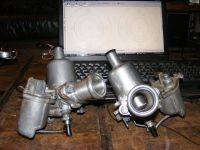
Re: Electronic ignition thread
paris, Fri Jun 28 2013, 10:44PM
hmmm....... 2 cyl / 8 valve / su carb bowls indicate cylinder bank leans forward..... wait and see
Re:
Electronic ignition thread
Ash Small, Fri Jun 28 2013, 11:22PM
paris wrote ...
hmmm....... 2 cyl / 8 valve / su carb bowls indicate cylinder bank leans forward..... wait and see
Those particular carbs will allow me to tilt the engine foreward if I decide to. I have the figure of 15 degrees in mind, but I'm still undecided.
On the subject of 'foreward leaning engines', here's another 'mad' photo from last weekend:
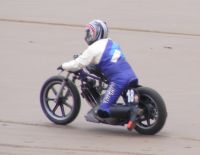
Re:
Electronic ignition thread
Ash Small, Wed Jul 03 2013, 10:09AM
The Champion G63 spark plugs arrived this morning
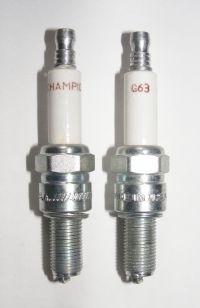
These are un-suppressed racing plugs.
Now I can start making some sparks
Re: Electronic ignition thread
paris, Fri Jul 05 2013, 09:30AM
those are long and no ribs. Are you using flywheel sensor then ? Im guessing the motors in pieces.
Re:
Electronic ignition thread
Ash Small, Fri Jul 05 2013, 10:37PM
paris wrote ...
those are long and no ribs. Are you using flywheel sensor then ? Im guessing the motors in pieces.
Yes, I bought the motor in bits. It seems to be standard practice around here, so you can see exactly what you're buying. I had a choice with some of the parts as well, other cranks, nikasil barrels, and different heads were offered to me. I basically picked the parts I wanted. I've pretty much got everything for the engine now, except the ignition system.
Ignition was previously driven from the exhaust camshaft. The interspan pickups are still there, but configured for a 360 degree crank rather than the 180 degree crank I have.
The plugs are quite long, but the head is pretty thick, and they are angled slightly in the head.
I found this article from 1970 on CDI ignition, which is quite interesting:
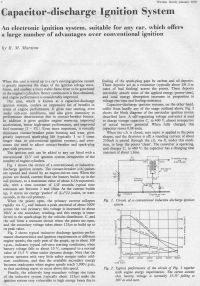
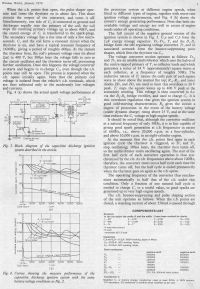
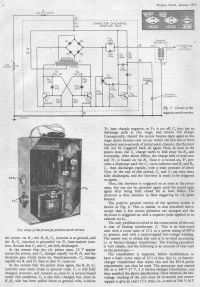
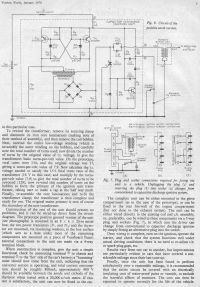
Re:
Electronic ignition thread
Ash Small, Sat Dec 14 2013, 10:59PM
I picked up a clutch for it today, if anyone is still following this thread:
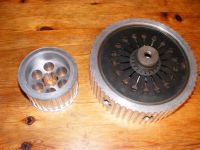
EDIT: If anyone is looking for anything similar, maybe BSA, Norton, Triumph, Godden, Weslake, etc (can obviously be made to fit anything), 'The Man' has a pile of blanks waiting to be machined. As well as diaphragm, four and six spring versions are also available, along with a smaller, lighter version.Maybe I'll post pics of the sealed bearing later. PM for more details.
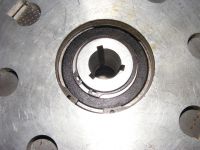
(sealed bearing)
Re: Electronic ignition thread
paris, Sun Dec 15 2013, 01:44AM
"the man" is pretty good!! .....been wondering about the ign circuit , I was not keen to see 2n3055 .
in mean time I went and got a splitdorf mag = 4.5kg spark plug :0)
Re:
Electronic ignition thread
Ash Small, Sun Dec 15 2013, 02:11AM
paris wrote ...
"the man" is pretty good!! .....been wondering about the ign circuit , I was not keen to see 2n3055 .
in mean time I went and got a splitdorf mag = 4.5kg spark plug :0)
I've a few ideas 'buzzing around', but I need to assemble the rest of the bike, so I still have a 'few months' to finalize the details of the 'prototype' ign system. Thanks for the reply, Paris

Re:
Electronic ignition thread
Peter02, Thu Jan 09 2014, 02:00AM
Hi,
i just read this thread with great interest.
Some years ago i was also experimenting with different types of ignition systems. While researching this topic i came across one patent which intrigued me greatly.
https://patentimages.storage.googleapis.com/pdfs/US4589398.pdfAs is already mentioned in this thread, one problem with conventional ignition systems is the impedance mismatch between the ignition coil and the spark plug which leads to energy transfer efficiencies on the order of 1%.
One advantage of these ignition coil type systems is the relatively long burning arc which works quite reliable if the plug is clean.
Whatever, i decided to test this new scheme and build a relatively high energy (about 4 Joules per Pulse) Capacitor discharge system in combination with a normal ignition coil and a peaking capacitor of about 1nf directly connected across the sparkplug.
All of this was fitted to a 1 Cylinder Honda 4-stroke engine at a friends house driving an 3kw Generator.
The difference between the standard magneto and the new system was very noticable.
The exaust gases lost its smell and the engine ran at a higher rpm at the same throttle. This was also testet in comparison to the cdi system without the peaking cap to make sure that the possibly different timing between the magneto and the cdi was not the reason for that.
Another difference was that the engine was able to run with much much leaner air/fule ratios where it did not even start with the magneto or the cdi alone, so that was a very objetive difference.
The next step was to fit the system to a car. The problem here was the limited space for the capacitors and the energy wasted in the distributor which hindered me from getting it to work with a single coil at all. So i have no idea how the advantages would have translated to the car.
here is another interesting paper on the topic:
http://files.uloziste.com/7b1d3568a8a91418/SAE_02ffl_204.pdfWhen i ge the time i will try again to fit such a system into my car with seperate ignition coils to remove the losses of the distributor.
Greetings and a happy new year.
Edit: Sorry for the link issue
Re:
Electronic ignition thread
Ash Small, Thu Jan 09 2014, 03:41AM
Sounds very interesting, Peter. Unfortunately your link doesn't appear to have shown up in your post. Could you possibly either try posting it again, or give me some tips on what to google?
Your suggestions sound very similar to what I'm investigating. Proud Mary suggested a 'peaking capacitor' and I agree that adding some capacitance to the output sounds like a very good idea.
The person I bought this engine from recently told me, when I bought the clutch, that he had the person who owns 'Interspan ignition' at the first race meeting that he tried the Interspan ignition unit at there, and he couldn't understand why it mis-fired.
I've a few ideas I'm working on at the moment, but I'm also researching inductors/Xformers in general. I was thinking about a 'multi-spark' system, but I'd need to 'energise' the primary in ~100nS to make it work, which is 'tricky' to say the least.
As this is a motorcycle the system can't be too bulky, and as it's a 180 degree crank (firing at 90 degrees and 270 degrees) I basically need one ign. system for each cylinder (this was the problem with the Interspan unit, I believe. They did 'crack it' in the end)
The idea I'm working on at the moment is basically to charge a capacitor, then 'dump' it into the primary coil. High compression (~11:1 at the moment) and a lean mixture WILL require a BIG spark to ignite it, (or multiple sparks, which will charge the peaking capacitor until it fires, then continue to provide a 'cleaner burn'.
I'm not too concerned about power consumption as I've managed to fit 1000 Watt alternators to this type of motor in the past.
Please re-post the link.
EDIT:
paris wrote ...
I was not keen to see 2n3055 .
Sorry I didn't pick up on this point sooner, Paris, but some 2N3055's are a lot better than others (I've done my research). I'm not sure I'll use them for this project, though. I'm thinking of 'maybe' using SiC devices, although at least one person here (Steve Connor, if I remember correctly) has suggested this may not be the best option.
Re:
Electronic ignition thread
Peter02, Thu Jan 09 2014, 12:39PM
Hi,
Sorry for the missing links, i have used the Link option in a wrong way and forgot to check because i was nearly sleeping already.
If you want to build a multispark system with 100ns risetime (0 to 20kV) on the peaking cap (if that is what you meant) and you have a peaking capacitor of 1nf for example, you would have peak currents of 180 Amperes on the High voltage site. Translating to a primary of about 1000V would require about 2000 amperes peak current with a current rising speed of over 30kA/µs.
These conditions are not so easy to achieve.
The patent i posted earlier discusses methods to do this in some detail. In my experiment i tried many different phase control SCRs in combination with saturable inductors to speed up the switching of the SCR using the method discribed in this patent:
http://patentimages.storage.googleapis.com/pdfs/US4266148.pdfIt worked surprisingly well and i achieved speeds of up to 5000A/us with 150A/us SCRs but the SCRs still overheated very rapidly when i increased the pulse frequency.
The speed would be managable with Mosfets, but they dont tolerate these high peak currents, and neither do normal IGBTs. They are commonly only rated for Peak currents of 2 times their average currents.
The only good solution i know would be to use Pulse SCRs which do exist with these ratings, as discribed here:
http://mdk2001.web.cern.ch/mdk2001/Proceedings/Session13/Glidden.pdfin the last years i gathered about 400MB of Documents concerning Pulsed Power and Ignition systems But the Problem is still the same: finding the right switch.
The reason why i wanted a fast rising pulse was not to be able to do multispark but to overcharge the gap of the sparkplug to increase power density and reliability (Same spark energy independant of cylinder contitions like pressure, temperature, mixture etc.) as explained in the first patent. Because that was not possible for me i went for the normal approach with a slower pulse and a normal coil.
In my tests with lean fuel i also experienced the problem with increased breakdown voltage of the gap which went as far as the spark jumping outside of the plug across the insulator for a gap electrode distance of only about 0.5mm.
If you want to deliver anything over a few tens of milijoules to the plug the 2n3055 will surely not be the best choice even if you have a very good one. I would start testing with a high power CDI+peaking cap and single spark to see if you can reach your performance goal with that already.
Edit.: I just saw, that the 3055 was only used in that article in the power supply which is not th critical part. Otherwise it is just a standard CDI which uses an old and obsolete 400V 5A SCR (2n3525). If you want to build this i would try to use more modern and readily available parts.
For Pickups i used a hall sensor and a magnet which worked fine, but why not use the existing pickup coil?
Greetings and good luck
Re:
Electronic ignition thread
Ash Small, Thu Jan 09 2014, 07:06PM
Thanks Peter, that's quite a bit of reading and should keep me busy this evening
By the way, at least the first link in your first post still doesn't work, but I did manage to 'copy and paste' it into google. This site does have a few 'idiosyncracies, but we've learned how to live with them.
I agree with your points regarding 2N3055's, I was just pointing out that some are a lot better than others, but none would be suitable as the main switches in anything other than a more conventional transistorised ign. circuit.
Regarding the point you make about "Same spark energy independant of cylinder contitions like pressure, temperature, mixture etc.", as far as I'm aware, breakdown will occur at whatever voltage suits the prevailing conditions 'at that time', and these don't remain constant under all conditions, so voltage rises, due to the capacitance of the plug, assuming no peaking capacitor, which is ~15 picoFarads, if I remember correctly, until breakdown occurs, resulting in more current for lower breakdown voltages. A multi-spark system would also charge the capacitance of plug, plus any peaking capacitor until breakdown occurs, where after any subsequent sparks would be of higher current/less voltage as breakdown has already occured, hopefully resulting in more complete combustion. As you've pointed out, this would be difficult to achieve, owing to the need for very low ESR capacitors and very low inductances for both primary and secondary, although the secondary inductance could be considerably higher than the primary (modern monitor flybacks, from CRT monitors work in this fashion, and produce a 'more or less' continuous output).
The best idea I've come up with so far is to try something like an inverter microwave oven flyback transformer, as these have a relatively large cross section, plus some other 'trickery' that I don't yet understand, like having a second air gap which is only inside the primary, not the secondary (another air gap is inside both).
The ~100nS rise time is only approximate, it could be several times this in practice, but you'd only have a few mS at most for multiple sparks (this is a fairly low revving engine).
The advantage, as I see it of a multiple spark system over a single spark system is that you'd only need to 'dump' a fraction of the energy into the coil on each pulse, but the output wouldn't be much different to a single, longer lasting spark, in reality, and ferrite does seem to prefer higher frequency, lower energy pulses. You'd still require a high voltage from each pulse, but lower current per pulse to charge the peaking capacitor until breakdown/discharge occurs.
I think any kind of SCR is out of the question for a multi-spark system, as you wouldn't be dumping all of the energy in the capacitors into the primary at once. Silicon carbide FET's appear to be the fastest I've seen so far, but the highest voltage devices I've seen are ~1700V, which would limit the primary voltage to ~500V, allowing 3.142 x voltage as a safety margin, if I remember correctly. Volts per turn of ferrite increases with frequency, I think, but I've not done any maths in that department yet. I also need to read up on turns ratios of flybacks as there is some 'trickery' that can be used here too, but I forget the formulas.
I have a Panasonic microwave oven inverter here (~1kW), and some Litz wire, but don't as yet have any suitable capacitors or switches. The plan is to experiment, and see what happens. Insulating the secondary will present more problems, though.
As I said earlier, the main advantage of a multi-spark system with peaking capacitor is that you don't need to dump all the energy into the primary at once.
Now, back to reading those links you provided.
Re: Electronic ignition thread
paris, Tue Jan 14 2014, 08:15PM
fist ful of questions ....is there room in there for dual plugs?
the pic looks pretty tight.
i dont know the guff behind them but can they have smaller gaps , theyre series? smaller gaps in hi comp is what Im thinking.
some coils the sec coil is isolated from pri so the 2 plug gaps complete the circuit...either that or burn out!
Re: Electronic ignition thread
paris, Tue Jan 14 2014, 08:18PM
aww gawd....I see Ive already asked that question at top of page Dooohhhh!
Re:
Electronic ignition thread
Ash Small, Tue Jan 14 2014, 11:26PM
paris wrote ...
aww gawd....I see Ive already asked that question at top of page Dooohhhh!
The answer is still the same, I think, Paris, not a lot of room
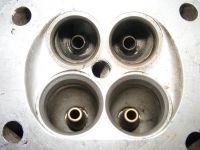
I'm reading up on flyback theory again, but this time from a reference I can easily understand, I think I'm getting somewhere now

,d.bGE&cad=rja
(Thanks to Finn Hammer)
Re:
Electronic ignition thread
Ash Small, Wed Jan 15 2014, 03:40AM
I was tired and confused when I wrote this, and should have put something like 'high impedance connected accross secondary and low impedance connected accross primary', instead of talking about big and small capacitors. The bit about the diodes is not correct either, but I've a clearer picture of the whole idea now. I'll develop this further down the thread.
Sorry about the double post, but 'new information'.
I've been reading the link above, and I think I'm starting to 'get it'.
Firstly, to Steve Ward, I now realise I obviously will need diodes on the secondary, that's how flybacks work.
Now, to summarise, and I'll try to get a schematic, or the beginnings of one, started tomorrow (it's 3:30am here).
suppose you disconnect the transistor from the primary circuit once it turns off (I know, it's just a thought experiment for now, but it makes it easier to understand), and you have a 1:1 turns ratio on primary and secondary, so that
the current on both sides is the same (the transistor does the same thing as a 'blocking diode' does on the secondary when the transistor is off anyway), but you have a 'freewheeling diode' on the primary, that blocks the primary current when the transistor is on, so the 'freewheeling diode' and the diode(s) on the secondary both conduct when the flyback is 'charged' (ie no charging current flowing in the primary), BUT you have a
small capacitor connected to the secondary, and a large capacitor connected to the primary. The voltage generated across the small capacitor on the secondary will be higher than the voltage generated accross the large capacitor on the primary, simple.
Now, obviously you don't disconnect the transistor, but the freewheeling diode and large capacitor will protect it, and the capacitor effectively re-cycles the power it absorbs, and it is available to magnetise the core the next time the transistor switches on. Also, you don't have a 1:1 ratio, primary to secondary, that's just to explain a point.
A small capacitor on the secondary (spark plug capacitance plus 'peaking capacitor' will reach a much higher voltage than a large 're-cycling capacitor' on the primary, and the large capacitor on the primary 'protects' the transistor.
At least, that's where I am at the moment. I'll draw a schematic, but I think I'm nearly ready to start blowing up some silicon.
Of course, if anyone can spot any problems with this, I'd appreciate your comments, and thanks again to Finn for the above link.
Re:
Electronic ignition thread
Peter02, Fri Jan 17 2014, 07:03PM
Hi,
Maybe i dont understand what you mean, but i think you mixed up the flyback and the forward converter.
The flyback converter works the same way as the boost converter but with a transformer instead of a simple inductor.
Lets look at a the basic flyback circuit in the picture with primary switch / transistor Q1, the transformer made from inductors L1 and L2, secondary diode D1 and Output capacitor C1. C2/R2 are only included to dampen the ringing a little bit.
We have a primary Voltage Supply V1 of 100V DC. When the Transistor Q1 switches on, its Drain to Source Voltage (V_DS in the picture) sinks from 100V to 0V, so we have 100V across inductor L1 with the negative potential at the dottet side of it. This voltage drop creates a Current in L1 which rises linear while the switch is on (as predicted by Faradays law of induction : U=-L di/dt or solved for di/dt: di/dt= -U/L). This means that the currents rises faster with higher Voltage on the inductor and also when the inductance is lowered. Since L1 and L2 are coupled and of the same Value, they form a 1:1 Transformer.
Therefore while the switch is on we get 100V across the seccondary as well, again with the negative potential at the dottet site of the coil. This induced Voltage will not find any way to create a current since D1 is in its blocking state for this polarity.
So all that happens ist that current is rising and simultanously a magnetic field is created inside and around the 2 inductors storing energy E=1/2 L * I^2.
Now the Transistor Q1 switches off, but we still have that energy trapped in the magnetic field which needs the current to exist. So the current will continue to flow, driven by the voltage induced by the collapsing magnetic field. This Voltage is now of the opposite polarity as the voltage which created the magnetic field in the first place, so it will be positive at the dottet site of the coils.
Looking at the positive site we see that now the diode will be forward biased since it's anode is connected to the dotted side of the inductor L2 where a positive Voltage appears. Now the current has found a new way to close a circuit and continue to flow. It will charge up C1 starting with the same current which was in L1 at the point Q1 switched off. This process takes energy out of the magnetic field, so the current ramps down again until it reaches 0A and the Whole Energy which was stored in the magnetic field is now transfered to C1. Its Voltage can be calculated with the formula E=1/2 C * U^2.
So we see that while the Magnetic field collapses we have not a fixed voltage on L2 but a voltage as high as necessary to support the current which is needed to hold up the momentarily magnetic field (which is shrinking while losing energy, so the current shrinks too).
This is one complete cycle. It is important to look at the voltage across the Transistor Q1 while the Coil/Transformer discharges. There will be the same voltage across L1 as there is over L2, so at the Drain we will start with a voltage of 100V rising up to the final voltage Of C1 + 100V. This of cource only holds up for a inductance ratio of 1:1.
In the plot you can see the voltages and the primary current of a simple simulatio of the circuit.
i hope that this explanation does not confuse more than it helps.
So one important property of the flyback converter is that the energy is transferred while the switch is open and not while it is closed. To get the forward converter one only has to reverse either L2 Or D1, then the energy would be transferred while the switch is closed and the voltage on the secondary would be fixed according to the turns ratio.
To get a basic understanding of this i would start with looking into the boost converter.
Greetings
PS.: V(n002) in the picture is the voltage across the secondary L2.
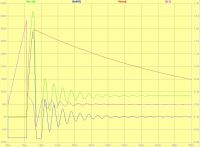
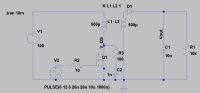
Re: Electronic ignition thread
Ash Small, Fri Jan 17 2014, 11:12PM
Peter, I certainly am confused over that point, and have been for some time. I have been reading exactly what you suggest, as well as some old posts on this forum, and I've also read it is possible to 'recover' energy from the primary, so that the only energy 'used' is that which flows in the secondary. I'm still confused over this point, and I'll look into it further.
But yes, the point about primary and secondary having, for example, the same number of turns, and the same current flows in each, if the secondary has, say, a small capacitor, the voltage will be higher. (I suppose I should say 'if the secondary load has a higher impedance the voltage will be greater'.
This contrasts with the 'general rule' that a 1:1 turns ratio will have the same voltage in the secondary as in the primary.
EDIT: Could you post a copy of the, presumably, LTSpice file, to save me having to start from scratch on a simulation please? I spent most of last night reading up on how to enter coupled inductors into LTSpice.
Re: Electronic ignition thread
Andy, Fri Jan 17 2014, 11:57PM
Ash, not sure if this is helpful, but if you have say two primarys and one secondary all with 1 turn, one of the primarys is driven by ac, the second primary has a switch, close it,it will collpase the primarys field quickly and make more voltage onto the secondary.
Re:
Electronic ignition thread
Peter02, Sat Jan 18 2014, 01:04PM
Hi,
i have attached the LTspice file, and 2 additional links, one explaining flyback operation and converter design in great detail and the other discussing one method of providing a lossless snubber to improve eficciency and lower the voltage stress to the primary switch.



Greetings
Re: Electronic ignition thread
Ash Small, Sat Jan 18 2014, 07:42PM
Thanks Peter. I've had a quick look at the snubber and noticed it has an inductor in it (at least from first impressions). I don't think I've come accross one like it before. I'm more familiar with the diode capacitor resistor types.
I'll read it in more detail later.
EDIT: In my earlier post above, the confusing one, I should have put 'high impedance conected to secondaty and low impedance connected to primary' I think. Maybe that would have made more sense. It was 3:30am and I was tired.
Re: Electronic ignition thread
Ash Small, Mon Jan 20 2014, 02:53AM
post deleted
Re: Electronic ignition thread
Ash Small, Tue Jan 21 2014, 07:09PM
I think I've now 'cracked' tjhe whole 'flyback transformer' mystery.
From Switching Power Supply Design Third Edition
Abraham I. Pressman
Keith Billings
Taylor Morey
"The rules for an inductor with more than one winding are as follows:
The primary to secondary ampere-turns ratios are conserved (not the
voltage ratios, as was the case with a true transformer). For example,
if the primary is, say, 100 turns and the current when Q1 turns “off†is
1 amp, then we have developed 100 ampere-turns in the primary. This
must be conserved in the secondaries. With, say, a single secondary
winding of 10 turns, the secondary current will be 10 amps (10T ×
10A = 100 ampere-turns). In the same way, a single turn will develop
100 amps or 1000 secondary turns will develop 0.1 amps.
So where do we stand with regard to voltage?Well, to the first order,
there is no correlation between primary and secondary voltages. The
secondary voltage is simply a function of load. Consider the 10-turn
10-amp (100 ampere-turns) secondary winding example mentioned
above. If we terminate the winding with a 1-ohm load, we will get
10 volts. What is more striking because the 10 amps must be conserved
is that if we terminate it with 100 ohms, we will get 1000 volts!
This is why the flyback topology is so useful for generating high voltages
(don’t try to open circuit this winding because it will destroy
the semiconductors).With several secondary windings conducting at
the same time, then the sum of all the secondary ampere-turns must
be conserved.
So the lesson we learn here is that flyback “transformers†actually
operate as inductors and must be designed as such. (In Chapter 7, I
use the term choke instead of inductor because the core must support
both DC and AC components of current.) If flyback “transformersâ€
had originally been called by their correct functional name, “flyback
chokes,†then a lot of confusion could have been avoided.
We must not forget that voltage transformation is still taking place
between primary and secondary windings even if they are not conducting
at the same time. Taking the above example of 10 turns terminated
in 100 ohms, the 1000 volts thus developed on this secondary
winding will reflect back to the primary as 10,000 volts; this added
to the supply of 100 volts will stress Q1 in its “off†state with 10,100
volts (where did I put that 11,000 volt transistor?). Hardly practical,
but the theory holds."
I take it this means that the only reason why you need a 'turns ratio' between primary and secondary is so that the voltage reflected from secondary to primary doesn't blow the silicon.
Also, if you have several one turn primaries, each with their own switch, in parallel, for example, the total reflected voltage would be shared by the switches as if they were in series, I think.
If my assumptions are true I think I've got the beginnings of my circuit.
Any comments would be welcome.
Re: Electronic ignition thread
Shrad, Tue Jan 21 2014, 08:18PM
maybe a split primary with a central copper ribbon connected to several ribbon coils distributed along the core would be a nice model to start with...
if the primary is in the outer layer you can even solder the primary terminals directly on the PCB
Re:
Electronic ignition thread
Ash Small, Wed Jan 22 2014, 12:48AM
Shrad wrote ...
maybe a split primary with a central copper ribbon connected to several ribbon coils distributed along the core would be a nice model to start with...
if the primary is in the outer layer you can even solder the primary terminals directly on the PCB
Yes, I think something along those lines would be worth trying. I'm still reading up on gapped cores, etc. and I'm thinking of running some test using a car battery, to get some huge currents flowing. I'll have to use HV rated wire for the secondary (or secondaries, I'm considering using multiple cores with the secondaries in series, although I've not decided yet.), and I'm also contemplating using a separate mosfet for each primary turn (or set of primary turns).
I do think foil primaries is the way to go, though.
Re: Electronic ignition thread
Ash Small, Wed Jan 22 2014, 02:25AM
post deleted
Re:
Electronic ignition thread
Peter02, Wed Jan 29 2014, 05:49PM
Hi,
that explanation of flyback transformer operation is very good i think.
Splitting the primary is a good way to share the load between several primary switches. This method is extensively used in particle accelerators and higher power pulsed laser supplies.
here are two links on the subject, these and many more can be found with search terms like "inductive Voltage Adder" or "Linear Transformer Driver"


Also, if you have several one turn primaries, each with their own switch, in parallel, for example, the total reflected voltage would be shared by the switches as if they were in series, I think.
I think that should be right, the reflected voltage is also the same if you use only one one-turn primary. The benefit is mostly the current sharing between the primaries and their switches.
Greetings
Re: Electronic ignition thread
Ash Small, Wed Jan 29 2014, 11:54PM
That first link is amazing, Peter. Firstly, it confirms that what I wanted to do in the first place is possible (100 nanosecond primary switching times) and secondly, it confirms that I'm on the right track (multiple cores with parallel one turn primaries, and secondaries in series).
It also explains pretty much how to achieve it. I'm thinking of using a stack of powdered iron toroidal cores, and maybe having something like a ten turn secondary, and running in 'flyback mode', incorporating diodes into the secondary, but otherwise it looks like a very similar design. I don't think I'll need as many MOSFETS per primary, though.
Re:
Electronic ignition thread
Ash Small, Wed Feb 05 2014, 04:38PM
Well, this is where I am at the moment. Based on the 100nS pulsed supply linked to by Peter, here:

I've come up with this:
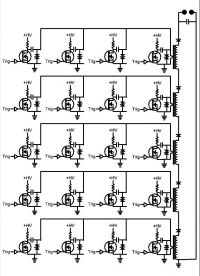
I need to start filling in some numbers, etc., but assuming I use the same high speed MOSFET's and MOSFET Drivers as used in the above link, (MOSFET IXZR08N120, MOSFET gate driver IXDD614SI), and run it in 'flyback mode', and maybe use powdered iron toroidal cores, I think I can get up to 1000 'pulses' in a millisecond, which equates to ~3 degrees at 5000RPM, so I think I may be 'in the ballpark'.
]mosfet_datasheet.pdf[/file]
]mosfet_driver.pdf[/file]
I'll post again when I've done a bit of maths

EDIT: Well, at ~£40 each for those MOSFET's from Farnell, I'll be looking at alternatives, I think.
Re:
Electronic ignition thread
Sulaiman, Wed Feb 05 2014, 06:48PM
You could make the pulse transformers using 'binocular'/'balun'/'pig-nose' ferrite
for high turns ratio use single turn primary tube, with secondary turns wound inside the primary tube for close coupling.
e.g. my HF PA (still characterizing i/p o/p etc.) over 50W over 50 MHz so far so definitely fast enough for your use and easier to construct low leakage transformer.these are 2861006802 but I also have larger in 43 and 61 material in case a re-work is reqd...still playing.
For your purposes I'd go for 2861010002 and slip a ptfe tube inside the primary tube/pipe then thread the secondary turns through that.
You can closely stack the cores with little interaction.
The cores behave pretty much as two isolated sleeve cores,
which are also often used and have even larger central hole diameters.
Whichever transformer style you use, insulating the pri:sec won't be trivial.
info here

Look at construction of transformer (1:2 turns ratio in this case) on left.
P.S. I've multiple purchased MRF185 from an eBay uk seller,
(good to deal with, no connection to me)
they are used but at GBP10 good for up to 85W output, d.c. to 1GHz and experimenting/sacrificing.
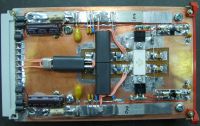
Re: Electronic ignition thread
Ash Small, Thu Feb 06 2014, 04:28PM
Thanks for the suggestions, Sulaiman. What I had in mind was using powdered iron toroidal cores, with a distributed air gap, as I'm planning on running this in flyback mode. I'd need gapped cores if I use ferrite, plus the permeability of the powdered iron cores is significantly higher than ferrite, I believe. I understand there may be fewer magnetic losses with ferrite though.
One of the 'mistakes' in the schematic, because I was unsure how to represent it, and what is there gives a good idea of what I'm thinking, but I was planning on stacking the toroidal cores with their individual primaries, then just passing ten turns of copper cored ignition lead through the stack, as this would take up less space (how would you represent this in a schematic?).
I'm looking at various MOSFET/voltage/primary switch on time combinations at the moment.
EDIT: Very nice bit of work there, Sulaiman.
Re: Electronic ignition thread
Sulaiman, Thu Feb 06 2014, 06:15PM
my mistake, I assumed that to get the required dv/dt the transformers would be in feed-forward / pulse type operation.
( massive leading edge current / almost instantaneous spark)
If flyback then you are back to limited secondary current / low dv/dt
Re:
Electronic ignition thread
Ash Small, Thu Feb 06 2014, 08:11PM
Sulaiman wrote ...
my mistake, I assumed that to get the required dv/dt the transformers would be in feed-forward / pulse type operation.
( massive leading edge current / almost instantaneous spark)
If flyback then you are back to limited secondary current / low dv/dt
My understanding is that 'feed-forward' is voltage dependant (ie voltage is proportional to turns ratio), and 'flyback mode' is current dependant (ie voltage can rise much higher than turns ratio alone).
I 'assumed' flyback mode would be the preferred option here. Would 'feed-forward' work ok with the diodes on the secondaries?
My plan is to get, say, 1000 pulses in a millisecond (figures not finalised yet), which will charge the capacitor until voltage is sufficient for breakdown to occurr, with breakdown occuring at a lower voltage during subsequent pulses. The figure I'm working on for maximum breakdown voltage is <=50kV. With a turns ratio of 50:1 (or is it 1:50?), my understanding is that with 'feed-forward' I'd require a primary voltage of 1000V, whereas this is not the case for flyback mode.
Re: Electronic ignition thread
Sulaiman, Thu Feb 06 2014, 09:56PM
rf (plasma) ignition seems to be the direction that you're moving,
plenty documentation on that.
based on playing with flybacks, ignition coils etc.,
I think that you are heading for a whole load of insulation problems
at your intended voltage, dv/dt and prf.
Re:
Electronic ignition thread
Ash Small, Thu Feb 06 2014, 10:16PM
Sulaiman wrote ...
based on playing with flybacks, ignition coils etc.,
I think that you are heading for a whole load of insulation problems
at your intended voltage, dv/dt and prf.
I imagine there may be a few problems, but I'm sure they can be overcome. The biggest problem at the moment seems to be my reluctance to spend £1,600 on MOSFET's that I'm bound to blow during 'development'

Re: Electronic ignition thread
Sulaiman, Fri Feb 07 2014, 10:27AM
with your experience I'm sure you will not blow up too many transistors,
I'd START with the transformer design as that is obviously the weakest link
lash-up an ignition coil or flyback Xfmr and experiment with dry insulating windings etc. don't want to spend $$$$$ on transistors for a project that gets shelved due to problems other than the transistors, which will be superceeded by better ones in a month or two anyway ... last choice.
why are any secondary diodes required whether feed-forward/pulse or flyback ?
I imagine that for efficiency and for low electrical stresses
if you want say 1000 pps for ignition
design the sum of transformer secondary inductances to resonate with the sum of secondary capacitances to resonate at 500 Hz ... etc.
then flyback would be a good option.
Just to state the obvious
... emi/rfi radiation from such an ignition system will be significant
Re:
Electronic ignition thread
Ash Small, Fri Feb 07 2014, 12:25PM
Sulaiman wrote ...
why are any secondary diodes required whether feed-forward/pulse or flyback ?
Because the capacitor needs DC to charge up to the point that breakdown occurs. This will vary due to varying conditions within the combustion chamber.
The plan is to build one MOSFET/ trigger/capacitorcoil unit and see what happens, I suppose, but I'll probably use cheaper MOSFET's for initial testing.
Re:
Electronic ignition thread
Ash Small, Wed Mar 05 2014, 10:25PM
Aluminium fuel tank arrived today
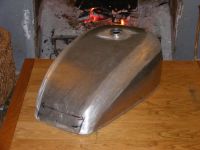
I'll post another photo after it's polished and fitted with a fuel cap.
Re: Electronic ignition thread
paris, Fri Apr 04 2014, 01:57AM
I keep a keen eye on this thread
(.... PENDINE SANDS is up soon , this weekend me thinks , not sure)
Re:
Electronic ignition thread
Ash Small, Fri Apr 04 2014, 04:11AM
paris wrote ...
I keep a keen eye on this thread
(.... PENDINE SANDS is up soon , this weekend me thinks , not sure)
I looked into it a couple of weeks ago, and apparently it's not happening this year, although there is a car event around the last weekend in June.

EDIT: The thing that's holding up progress on this thread at the moment is a lack of affordable high speed mosfets (around 10nS switching time, not including delay, around 1200V and around 30A continuous (60A to 80A pulsed). There is some room for manouvre, but the 5nS switching time mosfets used in the pulse generator linked to above are £40 each from Farnell, and the only other ones I've found that come close are very reasonably priced, but are in California and the postage costs are ridiculous, so if anyone has any suggestions I'd be grateful.
EDIT: RS is now stocking these:

which aren't too far off the mark. I'll have to see what others are in the ST range. These have 78A pulse rating, but switching times are a little slow, nearly 15nS and only 800V. Price is good though, £2.33 each if I order 50. They should certainly be good enough to run some initial tests, but I'll keep looking for a while longer.
Link to the ST range of SuperMESHâ„¢ 5 power MOSFETs

Re:
Electronic ignition thread
Ash Small, Tue Aug 19 2014, 10:50PM
If anyone is still following this thread, the twin disc WP upsidedownies arrived a couple of days ago, and I fitted them to a set of yokes (triple tree) today;
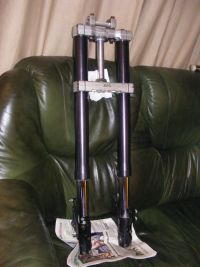
Re: Electronic ignition thread
paris, Thu Aug 28 2014, 09:08PM
your money . and the MOSFETs ?
Re:
Electronic ignition thread
Ash Small, Tue Sept 02 2014, 08:45PM
paris wrote ...
your money . and the MOSFETs ?
Not quite sure what your point is, but as new MOSFET's are becoming available all the time, and the fast ones are getting cheaper, I'm in no immediate hurry to order MOSFET's while I still need to get other parts etc.
I am planning to build some test circuits using slower, cheaper MOSFET's, but again, the technology is developing, so I feel I'm better off getting other parts as they become available on Ebay, etc.
I'm also considering some of the points Sulaiman mentioned above, such as insulation for ~100nS pulses @ ~50kV.
The yokes I had (pictured above) turned out to be 30mm too close together to get the hub and discs I have into, but I managed to get some suitable ones (from two different sellers) on Ebay, which arrived this weekend:
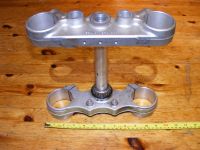
The bottom yoke will need 3mm sleeves machined, though

Re: Electronic ignition thread
paris, Sat Sept 06 2014, 06:08AM
no not smart mouthing .
been reading article on XS650 crank rephasing from 360 to 270 hmm lot to it
Re:
Electronic ignition thread
Ash Small, Sat Sept 06 2014, 01:59PM
paris wrote ...
been reading article on XS650 crank rephasing from 360 to 270 hmm lot to it
Is the XS650 crank one piece, or does it bolt together? I can't remember offhand.
It's basically just crank and cams. Some of the early Japanese camshafts were bolt together too, if I remember correctly.
Obviously ignition timing needs sorting too, but that's usually pretty straight forward. You can also have issues with single carburettors, but if I remember correctly, all the XS's were twin carb.
Obviously, a one piece crank machined from something like EN21 ( I can't remember offhand what the Weslake cranks are machined from, it may be EN24, but I can check) would be a lot stronger. I'd love to have space for a bigger lathe

Re:
Electronic ignition thread
paris, Sat Sept 06 2014, 08:18PM
Ok , so weve established ,you havent got XS650
phil irving was all for rephasing triumph but they disagreed!! (with irving, thats just wrong)
the XS crank is all pressed together.
Im keen to see how ign will turn out . 2 strokes are so fast reving surely they must be reliable for 4 strokes at half the speed ??
Re:
Electronic ignition thread
Ash Small, Sat Sept 06 2014, 09:44PM
paris wrote ...
phil irving was all for rephasing triumph but they disagreed!! (with irving, thats just wrong)
I think Triumph tried it with some of the unit 350's, at least a mate of mine had a 90 degree 3TA when I was a teenager, I assumed it was a standard 'factory job'. Most of the talk on Brit Bike Forum regarding 90 degree and 76 degree cranks relates to Triumph based stuff. Weslake has been producing them for years. I've also come across some 90 degree Weslake cranks for Nortons (The Norton crank can be squeezed into Triumph cases as well, and there are loads of Norton based diaphragm clutch kits that will fit other engines.)
paris wrote ...
the XS crank is all pressed together.
Can you unbolt it and turn one side through 90 degrees, then bolt it back together? (You'd still be better off with a one piece crank though, as I mentioned above. This would also facilitate a longer stroke. I've come across a few long stroke XS's, I think the biggest worked out at ~1,000cc's, maybe even bigger.)
paris wrote ...
Im keen to see how ign will turn out . 2 strokes are so fast reving surely they must be reliable for 4 strokes at half the speed ??
As I mentioned earlier in this thread, I'm only aiming for around 5000 RPM with this project, with separate coils for each cylinder, although the same principle, with sufficiently fast (read 'expensive') MOSFET's, should be able to be adapted for higher RPM.
As an aside, when Jaguar developed the V12 engine, they had to have special coils developed, as the existing V8 coils weren't up to the job (I think I touched on this earlier in the thread as well).
Re:
Electronic ignition thread
paris, Sun Sept 07 2014, 07:26AM
no taper, no key , no nuts, no thread ...no weld!
this is the article , Im reading the mag

Re:
Electronic ignition thread
Ash Small, Sun Sept 07 2014, 10:45AM
paris wrote ...
no taper, no key , no nuts, no thread ...no weld!
this is the article , Im reading the mag

Interesting. A one piece crank won't be possible due to the four main bearings and needle roller big ends.
It does seem that 'modern day' thinking prefers Phil Irving's 76 degree crank. There are several threads on this subject on Brit Bike Forum. I think I posted some links earlier in the thread.
EDIT: I found this formula for calculating the optimum offset for parallel twins:
Balance angle = 90 degrees minus the
maximum thrust angle. Maximum thrust
angle: arc tangent, also known as tangent
^-1 of (1/(2*rod length)/(stroke length))
To do this on a scientific calculator:
1. rod length [enter]
2. times 2 [enter]
3. divide by stroke length [enter]
4. invert (1 / X)
5. click [Inv] box, then [TAN]
6. subtract 90
7. result is offset angle
(information provided by Jeff Diamond)
For a 650 triumph it's 72 degrees. This is where when one piston is stationary, the other is at maximum speed.
Lots more info here:

Re:
Electronic ignition thread
Sulaiman, Sat Oct 04 2014, 10:50AM
Just to show the larger ferrite core that I mentioned above, 2861010002;
this core can handle 50 Vrms/turn at 1 MHz and 500 Vrms/turn at 10 MHz,
less at higher frequencies.
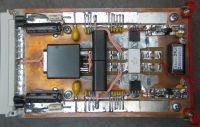
Re:
Electronic ignition thread
Ash Small, Sat Oct 04 2014, 12:36PM
Sulaiman wrote ...
Just to show the larger ferrite core that I mentioned above, 2861010002;
this core can handle 50 Vrms/turn at 1 MHz and 500 Vrms/turn at 10 MHz,
less at higher frequencies.
My current plan (which isn't finalised) is based on using ~ten turns of copper cored ignition lead (~8-10mm diameter) passing through ~5 toroidal cores, with solid aluminium single turn primaries (wound separately on each core). I'm aiming for 1000V per turn per core on the secondary in flyback mode. 5 cores x ten turns gives 50kV (that's the theory), so I'll need toroidal cores in order to fit the windings into the winding window.
The solid aluminium primaries should aid cooling. I think I need to stick with toroidal cores in order to stand any chance of success as far as insulation is concerned. Insulation will be the main issue at these frequencies.
The pulse generator linked to above used 1000V per turn on exotic solid metal cores in push-pull mode, so I guess I'll need powdered iron cores in flyback mode, rather than ferrite to achieve the VPT required, along with the distributed gap required for flyback operation..
Re: Electronic ignition thread
Sulaiman, Sat Oct 04 2014, 02:44PM
Yes, winding a well insulated many-turn secondary in the core(s) I showed would be challenging !
I don't think that the peak voltage in a flyback is proportional to core size/type
it's basically set by two things;
1) Insulation breakdown ... primary, secondary and switch (due to turns ratio)
2) 0.5 x L x Ip^2 > 0.5 x C x Vs^2,
energy stored in the magnetic field goes (mostly) to secondary capacitance.
Re:
Electronic ignition thread
Ash Small, Sun Oct 05 2014, 12:01PM
Sulaiman wrote ...
Yes, winding a well insulated many-turn secondary in the core(s) I showed would be challenging !
I don't think that the peak voltage in a flyback is proportional to core size/type
it's basically set by two things;
1) Insulation breakdown ... primary, secondary and switch (due to turns ratio)
2) 0.5 x L x Ip^2 > 0.5 x C x Vs^2,
energy stored in the magnetic field goes (mostly) to secondary capacitance.
Thanks for that furmula, Sulaiman. I'll look into it in greater detail later.
Yes, I've realised that the 'reflected voltage', due to turns ratio will be 'seen' by the switches, this is why I need switches rated for 1kV, at least, with a 50:1 turns ratio if I want 50kV max.
Breakdown voltage should be lower than this figure, even in the most demanding of cumbustion chamber conditions. I realise I need to do some experimenting, but I'm not planning on buying any MOSFETs this side of Xmas, at least, not at the moment.
Re:
Electronic ignition thread
Ash Small, Thu Apr 16 2015, 11:13PM
Just for Paris, and anyone else who is interested, Pendine Speed Week is on this year again, from 23rd to 25th May (bit of a short 'week', but anyway...).
Just got my copy of the 'Rulebook', although my bike won't be ready for this year's event, but it gives me a pretty good idea of what's required if I want to enter it in the future. I do need to contact the Pendine Land Speed Racing Club for clarification on a few points, but I now know what questions I need to ask
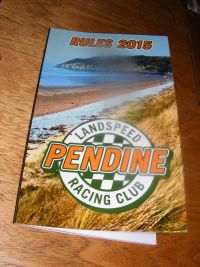
I have made a bit more progress, but before I order some Borrani rims from Italy, I do need to check what rating tyres I need. It depends on the 'class record' for 'my class', I'm not expecting to hit over 150MPH over a mile, but the class record may require tyres rated for 200MPH, for example

(I think I'll be in the 1350cc 'special construction' 'A' class)
Any more guesses, Paris?