BIG electromagnet...
Noah Hoppis, Sun Mar 24 2013, 08:09PM
I was wondering about constructing a large electromagnet for my cyclotron vs just buying one. Would plain steal or iron work? what about laminated? (if yes what kind of surface contact is required to transfer the magnetic flux?)
Re: BIG electromagnet...
Ash Small, Sun Mar 24 2013, 09:15PM
I know nothing about cyclotron magnets, but I assume it's just a huge, presumably DC, solenoid type thingy.
I imagine steel may have some benefits over iron, I read somewhere I think, that It's about 1.2 times as efficient than iron in this type of application, but you'd need to check this.
I imagine you just follow the usual advice for coils in general, but just think a bit bigger.
I imagine some of the coil gun builders can supply the maths for a 0.9T magnetic field.
Re: BIG electromagnet...
doctor electrons, Sun Mar 24 2013, 09:35PM
Laminated steel cores are constructed as such to eliminate eddy currents in the core and stabilize the
larger field around the entire core. That's why most transformers, if not all, are constructed that way.
The larger electromagnets you see in scrap yards are a different story. They use a large solid steel or iron core.
They also have a backup battery system in case of power failure while making a pick. Generally that backup battery
only provides enough time to warn anyone in the area to get away! The latter is about as simple an electromagnet
as it gets. In both cases the coils are wound around the cores. Surface contact is not an issue because the core is magnetized by the flux generated by the energized coil. If the core is inside the flux it will magnetize.
Re:
BIG electromagnet...
klugesmith, Mon Mar 25 2013, 05:04AM
Hi Noah.
Since your cyclotron magnet is DC, with a large gap between the poles:
- Laminations are unnecessary.
- Air gaps between core sections are no problem, if much thinner than the main gap.
They only matter in transformers and lifting magnets which ideally have -no- gap.
- at 0.9 teslas, materials more expensive than ordinary steel won't improve performance significantly.
Time to learn the difference between your B and your H. I'd recommend sticking with SI units, and reading a tutorial. Just found this one, which looks quite respectable.

If you read the first five chapters, or equivalent in another reference, you'll be able to calculate the ampere-turns you need, and you'll understand what laminations are for.
Here's an alternate starting point.

Good luck!
-Rich F.
Re: BIG electromagnet...
Noah Hoppis, Mon Mar 25 2013, 11:23PM
I knew what lamination were for in transformers; to avoid eddy currents at 60 Hz AC and to stop unnecessary heating. The Questions were more posed towards whether the lamination would cause unnecessary loss, because 4"x1"x18" bar is much easier to get and bolt together than a several hundred pound magnet core!
Re:
BIG electromagnet...
Ash Small, Mon Mar 25 2013, 11:48PM
Noah Hoppis wrote ...
I knew what lamination were for in transformers; to avoid eddy currents at 60 Hz AC and to stop unnecessary heating. The Questions were more posed towards whether the lamination would cause unnecessary loss, because 4"x1"x18" bar is much easier to get and bolt together than a several hundred pound magnet core!
I think as long as it's steel, it's not going to matter much.
Re: BIG electromagnet...
Steve Conner, Tue Mar 26 2013, 11:01AM
A cyclotron magnet needs a very uniform field. Any wiggles and lumps will break the beam up. Traditionally the field was tweaked by hand after assembly, by inserting steel shims between the magnet pole and the chamber lid.
I'm sure you could make a perfectly good magnet out of smaller steel bars bolted together, especially if you used some simulation beforehand to work out what the field would end up looking like. Maybe there would be some weird arrangement of bars that would give a more uniform field than the obvious arrangement.
Re:
BIG electromagnet...
klugesmith, Fri Apr 05 2013, 10:39PM
Stumbled on this uniform-field magnet on ebay.

Its size can be guessed.
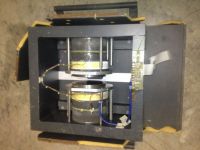
Because of the small amount of wiring, and no plumbing, I bet it uses permanent magnets.
But... there may be some electromagnet coils also, to fine-tune field strength, for example as the permanent magnet temperatures change.
Along those lines, an amateur cyclotron magnet might be designed with main coils powered by rectified but unregulated mains voltage (aptly named). The natural inductance would limit current ripple to a few percent, if my calc's are right. Then smaller "vernier" coils using much less electrical power could be driven dynamically to cancel the effects of ripple current and mains voltage fluctuation.
Might not be worth the trouble, compared with just making a multi-kW regulated DC supply for the main coils.
Re:
BIG electromagnet...
Ash Small, Sat Apr 06 2013, 01:15AM
klugesmith wrote ...
Might not be worth the trouble, compared with just making a multi-kW regulated DC supply for the main coils.
How many kW will be required for 0.9T?
I was thinking a lead/acid battery bank would be the easiest way to provide a 'smoothed' supply, but how much power are we talking here?
Re: BIG electromagnet...
klugesmith, Sat Apr 06 2013, 03:00PM
Depends on your pole diameter and gap length, and the resistivity of copper.
Got some dimensions in mind?
Last month Noah and I analyzed a design for D,G = 8",2". Then I did one for 3", 1" .
The unreviewed results (on the order of 3 or 4 kW and 1kW) aren't here now, but I'll post 'em later. Someone can compare them with historical & university cyclotron numbers.
Spreadsheet calculations demonstrated 2 principles.
1) You can design for any voltage by choice of wire gauge, with no change in power, coil size, or copper weight and cost.
2) You can reduce power by using more copper, but that needs longer or (less efficiently) wider coils, thus a bigger yoke.
Re:
BIG electromagnet...
Ash Small, Sat Apr 06 2013, 04:14PM
klugesmith wrote ...
Depends on your pole diameter and gap length, and the resistivity of copper.
Got some dimensions in mind?
Last month Noah and I analyzed a design for D,G = 8",2". Then I did one for 3", 1" .
The unreviewed results (on the order of 3 or 4 kW and 1kW) aren't here now, but I'll post 'em later. Someone can compare them with historical & university cyclotron numbers.
Spreadsheet calculations demonstrated 2 principles.
1) You can design for any voltage by choice of wire gauge, with no change in power, coil size, or copper weight and cost.
2) You can reduce power by using more copper, but that needs longer or (less efficiently) wider coils, thus a bigger yoke.
Thanks for the figures, Rich.
I'd realised you could design for any voltage, and three or four kW should be 'do-able' using lead/acid batteries for smoothing (I think

).
Re:
BIG electromagnet...
klugesmith, Sat Apr 13 2013, 05:30AM
I'd like to post an analysis, for review, of power & weight
for a reference electromagnet configuration, easily scaled.
No consideration is given to details like field flatness.
Please let me know if the aspect ratios shown in this drawing are not well chosen.
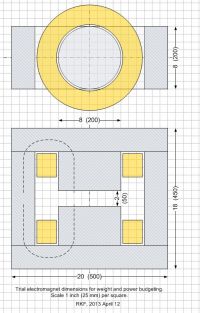
Not sure which set of dimensions to write up:
the round numbers of millimeters, or the round numbers of inches.
The difference is like that between decimal and binary kilo, mega, giga multipliers.
3.2% in linear dimensions, 6.5% in areas, and 9.9% in volumes / weights / costs.
Anyone care to give a preference?
thanks
Rich
Re:
BIG electromagnet...
Ash Small, Sat Apr 13 2013, 10:16AM
klugesmith wrote ...
Anyone care to give a preference?
Well, everything I've read recently regarding magnetics suggests using SI units from the start, as it's supposed to simplify calculations later.
Re: BIG electromagnet...
klugesmith, Sat Apr 13 2013, 03:46PM
OK, let's see how fast and simple-looking we can make this.
First, how much "magnetomotive force" do we need, according to Ampère's law?
Given:
* Air gap flux density B_air = 0.9 T.
* Air gap length L_air = 0.05 m. (2 squares in drawing).
For magnetic permeability of air, use the physical constant
* u0 = 4e-7 * pi teslas per (ampere/meter).
Magnetizing field in air
* H_air = B_air / u0 = 716000 A/m.
Integrating H along the air section of dashed line in drawing, we have
* MMF (for air) = H_air * L_air = 35800 amperes.
The MMF for the steel section of flux path will contribute negligibly to the total.
Here's why.
* Flux density B_s is roughly the same as B_air, if x-section areas are similar.
* Permeabilty of steel, u_s, is greater than u0 by a factor of thousands -- say 3500.
So magnetizing field in steel H_s = B_s / u_s is less than H_air by that factor of thousands. Say 200 A/m (2.5 oersteds). Could look it up on a published "B-H curve" for the steel.
* Flux path length L_s is about 1 meter (40 squares in drawing).
Integrating H around the steel section of dashed line in drawing, we have
* MMF (for steel) = H_s * L_s = some value on the order of 200 amperes
Design coil(s) for 36000 ampere-turns.
To be continued...
Re: BIG electromagnet...
klugesmith, Sun Apr 14 2013, 06:08AM
Next, how much electric power does it take to push I = 36000 amperes around the magnet axis? Let's figure it for copper wire. Aluminum magnet wire is probably lighter and less expensive, but bulkier, for the same resistance and power.
Given:
* Average turn diameter d = 0.275 m ( 11 squares in drawing ). Average wire length per turn L = pi*d = 0.864 m.
* Whole coil cross-section copper area A = 5000 mm^2 = 0.005 m^2 (8 squares in drawing ). That's only 53% of the shaded area in drawing, leaving plenty of room for insulation, cooling system, and wasted space between round wires.
The current density is 7.2 A/mm^2, much higher than the design limit in ordinary transformers, so active cooling will be required.
With copper density Ï = 8890 kg/m^3, the copper mass M = Ï * L * A = 38.4 kg.
* Conductivity of wire materials is often expressed in percent of IACS, the International Annealed Copper Standard (which turns 100 in 2013). It says that at 20 degrees C, the standard resistance is 1/58 ohm (0.017241 ohm) in wire of 1 meter by 1 mm^2. That works out to Ï = 1.7241e-8 ohm-meter. Typical magnet wire today is specified to have conductivity of at least 101% IACS. From there we'll derate the resistivity by 8% to allow an average wire temperature of 40 degrees C. So Ï = 1.07 * Ï_IACS = 1.845e-8 ohm-m.
Now consider the coil as a single turn. ( Its thickness on the AWG scale would be around 20-ought ).
Resistance R = Ï L / A = 3.188e-6 ohms.
Voltage V = I R = 0.115 volts.
Power P = V I = I^2 R = 4131 watts.
To match a practical power supply, the coil can be split into N turns of wire carrying current I/N, giving the same total ampere-turn value I.
Then wire area = A / N and wire length = N L.
Wire resistance = N^2 R and wire voltage = N V.
Wire mass, current density, volts per turn, and power are the same as in the single-turn coil, for any value of N.
The copper area A in this example came from trying 2400 turns of AWG14 wire with 15 amperes.
Power can be reduced by increasing the coil's copper area A, along with its weight and cost. Volume power density would go down by the square of that factor.
I hope that's all easy to understand, and technically correct.
-Rich
[edit]
Power is also, of course, proportional to the square of the air gap length and flux density B. (hint to Noah)
Re: BIG electromagnet...
Ash Small, Sun Apr 14 2013, 11:43AM
So at, say, 12V, we're looking at ~350Amps, and ~100 turns?
(I'm guessing that half a dozen, or so, car batteries should do a pretty good job of smoothing this?)
(Maybe a welding transformer, and car batteries arranged in a series/parallel configuration could be used here as a 'ghetto' solution?)
Re:
BIG electromagnet...
Ash Small, Mon Apr 22 2013, 12:43PM
I understand there is now a thread on fusor.net regarding this, which I've not looked at yet (I can't post there unless I set up ANOTHER pseudonym, etc).
Rich sent me a link via Email to this magnet on Ebay:

It's 1.13T @ 30A and 45V, so could be run @ 0.9T @ reduced power.
I'd suggest it could be run from a small, variable current welding transformer, using four 12V car batteries in series if any smoothing is required (with maybe a variac for additional control if required, although the welding transformer should control current adequately by itself)
I may look into this further myself, although I'm not planning on spending that amount on a magnet. I'm still of the opinion that electro-static accelerators have some advantages over cyclotrons
EDIT: I've just noticed that the above magnet has a variable gap, and is 1.13T @ 1" gap, which 'may' present some problems.
Re:
BIG electromagnet...
klugesmith, Tue Apr 23 2013, 12:03AM
Ash Small wrote ...
I'd suggest it could be run from a small, variable current welding transformer, using four 12V car batteries in series if any smoothing is required (with maybe a variac for additional control if required, although the welding transformer should control current adequately by itself)
Ash, Noah, et al,
I also see that the magnet in that link is nominally a 4 inch size. Would guess that means pole diameter, not gap length (which is probably trivial to change). The former affects the power requirement, because it sets the necessary wire length per turn.
I'd been meaning to address the "smoothing" requirement, noting that it's current ripple that counts. Not voltage ripple, and we have a highly inductive load.
Here we go.
* What are the magnet's inductance, and its characteristic L/R time constant?
* What does that imply for "smoothing" when run from rectified mains? (as one Fred Niell did successfully.)
First, some minor dimensional changes to ease the power requirement while illustrating some design factors.
Version 2 is the right half of this scale drawing.
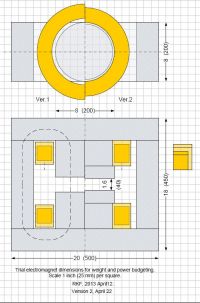
0. Flux density B, copper mass density rho, and (warm) copper electrical resistivity rho are unchanged.
1. coil average diameter is reduced from 275 to 250 mm (11 to 10 squares).
--> weight, cost, resistance, and power factor = 10/11.
2. coil cross-sectional copper area is increased from 5000 to 6250 mm^2 (8 to 10 squares).
--> weight and cost factor = 5/4. Resistance and power factor = 4/5.
3. Gap length is reduced from 50 to 40 mm (2 to 1.6 squares).
--> H field and current factor = 4/5.
4. Combining the coil geometry factors,
-->
Weight & cost *= 25/22 (114%), from 38.4 to 43.6 kg.
-->
Resistance *= 8/11 (73%), from 3.188 to 2.318 microohms per (turn^2).
5. Throwing in the reduced gap length,
-->
Current *= 4/5 (80%), from 36000 to 28800 ampere-turns.
-->
Voltage *= 32/55 (58%), from 115 to 67 mV/turn.
-->
Power *= 128/275 (47%), from 4131 to 1923 watts.
[edit] and for the record
--> Current density *= 16/25 (65%), from 7.2 to 4.6 A/mm^2.
--> Power density *= 256/625 (41%), from 0.96 to 0.39 W/cm^3.
6. Now the inductance, unlike the other electrical parameters we've discussed, depends on the
area of the air gap.
We can figure it from the total flux linkage (Weber turns) at 1 ampere, or by equating the magnetic energy in the gap (B*H/2 * volume) with inductor energy storage E=L*I^2/2, ignoring the steel terms.
Among the dimension changes in Version 2, only the gap length matters.
-->
Inductance *= 5/4 (125%), from 0.790 to
0.987 microhenries per (turn^2).
If made with 3000 turns, for 200 volt operation, that would be 8.88 henries.
7. Inductance tends to make current "smoother" than voltage.
A figure of merit is the time constant L/R, which does not depend on the turns count.
Version 2 changes L/R by a factor of 55/32 (172%) from 0.248 to 0.426 seconds.That's respectably long. It always gets better with physical bigness of the coil and core, here offset by the inordinately long air gap.
To be continued...
Re:
BIG electromagnet...
klugesmith, Thu Apr 25 2013, 04:27AM
Sorry to bump my own post. Hope -somebody- is learning from this thread. Or checking my work for mistakes, other than continuing to flaunt an obsession with pedantic writing.

Before getting into the inductance thing (which makes the magnet take several seconds to get up to full power after full voltage is applied), I got to thinking about practical costs.
There's a lesson in "green" economics, especially if no terrific wire-scrounging opportunity appears.
The going rate for new magnet wire through ebay seems to be around $10/lb, with a sweet spot at around AWG 10 size. I think scrap dealers -pay- about $4/lb for #1 (that's a scrap grade, not an AWG size) bare copper wire.
In magnet version 2 (previous post), I made the coil 25% thicker to save power. Used 3000 turns of AWG14 (or equivalent division of 6250 mm^2 total copper area). That reduced the water cooling technology to a no-brainer, considering that enameled copper magnet wire comes in temperature ratings of 155 and 200 degrees C.
But it would take at least a couple thousand hours of operation for the electricity savings to offset the extra copper cost.It might be better to choose a less expensive design that wastes electric power. Version 2 was still too much power for comfort from regular 120V outlets, and
_far_ below the limit for 240V applications in North America.
My numbers for 3000, 2400, 1800, 1500 turns of AWG14:* Total wire length 2356, 1885, 1414, 1178 meters.
* Wire cost $960, $768, $576, $480 (half of ver.2 cost) at $22/kg.
* Power 1923, 2404, 3205, 3846 watts (twice the ver.2 power)
* Power density 0.39, 0.61, 1.01, 1.57 watts/cm^3 (four times the ver.2 density, and not trivial to cool).
The power density record in resistive magnets (Bitter solenoids for generating tens of teslas continuously, where iron is of no use as a concentrator)
appears to be about 14,000 watts per cubic centimeter. 
[edit] Speaking of scrounging, I found a $200 solution using 220 feet of triple-ought aluminum building wire presently up on ebay. 83 turns, 2864 watts (347 amps at 8.3 volts). Now how much will the power supply cost?

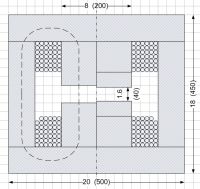
Re:
BIG electromagnet...
Ash Small, Thu Apr 25 2013, 08:49AM
klugesmith wrote ...
[edit] Speaking of scrounging, I found a $200 solution using 220 feet of triple-ought aluminum building wire presently up on ebay. 83 turns, 2864 watts (347 amps at 8.3 volts). Now how much will the power supply cost?

~350A @ ~8.5V doesn't sound very practical, although, according to past experience I do know that your average 'continuously variable current welding transformers' do obey Ohm's law, ie the voltage and current are dependant on the load. (at least with resistive loads, ie electro-chemistry).
I assume that this application will require a continuously variable power supply in order to 'tune' it to 0.9T, and, for these amperages I'd assume that a second hand welding transformer or two, plus rectifiers, will probably be the most economical solution, although a welding transformer 'may' be more suited to more turns @ lower current and higher voltage
Re: BIG electromagnet...
klugesmith, Thu Apr 25 2013, 08:22PM
Ash, this magnet (which I have no room to build) is driving me to distraction.
The 3/0 Al wire was just put up as an example of being flexible if the goal is to minimize materials cost.
You're right about it being better to match more convenient power supply voltages.
I found that heavy gauge copper building wire goes for less money per pound (of Cu) than magnet wire. The thicker insulation makes it bulkier, but as stranded wire it's easier to wind. And could always be unwound and re-sold as useful building wire.
AWG #2 copper is about right for 12 volt designs of this diameter. There's a 500 foot length (whose wooden spool was damaged) on ebay for $600 or best offer; that's 100 lbs of Cu at $6/lb.
Just right for my original Version 2 design: same 1923 watts, now 186 turns x 155 amps, 12.4 volts.
As I explained yesterday, one could use a shorter length of that wire to make the coils more compact.
Voltage requirement would be unchanged, but current and power would go up.
At my day job we use large numbers of compact 12 volt 200 amp SMPS's.
There are also mains-frequency transformer options (e.g. for low voltage lighting),
MOT rewinds (perhaps 2 in series to get the power; easy to air-cool),
and heavy-duty car alternators. How 'bout driving around with a mobile cyclotron instead of an earth-shaking amplified sound system?
[edit] For a better match to your welder, coils made with AWG #6 wire would take about 31 volts.
If you use the full 43.6 kg of Cu, that would be 470 turns x 61 amperes, with 0.5-ohm coil R.
Re: BIG electromagnet...
Ash Small, Fri Apr 26 2013, 08:57AM
That's an interesting point you make about car alternators, Rich. It's the voltage regulation that limits them. It's quite easy to 'hack' them to produce higher voltages, easily up to 120V (you may have to fit diodes of higher voltage rating for rectification).
I assume you'd still be able to pull 60-80 amps from them at higher voltage. There are numerous 'how to's' on the internet.
Re:
BIG electromagnet...
Steve Conner, Fri Apr 26 2013, 09:34AM
I believe the original cyclotrons had their magnets powered by motor generators, as they were built before good high-current rectifiers became available. A car alternator might be a vintage-correct solution.

The problem with building wire is that it has PVC insulation that softens and shorts out at a relatively low temperature compared to "real" magnet wire.
A cost-benefit analysis should include the cost of any power supply parts that you don't already have lying around the junk box (shed, 40 foot container, warehouse

)
Re:
BIG electromagnet...
Ash Small, Fri Apr 26 2013, 12:38PM
Steve Conner wrote ...
I believe the original cyclotrons had their magnets powered by motor generators, as they were built before good high-current rectifiers became available. A car alternator might be a vintage-correct solution.

Would these not have been dynamo powered? Alternators still require 'good high-current rectifiers'.
Re: BIG electromagnet...
Steve Conner, Fri Apr 26 2013, 12:58PM
Yes, a motor generator was a kind of primitive mechanical rectifier, a 3 phase induction motor driving a brushed DC generator. You also got a "rotary converter", which was the same thing but combined into a single machine. In both cases the rectification was mechanical by a commutator and brushes.
So if you want to be pedantic, an induction motor driving a car alternator isn't really vintage correct, you would have to use a dynamo from an ancient car.
Re:
BIG electromagnet...
Noah Hoppis, Fri Apr 26 2013, 03:57PM
True that most alternators are rather flimsy nowadays, I have seen several horse power DC motors that are about 1.5ft in diameter around but they went of to scrap long ago

. Wonder about welding transformers, I have on rated for 250A @ 2.5V and given enough transformers in series then a good output could be achieved. Aluminum wire was a clever idea, I recently bought 90ft for $15.
Re: BIG electromagnet...
..., Fri Apr 26 2013, 09:50PM
For power, just get a vicor megapak off ebay (then usually go for $100-200). Most of them will run from single phase, although I think some of the higher power ones will shut down if you try and draw the full 4kw from a single phase 240v line. Most of them are adjustable (they don't state it, but there is a header for 'trimming' the output) 90-110%, although some of them are adjustable 10-110% (unfortunately, it is almost never stated on the sticker which type of vicor brick is used internally), but if you get one that is like 10x 5v modules you can tap to the nearest 5v and use a large resistor (or transistor + opamp system) to do the fine tuning.