"The HOG" Supersized QCWDRSSTC
Goodchild, Mon Nov 12 2012, 09:49PM
Ok folks, we have have had enough progress on this project that we figured it was time to start a project thread. I will start out with saying this is a joint project between myself and Steven Caton. We have been designing and gathering parts now for a little more than 6 months. Let there be no illusions this is a long term project and we don't expect to have it running anytime soon.
So what are we building? Simple the worlds largest QCWDRSSTC! The design goal on the system is 12+ feet of sword sparks. This is to be a very complex build. Most of the system is designed we just have to get the rest of the parts and build it.
Some Specs!!!
Fres: 450KHz
Secondary MMC for spark capacitance compensation.
Peak primary current 800A
Pulse widths on the order of 100mS+
Tank cap: MMC consisting of 12 10Kv 5.6nF high RMS current MICA caps
Primary: 3/8 water cooled conical
Controller: ZVS driver with full phase shift modulation
Power electronics:
32x IXYN82N120 100A 1200V high speed IGBTs with positive tempco (that's right 32 of them!)
Topology: full bridge 8x
Current sharing/impedance matching network (8 ferrite transformers)
A grand total of 120mF of bus capacitance with an energy storage of 30KJ
Water cooled copper heatsinks (that are 1" think)
fully laminated copper bus structure.
Here is one of the 4 bridge assemblies. It has 8 IGBTs inside and 30mF of total bus C

An exploded view of the bridge assembly:
All the parts on the bridge are to be water jetted and laser cut.
A large amount of simulation and modeling has been conducted regarding the modulation topology and spark loading on the secondary circuit. We still have plans to measure the capacitance added by sword sparks by extrapolating a general equation from data we plan to collect from my small QCW. This will give use the numbers we need to accurately choose the secondary MMC size based on our 10 to 12 foot design goal. Without the secondary MMC the resonant frequency will easily shift many 10's of KHz possibly pulling the system out of resonance by the end of the burst (below the magic 380KHz zone).
I will add more info and photos later. But this gives a good idea of the magnitude of the project.
As usually high res photos can be found here:
UPDATE 11/24/12Ok So some of the parts have come in for the HOG. We now have all the water cooling parts, ferrite cores for the sharing networks, wire, bridges and transistors, DC block caps, and copper (note shown). Also in the photo is the two radiators that will cool the water in this closed system. Each radiator has three 120mm fans with speed control, so we should be able to keep this coil rather silent.
The water blocks and transistors have been assembled for some time now and as soon as the bus caps come in we can start fabricating the bridge modules.
UPDATE 12/28/12Ok so probably the last update on this project for this year. All of the MICA caps for the Tank circuit have come in and 8 of the bus caps have arrived. We plan to build one bridge module to start and then once we have tested it fully build the remaining 3.
UPDATE 8/26/13OK so we actually built something.... We changed our bridge design drastically from out last design, we even changed the transistors. We plan to change the modulator again however from a discrete logic and analog to a full 100MS/S ADC front end with a FPGA DSP doing the heavy lifting. That's right folks we are going to do phase lead all in digital!
The great thing about our new controller is the it will be highly configurable, simply by changing the software it could act like a a UD1.3 UD2 or in ZVS phase shift modulation mode. It's truly a universal driver!
Until then here are some photos of the new bridge and the older analog controller.
Bridge and gate driver daughter board:
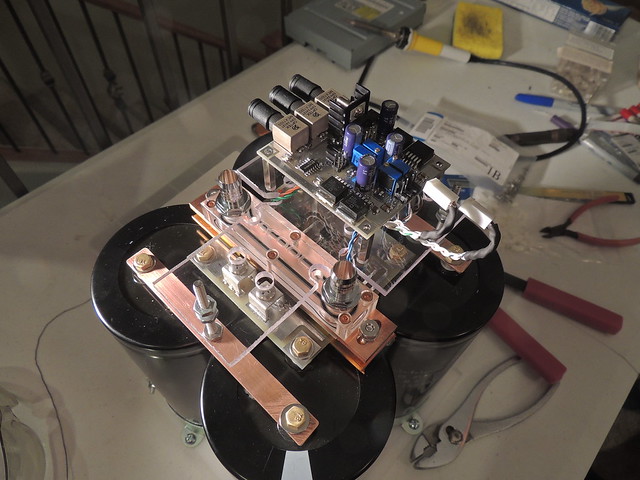
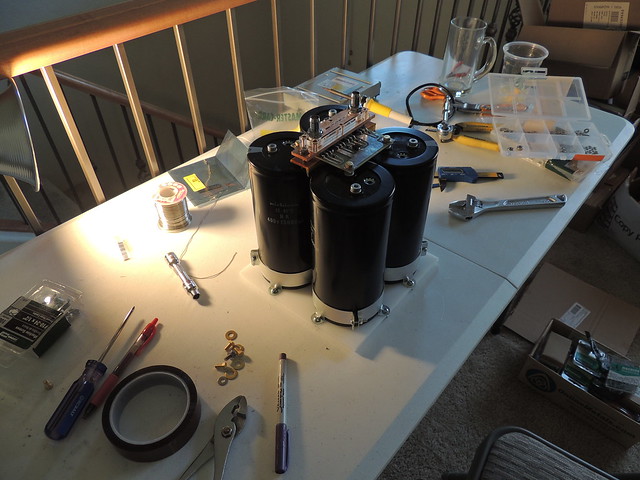
Old analog ZVS phase shift modulated controller:
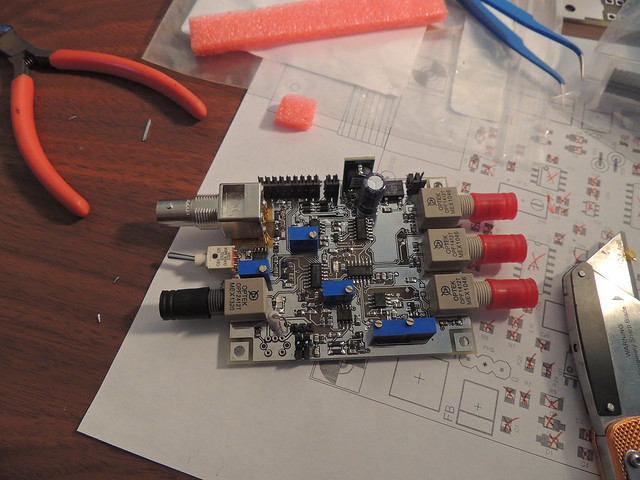
Re:
"The HOG" Supersized QCWDRSSTC
Dr. Drone, Mon Nov 12 2012, 11:00PM

Re:
"The HOG" Supersized QCWDRSSTC
nixie, Tue Nov 13 2012, 12:27AM
Goodchild wrote ...
Power electronics:
32x IXYN82N120 100A 1200V high speed IGBTs with positive tempco (that's right 32 of them!)
Topology: full bridge 8x
Current sharing/impedance matching network (8 ferrite transformers)
A grand total of 120mF of bus capacitance with an energy storage of 30KJ
Water cooled copper heatsinks (that are 1" think)
fully laminated copper bus structure.
Wow, that certainly fits into the "go big, or go home" arena.
I can hardly wait to see how you'll drive the eight parallel IGBT's comprising each quadrant of the bridge, and the balanced output transformers.

P.S. nice modelling!
Regards, Jeff
Re:
"The HOG" Supersized QCWDRSSTC
Uspring, Tue Nov 13 2012, 12:03PM
Hi Eric,
you wrote:
We still have plans to measure the capacitance added by sword sparks by extrapolating a general equation from data we plan to collect from my small QCW. This will give use the numbers we need to accurately choose the secondary MMC size based on our 10 to 12 foot design goal. Without the secondary MMC the resonant frequency will easily shift many 10's of KHz possibly pulling the system out of resonance by the end of the burst (below the magic 380KHz zone).
I find this very interesting, since I've been attempting to model QCW spark characteristics myself. Maybe you want to share some of your results.

Steve Wards tesla gun requires about 25kW peak power for a 50" spark. By Freaus relation you would need about 210kW for 12'. According to my current model, QCW spark length rises with the square(!) of the voltage. This is a bit radical, but it seems to agree with my own measurement for shorter (30") sparks. Extrapolation from Wards data 65kVpk for 50" would require a voltage of only about 110kVpk for 12'. The arc load resistance is then 29k. By the hungry streamer model, which seems to hold for my shorter arcs, reactance of the arc load capacitance and the arc load resistance are the same. For 450 kHz frequency that amounts to a 12pF capacitive arc load. This is heavily extrapolated and speculative. What do you think?
Re:
"The HOG" Supersized QCWDRSSTC
Steve Conner, Tue Nov 13 2012, 12:49PM
I think crank the sucker up and see what happens!

Did you leave room for a bunch of plastic film caps in your buswork? If you're switching at 500kHz, your DC bus decoupling will have to be good up to several MHz.
Re:
"The HOG" Supersized QCWDRSSTC
Goodchild, Tue Nov 13 2012, 04:17PM
Uspring wrote ...
Hi Eric,
you wrote:
We still have plans to measure the capacitance added by sword sparks by extrapolating a general equation from data we plan to collect from my small QCW. This will give use the numbers we need to accurately choose the secondary MMC size based on our 10 to 12 foot design goal. Without the secondary MMC the resonant frequency will easily shift many 10's of KHz possibly pulling the system out of resonance by the end of the burst (below the magic 380KHz zone).
I find this very interesting, since I've been attempting to model QCW spark characteristics myself. Maybe you want to share some of your results.

Steve Wards tesla gun requires about 25kW peak power for a 50" spark. By Freaus relation you would need about 210kW for 12'. According to my current model, QCW spark length rises with the square(!) of the voltage. This is a bit radical, but it seems to agree with my own measurement for shorter (30") sparks. Extrapolation from Wards data 65kVpk for 50" would require a voltage of only about 110kVpk for 12'. The arc load resistance is then 29k. By the hungry streamer model, which seems to hold for my shorter arcs, reactance of the arc load capacitance and the arc load resistance are the same. For 450 kHz frequency that amounts to a 12pF capacitive arc load. This is heavily extrapolated and speculative. What do you think?
I'm glad you bring this up because I can't claim I know a whole lot on the subject yet. From my experimentation with the little QCW it seems that QCW sparks need way more power than a regular DR for a given length of spark and this makes sense given they are thicker brighter, higher energy plasma. However we run QCWs at drastically lower break rates than a regular DRs. Hence at least from my QCW experiments assuming I stayed at 5 to 10 Hz I was able to match regular DR spark length with the same input power.
I
think that regular DRs follow a very similar model to that of the QCW spark in terms of amount of voltage needed in relation to length. So if once again we keep the break rate reasonable 5-10Hz we should be able to make 10 or 12 feet at a similar input power to an equivalent sized DR.
This is however speculator. I need to gather more data before I can make any concreate assumptions. The main info we need is capacitance added per foot. It's probably not linear because that would be too easy. Most likely it is logarithmic or exponential. We plan to find this data by looking at shift in frequency and relate this to spark length.
Any other info you have gathered on your model or just general DR model would be of great help. I welcome others that have data or theories on this subject. One of the main reasons for this project is to help answer some of these questions.
Steve,
Thankfully our caps only have to be 5-20nF due to the ZVS operation but they have to be rated for a lot of current due to the commutation of the current on the rising and falling edges that can be as high as 80 to 100 amps. We are thinking of using some of the 940C caps for this application. GO figure we are finally using 940C's for their designed purpose...
We did leave a generous amount of room for caps so no matter the solution we should be in good shape.
Re:
"The HOG" Supersized QCWDRSSTC
Uspring, Wed Nov 14 2012, 10:46AM
Eric wrote:
From my experimentation with the little QCW it seems that QCW sparks need way more power than a regular DR for a given length of spark and this makes sense given they are thicker brighter, higher energy plasma. However we run QCWs at drastically lower break rates than a regular DRs. Hence at least from my QCW experiments assuming I stayed at 5 to 10 Hz I was able to match regular DR spark length with the same input power.
Yes, the main difference between QCW coils and others is the duty cycle. They don't differ as much in peak power. A SGTC might have a burst length of 100us and a bang energy of 10J, which amounts to a peak power of 100kW. The 210kW value I guessed at for your project is meant as a peak value at the end of the rampup.
I think that regular DRs follow a very similar model to that of the QCW spark in terms of amount of voltage needed in relation to length. So if once again we keep the break rate reasonable 5-10Hz we should be able to make 10 or 12 feet at a similar input power to an equivalent sized DR.
I agree that you can probably get the same performance in terms of spark length with similar power values, but I believe, that the voltage required is much lower for QCWs. A SGTC has a very short burst length so there is little time to heat up the plasma and make it conductive. The low conductivity requires more voltage from the coil to transport charge to the tip of the arc, which is needed to make it grow.
The main info we need is capacitance added per foot. It's probably not linear because that would be too easy. Most likely it is logarithmic or exponential. We plan to find this data by looking at shift in frequency and relate this to spark length.
I'd be very interested in seeing that data and also info on spark length versus voltage

You need to be careful in your analysis of the data, since your coils frequency also depends on the resonant frequency of your primary tank.
I know only 2 theoretical approaches relating to the arcs capacitance. The simpler one is based on a wire model, where the arc is assumed to have the capacitance of a perfectly conducting thin wire. That would predict a linear growth of capacitance with arc length. I've posted a more complicated theory on TCML a while ago

That model is base on some unproven assumptions, but it seems to work for the smaller (30") arcs, that I measured. It also predicts a linear rise of capacitance with arc length.
Re:
"The HOG" Supersized QCWDRSSTC
Steve Conner, Wed Nov 14 2012, 12:00PM
Very interesting TCML thread.

There are some good pointers for possible experimental work there.
I'll add in a puzzler of my own. Is all the power consumed by a streamer fed in through the root from the breakout point? Or does it draw some from the surrounding E-field? I've seen people try to measure breakout point current before, but that could be the wrong approach.
Re: "The HOG" Supersized QCWDRSSTC
Uspring, Wed Nov 14 2012, 03:13PM
I've noticed that longer breakout wires lead to an earlier flattening of the primary current. That can be due to an earlier breakout or a higher top load capacitance or some effects of the field on the arc or whatever. Hard to tell. It's definitely worthwhile considering the toroids E-field in arc models.
I've seen breakout current measurements with the electrum. Do you know of any others?
Re: "The HOG" Supersized QCWDRSSTC
Goodchild, Wed Nov 14 2012, 05:40PM
Another interesting thing that I have noted is that high frequency needs less voltage as well. If I remember right Steve Ward showed this with his QCW when he took voltage measurements at 380KHz and then 500KHz and was able to get the same sparks but with less voltage. I'm curios if this also relates to less spark capacitance with an increase in frequency or if it's strictly based on overall volume and density of the plasma.
I will have to find some time to sit and read your TCML thread it look very interesting!
Re:
"The HOG" Supersized QCWDRSSTC
Uspring, Thu Nov 15 2012, 11:39AM
Goodchild wrote:
Another interesting thing that I have noted is that high frequency needs less voltage as well. If I remember right Steve Ward showed this with his QCW when he took voltage measurements at 380KHz and then 500KHz and was able to get the same sparks but with less voltage.
Thank you for the info. When I compared my measurements with Wards, it also looked like higher frequencies required less voltage. My coil runs at 220kHz and needed 70kV for mere 30".
I'm curios if this also relates to less spark capacitance with an increase in frequency or if it's strictly based on overall volume and density of the plasma.
That is an interesting question. I'd also like to know, whether higher frequency affects the spark capacitance. For the unbranched sparks you're looking for, capacitance is probably less than for branched ones.
The model suggests lower voltage requirements for higher frequencies because of the heavier load the capacitances create. That makes the spark hotter and more conductive. Lower voltage is not an advantage, though, since the power requirements rise with frequency for a given spark length. It is not so difficult to achieve high voltage. The problem is to keep it up, once the arc begins to load it. That is where you need power.
I believe, that this is the main difference between QCWs and SGTCs. A SGTC needs a lot of voltage since the arcs don't have much time to grow.
Re: "The HOG" Supersized QCWDRSSTC
Ash Small, Thu Nov 15 2012, 11:58AM
I'll throw something in here.
Higher frequency = more current per unit of time.
power = voltage x current.
You therefore get the same power for less voltage. (same heating, etc)
Higher frequency results in a hotter plasma, requiring less voltage to maintain.
Re: "The HOG" Supersized QCWDRSSTC
Steve Ward, Thu Nov 15 2012, 07:41PM
I still think you need to work on you cooling system.
As it stands, you have built a thermal capacitor with that big block of copper. On top of that, copper represents thermal resistance, ideally youd be putting water in direct contact with the Si with no copper in the way at all.
"Poor" thermal management is what caused my first dual-bridge QCW system to explode at ~12kVA input power. Even with a significantly better water cooling system than your proposed one, it still had its breaking point. The problem? too much copper between my Si and water!
It may not matter on a single shot basis, but you will be severely crippling the power capability of those transistors with the design you have now.
Re: "The HOG" Supersized QCWDRSSTC
Patrick, Thu Nov 15 2012, 08:54PM
the cooling system is a bottle neck for many well and poorly designed systems, as Steve Ward points out, copper and aluminum bolcks merely store and delay heat rise...
ideally the math and physics do support Steve wards point on zero copper and max water in contact with silicon, but practically youll need some well justified (through math and physics) metal solution, like: (1) large cross section for initial conduction, for the (2) spreading and interfacing from the silicon to the water and (3) but a minimum path length to prevent thermal resistance. So thats a machined face of copper to your silicon, then fins (high SA) to the fluid... yet it should be highly physically (dimensionally) optimised.
If he plans to use a single fluid path for all his different potentials, he may need to switch from DI water to canola food oil or diala/univolt oil. If he does plan to use fluid, mica or silicone isolators would be unwise.
thats what i think.
Remember, when we oh-so-smart engineers and scientists F-up thermal matters, nature steps in and rights the situation with noise, flames and plasma...
Since Goodchild has planned a fluid cooled primary and copper block transistor head, he may have to switch to oils... even DI water can be made to explosively decompose.
EDIT: i dont want to put words in Steve Wards mouth, but i think Ward is implying a single hole through the one-inch thick copper block will be insuffcient for fast fliud heat transfer. (single hole, i gather from high res on flickr)
Re: "The HOG" Supersized QCWDRSSTC
Goodchild, Thu Nov 15 2012, 10:36PM
I agree that water directly in contact with the package is the best way to go, however that represents a rather complex heatsink to manufacture at least the way I'm thinking about it. Currently there is a 3/8 water channel though the center of the block and we have a rather large pump to shove water through it at a high pressure. I would also like to add that we got the copper free so it's also a case of stuff we had on hand.
This being said it's not our goal to run the transistors on the absolute edge of their SSOA, that is why we have 8 bridges. So that we can run them at a modestly high level without heating issues. The water blocks are merely a way to stay away from forced air approach and make the bridges more compact. Currently I'm not even convinced that with our available power (about 15Kw) that we will even come close to the overall thermal rating of the system.
The other great thing about our bridges is that it is very easy to change out the block in the future to something more like what Steve Ward proposed with water flow directly over the transistors.
Re:
"The HOG" Supersized QCWDRSSTC
Patrick, Thu Nov 15 2012, 11:06PM
Goodchild wrote ...
The other great thing about our bridges is that it is very easy to change out the block in the future to something more like what Steve Ward proposed with water flow directly over the transistors.
I figured youhad put some thought into this, but remember, direct fluid contact may not be enough. if you cuase boiling you could increase the C'/W resistance rating. Then youd be stuck with thermal run away, and load shedding or hogging on different bridges.
Re:
"The HOG" Supersized QCWDRSSTC
Goodchild, Fri Nov 16 2012, 01:12AM
Patrick wrote ...
Goodchild wrote ...
The other great thing about our bridges is that it is very easy to change out the block in the future to something more like what Steve Ward proposed with water flow directly over the transistors.
I figured youhad put some thought into this, but remember, direct fluid contact may not be enough. if you cuase boiling you could increase the C'/W resistance rating. Then youd be stuck with thermal run away, and load shedding or hogging on different bridges.
Even if we had boiling which is unlikely given the amount of water flow and the fact that we will not be running at the edge of failure; it would be impossible to have a thermal runaway. As referenced in the first post the IGBTs we are using have a positive tempco under all operating conditions unlike 60N60s. On top of this we have a matching network for all the bridges further making it very unlikely of any substantial mismatch.
Re: "The HOG" Supersized QCWDRSSTC
Patrick, Fri Nov 16 2012, 03:24AM
a positive tempco is a good thing to look for, but it wont just cuase load shedding to the other bridges, it will accerlerate the heating, even at the same or lower power. As for derating, thats your best bet for controlling this situation. over spec the components and under power the system.
You can also back-calculate the thermal resistance from temp rise, and predict your power red line.
Re:
"The HOG" Supersized QCWDRSSTC
..., Fri Nov 16 2012, 04:15AM
A single 3/8" line is a little on the small side, but it is amazing what having a decent pump (a few gpm at 50psi is what I usually see) can do to make up for lack of area on the waterblock. I started out using elaborate waterblocks designed for cpu watercooling, and when I saw the cooling channels in my big laser (

) I thought it had no chance of working, but the 500w of heat over the roughly 5in^2 of copper/water area is enough and keeps it at about 5 degrees above the water temperature.
In any case it looks like an amazing project, can't wait to see the sparks!
Re:
"The HOG" Supersized QCWDRSSTC
Patrick, Fri Nov 16 2012, 04:44AM
... wrote ...
.....but the 500w of heat over the roughly 5in^2 of copper/water area is enough and keeps it at about 5 degrees above the water temperature.....
this is good to know. i guess at a few GPM?
Re: "The HOG" Supersized QCWDRSSTC
Tetris, Fri Nov 16 2012, 05:59AM
If QCW sparks are "safe" to touch, and DRSSTC sparks are deadly, where does your soon-to-be-built coil fall in the "safe" range?
Re:
"The HOG" Supersized QCWDRSSTC
Goodchild, Fri Nov 16 2012, 06:51AM
a positive tempco is a good thing to look for, but it wont just cuase load shedding to the other bridges, it will accerlerate the heating, even at the same or lower power. As for derating, thats your best bet for controlling this situation. over spec the components and under power the system.
You can also back-calculate the thermal resistance from temp rise, and predict your power red line.
This is what we plan to do as I said before. That is why we have 8 bridges, we don't plan to run the snot out of the IGBTs but rather run them at a reasonable leave at a little lower than datasheet spec. For the thermal calculations we have already done this falls well within this operating margin.
A single 3/8" line is a little on the small side, but it is amazing what having a decent pump (a few gpm at 50psi is what I usually see) can do to make up for lack of area on the waterblock. I started out using elaborate waterblocks designed for cpu watercooling, and when I saw the cooling channels in my big laser ( ) I thought it had no chance of working, but the 500w of heat over the roughly 5in^2 of copper/water area is enough and keeps it at about 5 degrees above the water temperature.
In any case it looks like an amazing project, can't wait to see the sparks!
Well that is promising for us considering each bridge only dishes out about 267W in heat at full power. And we have similar pump specs. We also plan to have a radiator system on the coil as well to help keep the water at a little about room temp.
If QCW sparks are "safe" to touch, and DRSSTC sparks are deadly, where does your soon-to-be-built coil fall in the "safe" range?
The short answer is that they would probably not kill you but I'm not willing to stake my life on it considering the massive amount of pulsed power this coil will dish out per burst.
DRSSTC sparks are also not deadly (i'm still living to tell the tale), they just hurt a heck of a lot more. Not entirely sure why.
Re: "The HOG" Supersized QCWDRSSTC
teravolt, Fri Nov 16 2012, 05:10PM
hi Eric if you plan to use the fets in a SSOA 100A is at 25C. you could solder some brass studs in a 1/8 copper plate and solder a water jacket around the copper sheet or solder lots of tubing to it
Re: "The HOG" Supersized QCWDRSSTC
Patrick, Fri Nov 16 2012, 05:38PM
given what "..." siad goodchild might be able to calculate a single holes' surface area and get a high enough thermal transfer with low thermal resistance, with a few GPM. that would be easier than anything else.
but Goodchild, are you using multiple fluid circuits or just one fluid path from you primary to the bridges? are your transistors internallt isolated from the tab or are you using the mica/silicone isolators extrernally?
Re: "The HOG" Supersized QCWDRSSTC
Intra, Sat Nov 17 2012, 07:49PM
where you found 10Kv 5.6nF high RMS current MICA caps? google tell nothing about it((
Re:
"The HOG" Supersized QCWDRSSTC
Goodchild, Sat Nov 17 2012, 09:19PM
As for our water cooling design we know that it's not an "optimal" design, but the fact remains we used materials we have on hand. We also don't plan to run the bridges at any extreme levels so out current design fall into the spec we plan to run at.
The MICA caps are from
Re: "The HOG" Supersized QCWDRSSTC
Jrz126, Sat Nov 17 2012, 10:57PM
Looks good.
Any fancy scheme for driving the gates?
Re:
"The HOG" Supersized QCWDRSSTC
Goodchild, Sun Nov 18 2012, 02:34AM
Jrz126 wrote ...
Looks good.
Any fancy scheme for driving the gates?
The gate dive will be GDT but with a twist, because the two sides of the half bridge are not 180 out of phase like a normal DR we will be using two GDTs one for each half bridge. Each bridge unit has it's own driver and OCD circuitry and they all link back to a main controller via a fiber optic link that sends gate dive signals. The main controller has all the circuitry for timing and modulation along with yet another fiber input for an analog input that will be used as the reference to set the overall modulation level.
When we get our final PCBs designed I will update the thread with some photos.
Re: "The HOG" Supersized QCWDRSSTC
tobias, Mon Nov 19 2012, 04:12AM
Hi Eric
Really nice work!
Are you using SolidWorks? If you are, adding "Exploded Line Sketch" lines can make your Exploded View look even nicer =)
Re: "The HOG" Supersized QCWDRSSTC
Goodchild, Mon Nov 19 2012, 08:21AM
I indeed am using SolidWorks, and I did have the line sketch but it made it look so cluttered.... So many lines for so many parts.
Re: "The HOG" Supersized QCWDRSSTC
tobias, Wed Nov 21 2012, 01:03AM
I usually group the pieces in subassemblies and then pull only a few lines between them. Depending on the assembly that is not an option though.
Is the assembly so heavy it will just sit flush or do you have some kind of mechanical attachement planned?
Re: "The HOG" Supersized QCWDRSSTC
Goodchild, Sat Nov 24 2012, 07:38PM
Main thread updated with parts and water block assemblies.
tobias:
We will have the bridges sitting on two T-slot extruded rails that will be supporting the bridges. It will be attached via 90* brackets that mechanically attach it to the rails.
Re:
"The HOG" Supersized QCWDRSSTC
Goodchild, Fri Dec 28 2012, 08:28AM
Main thread update with MICA caps and bus caps.
Last update of 2012 wee! The project is entering it's second year now. We started back in late 2011 around this same time.

Re: "The HOG" Supersized QCWDRSSTC
teravolt, Sat Dec 29 2012, 02:20AM
if your blocks store to much heat you could hog out the back to increase the water surface area and solder a back plate on
Re: "The HOG" Supersized QCWDRSSTC
Goodchild, Tue Aug 27 2013, 06:16AM
UPDATE 8/26/13
Updated original post with new progress.
Re: "The HOG" Supersized QCWDRSSTC
Chris Cristini, Tue Aug 27 2013, 07:29PM
Love the solid works Design and your work reminds me of something a manufacture came up with great standards.
Re: "The HOG" Supersized QCWDRSSTC
Gregory, Wed Aug 28 2013, 02:40AM
What IGBT do you plan to use?
I already made some FPGA based phase-shift and it appear to works pretty well.
I used a counter to make the ramp and it was even auto-ajustable to the FB frequency. Something that is not possible with the constant-current source with capacitor with analog ramp generation
Re:
"The HOG" Supersized QCWDRSSTC
Goodchild, Wed Aug 28 2013, 03:47PM
Gregory wrote ...
What IGBT do you plan to use?
I already made some FPGA based phase-shift and it appear to works pretty well.
I used a counter to make the ramp and it was even auto-ajustable to the FB frequency. Something that is not possible with the constant-current source with capacitor with analog ramp generation
Gregory,
When you did your FPGA design did you use an ADC front end? Or did you use a standard comparator/inductor and phase lead setup like on the UD2 to produce a clock that feeds the FPGA?
I'm curios if you did use an ADC front end how fast of one you used? I have been battling with ADC speed over cost and will probably settle for something in 10-bit 100MSPS range.
I plan to do the phase lead (normally done via an inductor and comparator) all inside of the FPGA. This gets rid of one of the CTs and a bunch of extra hardware on the board. It also builds in much finer control of the primary current, becasue the FPGA gets access to the amplitude information for regulation and current limiting.
Re: "The HOG" Supersized QCWDRSSTC
Gregory, Thu Aug 29 2013, 02:15AM
I used the standard inductor with comparator. I think that 100MSPS is actually much more, MUCH more than what you really need. Something around 1MSPS will do the job very well.
I go a little further and say that you can do it with a 8 bit ADC. But, 10 bits will do only better.
I don't know if I like the idea of have a ADC reading a feedback of a tesla coil, but I don't see why it can't work.
My skype is: gregory_gusberti I deleted my facebook.
Re:
"The HOG" Supersized QCWDRSSTC
Goodchild, Thu Aug 29 2013, 07:20AM
Gregory wrote ...
I used the standard inductor with comparator. I think that 100MSPS is actually much more, MUCH more than what you really need. Something around 1MSPS will do the job very well.
I go a little further and say that you can do it with a 8 bit ADC. But, 10 bits will do only better.
I don't know if I like the idea of have a ADC reading a feedback of a tesla coil, but I don't see why it can't work.
My skype is: gregory_gusberti I deleted my facebook.
It could be done with a 1MSPS ADC I think, however I decided not to for a couple reasons. First by oversampling at 100MSPS I can run the FPGA and ADC from the same clock (100MHz) and do real time computations on the input signal. If I ran at 1MSPS that would be just a little over the first nyquist zone (2*f) and would require that the FPGA do extra math to construct the rest of the sine wave. This is important because the FPGA needs to be able to make changes in the output signal with a resolution of at least 10nS in order to work properly for phase lead at the frequency I'm running.
Gregory, if you ran at 1MSPS how would correct for the fact that you only had two data samples per period?
Lastly at $16 a 100MSPS 10 bit ADC is not that expensive, coupled with an $18 FPGA it ends up being a rather cheap controller with a lot of horse power.
If anyone has experience with DSPs I would love to hear your take on this! I'm new to this kind of advanced DSP and I'm learning as I go.
Re:
"The HOG" Supersized QCWDRSSTC
Steve Conner, Thu Aug 29 2013, 03:06PM
Yeah I agree something like 10-100MSPS is a nice round number, I would have used about that sample rate myself
If you have several samples per period, you can do "Prediktor" phase lead with a simple IIR digital filter, and you can also do the current limit digitally because you have a good chance of capturing the actual peak value.
It also makes life easier if you are sampling fast enough to just drive the gate drivers directly with a 1-bit output. For each sample, you only need to decide if the gate drivers should be off or on. At 1MSPS you would have to synthesize the gate drive waveforms using something like a PWM or timer peripheral clocked off a higher sample rate, and it would degenerate back to being a PLL driver with a digital loop filter. I believe Steve Ward and Phillip Slawinski's latest driver works like this, and it is fine, but full sub-cycle control would be nicer.
Anyway, go Eric!

Re:
"The HOG" Supersized QCWDRSSTC
Goodchild, Thu Aug 29 2013, 05:04PM
Steve Conner wrote ...
Yeah I agree something like 10-100MSPS is a nice round number, I would have used about that sample rate myself
If you have several samples per period, you can do "Prediktor" phase lead with a simple IIR digital filter, and you can also do the current limit digitally because you have a good chance of capturing the actual peak value.
It also makes life easier if you are sampling fast enough to just drive the gate drivers directly with a 1-bit output. For each sample, you only need to decide if the gate drivers should be off or on. At 1MSPS you would have to synthesize the gate drive waveforms using something like a PWM or timer peripheral clocked off a higher sample rate, and it would degenerate back to being a PLL driver with a digital loop filter. I believe Steve Ward and Phillip Slawinski's latest driver works like this, and it is fine, but full sub-cycle control would be nicer.
Anyway, go Eric!

I'm glad someone can validate my thought process! At least I know I'm not completely off the deep end, yet...
From what I have looked at, my current sample rate gives about 200 samples/period at a 500KHz Fres. I like the idea of being able to just adjust the gate drive output based on the sampled points. That's what originally attracted me to choosing the higher sample rate.
My FPGA can run up to 300MHz and I'm tempted to pick an ADC that can run even faster than 100MSPS. 200 samples/period (10nS resolution) seems like it may be pushing the limits of what should be "enough" samples in a single period. But then again the comparator used in the UD phase lead board is 10nS resolution and runs fine it seems.
I guess the only thing that deters me from going to a faster ADC is that after you go past the 100MSPS mark it seems ADCs go into a whole new ball park of price range! Some even as high as $40 parts for only a marginal improvement in performance.
Re: "The HOG" Supersized QCWDRSSTC
Gregory, Fri Aug 30 2013, 06:00PM
Ohh.. I was thinking you want to use it as a 50khz driver hence I said 1MSPs would be fine.
IIR filter you works just fine for the phase-lead compensator, maybe you will have the first cycle not compensated because the capture time for the right initial states on the filter.
Re: "The HOG" Supersized QCWDRSSTC
Steve Conner, Fri Aug 30 2013, 09:23PM
This won't be a problem if you run the ADC and digital filter continuously. The filter will already have the right initial state because it was running before the burst began.
Re: "The HOG" Supersized QCWDRSSTC
Gregory, Fri Aug 30 2013, 10:22PM
The filter will almost stabilize to a zero value like the inductor and you will lsot the first prediction cycle. My idea is to pause the filter atualization at the end of the burst
Re: "The HOG" Supersized QCWDRSSTC
Goodchild, Sat Aug 31 2013, 08:34AM
My plan was not to lead on the rising edge of the first half cycle. You need to create a start pulse to get the current moving in the circuit. However it would only be the very first turn on (when there is zero current) every other transition would run phase lead.
I don't see how you could do phase lead before this time anyway considering the fact that there is no current flowing before this time to lead in the first place.
On top of phase lead however I also have to do all the phase shift modulation and ZVS delay junk as well. It's going to be one busy little FPGA!
I may even consider doing an interleaved ADC design, lord knows I have the pins on the FPGA to do it, but this is yet to be decided.
Re: "The HOG" Supersized QCWDRSSTC
Gregory, Sun Sept 01 2013, 01:40AM
Iterleaved ADC will be great. You can try to run a digital based PLL loop to control the output frequency. I think it can regenerate and stabize much faster than a analog simple PLL. This is the hard think on use normal PLL on DRSSTC tesla coils, at QCW system PLL seems to make the job more easy. With the PLL you can make all the lead design, but, I think, you will always miss the first cycle.
If you design a sate machine approach for me it seems simpler to do the phase lead, now you will lost only the first edge, and not all the first cycle.
Re: "The HOG" Supersized QCWDRSSTC
Intra, Tue Oct 08 2013, 01:39PM
Eric, why are you change IGBT from IXYN82N120 to TO-247? is this mean IXYN82N120 aren't working because of it is too high frequency for this IGBT or here is a cooling trick?
Re: "The HOG" Supersized QCWDRSSTC
Dr. Dark Current, Tue Oct 08 2013, 02:54PM
I think if the phase lead misses a few cycles, it is no deal, especially in a QCW coil where the current takes many cycles to ring up. The phase lead is important during the time when the tank current is near its maximum value.
Re:
"The HOG" Supersized QCWDRSSTC
Chris Cristini, Tue Oct 08 2013, 07:29PM
Goodchild wrote ...
As for our water cooling design we know that it's not an "optimal" design, but the fact remains we used materials we have on hand. We also don't plan to run the bridges at any extreme levels so out current design fall into the spec we plan to run at.
The MICA caps are from
I want your Job.

Great work!