Monitoring Heatsink Temperature...
Ash Small, Thu Aug 23 2012, 04:42PM
I picked up some Constantan wire this morning for the type 'T' thermocouples required for this 'Projects' thread:

All was going fairly well until I realised that the moving coil meters I'm planning to use as temperature guages have an internal resistance of ~750 Ohms.
As the thermocouples only produce ~5milli Volts @100 degrees C and I require @100micro Amps this (I think) means I need to amplify the thermocouple signal using transistors. (I was hoping I could connect thermocouples in series (thermopiles) and get a sufficiently strong signal that way)
I've only been able to measure micro Amps generated by the thermocouples when heating with a lighter (significantly higher temperature than 100C) but I assume this is due to the internal resistance of my DMM, and not a reliable indication.
Can anyone suggest suitable transistors to try for signal amplification?
(BC109, maybe?)
]bc107_108_109_4.pdf[/file]
Re:
Monitoring Heatsink Temperature...
klugesmith, Thu Aug 23 2012, 06:36PM
Any reason you can't use different meters, with coil resistances in the 10 to 100 ohm range?
A thermocouple's voltage output is very small, but it can generate current limited only by the resistance of the circuit.
Consider a gas pilot light safety valve, with a single copper-constantan junction pair. When the hot junction is kept at a few hundred degrees C, the thermocouple directly powers a solenoid that holds a gas valve open. A solenoid wound for low voltage, i.e. with relatively
few turns of
thick wire.
I made a handheld pyrometer using type K metals in the form of solid wires, about AWG10 (coat hanger wire size).
Chose an appropriate meter from a bin at the surplus store. Had gone there armed with a battery and voltage divider, designed to put out about 10 millivolts.
The pyrometer's full scale temperature was set to about 1200 degrees C by choosing a series resistor, IIRC in the middle tens of ohms, to bring the total resistance to a calculated target value.
Good luck.
[edit] Just spent some online search time looking for
data about meter movements. Harder than I expected. Here's one line of analog panel meters, DC, available down to 15 mV full scale.

Re:
Monitoring Heatsink Temperature...
Steve Conner, Thu Aug 23 2012, 07:34PM
If you can't find a suitable meter, the best bet is a precision op-amp with low offset voltage, maybe the OP07. Believe me, you don't want to try making a discrete transistor amplifier. If you're curious, one of Bob Pease's books has a good circuit. Or maybe it's in the LM394 datasheet, I forgot.
I believe the old-school way was to convert the thermocouple signal to AC with a mechanical "chopper" and then step it up with a transformer.

Re: Monitoring Heatsink Temperature...
Sulaiman, Thu Aug 23 2012, 07:40PM
For a thermocouple to read temperature accurately
a high impedance very low offset voltage VOLTMETER
and a reference 'cold junction' are required
together with some (non-linear)correction factors.
For heatsink temperature monitoring I would use an NTC thermistor
or my old favourite wan an LM35 - or a new version.
Re: Monitoring Heatsink Temperature...
Dr. Slack, Thu Aug 23 2012, 08:08PM
DIY metering of thermocouples is hard work. The two best options are a) buy a dedicated thermocouple pre-amp, search RS for "thermocouple amplifier" and you'll find several Analog Devices parts with varying accuracy for around £5 +/- . They do cold junction compensation and give an output with defined volts/degree scaling, just add a multi-meter or b) hit fleeBay for a Chinese knock-off thermocouple meter. I've just bought one for £15, it delivered better than +/- 1C out of the box, and can be calibrated with ice and steam to the probes. Don't buy a multimeter with thermocouple input - horrible accuracy.
NTC thermistors are good, as their output is huge. There is a cunning trick to get a substantially linear voltage output from them over a 20C range, and perfectly usable outside that. Choose a temperature range, for heatsinks you might pick 60C to 80C. Measure the resistance of the NTC at the mid-scale temperature, 70C in this case. Put a fixed resistor of that value in series with the NTC, and feed them from a constant voltage. Measure the voltage across the resistor. The voltage will be offset + scale*temperature. Or measure the voltage from the wiper of a pot across the voltage source to the R/NTC junction, which will allow offset to be adjusted to zero. Or you can measure the voltage from mid-voltage-source to the R/NTC junction. The voltage will be +/- scale*(temperature-mid_temperature).
Nice to see the heatsinks in use so soon
Re: Monitoring Heatsink Temperature...
Sulaiman, Thu Aug 23 2012, 08:36PM
Most industrial temperature monitoring systems use type 'J' or 'K' thermocouples,
or a PT100 resistor.
Cheap dmm with thermocouple input are not absolutely accurate but usable.
Set the dmm to thermocouple input, short the terminals and read ambient temperature.
If a few meters give the same reading +/- 1C I'd call that good enough.
your type T will have about 45 uV/C sensitivity
a single silicon diode or base-emitter junction voltage varies by about -2 mV/C ... 44x more!
Re:
Monitoring Heatsink Temperature...
Ash Small, Fri Aug 24 2012, 06:50AM
Thanks for all the replies.
klugesmith wrote ...
Any reason you can't use different meters, with coil resistances in the 10 to 100 ohm range?
I need four meters, one for each diode in the rectifier. I have these ones, however I may have to consider alternatives if I can't get these to work satisfactorily.
Sulaiman wrote ...
For heatsink temperature monitoring I would use an NTC thermistor
or my old favourite wan an LM35 - or a new version.
Sulaiman wrote ...
you should get a (cheap) multimeter that can use a thermocouple,
make or buy a few thermocouples
(you can use themocouple extension wire to make thermocouples)
and measure the temperatures of
- ambient air
- transistor case (the top part will do for static measurements)
- the heatsink as close to the transistor/heatsink interface as possible
- the temperature of the heatsink far from the transistor
(the last two will require drilling into the heatsink)

It was this post that got me thinking about TCs in the first place.
I don't need it to be linear, or particularly accurate. I just need ~100uA @ 100C (or 80C above ambient), so that the meters go into the red at around 100-120 C.
Using moving coil meters allows me to easily see if anything is amiss.
Sulaiman wrote ...
your type T will have about 45 uV/C sensitivity
a single silicon diode or base-emitter junction voltage varies by about -2 mV/C ... 44x more!
Thanks for pointing that out. It sounds like using silicon to amplify the signal is out of the question then.
Steve Conner wrote ...
If you can't find a suitable meter, the best bet is a precision op-amp with low offset voltage, maybe the OP07.
Will this have the same limitations as silicon, ie -2mV/C ?
I was originally thinking of putting the meter (in series with a resistor) in parallel with a resistor that is in series with the collector/emitter, then putting a third resistor in series with the TC, and connecting to the base/emitter.
If I choose the values of the resistors carefully, and the transistor has sufficiently high gain, small variations in the silicon resistance shouldn't be significant (I think!)
(I'll draw a schematic later, if the above description sounds confusing)
Re:
Monitoring Heatsink Temperature...
Shrad, Fri Aug 24 2012, 07:45AM
you should read this appnote from linear

it is really well written, and contains decent examples with complete schematics
Re:
Monitoring Heatsink Temperature...
klugesmith, Fri Aug 24 2012, 02:44PM
Shrad wrote ...
you should read this appnote from linear

it is really well written, and contains decent examples with complete schematic
I agree, that's great. Don't miss figure 2, which compares TC's with other kinds of electronic temperature sensors. RIP, Jim Williams.
With respect, your single transistor (or 2 discrete transistor) approach with a TC and analog meter would be a waste of time. You have V_BE variations in series with TC voltages.
Re. simple voltage amplifiers using a low-offset-voltage quad op amp: will your TC cold junctions be at a constant temperature, within your desired instrument accuracy?
Since you have 4 meters already on hand, I recommend Dr. Slack's solution using NTC thermistors and a handful of R's. You can use a variable R to calibrate each meter at one temperature point, such as 100 C.
In defense of my three-component (including the TC) pyrometer solution: It served well for many years in my backyard foundry. (Until I broke the hot junction. That had become stuck in Hawaii, when lava at 1800 degrees F crusted over.) Anyway, the type K nonlinearity between 60 and 2400 F can be ignored, or taken care of with nonlinear scale on the meter card. For cold junction compensation, I used the meter movement's offset screw to make pointer indicate the known ambient temperature.
Re: Monitoring Heatsink Temperature...
radiotech, Fri Aug 24 2012, 06:25PM
The classical method to read thermocouples with traceable calibration was to use a
potentiometer, with a standard cell (Weston) as reference. If you are interested
look up Leeds and Northrup history.
However today with Arduino-like processors, you could set up a four
input data logger for a few dollars. An added bonus, it also could log other
parameters of the rectifier system for correlation.
All you need is a usable signal, i.e. in the millivolt range.
Large processes monitored hundreds of temperatures with miles of
bi metalic signal cables strung everywhere. Like the shield probes on the
Columbia, some were more important than others.
Re: Monitoring Heatsink Temperature...
2Spoons, Fri Aug 24 2012, 09:13PM
I like the AD590, which is a current output of 1uA/K. Only two wires, which could be any length as its a current output - wire and connector resistance have no effect. In your case you would either rescale your meters to read ~400uA FS or add a 273uA offset (AD590 outputs absolute temperatue)
Re:
Monitoring Heatsink Temperature...
Ash Small, Tue Aug 28 2012, 09:49PM
I've been away camping and watching power boat racing over the bank holiday weekend so I've not got around to replying until now.
Thanks for all the replies. I'll consider each in detail before making a final decision, however, in the meantime I've come up with the following idea to (possibly) overcome the issue mentioned by Klugesmith (and others), and would appreciate any comments:
klugesmith wrote ...
With respect, your single transistor (or 2 discrete transistor) approach with a TC and analog meter would be a waste of time. You have V_BE variations in series with TC voltages.
If you build the following circuit, with both transistors biased to be switched on halfway:
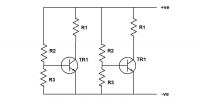
Then connect a thermocouple accross the bases, one will switch more current than the other:
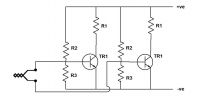
If you then connect a moving coil meter accross the two collectors, the meter will deflect. The Vbe variations will cancel out.
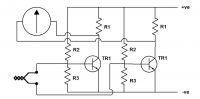
Comments please (I'm sure the solution can't be this simple).
Re: Monitoring Heatsink Temperature...
2Spoons, Tue Aug 28 2012, 10:33PM
For that to have even a slight chance of working the two transistors must be extremely well matched, in the same physical package, preferably on the same die. Such things do exist but are not that cheap. e.g MAT12 made by analog devices, is over $20 at Digikey.
The base bias resistors are going to have to be high values (they load the TC) and very accurate.
Also there is no cold junction compensation.
What you have drawn is very similar to the differential front end of a bipolar op-amp (minus one or two important features). So why not just use an op-amp?
Or better still use the purpose designed chips that include cold junction compensation (available at ~$2 up). There's plenty to choose from.
Re: Monitoring Heatsink Temperature...
Dr. Slack, Wed Aug 29 2012, 07:15AM
Let's spell it out. The TC is putting out uV, microvolts. Each transistor has a VBE tempco in the order of mV, millivolts, 1000x bigger. As the TC makes the transistors take different currents, the transistors will dissipate different powers, and so end up at different temperatures. How different will depend on the thermal detail of how the circuit is built, drafts, the rail voltage, the meter load. If you build one circuit, and mount it in a thermally stablised container with an accurately stablised power supply, you could perhaps calibrate it. If you build another one, it's likely to be different. If you use it with a different meter, it will be different yet again.
If you buy a TC conditioning amplifier, then it doesn't need calibrating, will work with any meter, at any voltage, and if you build another it will be the same.
Re:
Monitoring Heatsink Temperature...
Ash Small, Wed Aug 29 2012, 09:58AM
I found a paper here:

that I'm currently reading.
The non-linearity of type 'T' thermocouples is a bonus for this application.
The only thing I need to accurately calibrate for this application is the approximate temperature that the meter goes into the red, so I dont really need to compensate for reference junction variaton either.
Re: Monitoring Heatsink Temperature...
Steve Conner, Wed Aug 29 2012, 12:51PM
Congrats on your almost-reinvention of the long-tailed pair, but it won't perform well enough as Dr. Slack explained. I have some experience designing input stages for audio power amps, and it is tough to get the offset voltage below some tens of millivolts, let alone microvolts.
Re:
Monitoring Heatsink Temperature...
Ash Small, Wed Aug 29 2012, 04:31PM
Steve Conner wrote ...
Congrats on your almost-reinvention of the long-tailed pair,
Thanks Steve

.
I've been reading up on the AD8497.
Although it is designed for type 'K' tc's, it should be ok for my application as I don't really want linear amplification. It looks fairly simple to use.
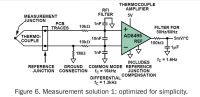
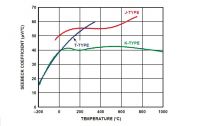
Ideally I want this output:
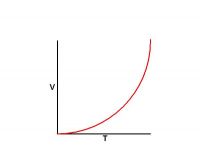
so that at lower temperatures within the operating range the meter doesn't move much, and moves more as the temperature approaches ~100C.
From what I can gather from the output, 5mV/degree C through a 100k Ohm resistor, I may need to either further amplify the signal or use two or three thermocouples in series, unless I can use a lower value output resistor, as my meters are 200uA FSD.
They are cheap and available, RS have them for £3.59 each or £27 for ten.
Re: Monitoring Heatsink Temperature...
Steve Conner, Wed Aug 29 2012, 04:37PM
Yes, I'm pretty sure you can use a lower value output resistor. 100k was chosen to get a low cutoff frequency for the filter without an excessively big capacitor. A moving coil meter doesn't need the filter, it reads the average value so it is filtering the signal already.
If this were my project, I'd take a step back and question the choice of a type T thermocouple in the first place. The solid-state temperature sensing ICs (LM35DZ, AD590 etc) are cheaper than the thermocouple amplifier chips.
Re:
Monitoring Heatsink Temperature...
Ash Small, Wed Aug 29 2012, 05:43PM
Steve Conner wrote ...
The solid-state temperature sensing ICs (LM35DZ, AD590 etc) are cheaper than the thermocouple amplifier chips.
The AD590 range are all a lot more expensive from RS.
The LM35DZ is half the price but is limited to 100 C.
The diodes I have are rated for 300 A at 125 C, but will run at 180 C.
I want the meters to enter the red @ ~100-120 C.
Also, I'd need to drill larger holes in the heatsink to accomodate the transistor type packages.
It looks to me like the AD8497 is a better solution for this application.
Re:
Monitoring Heatsink Temperature...
Avalanche, Wed Aug 29 2012, 07:13PM
I built a TC amplifier a few months ago around an LTC1050 chop-amp

which was a bit OTT in terms of performance and price, but it was a one-off project and I needed it to work!
If you're interested in why you can't just use a single thermocouple to measure temperature, I'd recommend reading the physics of the 'seebeck effect' - here's a link

It's actually impossible to only have one junction anyway, a 'thermocouple' will only give a voltage proportional to the difference between 2 junctions. The TC amp I built at work around the LTC1050 had an arrangement of thermocouple wire as shown in the diagram on that wiki page, the hot junction was attached to an IGBT baseplate, and the cold junction was on the melted surface of a block of ice. With software compensation for non-linearity, we got a ridiculous accuracy! With one junction embedded into the IGBT and the other in the heatsink, the TC amp gave a voltage proportional to heat/power flow through the baseplate

Re:
Monitoring Heatsink Temperature...
Ash Small, Wed Aug 29 2012, 08:52PM
Avalanche wrote ...
I built a TC amplifier a few months ago around an LTC1050 chop-amp

which was a bit OTT in terms of performance and price, but it was a one-off project and I needed it to work!
If you're interested in why you can't just use a single thermocouple to measure temperature, I'd recommend reading the physics of the 'seebeck effect' - here's a link

It's actually impossible to only have one junction anyway, a 'thermocouple' will only give a voltage proportional to the difference between 2 junctions. The TC amp I built at work around the LTC1050 had an arrangement of thermocouple wire as shown in the diagram on that wiki page, the hot junction was attached to an IGBT baseplate, and the cold junction was on the melted surface of a block of ice. With software compensation for non-linearity, we got a ridiculous accuracy! With one junction embedded into the IGBT and the other in the heatsink, the TC amp gave a voltage proportional to heat/power flow through the baseplate

I don't need extreme acuracy for this project, I just want to know if the diodes are getting above ~100-125 C so I can shut the rectifier down until it cools, These diodes aren't cheap. I don't need reference junction compensation really, but the AD8497 has it anyway. I'm not planning on putting 600A through the rectifier, it's a bit 'overkill' for HV projects but I do plan on using it for DC welding and electro-chemistry as well (electro-cleaning, electro-etching, electro-polishing, electro-plating, etc.).
Sounds ike an interesting project you had there!
Re:
Monitoring Heatsink Temperature...
Dr. Slack, Wed Aug 29 2012, 09:08PM
As an example of what you can get if you move away from thermocouples, here is the graph of the division ratio of a thermistor in series with a fixed resistor. The thermistor relation I've used is -4% per C, which is pretty typical. I've gone to the RS site, and there are more there than you can shake a stick at. This one is 68k at 25C, about £0.50 (in 5s, but then you want more than one), with a maximum operating temperature of 150C, in an 0603 package (there are packages that go up to 200C operating). I've simulated it in series with a 3200 ohm resistor, which is its nominal resistance at 100C.
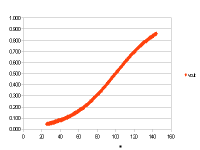
As you can (just about) see, it goes through 0.5 at 100C, as you'd expect. It doesn't go up very fast at low temperatures, like you asked for. Its highest sensitivity is where it matters, around 100C. It's pretty damned linear over +/- 10C from the mid point, at +/- 20C it is starting to bend visibly. But it is still completly usable, i.e. monotonic and with some sensitivity over the whole range.
If you are lucky, you should find a value and sensitivity that match your meter resistance at your target temperature, and can tolerate the self-heating that driving your meter would entail without too much loss of accuracy. Then you can simply put the thermistor in series with the meter, and drive both from a constant voltage source. I think that wins for simplicity. Otherwise, just use a resistor as a load and scale the output voltage with an opamp and apply to your meter.
Re:
Monitoring Heatsink Temperature...
Ash Small, Thu Aug 30 2012, 09:40AM
I'm collecting five 100k thermistors from Maplins tomorrow for £4.50:

I'll evaluate them with my meters (using hot oil and a thermometer).
Re:
Monitoring Heatsink Temperature...
klugesmith, Thu Aug 30 2012, 06:28PM
Ash Small wrote ...
I'm collecting five 100k thermistors from Maplins tomorrow for £4.50
Finally!

And based on Dr. Slack's approach, your chose a value that supports
a very simple solution. I bet you can get the job done with, for each channel, one each of:
- thermistor,
5K variable resistor,
meter movement in parallel with one side of the variable R,
common voltage source.
A voltage reference or regulator IC at 1.2 or 1.25 V, like LM317, would be great.
Have fun!
Re:
Monitoring Heatsink Temperature...
Ash Small, Thu Aug 30 2012, 08:07PM
I'm still not convinced that epoxy bead thermistors of 4.5mm diameter will react as fast to temperature changes as a 1mm or so epoxy coated TC.
And using LM317's and variable resistors is not going to be much cheaper than using AD8497's.
My calculations suggest a 500 Ohm variable resistor would be more suitable than 5k (maybe I misunderstood how to connect the meter across the pot?)
Why not just use a voltage divider directly from 12V to give ~100uA @5kOhm? (this should also give me the non-linearity I want, I think!)
I'll have to run some tests

.
(Post edited.)
Re: Monitoring Heatsink Temperature...
Ash Small, Sun Sept 02 2012, 09:26PM
What wattage resistors should I use for the bias resistors R1 and R2 when biasing an LM317T?
Input voltage is 12V, output voltage is ~2V, current is ~1-1.5A.
I'm still dubious about using silicon when a simple voltage divider will do.
Re: Monitoring Heatsink Temperature...
brandon3055, Sun Sept 02 2012, 10:39PM
Won't you need a rather large heat sink for that? maby you could modify a buck converter from a cheap 12v phone charger to get 2v
Re:
Monitoring Heatsink Temperature...
Ash Small, Sun Sept 02 2012, 10:51PM
Destroyer of mosfets wrote ...
Won't you need a rather large heat sink for that? maby you could modify a buck converter from a cheap 12v phone charger to get 2v
I'm planning on running ALL the fans for cooling the heatsinks from 12V now. I did briefly consider using a 5V CPU fan to cool the LM317T but it didn't really make any sense.
Re:
Monitoring Heatsink Temperature...
Steve Conner, Mon Sept 03 2012, 07:07AM
Well, if you are worried about response speed, you have to ask yourself how quickly your big stud diodes can change temperature in the first place. You also have to ask yourself how often you will look at the temperature meters, since you never mentioned any sort of automatic cutout.
You are a serious candidate for this year's "Most Overcomplicated Rectifier" project. It's 4 diodes in a box, for goodness' sake.

I'd use a bimetallic thermal switch bolted to the heatsink, tripping a contactor in the mains supply to the transformer. Or, over current protection might be all that is needed, since the temperature of the diodes depends mainly on the current flowing.
Re:
Monitoring Heatsink Temperature...
Ash Small, Mon Sept 03 2012, 10:23AM
Steve Conner wrote ...
Well, if you are worried about response speed, you have to ask yourself how quickly your big stud diodes can change temperature in the first place. You also have to ask yourself how often you will look at the temperature meters, since you never mentioned any sort of automatic cutout.
This is an instrumentation system, not a control system.
Steve Conner wrote ...
You are a serious candidate for this year's "Most Overcomplicated Rectifier" project. It's 4 diodes in a box, for goodness' sake.

I'd use a bimetallic thermal switch bolted to the heatsink, tripping a contactor in the mains supply to the transformer. Or, over current protection might be all that is needed, since the temperature of the diodes depends mainly on the current flowing.
The way I see it, 'four diodes in a box' will get hot without efficient cooling. Last time they burned out, hence the instrumentation. These diodes aren't cheap.
Overcurrent protection won't give any warning of cooling fan failure for example.
The most simple solution I can come up with is to use a LM317T to give 2V, then have a string of 4 resistors each supplying 0.5V to each thermistor/meter. The resistor string will also smooth out the power available to each thermistor/meter,
I have no idea how the LM317T works, other than asuming the control pin is analagous to the base or gate of a tranistor, so I was wondering how to work out the power requirements (wattage rating) for R1 and R2.
Re: Monitoring Heatsink Temperature...
Steve Conner, Mon Sept 03 2012, 11:15AM
The LM317's "adjust" pin sources a few microamps, but you also have a current flowing through the resistor string, as determined by the supply voltage and Ohm's law. If you use the recommended 200 ohm resistor between Out and Adj, this works out about 5mA, so ordinary 1/4 watt resistors will be fine.
Re:
Monitoring Heatsink Temperature...
Ash Small, Mon Sept 03 2012, 11:44AM
Steve Conner wrote ...
The LM317's "adjust" pin sources a few microamps, but you also have a current flowing through the resistor string, as determined by the supply voltage and Ohm's law. If you use the recommended 200 ohm resistor between Out and Adj, this works out about 5mA, so ordinary 1/4 watt resistors will be fine.
Thanks Steve. I wasn't sure if the resistor string, R1, R2, 'sees' the input or output voltage, or what the 'trickery' inside the LM317 actually does.
I've a couple of small 500 Ohm presets, but I'm not sure of the wattage rating.
Re: Monitoring Heatsink Temperature...
Steve Conner, Mon Sept 03 2012, 12:02PM
The resistor string sees the output voltage, and the "trickery" drives the "Out" pin in such a way as to maintain 1.25V between "Out" and "Adj".
I think you can safely assume that the small presets are rated at least one-eighth watt.
Re:
Monitoring Heatsink Temperature...
Ash Small, Fri Sept 14 2012, 07:35PM
Well, Klugesmith was correct, as usual (Thanks Rich

).
I'll use 5k pots (presets) accross the meters, and ONE LM317T to drop the ~12V supply for the fans down to 2V, which is then divided over a string of 4 x 1 Ohm, 10W resistors to give 0.5V for each thermistor/meter.
I'll use 2 x 470 Ohm resistors in parallel to give 235Ohms for R1, and 3 x 470 Ohm resistors in parallel to give ~157 Ohms for R2 for the bias on the LM317T, with an additional 500 Ohm preset or two in parallel for 'fine tweaking'. (for starters, anyway).
I couldn't find a suitable 'wall wart' to power the cooling fans, but I did find a 15V 6A toroidal transformer, a 35A 1000V rectifier and a couple of 4700uF 50V 'lytics in the shed, so I'll try that as a supply.
Do I need the 0.1uF and 1uF (if I remember correctly) accross the input and output rails on the LM317T or not? (I have some 400V MKP's I'll probably use, but some sources say they aren't really needed).
I should have all the resistors by mid-week, in the meantime, here are a couple of photo's of my 'bread board'.
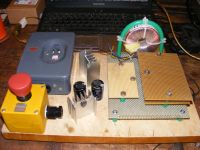
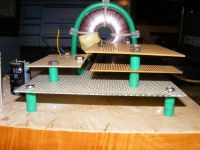
Re:
Monitoring Heatsink Temperature...
Conundrum, Sat Sept 15 2012, 07:16AM
LM317 uses a 1.25V internal reference.
It can be configured to output a constant voltage or constant current depending on circuit, and yes you can replace the bottom leg of the resistor divider with a thermistor.
It burns a lot of power being a linear device but does have failsafes.
BTW this setup looks a bit like the portable vortex generator off "Sliders"

What the heck are you trying to build anyway?
Re:
Monitoring Heatsink Temperature...
Ash Small, Sat Sept 15 2012, 11:09AM
Conundrum wrote ...
LM317 uses a 1.25V internal reference.
It can be configured to output a constant voltage or constant current depending on circuit, and yes you can replace the bottom leg of the resistor divider with a thermistor.
It burns a lot of power being a linear device but does have failsafes.
BTW this setup looks a bit like the portable vortex generator off "Sliders"

What the heck are you trying to build anyway?
I'm not replacing the bias resistor with a thermistor, I'm setting the output to 2V, then using a string of four 1 Ohm resistors to drop the voltage to 0.5V, then feeding 0.5V into each thermistor/moving coil meter.
At 100 degrees C, the combined resistance of each thermistor and meter is ~5k Ohms, which will have virtually no effect on the voltage accross the 1 Ohm resistors (~0.02%). so accuracy will not be affected by having the four thermistors and meters in series with each other.
It's part of this project:

Re:
Monitoring Heatsink Temperature...
Ash Small, Mon Dec 10 2012, 01:27AM
Well, I've finally got back to work on this project after a couple of months of 'not much spare time'.
I filled an enamelled cast iron saucepan with cheap cooking oil and put it on the aga with a thermistor connected to my DMM set to the Ohms setting, added a thermometer, stirred it continuously, and started plotting a graph of temperature V thermistor resistance.....
EDIT: I've now done some maths
and I think the rest of this post is incorrect. Please see post ten posts down....and have realised that the graph curves the 'wrong way' (I wanted a non-linear response, so that the meters don't move much until the thermistors start to get 'hot').
I guess the way around it is to put the meters in parallel with the thermistors instead of in series, and turn the meters upside down (and re-do the 'scale') so that the meters are at FSD @ room temp, but as the temp of the heatsinks (and thermistors) rises, the current through the meters falls. That way I should get the non-linearity I want. (In the right direction.)
I'll probably also need to add a resistance in series with each meter, to control the rate of 'rise' so that I get an acceptable 'curve'.
I can probably still use most of the rest of the circuit as described above, but will probably have to set the voltage supplied by the LM317T to a different voltage to the 2V described above (I've not done the maths yet).
I've only used one thermometer so far (up to 50C), I have a 'jam thermometer' which goes from 50C to over 200C to finish the 'plot')
Hopefully I'll get a chance to make a bit more progress tomorrow.

EDIT: Ignore the cross ar 170 C, 75 kOhms, it's not supposed to be there.
Re:
Monitoring Heatsink Temperature...
Proud Mary, Mon Dec 10 2012, 07:02PM
I use these inexpensive 1000V 25A bridge rectifiers for plasma electrolysis.

I use an industrial isolation transformer in ALL my experiments, but this is not essential.
I then have a big variac, the bridge rectifier above, and some big fat 10,000 uF 450V electrolytics for whatever amount of smoothing seems sensible.
I have the bridge rectifier bolted to a big black heat sink with a smear of heat sink compound, and that's all there is to it.
As my stuff is running off a 13A mains ring, with 13A fused plugs, there wouldn't be any point using any more powerful stuff than this. With all the arcing, bumping, boiling, and evolution of gas with 250 VDC going into a 500 ml beaker full of electrolyte, it's frightening enough as it is, without a lot of palaver about rectifier cooling. The fuses will blow long before the 25A maximum rectifier rating is exceeded. Just use a heat sink of the rating specifed in the rectifier datasheet and let the cooling take care of itself, or
you'll never get anything done!
Re:
Monitoring Heatsink Temperature...
Ash Small, Mon Dec 10 2012, 08:27PM
Proud Mary wrote ...
I use these inexpensive 1000V 25A bridge rectifiers for plasma electrolysis.

I use an industrial isolation transformer in ALL my experiments, but this is not essential.
I then have a big variac, the bridge rectifier above, and some big fat 10,000 uF 450V electrolytics for whatever amount of smoothing seems sensible.
I have the bridge rectifier bolted to a big black heat sink with a smear of heat sink compound, and that's all there is to it.
As my stuff is running off a 13A mains ring, with 13A fused plugs, there wouldn't be any point using any more powerful stuff than this. With all the arcing, bumping, boiling, and evolution of gas with 250 VDC going into a 500 ml beaker full of electrolyte, it's frightening enough as it is, without a lot of palaver about rectifier cooling. The fuses will blow long before the 25A maximum rectifier rating is exceeded. Just use a heat sink of the rating specifed in the rectifier datasheet and let the cooling take care of itself, or
you'll never get anything done! I will be using this for mains rectification.
I also used my last one for various electro-chemical processes, including electro-polishing, electro-etching, etc, where I often run it from a welding transformer, sometimes more than one in parallel.
I blew up my last one using it for DC TIG welding, where hundreds of amps can be flowing.
If I was just using it for mains rectification, I'd do the same as you. (I'm actually using one of those 35A, 1000V rectifiers (GBPC3510, as opposed to the KGBC2510 you linked to) for rectifying the 12V supply from the toroidal Xformer, for powering the cooling fans for the heatsink and 'instrumentation system' as it's all I had lying around).
The 300A, 1200V stud diodes cost me hundreds, so I'm not taking any chances this time.
I also plan on implementing temperature monitoring on the heatsinks of some of my other projects as well, so this research should come in useful for other projects as well.
EDIT: My stud diodes are Schottky's, so should also be ok for rectifying the output from high frequency ferrite cored Xformers as well, if I ever need to.
Re:
Monitoring Heatsink Temperature...
klugesmith, Mon Dec 10 2012, 09:37PM
Ash Small wrote ...
....and have realised that the graph curves the 'wrong way' (I wanted a non-linear response, so that the meters don't move much until the thermistors start to get 'hot').
I guess the way around it is to put the meters in parallel with the thermistors instead of in series, and turn the meters upside down (and re-do the 'scale') so that the meters are at FSD @ room temp, but as the temp of the heatsinks (and thermistors) rises, the current through the meters falls. That way I should get the non-linearity I want. (In the right direction.)
Good work, measuring the component.
1. Does the response agree with what you expect from datasheet?
2. Regarding the "wrong-way" nonlinearity:
Can you show us a chart of predicted meter current with respect to temperature?
It certainly won't be proportional to the thermistor resistance.
Dr. Slack's original recommendation mentioned a reasonably linear voltage variation around the temperature where NTC and fixed resistor divide the reference voltage in half.
Re:
Monitoring Heatsink Temperature...
Ash Small, Mon Dec 10 2012, 10:38PM
klugesmith wrote ...
Good work, measuring the component.
1. Does the response agree with what you expect from datasheet?
I don't have a datasheet, or even a manufacturer's part number. These were the only thermistors that Maplin stock. I had a 0C and 100C figure, and I didn't expect a linear response. It seems to be within a % or so of the figures I remember (5 k Ohm @100 C), but I can't guarantee the accuracy of the thermometer I'm using, and there may be some error in my 'experimental method', but, as I pointed out earlier in the thread, I don't need a huge amount of accuracy, I just want to know when the heatsinks are 'hot'. (I'm just plotting the graph from 40 C to 100 C at the moment, it will be posted as soon as it's finished).
klugesmith wrote ...
2. Regarding the "wrong-way" nonlinearity:
Can you show us a chart of predicted meter current with respect to temperature?
It certainly won't be proportional to the thermistor resistance.
Dr. Slack's original recommendation mentioned a reasonably linear voltage variation around the temperature where NTC and fixed resistor divide the reference voltage in half.
I'm working on this at the moment. I don't want the meter to rise much above a third FSD until ~80C, then I want it to rise to ~two thirds FSD @~100C (This is where it enters the 'red'), but I want it to rise progressively faster as the temp. rises,
The basic idea is that if the meter is reading less than 1/3 FSD I don't need to worry, if it reads between 1/3 and 2/3 FSD I need to keep an eye on it, if it gets to 2/3 FSD I need to start thinking about switching the power off.
I'll post the latest graph as soon as it's been plotted.
Re:
Monitoring Heatsink Temperature...
Ash Small, Mon Dec 10 2012, 11:29PM
Here's the latest graph. The red line is from the 'jam thermometer', the black line is from the 'cheap room thermometer'. I still have some more readings to take, and I've not checked anything yet, but it does give a 'rough idea' of the 'non-linear curve'.
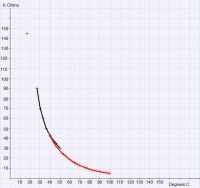
I'll post again tomorrow, when I have some free time.
Re: Monitoring Heatsink Temperature...
lightlinked, Tue Dec 11 2012, 12:40AM
how do you regulate current for tig welding? do you have to scratch start it?
i still dont get why you aren't using common k probes.
Re:
Monitoring Heatsink Temperature...
Ash Small, Tue Dec 11 2012, 01:06AM
lightlinked wrote ...
how do you regulate current for tig welding? do you have to scratch start it?
i still dont get why you aren't using common k probes.
I built an HF TIG starter around a 2N3055 and TV flyback (LOPT)
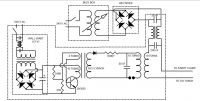
I was originally going to use T probes (copper/constantan), but my meters have an internal resistance of 750 Ohms, so was persuaded by the 'good folks here' to 'explore the possibilities of thermistors'. If you read the whole thread you'll see how I ended up here.
EDIT: current regulation is done by the 'buzz box'.
Re:
Monitoring Heatsink Temperature...
..., Tue Dec 11 2012, 01:06AM
Judging by your graph you have 100k NTC thermistor, there is an analytic formula to calculate the resistance for a given temperature, as R = R0 * e^[b] where R0 is the resistance at T0 (ex, 100k at 25c for your device) and B is as constant of about 4200 (varies slightly with manufacture).
There is also a nice plot of resistance vs temperature for a similar device at

(calculated for R0 = 100k, T0 = 25c, and B = 4200)
For most purposes you can use this datasheet as the datasheet for your device, the curves seem to match up pretty well

Re:
Monitoring Heatsink Temperature...
Ash Small, Tue Dec 11 2012, 02:16AM
[quote]
Judging by your graph you have 100k NTC thermistor, there is an analytic formula to calculate the resistance for a given temperature, as R = R0 * e^[b] where R0 is the resistance at T0 (ex, 100k at 25c for your device) and B is as constant of about 4200 (varies slightly with manufacture).
There is also a nice plot of resistance vs temperature for a similar device at

(calculated for R0 = 100k, T0 = 25c, and B = 4200)
For most purposes you can use this datasheet as the datasheet for your device, the curves seem to match up pretty well

[/quote1355192083]
The NXFpWF104 does look pretty similar. I'll have another look in the morning, as I've had a drink or three. Thanks for posting the link.

EDIT: The first link doesn't appear to work
Re:
Monitoring Heatsink Temperature...
Ash Small, Tue Dec 11 2012, 06:57PM
OK, I've now done some maths

and, at the moment, things are looking pretty good. I think I was mistaken in my earlier post (ten posts above) when I said the graph seems to curve 'the wrong way'.
I'm only really interested in the range from 80C to 125C. I want around 1/4-1/3 FSD @80C, ~2/3 FSD @100C (where the meters enter the red), and FSD @~125C.
I'm told (by the vendor at the hamfest where I bought the meters) that they require ~200uA for FSD, and ~100uA where they enter the red. I'm assuming that 50uA will give me ~ 1/4-1/3 FSD.
I've designed the power supply to give ~0.5V to each thermistor/meter. This is adjustable by adjusting a variable resistor connected to the 'adjust' pin on the LM317T voltage regulator (It will nominally be set for 2V, then fed into a string of four resistors, to divide the voltage between the four thermistor/meter circuits. (see earlier post)
@ 80C, thermistor resistance is ~ 10 kOhm. Ohm's law gives us 50uA.
@100C, thermistor resistance is ~5 kOhm. Ohm's law gives us 100uA.
@125C, thermistor resistance is ~ 2.5 kOhm. Ohm's law gives us 200uA. I've not measured this yet, but the Murata datasheet linked to a few posts above gives us this figure for a 100K thermistor)
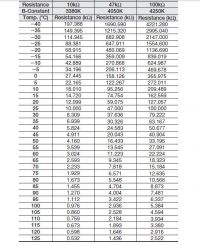
So, the meter won't move much until ~ 80C, should enter the red @ ~100C, and FSD will be ~125C. Exactly what I wanted in the first place

The above figures are all approximate, but are close enough to give me the accuracy required for this project.
I will have two basic adjustments for 'fine tuning, the adjustment of the LM317T to 'tweak' the voltage, and a variable resistor (5 kOhm) in parallel with each meter for 'fine tuning' of each thermistor/meter circuit.
It looks like Dr. Slack and Klugesmith (and others) were 'spot on' with their advice.

Next job is to check the meters to see if the information that the vendor gave me was accurate.........
(Unless anyone can find any mistakes in my maths)