Soldering using Indalloy 207 (pure silver)
Ash Small, Thu Jul 12 2012, 08:35PM
I've been googling this most of the day and found very little information on the subject, so I thought I'd ask here if anyone knows anything about soldering using pure silver (indalloy 207), or if anyone can point me in the right direction.
All I've been able to find is that pure silver IS listed in the table of soldering 'alloys' as Indalloy 207.

The question I'd specifically like answered is
'What flux to use when tinning copper with silver?'Could I use a flux like 'HT5', used for 'conventional' silver solders used at high temperatures (500-800 degrees C, typically used for soldering stainless steels), on copper when applying pure silver (melting point 960 C), or should I use something else?
Can anyone here please help me?
EDIT: Or should I try something like borax or borax/boric acid mix?
Re:
Soldering using Indalloy 207 (pure silver)
Ash Small, Fri Jul 13 2012, 09:59AM
I found this, relating to 'Old Sheffield Plate':
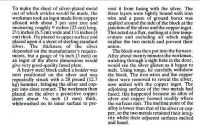
I'd still be interested in any further advice or tips, if anyone has any.
Re: Soldering using Indalloy 207 (pure silver)
..., Fri Jul 13 2012, 03:02PM
The only time I soldered using silver solder I used an acid based flux that was sold by the vendor that sold me the silver (also, I did not buy pure silver solder, it was a lower melting point alloy so that I could solder two pieces of silver together instead of welding them). I am not sure what was in it, but it worked great! You could try with normal rosin flux or rubyfluid, they will probably work, just not work well enough that 'real' companies would recommend them when they have better fluxes to sell you.
Re:
Soldering using Indalloy 207 (pure silver)
Forty, Fri Jul 13 2012, 04:15PM



These sources also say borax flux.
Re:
Soldering using Indalloy 207 (pure silver)
Ash Small, Fri Jul 13 2012, 07:14PM
... wrote ...
The only time I soldered using silver solder I used an acid based flux that was sold by the vendor that sold me the silver (also, I did not buy pure silver solder, it was a lower melting point alloy so that I could solder two pieces of silver together instead of welding them). I am not sure what was in it, but it worked great! You could try with normal rosin flux or rubyfluid, they will probably work, just not work well enough that 'real' companies would recommend them when they have better fluxes to sell you.
'Silver solder' is a name that is used for any solder containing silver. Most of these, contain less than 5%, along with tin and/or copper and or other alloying elements.
Re:
Soldering using Indalloy 207 (pure silver)
..., Sat Jul 14 2012, 01:54AM
Silver bearing solders usually have a low percentage of silver, we used silver solder (sold for jewelry applications, so presumably no heavy metals in the mix, just copper/tin) we ended up going with 70% silver, since the 80% stuff had a melting point of 825C, and my iron only goes to 850C.
In any case, unless you have a good reason otherwise, the normal acid based stuff, I think the type I used was

Re:
Soldering using Indalloy 207 (pure silver)
Ash Small, Sat Jul 14 2012, 06:44AM
I've done a bit of researches into fluxes and the most common 'hard' flux seems to be prips flux (no-one seems quite sure if it should have a capitol 'P' or an apastrophe before the 's'), which is Borax, Tri Sodium Phosphate, and Boric Acid in a ratio of 2:2:3. This is boiled in water for some time, then painted or sprayed on to the workpiece.
Zinc Chloride or ammonium chloride seem to be a popular choice for mid-range temperature soldering and rosin based fluxes seem to be only used for lower temperature work.
(There are a range of other fluxes for specialized electrical work, and applications where manufacturers don't want to have to clean the flux off.)
I used to use a mixture of borax and boric acid for brazing years ago, but it wasn't easy to clean off afterwards, especially if it was dirty and black (ie had absorbed a lot of oxides, etc.) My recent research indicates that a sodium carbonate or sodium bicarbonate solution (or several other solutions) will dissolve it quite readily and quickly.
I'm trying to avoid using a solder containing copper or lead for this particular application, although I am considering using solders containing tin as well as silver, although Sterling Silver (92.5% silver, 7.5% copper (or copper and/or other elements) will provide a harder wearing surface (according to my research).
From what I can glean, Borax seems to work fine on it's own, especially at higher temperatures, but other formulas are easier to remove afterwards.
While pure silver only melts at a temperature about 100 C below that of copper ( 962C compared to 1083C), they will 'fuse' at a lower temperature, as the alloy formed at the interface has a lower melting point.
I think I'm nearly ready to start running some tests

I found a very interesting book on the subject of plating copper with silver, written in 1912, which can be downloaded for free here:

EDIT: Another flux 'recipe' here:
-Boric acid powder 106.4 grams
-Sodium Acid Phosphate 70 grams (Di sodium hydrogen orthophosphate)
-Sodium Hydroxide 7 grams (Caustic Soda)
-Borax powder 70 grams
-Teepol 28.4ml (Dishwashing Liquid)
-Distilled water 1.5 litres