DCRSG
Hazmatt_(The Underdog), Thu Aug 03 2006, 07:42AM
I just picked up a D.C. brush type motor that looks like it just might do the trick for a stable and smooth spark gap. I had a lot of trouble getting the count 'correct' from the rotary optical counter because I had to keep adjusting the Systron for the proper amount of attenuation.
I was getting counts in the 23k and 24k range, and figured this must be the result of mis-triggering on the input. So I kept at it, kept adjusting the attenuation, and then the result became a consistant 10k count.
The motor works very well and is very smooth. Unfortunately I have no specs for this motor, but no worries, I am really good at determining these things.
The motor works quite well at 50V, and is at about 12XX r.p.m. which leads me to believe that this is a 90VDC motor and will run reliably at or slightly above 1800 r.p.m.
So what makes this a project? well, I will add the 90VDC controller in the future if I'm good enough to get that working reliably. I envision a regulated voltage source at around 90V with its own feedback of the optical counter locking it in at 1800 r.p.m., and then life would be really good.
So that's my plan. More to come as I progress.
Matt
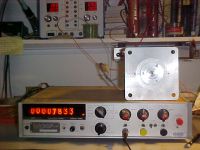
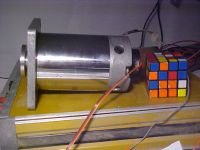
Re: DCRSG
Part Scavenger, Sat Aug 05 2006, 03:22AM
That looks just like it came out of a treadmill... Nice motor.
Re: DCRSG
Electroholic, Sat Aug 05 2006, 04:58AM
seems to be fairly powerful, you can probably afford to have a heavier disk for the RSG to stablize teh rpm.
Re:
DCRSG
Hazmatt_(The Underdog), Thu Aug 10 2006, 04:10AM
Well it turns out that the rotary optical counts 1000/ revolution. So I recalculated that I need 30 K counts/second, which then gives me 1800 r.p.m.
Now I was going to solve the problem myself with a closed loop control, and I will in the future, but since there is a time limit and a need for a proper solution, I must cheat.
I have here a DC motor control that gives me my speed I need and then-some. I have to enable an optoisolator to activate the controller. I want to enable the slow speed that is preset, then enable a higher speed to run. Why? Well because I want to make sure that its clearing okay for a while before ramping up to the final speed.
I also wanted the controller to send an enable pulse when the motor has reached the final speed, but we'll do that with a delay relay in the control board of the Tesla coil.
This is a superb control by Dart, and a great motor too. Very smooth and stable. It's giving me better then 1% without load.
Next step...turn this badboy into the rotary spark gap with precision control. A good coil is coming!
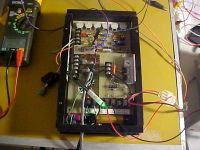
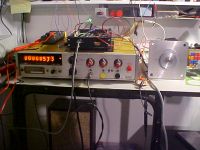
*********Update**********
I now have the motor tachometer sorted out for the most part. I need to make it all 4000 series logic so that its more flexible under the stresses of the EM field.
The motor outputs 30kc, so I needed a standard frequency of 66.66Hz for the display to readout 1800 r.p.m., so I took a 2MHz crystal and divided it by 30k. It works nicely and I hope to have a good looking tach. in a short time.
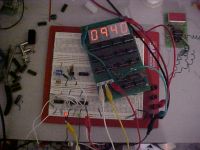
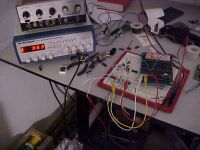
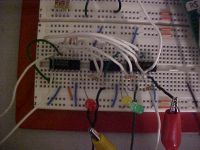
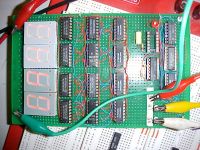
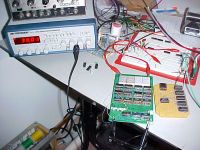
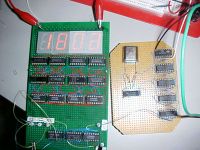
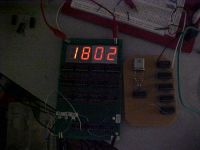
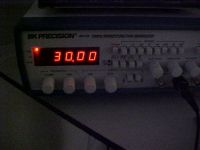